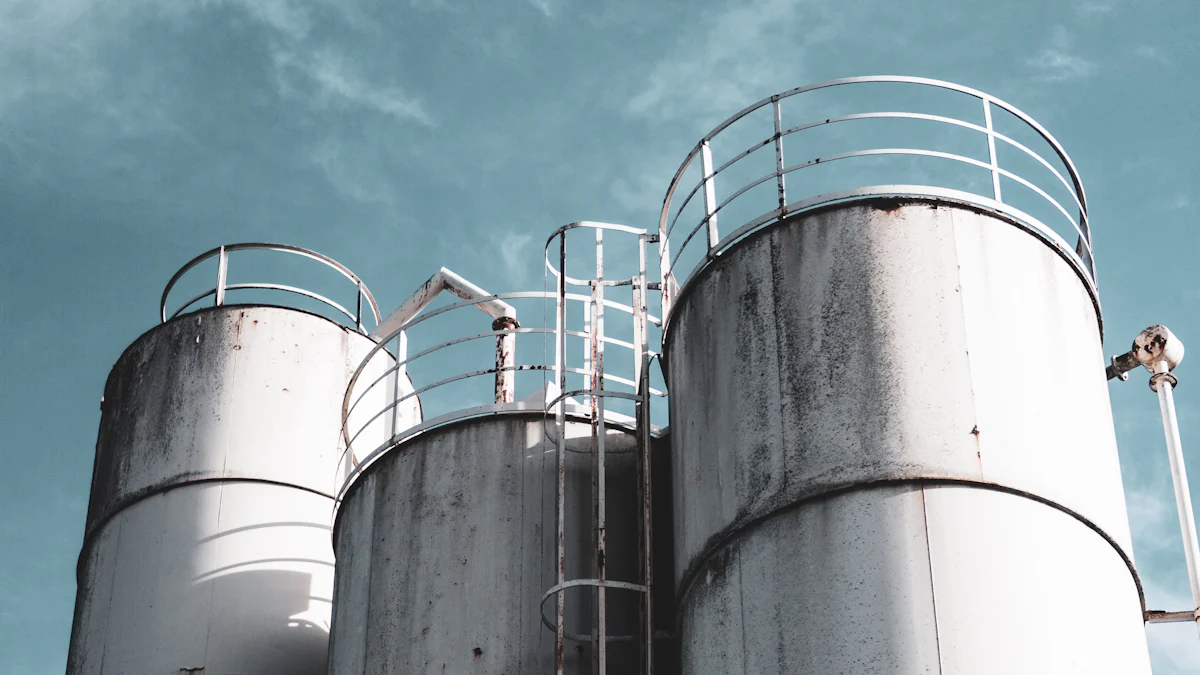
Chemical mixer tanks play a vital role in industries where precision and consistency are critical. You rely on these tanks to blend substances efficiently, whether in pharmaceuticals, food processing, or chemical manufacturing. For example, in chemical processing, tank mixers ensure uniform mixing of components like adhesives, paints, and detergents, directly impacting product quality. In pharmaceuticals, mixers help create sterile solutions and emulsions, while in food production, they maintain hygiene and consistency. With advancements in industrial tank mixers, modern equipment now offers enhanced efficiency, durability, and adaptability for diverse industrial applications, making them indispensable processing equipment.
Key Evaluation Criteria for Chemical Mixer Tanks
When selecting a chemical mixer tank, understanding the key evaluation criteria ensures you make an informed decision. These criteria focus on aspects like performance, design, and cost-effectiveness, which directly impact mixing efficiency and product quality.
Performance Metrics
Power Consumption
Power consumption plays a critical role in determining the operational efficiency of a mixer tank. Tanks equipped with energy-efficient motors reduce electricity usage while maintaining optimal mixing performance. Modern designs often incorporate variable speed drives, allowing you to adjust the motor speed based on the specific mixing requirements. This not only minimizes energy waste but also enhances the overall mixing quality. According to advancements in energy-efficient mixing technologies, optimized impeller designs further contribute to reducing power consumption without compromising performance.
Mixing Time
Mixing time is another vital metric that affects productivity. Tanks with advanced agitation systems ensure faster and more thorough blending of materials. Precision mixing tanks, for instance, utilize innovative impeller geometries to achieve uniform mixing in less time. Shorter mixing times translate to higher throughput, enabling you to meet production demands efficiently. By focusing on mixing performance, you can ensure consistent results while maximizing operational output.
Design Features
Impeller Geometry
The geometry of the impeller significantly influences the mixing process. Impellers with optimized designs create better fluid flow patterns, ensuring even distribution of materials. For example, impellers designed using computational fluid dynamics simulations enhance mixing efficiency by minimizing air pockets and dead zones. This results in improved mixing quality, which is crucial for industries like pharmaceuticals and food processing. Selecting a tank with the right impeller design ensures you achieve the desired consistency and texture in your products.
Tank Material and Durability
The material of the tank determines its durability and suitability for specific applications. Stainless steel tanks are widely preferred due to their corrosion resistance, hygiene, and ease of cleaning. These tanks are ideal for industries requiring high sanitation standards, such as food and beverage or pharmaceuticals. Additionally, durable materials extend the lifespan of the tank, reducing the need for frequent replacements. Investing in a robust tank ensures long-term reliability and consistent mixer performance.
Cost-Effectiveness
Initial Investment
The upfront cost of a chemical mixer tank is a significant consideration. While high-end tanks may seem expensive, they often come with advanced features that enhance mixing efficiency and reduce operational costs. For instance, tanks with energy-efficient motors and optimized impeller designs may have a higher initial price but offer substantial savings over time. Balancing your budget with the tank’s capabilities ensures you get the best value for your investment.
Long-Term Operational Costs
Operational costs include energy consumption, maintenance, and potential downtime. Tanks designed with energy-efficient technologies and durable materials help lower these expenses. For example, stainless steel tanks require minimal maintenance due to their resistance to wear and tear. Additionally, features like automated controls and IoT integration streamline operations, reducing labor costs and improving overall efficiency. Considering long-term costs ensures you select a tank that aligns with your financial and operational goals.
Top Chemical Mixer Tanks in 2023
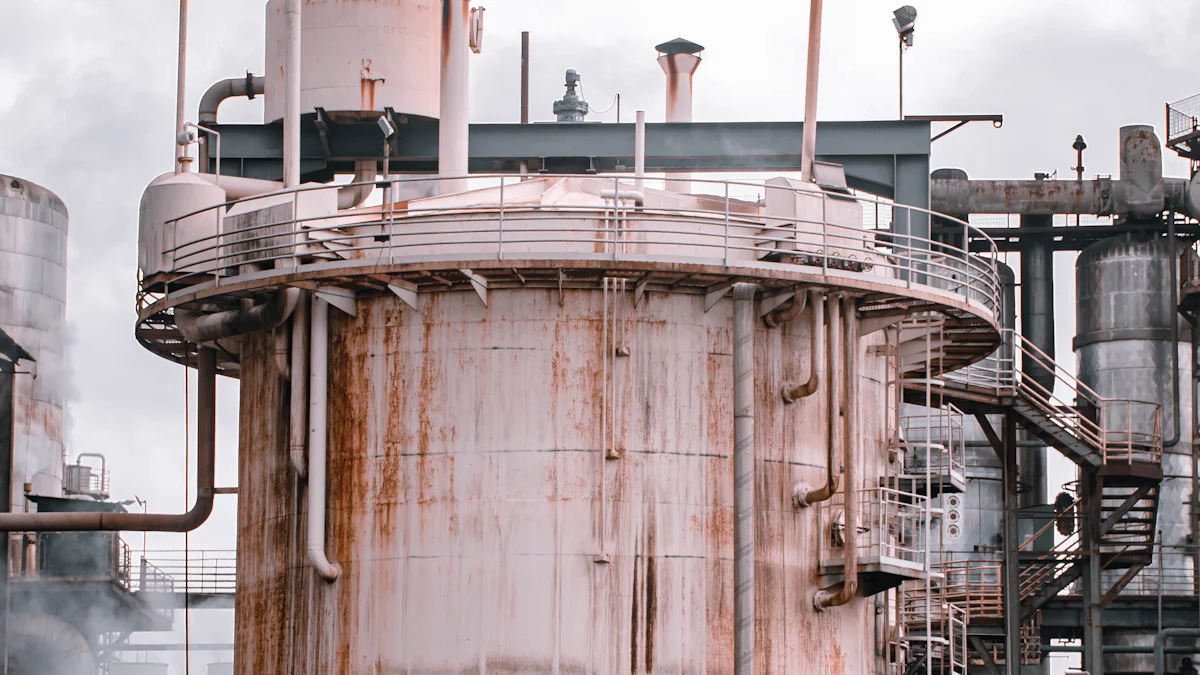
When it comes to selecting the best chemical mixer tanks, understanding their unique features and applications is essential. Below, we review three standout options for 2023, highlighting their specifications, strengths, and ideal uses.
Chenma Stainless Steel Mixer Tank
Specifications and Features
The Chenma Stainless Steel Mixer Tank stands out for its precision and versatility. Built with high-grade stainless steel, this tank offers exceptional durability and resistance to corrosion. It features advanced impeller designs that ensure efficient mixing, even for complex formulations. The tank complies with international safety and quality standards, including ISO9001 and EU CE certifications, making it a reliable choice for industries with stringent requirements.
Key features include:
- High-performance stainless steel construction.
- Energy-efficient motors with variable speed drives.
- Customizable designs tailored to specific industrial needs.
Strengths and Weaknesses
This mixer excels in industries like pharmaceuticals, food processing, and chemical manufacturing. Its robust construction ensures long-term reliability, while its smooth surface facilitates easy cleaning and sanitization. The tank’s energy-efficient design reduces operational costs, making it a cost-effective solution for businesses. However, its premium build may come with a higher initial investment.
Ideal Applications
The Chenma Stainless Steel Mixer Tank is ideal for applications requiring high hygiene standards and precise mixing. It is particularly suited for blending sterile solutions in pharmaceuticals, creating consistent emulsions in food production, and handling corrosive chemicals in manufacturing processes.
PrecisionMix Pro 5000
Specifications and Features
The PrecisionMix Pro 5000 is engineered for meticulous mixing tasks. Its advanced agitation system creates optimal turbulence, ensuring thorough blending of all components. This precision is critical for industries like breweries, distilleries, and chemical processing, where consistency directly impacts product quality. The tank also incorporates innovative impeller geometries to reduce mixing time without compromising efficiency.
Key features include:
- Advanced agitation systems for uniform mixing.
- Optimized impeller designs for faster blending.
- Durable construction suitable for demanding environments.
Strengths and Weaknesses
The PrecisionMix Pro 5000 delivers exceptional performance in achieving uniformity and consistency. Its ability to handle complex chemical reactions and maintain flavor profiles makes it a favorite in the beverage and chemical industries. While its focus on precision may limit its use in high-volume applications, it remains a top choice for specialized tasks.
Ideal Applications
This mixer is perfect for applications requiring precise control over mixing parameters. It excels in breweries and distilleries, where maintaining consistent flavor profiles is crucial. It is also well-suited for chemical processes that demand exacting standards.
HygienicBlend 300 Series
Specifications and Features
The HygienicBlend 300 Series is designed for large-scale operations. With its high-capacity tank, this mixer can handle substantial volumes, making it ideal for industries like water treatment, petrochemicals, and large-scale chemical manufacturing. Its robust construction ensures structural integrity, while its efficient mixing capabilities meet the demands of high-throughput environments.
Key features include:
- Large-capacity design for high-volume processing.
- Structural integrity for handling heavy loads.
- Easy maintenance with accessible cleaning features.
Strengths and Weaknesses
The HygienicBlend 300 Series shines in high-volume applications. Its ability to process large quantities efficiently makes it indispensable for industries scaling up operations. The tank’s ease of maintenance further enhances its appeal. However, its size and capacity may not suit smaller-scale or precision-focused tasks.
Ideal Applications
This mixer is best suited for large-scale applications, such as water and wastewater treatment, petrochemical processing, and bulk chemical manufacturing. Its robust design ensures reliable performance in demanding industrial settings.
AgiTech Industrial Mixer Tank
Specifications and Features
The AgiTech Industrial Mixer Tank is a powerhouse designed for industries requiring robust and efficient mixing solutions. Built with industrial-grade materials, this tank ensures durability and reliability in demanding environments. Its advanced agitation technology optimizes the mixing process by creating consistent fluid motion, which is essential for achieving uniform results. The tank also features a modular design, allowing you to customize it based on your specific operational needs.
Key features include:
- High-capacity mixing capabilities for large-scale operations.
- Advanced agitation systems to ensure thorough blending of materials.
- Durable construction to withstand harsh industrial conditions.
- Customizable configurations to adapt to various applications.
This mixer incorporates cutting-edge engineering to handle complex mixing tasks efficiently. Whether you need to suspend solids in liquids or blend viscous materials, the AgiTech tank delivers consistent performance.
Strengths and Weaknesses
The AgiTech Industrial Mixer Tank excels in versatility and durability. Its ability to handle a wide range of mixing applications makes it a valuable asset across multiple industries. The tank’s advanced agitation system reduces mixing time, boosting productivity and ensuring consistent quality in every batch. Its modular design also allows you to scale operations as your business grows.
“The AgiTech tank’s robust construction and efficient mixing capabilities make it a top choice for industries scaling up their production processes.”
However, its industrial-grade build may not be ideal for smaller-scale operations or precision-focused tasks. While it offers exceptional performance for high-volume mixing, it might exceed the requirements of businesses with limited production needs.
Ideal Applications
The AgiTech Industrial Mixer Tank is perfect for industries that demand high-capacity and efficient mixing solutions. It is particularly well-suited for:
- Chemical manufacturing, where uniform mixing of raw materials is critical.
- Petrochemical processing, which requires tanks capable of handling heavy-duty operations.
- Water and wastewater treatment, where large volumes of liquids must be processed efficiently.
This tank is an excellent choice for businesses looking to enhance their operational efficiency while maintaining consistent product quality. Its adaptability and robust design ensure it meets the challenges of high-demand industrial environments.
Comparison Table of Top Chemical Mixer Tanks
When choosing the right chemical mixer tank, comparing key features side by side helps you make an informed decision. Below is a breakdown of the top chemical mixer tanks in 2023, focusing on performance metrics, design features, and cost-effectiveness.
Key Features Compared
Performance Metrics
Performance plays a pivotal role in determining how well a mixer meets your industrial needs. The Chenma Stainless Steel Mixer Tank excels in energy efficiency with its variable speed drives, allowing you to adjust motor speeds for optimal mixing performance. This feature reduces power consumption while maintaining consistent mixing quality. Similarly, the PrecisionMix Pro 5000 stands out for its advanced agitation system, which ensures uniform blending and shortens mixing time. If you prioritize high-capacity operations, the HygienicBlend 300 Series and AgiTech Industrial Mixer Tank deliver exceptional throughput, making them ideal for large-scale applications.
Each tank’s impeller design also significantly impacts mixing efficiency. The Chenma Stainless Steel Mixer Tank and PrecisionMix Pro 5000 feature optimized impeller geometries that enhance fluid flow and minimize dead zones. These designs ensure thorough mixing, even for complex formulations. On the other hand, the HygienicBlend 300 Series and AgiTech Industrial Mixer Tank focus on handling substantial volumes efficiently, making them indispensable for industries like water treatment and petrochemical processing.
Design Features
The design of a mixer tank directly influences its durability, ease of use, and adaptability. Stainless steel construction, as seen in the Chenma Stainless Steel Mixer Tank, offers superior corrosion resistance and hygiene, making it perfect for industries with strict sanitation requirements. The PrecisionMix Pro 5000 incorporates innovative impeller designs that reduce mixing time, while its compact structure suits environments with limited space.
For large-scale operations, the HygienicBlend 300 Series and AgiTech Industrial Mixer Tank provide robust structural integrity. These tanks are built to withstand heavy loads and harsh industrial conditions. Additionally, their modular designs allow for customization, enabling you to adapt the tank to specific operational needs. Easy maintenance features, such as accessible cleaning ports, further enhance their usability.
Cost-Effectiveness
Balancing initial investment with long-term operational costs is crucial when selecting a mixer tank. The Chenma Stainless Steel Mixer Tank may require a higher upfront cost, but its energy-efficient motors and durable materials reduce maintenance expenses over time. Similarly, the PrecisionMix Pro 5000 offers precision-focused features that justify its price, especially for industries requiring meticulous mixing.
For businesses scaling up operations, the HygienicBlend 300 Series and AgiTech Industrial Mixer Tank provide excellent value. Their ability to handle large volumes efficiently minimizes downtime and maximizes productivity. While these tanks cater to high-capacity needs, their robust construction ensures longevity, reducing the need for frequent replacements.
By comparing these features, you can identify the tank that aligns with your industry requirements, budget, and operational goals. Whether you need precision, high capacity, or durability, each tank offers unique advantages tailored to specific applications.
Expert Recommendations for Choosing the Right Chemical Mixer Tank
Selecting the right chemical mixer tank requires careful consideration of your industry needs, budget, and operational requirements. Each factor plays a critical role in ensuring optimal mixing performance and maintaining product quality. Below, you’ll find expert recommendations tailored to help you make an informed decision.
Industry-Specific Needs
Pharmaceutical Industry
In the pharmaceutical industry, precision and hygiene are paramount. You need industrial tank mixers that meet stringent regulatory standards and ensure sterile mixing environments. Stainless steel tanks with smooth surfaces and corrosion-resistant properties are ideal for this sector. These tanks prevent bacterial growth and facilitate easy cleaning, which is essential for maintaining product quality. Impellers designed for gentle agitation are also crucial, as they help preserve the integrity of sensitive formulations like emulsions and suspensions.
Food and Beverage Industry
For food and beverage applications, maintaining consistency and hygiene is critical. Cylindrical stainless steel tanks with optimized impeller designs are highly effective in achieving uniform mixing quality. These tanks ensure even distribution of ingredients, which is vital for preserving flavor profiles and texture. Additionally, tanks with easy-to-clean features and food-grade certifications streamline operations and reduce downtime. Whether you’re blending sauces, beverages, or dairy products, selecting a tank with high mixing efficiency ensures consistent results.
Chemical Manufacturing
Chemical manufacturing demands robust equipment capable of handling aggressive substances and complex mixing processes. Tanks with advanced impeller geometries and durable materials like stainless steel excel in this environment. They provide the strength needed to withstand corrosive chemicals while ensuring thorough mixing. For processes requiring high agitation, such as suspending solids in liquids, tanks with powerful motors and variable speed drives deliver superior performance. Customizable designs also allow you to adapt the tank to specific chemical formulations, enhancing operational flexibility.
Budget Considerations
High-End Options
High-end industrial tank mixers offer advanced features that maximize mixing performance and long-term efficiency. These tanks often include energy-efficient motors, automated controls, and IoT integration, which streamline operations and reduce operational costs. While the initial investment may be higher, the durability and enhanced mixing quality of these tanks provide significant value over time. For industries prioritizing precision and scalability, high-end options are a worthwhile investment.
Budget-Friendly Alternatives
If you’re working within a limited budget, there are cost-effective alternatives that still deliver reliable performance. Look for tanks with essential features like durable construction and optimized impeller designs. While these models may lack advanced automation, they still provide consistent mixing quality for smaller-scale operations. Budget-friendly tanks are ideal for startups or businesses focusing on straightforward mixing tasks without compromising on product quality.
Operational Requirements
Batch Size and Volume
Your production scale directly influences the type of tank you need. For large-scale operations, tanks with high-capacity designs and robust structural integrity are essential. These tanks handle substantial volumes efficiently, ensuring consistent mixing performance even under heavy loads. Conversely, smaller batches benefit from compact tanks with precise impeller configurations, which optimize mixing quality for lower volumes. Matching the tank size to your batch requirements ensures efficient resource utilization.
Mixing Complexity
The complexity of your mixing process determines the features you should prioritize. For simple blending tasks, standard impeller designs and basic agitation systems suffice. However, if your process involves complex formulations or requires precise control over mixing parameters, advanced impeller geometries and variable speed drives become indispensable. These features enhance mixing efficiency and allow you to achieve the desired consistency and texture in your products.
By aligning your choice of chemical mixer tank with these expert recommendations, you can ensure optimal performance, cost-effectiveness, and suitability for your specific application. Whether you’re in pharmaceuticals, food production, or chemical manufacturing, understanding your unique requirements will guide you toward the best solution.
Innovations in Chemical Mixer Tank Technology in 2023
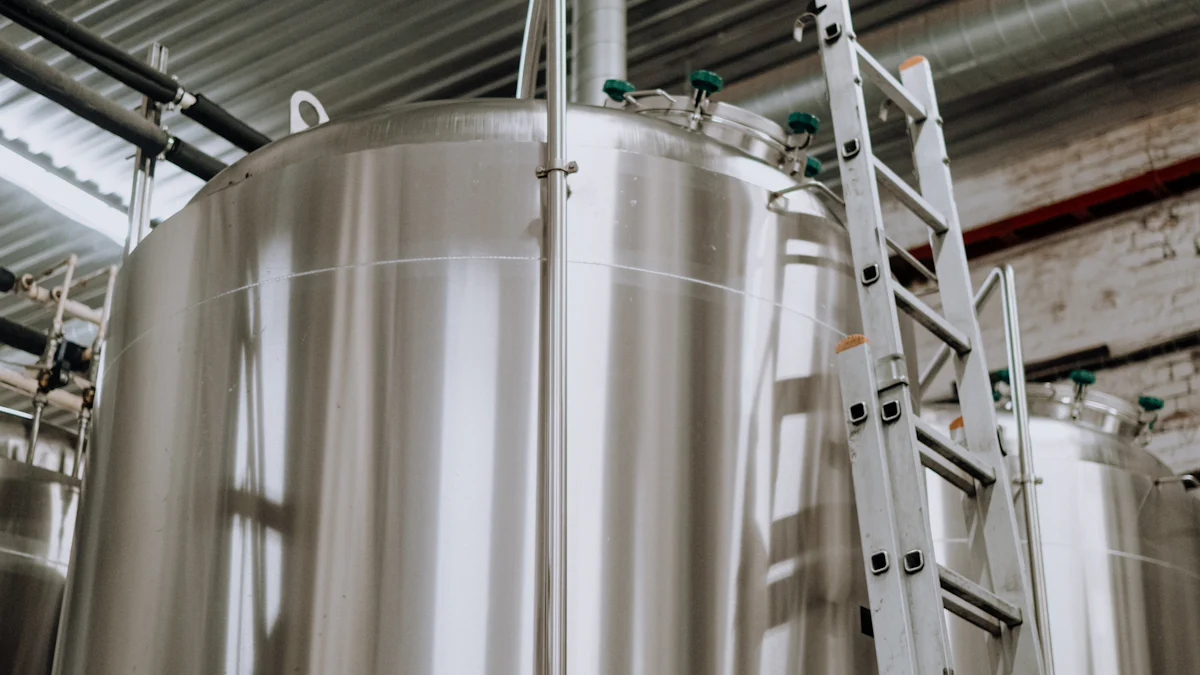
The chemical mixer tank industry has seen remarkable advancements in 2023, driven by the need for greater efficiency, precision, and sustainability. These innovations not only enhance the mixing process but also align with modern industrial demands for smarter and more eco-friendly solutions. Below, we explore the cutting-edge features shaping the future of chemical mixer tanks.
Smart Features
IoT Integration
The integration of IoT (Internet of Things) technology into chemical mixer tanks has revolutionized how you monitor and control the mixing process. IoT-enabled tanks allow you to track real-time data, such as temperature, mixing speed, and impeller performance, through connected devices. This level of connectivity ensures that you can make adjustments instantly, optimizing the mixing process for better results.
For example, IoT systems can send alerts when the impeller encounters resistance or when the tank requires maintenance. This predictive capability minimizes downtime and prevents costly disruptions. By leveraging IoT, you gain deeper insights into your operations, enabling you to maintain consistent product quality while reducing operational inefficiencies.
Cedarstone Industry Experts emphasize, “Automated monitoring through IoT not only improves efficiency but also ensures that tanks operate within safe parameters, reducing the risk of errors.”
Automated Controls
Automated controls have become a cornerstone of modern chemical mixer tanks. These systems allow you to pre-program mixing parameters, such as speed, duration, and impeller direction, ensuring consistent results every time. Automation eliminates the guesswork, making it easier to achieve precise mixing for complex formulations.
Advanced automated systems also adapt to changes in the mixing environment. For instance, if the viscosity of the material increases, the system can adjust the impeller speed to maintain optimal performance. This adaptability is particularly valuable in industries like pharmaceuticals and food processing, where precision is critical.
By incorporating automated controls, you can streamline your workflow, reduce manual intervention, and focus on scaling your operations without compromising quality.
Sustainability
Energy-Efficient Designs
Energy efficiency has become a top priority in the design of chemical mixer tanks. Modern tanks now feature energy-efficient motors and optimized impeller geometries that reduce power consumption without sacrificing performance. Variable speed drives, for instance, allow you to adjust the motor speed based on the specific mixing requirements, ensuring that energy is used only when needed.
These designs not only lower your operational costs but also contribute to environmental sustainability. By consuming less energy, you reduce your carbon footprint, aligning your operations with global sustainability goals.
Micet Group Engineers highlight, “Energy-efficient designs are essential for industries looking to balance performance with environmental responsibility. Optimized impeller configurations play a key role in achieving this balance.”
Eco-Friendly Materials
The use of eco-friendly materials in chemical mixer tanks has gained traction in 2023. Stainless steel remains a popular choice due to its durability, corrosion resistance, and recyclability. Unlike other materials, stainless steel does not degrade over time, ensuring that your tank maintains its structural integrity while minimizing waste.
Some manufacturers are also exploring alternative materials that are both durable and environmentally friendly. These innovations aim to reduce the environmental impact of tank production and disposal, making them a sustainable choice for forward-thinking industries.
By choosing tanks made from eco-friendly materials, you not only enhance the longevity of your equipment but also contribute to a more sustainable industrial ecosystem.
Common Mistakes to Avoid When Selecting a Chemical Mixer Tank
Choosing the right chemical mixer tank is critical for ensuring efficient operations and maintaining product quality. However, many buyers make avoidable mistakes during the selection process. By understanding these common pitfalls, you can make a more informed decision and avoid costly errors.
Overlooking Key Specifications
Failing to evaluate the technical specifications of a mixer tank can lead to poor performance and operational inefficiencies. Each tank is designed with specific parameters, such as motor power, impeller type, and mixing speed, to suit particular applications. Ignoring these details may result in a tank that cannot handle your process requirements.
For example, if your operation involves blending viscous materials, selecting a tank with insufficient motor power or an incompatible impeller design will hinder mixing efficiency. Tanks with advanced features, such as precision monitoring systems, allow you to adjust parameters like speed and temperature, ensuring optimal performance. Always match the tank’s capabilities to your process needs to avoid underperformance.
Pro Tip: Review your production requirements thoroughly. Consider factors like material viscosity, batch size, and required mixing time before finalizing your choice.
Ignoring Long-Term Costs
Focusing solely on the initial purchase price often leads to higher expenses over time. While budget-friendly tanks may seem appealing, they might lack energy-efficient motors or durable materials, resulting in increased operational costs. Energy consumption, maintenance, and downtime are significant contributors to long-term expenses.
Modern tanks with energy-efficient designs reduce power usage without compromising performance. For instance, variable speed drives enable you to adjust motor speeds based on your mixing needs, minimizing energy waste. Additionally, tanks made from durable materials, such as stainless steel, require less frequent maintenance and have a longer lifespan. Investing in a high-quality tank upfront can save you money in the long run.
Industry Insight: According to advancements in tank mixer design, energy-efficient motors and optimized impeller geometries significantly lower operational costs while improving mixing efficiency.
Choosing the Wrong Size or Capacity
Selecting a tank with the wrong size or capacity can disrupt your production process. A tank that is too small may require multiple batches, increasing labor and time costs. Conversely, an oversized tank can lead to inefficient mixing, as the impeller may not create sufficient turbulence to blend materials effectively.
To determine the right size, assess your batch volume and production scale. High-capacity tanks are ideal for large-scale operations, while compact tanks work better for smaller batches. Customizable designs also allow you to adapt the tank to your specific needs, ensuring efficient mixing regardless of your production scale.
Key Takeaway: Always align the tank’s capacity with your operational requirements. Oversized or undersized tanks can compromise both efficiency and product quality.
By avoiding these common mistakes, you can select a chemical mixer tank that meets your operational needs, reduces costs, and enhances productivity. Careful planning and attention to detail will ensure you make the best investment for your business.
Maintenance Tips for Prolonging the Life of Your Chemical Mixer Tank
Proper maintenance of your chemical mixer tank ensures consistent performance and extends its lifespan. By following a structured approach, you can avoid costly repairs, reduce downtime, and maintain product quality. Below are practical tips to help you keep your mixing equipment in top condition.
Routine Cleaning and Inspection
Regular cleaning and inspection are essential for preventing buildup and identifying potential issues early. Residue from previous batches can compromise the quality of your mixing process, especially in industries like food and pharmaceuticals where hygiene is critical. Cleaning the tank after each use removes contaminants and ensures a sterile environment.
During inspections, check for signs of wear, such as cracks, corrosion, or loose components. Pay close attention to the impeller and motor mount, as improperly secured parts can lead to inefficiencies or damage. For example, improperly mounted mixers may cause vibrations that waste materials and damage the tank. Addressing these issues promptly prevents further complications.
Pro Tip: Use non-abrasive cleaning agents compatible with the tank material to avoid surface damage. Stainless steel tanks, for instance, benefit from gentle cleaning solutions that preserve their corrosion-resistant properties.
Preventive Maintenance Practices
Preventive maintenance minimizes the risk of unexpected breakdowns and extends the operational life of your mixer tank. Create a maintenance schedule that includes tasks like lubricating moving parts, tightening bolts, and calibrating the motor. These small actions ensure the tank operates smoothly and efficiently.
Replace worn-out components, such as seals and gaskets, before they fail. This proactive approach prevents leaks and maintains the integrity of the mixing process. Additionally, ensure the tank and mixer are compatible with the chemicals you use. Selecting the right materials for your tank prevents chemical reactions that could damage the equipment or contaminate the product.
Key Insight: Preventive maintenance not only reduces repair costs but also enhances the reliability of your mixing operations, ensuring uninterrupted production.
Troubleshooting Common Issues
Even with regular maintenance, issues can arise. Knowing how to troubleshoot common problems helps you address them quickly and effectively. For instance, if the mixer produces uneven results, check the impeller for damage or improper alignment. Adjusting or replacing the impeller often resolves this issue.
If the motor overheats, inspect the ventilation system and ensure the motor is not overloaded. Overheating can also result from excessive friction, so verify that all moving parts are properly lubricated. In cases where the tank vibrates excessively, examine the mounting brackets and secure them tightly to prevent further damage.
Quick Fix: Keep a log of recurring issues and their solutions. This record helps you identify patterns and implement long-term fixes, improving the overall efficiency of your mixing system.
By incorporating these maintenance practices into your routine, you can maximize the performance and longevity of your chemical mixer tank. A well-maintained tank not only saves money but also ensures consistent mixing quality, which is vital for meeting production standards.
The Role of Stainless Steel in Industrial Tank Mixers
Stainless steel has become the gold standard for industrial tank mixers due to its unmatched combination of durability, hygiene, and versatility. Whether you work in food production, pharmaceuticals, or chemical manufacturing, stainless steel tanks provide the reliability and performance needed to meet stringent industry demands. Below, we explore the key advantages of stainless steel and its applications in high-hygiene industries.
Advantages of Stainless Steel Tanks
Hygiene and Easy Cleaning
Stainless steel offers a smooth, non-porous surface that resists bacterial growth, making it ideal for industries where cleanliness is critical. You can clean these tanks easily, ensuring no residue or contaminants remain after each use. This feature is especially important in sectors like food and pharmaceuticals, where even minor contamination can compromise product quality.
The material’s resistance to corrosion further enhances its hygiene benefits. Unlike other materials, stainless steel does not degrade when exposed to cleaning agents or harsh chemicals. This ensures that your tank remains sanitary and maintains its structural integrity over time. Regular cleaning and inspection of the impeller and tank interior help you maintain optimal performance while adhering to strict hygiene standards.
Maintenance Professionals emphasize, “Proper cleaning and maintenance are essential for stainless steel mixing tanks. These practices ensure product quality and prevent contamination.”
Durability and Corrosion Resistance
Stainless steel stands out for its exceptional durability. It can withstand extreme temperatures, high pressures, and exposure to aggressive chemicals without losing its structural integrity. This makes it a reliable choice for demanding industrial environments. The material’s corrosion resistance also ensures longevity, reducing the need for frequent replacements and lowering long-term operational costs.
The impeller, a critical component of any tank mixer, benefits significantly from stainless steel construction. Impellers made from this material resist wear and tear, ensuring consistent mixing performance even under challenging conditions. By investing in a stainless steel tank, you gain equipment that delivers reliable results and withstands the test of time.
Applications in High-Hygiene Industries
Food and Beverage
In the food and beverage industry, maintaining hygiene is non-negotiable. Stainless steel tank mixers excel in this sector by ensuring uniform mixing while preventing contamination. Whether you’re blending sauces, beverages, or dairy products, these tanks provide the consistency and cleanliness required to meet regulatory standards.
The smooth surface of stainless steel facilitates thorough cleaning, allowing you to switch between batches without risking cross-contamination. Impellers designed for gentle yet effective agitation ensure that ingredients mix evenly, preserving flavor profiles and texture. With stainless steel tanks, you can achieve high-quality results while maintaining the highest hygiene standards.
Pharmaceuticals
Pharmaceutical production demands precision and sterility. Stainless steel tank mixers meet these requirements by providing a controlled environment for mixing sensitive formulations. The material’s resistance to corrosion and ease of cleaning make it ideal for creating sterile solutions, emulsions, and suspensions.
Impellers in pharmaceutical mixers often feature advanced geometries to ensure thorough blending without introducing air bubbles or dead zones. This level of precision is crucial for maintaining the efficacy and safety of pharmaceutical products. By using stainless steel tanks, you can comply with stringent industry regulations while achieving consistent, high-quality results.
Industry Insight: Stainless steel mixing tanks are indispensable in high-hygiene industries due to their ability to combine durability, cleanliness, and efficiency.
Trends in the Industrial Tank Mixers Market
The industrial tank mixers market continues to evolve, driven by advancements in technology and shifting industry demands. Staying informed about these trends helps you make better decisions when selecting equipment for your operations. Below, we explore three key trends shaping the market in 2023.
Growth in Food-Grade Mixer Tanks
The demand for food-grade mixer tanks has surged as industries prioritize hygiene and safety. These tanks, often made from stainless steel, meet strict sanitation standards required in food and beverage production. Their smooth, non-porous surfaces resist bacterial growth, ensuring cleanliness during mixing processes. This feature is critical for maintaining product quality and complying with regulatory requirements.
Stainless steel food-grade tanks also offer durability and corrosion resistance, making them a long-term investment. They handle a wide range of mixing tasks, from blending sauces to emulsifying dairy products. The global food-grade mixer tank market, valued at $3.8 billion in 2022, is projected to grow steadily, reflecting their increasing adoption across industries.
Key Insight: The CDC recommends stainless steel for potable water storage due to its safety and longevity, further emphasizing its suitability for food-grade applications.
Increasing Demand for Heated Mixing Tanks
Heated mixing tanks have gained popularity in industries requiring precise temperature control. These tanks are essential for processes like melting, emulsifying, or maintaining the viscosity of materials. For example, in the chemical industry, heated tanks ensure uniform mixing of substances like adhesives and resins, which require specific temperatures for optimal results.
Modern heated tanks incorporate energy-efficient designs to reduce power consumption. Stainless steel remains the preferred material for these tanks due to its heat resistance and ability to withstand extreme conditions. The global heated mixing tank market is expected to grow significantly through 2031, driven by the need for efficient and reliable solutions in high-temperature applications.
Industry Trend: Energy-efficient motors and advanced insulation technologies are becoming standard features in heated tanks, aligning with sustainability goals.
Advancements in Agitation Technology
Agitation technology has seen remarkable progress, enhancing the efficiency and precision of mixing processes. Innovations in impeller design now allow for better fluid flow, minimizing dead zones and ensuring uniform distribution of materials. Computational fluid dynamics (CFD) simulations play a crucial role in optimizing these designs, making them more effective for complex formulations.
Industries like pharmaceuticals and chemical manufacturing benefit greatly from these advancements. For instance, precision mixing tanks equipped with advanced agitation systems deliver consistent results, even for challenging tasks like suspending solids in liquids. These improvements not only reduce mixing time but also enhance product quality, making them indispensable for modern industrial applications.
Expert Opinion: “Optimized impeller geometries and variable speed drives are transforming the way industries approach mixing, offering greater control and efficiency,” according to engineers specializing in industrial tank mixers.
By understanding these trends, you can align your equipment choices with the latest innovations and market demands. Whether you need food-grade tanks, heated solutions, or advanced agitation systems, staying ahead of these developments ensures your operations remain competitive and efficient.
Choosing the right chemical mixer tank is essential for optimizing your industrial processes. The reviewed tanks, such as the Chenma Stainless Steel Mixer Tank, demonstrate how advanced designs and features can enhance mixing precision and operational reliability. Whether you prioritize hygiene, durability, or scalability, these mixers cater to diverse industry needs. Evaluate your specific requirements, including batch size, mixing complexity, and budget, to make an informed decision. By selecting a tank that aligns with your goals, you ensure consistent performance, improved efficiency, and long-term value for your operations.
FAQ
What factors should you consider when choosing a chemical mixer tank?
You should evaluate several key factors to ensure the tank meets your needs. These include the viscosity of the materials, the specific gravity of the substances, the tank volume, and the required mixing speed. Each of these factors directly impacts the tank’s performance and suitability for your application. For example, high-viscosity materials may require tanks with powerful motors and specialized impellers to achieve uniform mixing.
Are stainless steel tanks better than other materials?
Yes, stainless steel tanks are often the preferred choice due to their durability, corrosion resistance, and hygiene. They are ideal for industries like food processing and pharmaceuticals, where cleanliness is critical. Stainless steel also withstands exposure to harsh chemicals and extreme temperatures, making it a versatile option for various applications. Additionally, its smooth surface prevents bacterial growth, ensuring easy cleaning and maintenance.
How do different tank shapes affect mixing performance?
Tank shapes play a significant role in mixing efficiency. Cylindrical tanks are common for general-purpose mixing, while conical-bottom tanks are better for draining and handling solids. Flat-bottom tanks work well for low-viscosity liquids, but they may create dead zones in certain applications. Choosing the right shape depends on your specific mixing requirements and the type of materials you process.
Tip: Consult with a tank manufacturer to determine the best shape for your operation.
Can you customize a chemical mixer tank?
Yes, many manufacturers offer customization options to meet specific industry needs. You can modify features like tank size, impeller design, and motor power to suit your process requirements. Customization is particularly beneficial for industries with unique challenges, such as handling corrosive chemicals or achieving precise mixing for sensitive formulations. Tailored designs ensure optimal performance and efficiency.
What is the importance of scalability in mixer tanks?
Scalability allows you to adjust production capacities based on demand. This flexibility is crucial for industries with fluctuating production needs, such as food and beverage or chemical manufacturing. Tanks designed for scalability can handle both small and large batches, reducing the need for multiple systems. Investing in scalable equipment ensures you can adapt to market changes without compromising efficiency.
How do you prevent chemical reactions during mixing?
To avoid unwanted reactions, you must select a tank compatible with the substances being mixed. Consider factors like the chemical properties, temperature requirements, and potential reactivity of the materials. For example, corrosive chemicals require tanks made from resistant materials like stainless steel. Proper system setup, including the right fittings and seals, also minimizes the risk of leaks or contamination.
What maintenance practices extend the life of a mixer tank?
Routine cleaning, regular inspections, and preventive maintenance are essential. Clean the tank after each use to remove residue and prevent contamination. Inspect components like the impeller, seals, and motor for wear or damage. Replace worn parts promptly to avoid operational disruptions. Lubricating moving parts and calibrating the motor periodically also ensures smooth operation and prolongs the tank’s lifespan.
Why is IoT integration important in modern mixer tanks?
IoT integration enhances monitoring and control of the mixing process. It allows you to track real-time data, such as temperature, mixing speed, and motor performance, through connected devices. This technology helps you optimize operations, reduce downtime, and maintain consistent product quality. IoT-enabled tanks also provide predictive maintenance alerts, ensuring issues are addressed before they escalate.
What are the benefits of energy-efficient mixer tanks?
Energy-efficient tanks reduce power consumption, lowering operational costs while maintaining performance. Features like variable speed drives and optimized impeller designs minimize energy waste. These tanks also align with sustainability goals by reducing your carbon footprint. Over time, the savings on energy bills and maintenance make energy-efficient tanks a cost-effective investment.
How do you choose the right tank size for your operation?
The right tank size depends on your batch volume and production scale. For large-scale operations, high-capacity tanks ensure efficient mixing without frequent refills. Smaller tanks work better for low-volume or precision-focused tasks. Oversized tanks may lead to inefficient mixing, while undersized tanks can increase labor and time costs. Assess your production needs carefully to select the appropriate size.
Key Insight: Customizable tanks offer flexibility, allowing you to adapt the size to your specific requirements.