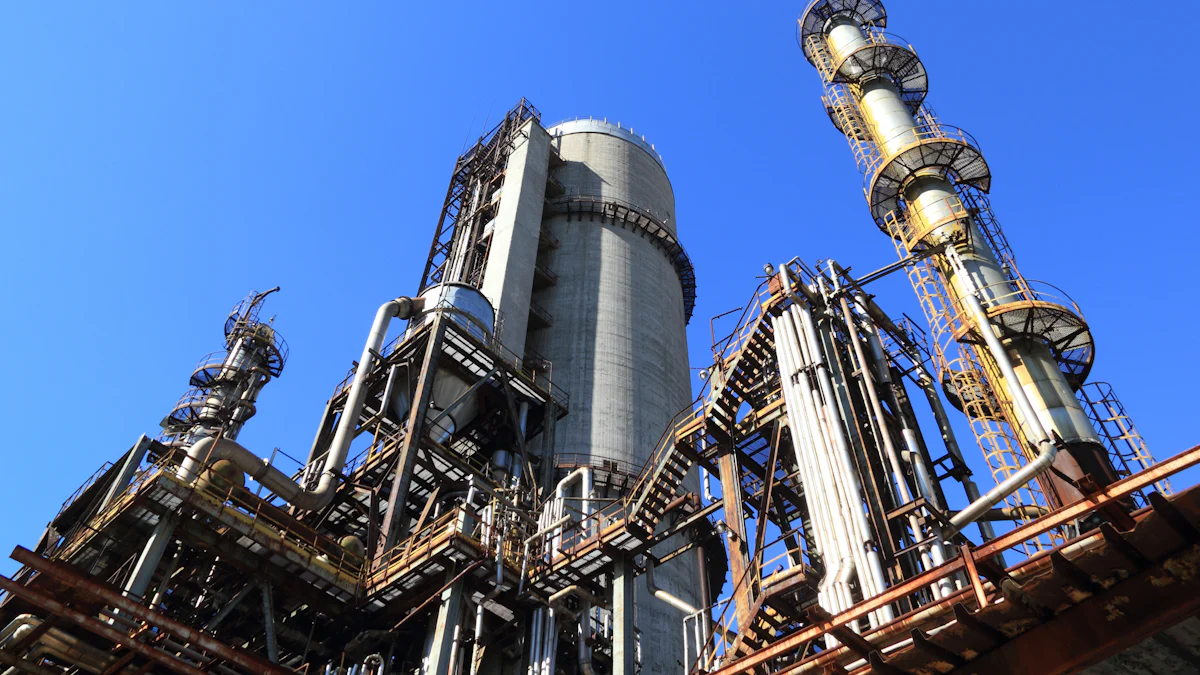
Efficient processing in industries relies heavily on the right equipment, and a chemical mixing tank with agitator plays a vital role in this. Agitators ensure uniform mixing, which guarantees consistent product quality. By preventing uneven distribution of materials, they enhance the efficiency of your operations. These systems also improve safety by minimizing risks like spills or leaks during mixing. Additionally, they reduce the time and energy required for processing, making them indispensable for productivity. Whether you handle hazardous chemicals or delicate formulations, an agitator ensures precision and reliability in every batch.
Key Benefits of Using a Chemical Mixing Tank with Agitator
Uniform Mixing for Consistent Product Quality
Achieving consistent product quality is essential in any industrial process. A chemical mixing tank with agitator ensures uniform distribution of materials, preventing uneven textures or inconsistencies in the final product. The agitator keeps particles suspended, avoiding sedimentation and ensuring that every component blends thoroughly. This uniformity is especially critical when working with complex formulations or sensitive ingredients.
Research and advancements in blade designs have optimized mixing processes, making agitators far more effective than traditional mechanical mixers. These innovations allow you to achieve superior results in less time.
By maintaining homogeneity throughout the mixing process, you can meet stringent quality standards and deliver reliable products to your customers.
Enhanced Efficiency and Reduced Processing Time
Time is a valuable resource in industrial operations. Agitators significantly reduce the time required for mixing by accelerating the blending process. Unlike traditional methods, which often demand lengthy mixing times, modern agitators use advanced technologies to streamline operations. For example, RAM technology has proven to cut labor and processing time drastically compared to older systems.
Agitators also improve energy efficiency. In baffled tanks, they reduce power consumption while maintaining optimal performance. This efficiency not only saves time but also lowers operational costs, allowing you to allocate resources more effectively.
Improved Safety in Handling Hazardous Materials
Handling hazardous materials requires precision and care. Agitators enhance safety by minimizing risks during the mixing process. They ensure controlled and stable mixing, reducing the likelihood of spills, leaks, or dangerous reactions. This is particularly important when working with volatile chemicals or substances that require exact proportions.
Additionally, the design of mixing tanks with agitators often includes features that further enhance safety. For instance, enclosed systems prevent exposure to harmful fumes, protecting both operators and the environment. By using an agitator, you can create a safer workspace while maintaining high productivity levels.
Cost Savings Through Optimized Resource Utilization
Investing in a chemical mixing tank with agitator can lead to significant cost savings by optimizing resource utilization. Agitators streamline the mixing process, reducing the time and energy required to achieve a uniform blend. Unlike traditional mechanical mixers, which often demand extended operation times, modern agitators incorporate advanced technologies like RAM (Rapid Agitation Mechanism). This innovation drastically cuts labor and processing time, allowing you to complete tasks more efficiently.
Efficient power consumption is another key advantage. In baffled tanks, agitators minimize energy usage while maintaining superior performance. This efficiency not only lowers electricity costs but also reduces wear and tear on equipment, extending its lifespan. By using less energy and requiring fewer repairs, you can allocate your budget to other critical areas of your operations.
Agitators also help you maximize the use of raw materials. Their ability to ensure thorough mixing prevents waste caused by uneven blending or sedimentation. For example, advanced blade designs have been developed through extensive research to enhance mixing precision. These designs ensure that every particle is utilized effectively, minimizing material loss and improving overall yield.
According to industry advancements, modern agitators outperform traditional systems in both efficiency and cost-effectiveness. They allow you to achieve better results with fewer resources, making them a smart investment for any industrial process.
By adopting a chemical mixing tank with agitator, you can reduce operational expenses, improve resource management, and enhance the profitability of your business.
How an Agitator Works in a Chemical Mixing Tank
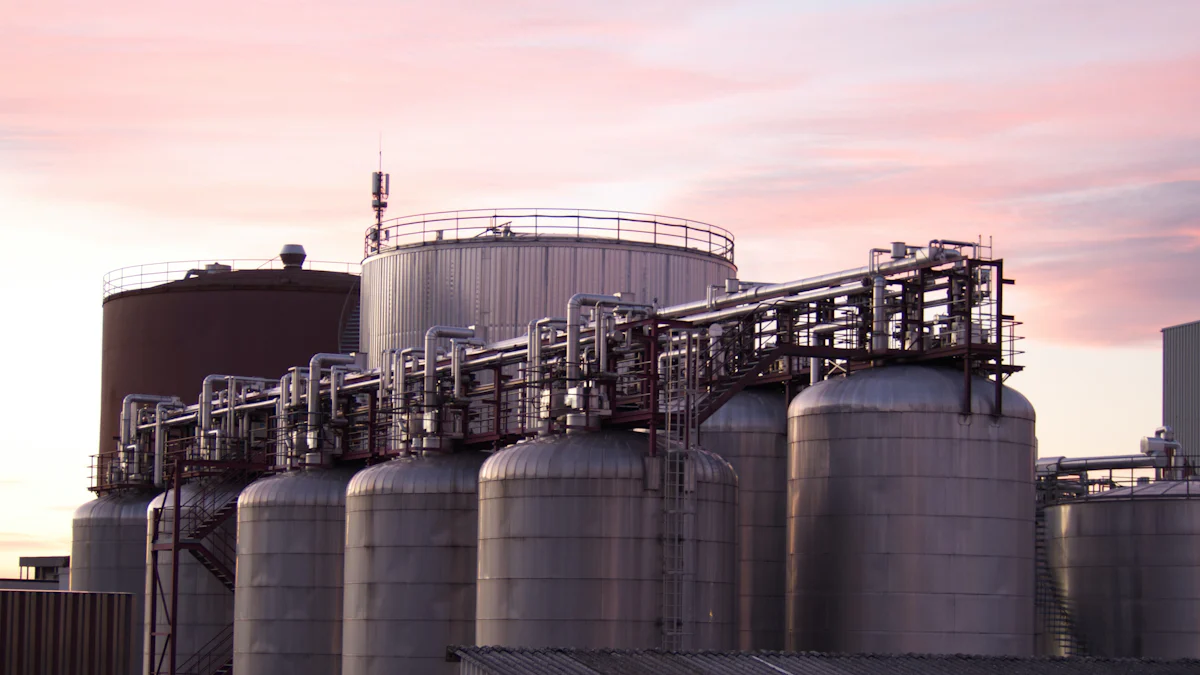
The Role of Agitators in Mixing Processes
An agitator serves as the driving force behind efficient mixing in a chemical mixing tank. Its primary role is to create motion within the tank, ensuring that all components blend uniformly. By generating controlled turbulence, the agitator prevents sedimentation and keeps particles suspended. This process guarantees a homogeneous mixture, which is essential for maintaining consistent product quality.
Agitators also enhance the dissolution of solids into liquids. For example, when you need to mix powders or granules with liquids, the agitator accelerates the process, saving time and energy. In addition, it ensures that immiscible liquids, such as oil and water, achieve a stable emulsion. This versatility makes agitators indispensable across various industries, from chemical manufacturing to food production.
“Agitators drastically reduce the risk of cross-contamination by streamlining the mixing process in single-use systems.” This feature is particularly beneficial in industries requiring strict hygiene standards, such as pharmaceuticals.
By understanding the role of agitators, you can appreciate their importance in achieving efficient and reliable mixing results.
Types of Agitators and Their Applications
Agitators come in various designs, each tailored to specific mixing needs. Choosing the right type depends on the materials you work with and the desired outcome. Here are some common types of agitators and their applications:
Propeller Agitators: These are ideal for low-viscosity liquids. They create axial flow, which moves materials vertically, ensuring rapid mixing. You often find them in industries like water treatment and beverage production.
Turbine Agitators: These are versatile and suitable for both low and high-viscosity fluids. They generate radial flow, which moves materials outward and then back toward the center. This design works well in chemical processing and pharmaceutical applications.
Paddle Agitators: These are best for gentle mixing. They are commonly used in food production, where maintaining the integrity of delicate ingredients is crucial.
Anchor Agitators: These are designed for high-viscosity materials. They scrape the tank walls to prevent buildup, making them perfect for mixing thick substances like creams or pastes.
Helical Ribbon Agitators: These are specialized for extremely viscous materials. They create a spiral motion, ensuring thorough mixing even in challenging conditions.
Each type of agitator offers unique advantages. By selecting the appropriate one, you can optimize your mixing tank’s performance and meet your specific processing requirements.
Factors Influencing Agitator Performance
Several factors determine how effectively an agitator performs in a mixing tank. Understanding these factors helps you maximize efficiency and achieve the desired results:
Tank Design: The shape and size of the mixing tank significantly impact the agitator’s performance. Baffled tanks, for instance, improve mixing efficiency by reducing vortex formation and ensuring better flow patterns.
Agitator Speed: The speed at which the agitator operates affects the mixing process. Higher speeds enhance turbulence, which is ideal for rapid blending. However, slower speeds are better for gentle mixing to avoid damaging sensitive materials.
Blade Design: The shape and angle of the agitator blades influence how materials move within the tank. Advanced blade designs, developed through extensive research, improve mixing precision and reduce processing time.
Material Properties: The viscosity and density of the materials being mixed play a crucial role. High-viscosity substances require more robust agitators, while low-viscosity liquids benefit from faster, lighter designs.
Mixing Time: The duration of mixing impacts the final product’s quality. Agitators equipped with technologies like RAM (Rapid Agitation Mechanism) drastically reduce mixing time. For example, RAM technology has been shown to cut batch processing time from 10.5 hours to just 30 minutes.
Efficient agitators not only save time but also reduce labor requirements. For instance, ingredient addition time can drop from 3.5 hours to just 2.5 minutes, simplifying operations and boosting productivity.
By considering these factors, you can ensure that your agitator operates at peak performance, delivering consistent and high-quality results.
Material Selection for Chemical Mixing Tanks with Agitators
Importance of Choosing the Right Tank Material
Selecting the right material for your mixing tank is crucial for ensuring durability and performance. The material directly impacts the tank’s ability to withstand the demands of industrial processes. For example, stainless steel is a popular choice due to its strength and resistance to wear. It provides a smooth surface that prevents contamination, making it ideal for industries like pharmaceuticals and food production.
The material also affects the efficiency of the agitator. A well-matched tank material ensures that the agitator operates without unnecessary strain, maintaining consistent mixing performance. Additionally, the right material minimizes the risk of chemical reactions between the tank and its contents. This compatibility is essential for preserving the integrity of your products.
“Research on agitation and heat exchange techniques has shown that optimizing tank materials enhances overall process efficiency.” This highlights the importance of careful material selection in achieving reliable results.
By choosing the appropriate material, you can ensure that your mixing tank meets industry standards and delivers consistent performance.
Corrosion Resistance for Chemical Compatibility
Corrosion resistance is a key factor when selecting a mixing tank material. Many industrial processes involve chemicals that can corrode standard materials, leading to equipment failure. Stainless steel, particularly grades like 316L, offers excellent resistance to corrosion. This makes it suitable for handling aggressive chemicals, including acids and alkalis.
A corrosion-resistant tank protects both the agitator and the contents of the tank. It prevents contamination caused by rust or material degradation, ensuring product purity. For example, in chemical manufacturing, a corrosion-resistant tank maintains the stability of sensitive formulations.
Advanced blade designs in agitators also benefit from corrosion-resistant materials. These designs ensure efficient mixing while reducing wear and tear, extending the lifespan of the equipment.
Investing in a corrosion-resistant mixing tank reduces maintenance costs and enhances the longevity of your equipment. It also ensures that your operations remain compliant with safety and quality regulations.
Longevity and Maintenance Considerations
The longevity of your mixing tank depends on the material you choose. Durable materials like stainless steel withstand the rigors of industrial use, providing a longer service life. They resist damage from mechanical stress, temperature fluctuations, and chemical exposure.
Maintenance requirements also decrease with high-quality materials. For instance, stainless steel tanks are easy to clean and maintain. Their non-porous surface prevents residue buildup, simplifying routine cleaning tasks. This reduces downtime and keeps your agitator functioning at peak efficiency.
Studies on agitation processes emphasize the importance of robust materials in minimizing maintenance needs. Tanks made from durable materials support the agitator’s performance, ensuring consistent results over time.
By prioritizing longevity and ease of maintenance, you can maximize the return on your investment. A well-maintained mixing tank with an efficient agitator ensures smooth operations and reliable output.
Compatibility of Chemical Mixing Tanks with Other Equipment
Integration with Pumps, Valves, and Sensors
Chemical mixing tanks with agitators must work seamlessly with other equipment to ensure smooth operations. Pumps, valves, and sensors play a critical role in maintaining the efficiency and precision of your processes. Proper integration of these components enhances the overall functionality of your system.
Pumps help transfer materials into and out of the tank. They ensure a steady flow rate, which is essential for maintaining consistent mixing. For example, centrifugal pumps are often used for low-viscosity liquids, while positive displacement pumps handle thicker substances. Choosing the right pump ensures that your tank operates without interruptions or delays.
Valves control the flow of materials, allowing you to regulate input and output with precision. Butterfly valves, for instance, provide quick and reliable shutoff, while ball valves offer excellent sealing capabilities. These features prevent leaks and spills, reducing the risk of costly exposures or environmental damage.
Sensors monitor critical parameters such as temperature, pressure, and liquid levels. They provide real-time data, enabling you to make adjustments as needed. For instance, temperature sensors ensure that heat-sensitive materials remain within safe limits. This level of control minimizes the chances of material failures, which could lead to environmental hazards or regulatory concerns.
“Proper integration of pumps, valves, and sensors not only improves efficiency but also enhances safety and compliance with industry standards.”
By ensuring compatibility between your mixing tank and these components, you can optimize performance and reduce the likelihood of operational issues.
Automation and Control Systems for Precision
Automation has revolutionized the way chemical mixing tanks operate. Modern control systems allow you to manage every aspect of the mixing process with precision. These systems eliminate manual errors, ensuring consistent results across batches.
Programmable logic controllers (PLCs) are commonly used to automate mixing operations. They enable you to set specific parameters such as mixing speed, duration, and temperature. Once programmed, the system executes these tasks automatically, freeing up your time for other responsibilities.
Advanced control systems also include features like remote monitoring. You can oversee operations from a distance, receiving alerts if any issues arise. For example, if a sensor detects an abnormal temperature, the system can automatically adjust the agitator speed or activate cooling mechanisms. This level of automation reduces downtime and prevents potential damage to your equipment.
Automation not only enhances precision but also improves scalability. It allows you to adapt your processes to meet changing production demands without compromising quality.
By incorporating automation and control systems, you can achieve greater accuracy, efficiency, and reliability in your mixing operations.
Scalability for Different Production Volumes
Scalability is a key consideration when selecting a chemical mixing tank with an agitator. Your equipment should adapt to varying production volumes, whether you’re handling small batches or large-scale operations. A scalable system ensures that you can meet customer demands without overextending your resources.
Modular designs make it easier to scale your operations. For instance, you can add or remove components like agitators, pumps, or sensors based on your production needs. This flexibility allows you to optimize your setup for maximum efficiency.
Larger tanks with high-capacity agitators are ideal for bulk production. They handle significant volumes without compromising mixing quality. On the other hand, smaller tanks are better suited for specialized applications or pilot projects. Choosing the right size ensures that your equipment operates efficiently, reducing energy consumption and material waste.
“Scalable systems not only improve operational efficiency but also reduce costs associated with upgrading or replacing equipment.”
By investing in a scalable mixing tank, you can future-proof your operations and maintain a competitive edge in your industry.
Applications of Chemical Mixing Tanks with Agitators Across Industries
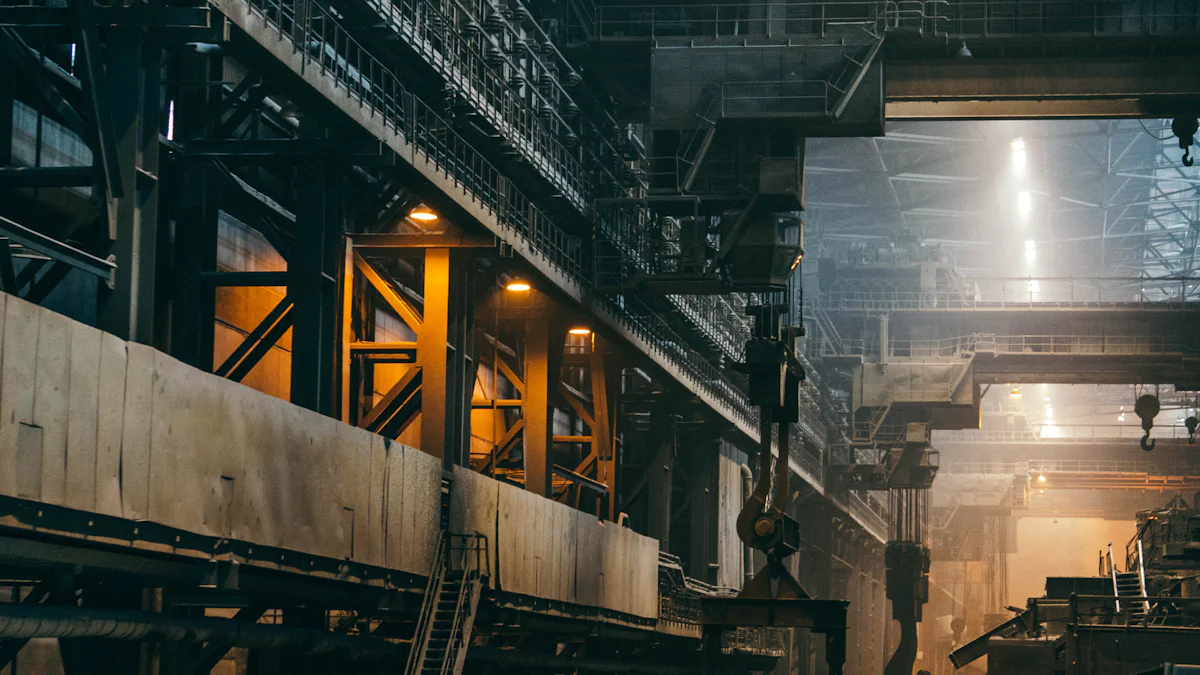
Chemical Manufacturing and Processing
In chemical manufacturing, precision and consistency are critical. A chemical mixing tank with an agitator ensures that every batch meets the required specifications. These tanks facilitate the uniform blending of raw materials, which is essential for producing high-quality chemicals. For example, when creating polymers or resins, the agitator prevents sedimentation and ensures a homogeneous mixture.
Agitator tanks also support processes like emulsification and dissolution. They help mix immiscible liquids, such as oil and water, into stable emulsions. This capability is vital for industries producing adhesives, paints, or coatings. Additionally, the controlled environment provided by these tanks minimizes the risk of unwanted chemical reactions, ensuring safety and reliability.
“Using chemical mixing tanks with agitators enhances the efficiency of chemical processing by reducing mixing time and improving product consistency.”
By incorporating these tanks into your operations, you can streamline production, reduce waste, and maintain compliance with industry standards.
Water Treatment and Waste Management
Water treatment facilities rely on chemical mixing tanks with agitators to ensure effective purification processes. These tanks play a crucial role in blending chemicals like coagulants, flocculants, and disinfectants into water. The agitator ensures that these substances disperse evenly, maximizing their effectiveness in removing impurities.
In waste management, agitator tanks assist in treating industrial effluents. They help mix neutralizing agents with hazardous waste, rendering it safe for disposal. For instance, in pH adjustment processes, the agitator ensures that acidic or alkaline substances mix thoroughly with neutralizing chemicals, achieving the desired balance.
The durability of these tanks, often made from corrosion-resistant materials like stainless steel, ensures long-term performance even in harsh environments. Their compatibility with dosing pumps and sensors allows for precise control over chemical addition, enhancing the efficiency of treatment processes.
“Agitator tanks in water treatment systems improve the quality of treated water while reducing operational costs and environmental impact.”
By using these tanks, you can contribute to sustainable water management and meet regulatory requirements with ease.
Food and Beverage Production
In the food and beverage industry, maintaining product quality and safety is paramount. Chemical mixing tanks with agitators ensure that ingredients blend uniformly, resulting in consistent flavors and textures. For example, in dairy production, agitators prevent cream separation, ensuring a smooth and homogenous product.
These tanks also support processes like fermentation and carbonation. In breweries or distilleries, agitators help mix yeast with wort or mash, promoting even fermentation. Similarly, in soft drink production, they ensure the uniform distribution of carbon dioxide, creating a balanced and refreshing beverage.
The use of stainless steel in these tanks provides a hygienic surface that resists contamination. This feature is particularly important in industries requiring strict adherence to food safety standards. Additionally, the ability to customize tank sizes and configurations allows you to adapt to varying production volumes.
“Agitator tanks in food and beverage production enhance efficiency, reduce waste, and ensure compliance with health regulations.”
By integrating these tanks into your processes, you can deliver high-quality products that meet customer expectations while optimizing operational efficiency.
Pharmaceutical and Cosmetic Industries
In the pharmaceutical and cosmetic industries, precision and consistency are non-negotiable. A chemical mixing tank with an agitator ensures that every formulation meets strict quality standards. These tanks provide a controlled environment for blending active ingredients, excipients, and other components, guaranteeing uniformity in every batch.
Key Applications in Pharmaceuticals
Formulation of Medicines: Agitator tanks play a critical role in mixing active pharmaceutical ingredients (APIs) with excipients. This ensures even distribution, which is essential for the efficacy and safety of medications. For example, in liquid syrups or suspensions, the agitator prevents sedimentation, maintaining a stable and homogenous mixture.
Sterile Mixing Processes: Pharmaceutical tanks are designed to meet stringent hygiene standards. Their stainless steel construction provides a non-porous surface, reducing the risk of contamination. Features like smooth welds and polished interiors make cleaning and sterilization easier, ensuring compliance with Good Manufacturing Practices (GMP).
Biopharmaceutical Production: In biopharmaceuticals, where cell cultures or enzymes are involved, agitators ensure gentle yet effective mixing. This prevents damage to delicate biological materials while promoting even nutrient distribution, which is vital for cell growth.
“Pharmaceutical tanks tailored to production lines ensure precise mixing and adherence to industry standards, making them indispensable for drug manufacturing.”
Key Applications in Cosmetics
Blending Creams and Lotions: Cosmetic products like creams, lotions, and serums require thorough mixing to achieve the desired texture and consistency. Agitators ensure that oils, water, and emulsifiers combine seamlessly, creating a smooth and stable emulsion.
Color and Fragrance Integration: In cosmetics, uniform distribution of colors and fragrances is crucial for product appeal. Agitator tanks facilitate this process, ensuring that every unit of product maintains the same quality and sensory experience.
High-Viscosity Mixing: Products like balms, gels, and pastes often have high viscosity. Agitators such as anchor agitators or helical ribbon agitators are specifically designed for these applications. They scrape the tank walls to prevent buildup, ensuring thorough mixing even in challenging conditions.
Benefits of Using Agitator Tanks in These Industries
Customizable Designs: Pharmaceutical and cosmetic tanks can be tailored to specific production needs. Features like customizable sizes, configurations, and accessories (e.g., platforms, ladders, and safety systems) enhance operational efficiency.
Corrosion Resistance: Stainless steel tanks resist corrosion, making them suitable for handling a wide range of chemicals used in these industries. This durability ensures long-term performance and reduces maintenance costs.
Precision Mixing: Advanced agitator designs, such as turbine agitators or paddle agitators, provide meticulous control over the mixing process. This precision is essential for achieving consistent product quality.
“Agitator tanks equipped with sensors and automation systems enable real-time monitoring, ensuring accuracy and reducing the risk of errors during production.”
By incorporating chemical mixing tanks with agitators into your pharmaceutical or cosmetic production line, you can achieve superior product quality, meet regulatory requirements, and optimize your operations. These tanks not only enhance efficiency but also ensure that your products consistently meet the high standards demanded by these industries.
Installation and Maintenance of Chemical Mixing Tanks with Agitators
Proper installation and maintenance of your chemical mixing tank with an agitator are essential for ensuring optimal performance and longevity. By following the right steps and adopting effective maintenance practices, you can maximize the efficiency of your equipment and minimize downtime.
Steps for Proper Installation
Installing a mixing tank with an agitator requires careful planning and execution. Follow these steps to ensure a smooth installation process:
Choose the Right Location
Select a stable and level surface for your mixing tank. Ensure the area has adequate ventilation and sufficient space for maintenance access. A well-chosen location prevents vibrations and ensures the agitator operates efficiently.Inspect the Equipment
Before installation, inspect the mixing tank and agitator for any visible damage or defects. Verify that all components, such as seals, blades, and motor connections, are in good condition. This step ensures the equipment is ready for use.Secure the Tank and Agitator
Anchor the mixing tank firmly to the ground to prevent movement during operation. Attach the agitator securely to the tank, ensuring proper alignment. Misalignment can lead to uneven mixing or damage to the agitator.Connect Power and Controls
Install the electrical connections for the agitator motor and control systems. Use a qualified technician to ensure compliance with safety standards. Test the power supply to confirm that the agitator operates at the correct speed.Calibrate the System
Adjust the agitator settings to match your specific mixing requirements. Set the speed, blade angle, and direction of rotation based on the viscosity and density of the materials you will mix. Calibration ensures precise and efficient mixing.
“Proper installation not only enhances the performance of your mixing tank but also reduces the risk of operational issues.”
By following these steps, you can set up your mixing tank and agitator for reliable and efficient operation.
Routine Maintenance Tips for Longevity
Regular maintenance keeps your mixing tank and agitator in top condition. Implement these tips to extend the lifespan of your equipment:
Clean the Tank and Agitator After Each Use
Residue buildup can affect mixing efficiency and contaminate future batches. Clean the tank and agitator thoroughly after every use. Use appropriate cleaning agents to remove stubborn residues without damaging the equipment.Inspect Moving Parts Regularly
Check the agitator blades, seals, and motor for wear and tear. Replace worn-out parts promptly to prevent further damage. Well-maintained components ensure consistent mixing performance.Lubricate Bearings and Joints
Apply lubrication to the agitator’s bearings and joints to reduce friction and prevent overheating. Use the recommended lubricant for your specific equipment model.Monitor Agitator Speed and Performance
Observe the agitator during operation to detect any unusual noises or vibrations. These signs may indicate misalignment or mechanical issues. Address problems immediately to avoid costly repairs.Schedule Professional Servicing
Arrange periodic inspections by a qualified technician. Professional servicing identifies hidden issues and ensures your mixing tank complies with industry standards.
“Routine maintenance not only improves the efficiency of your agitator but also minimizes downtime and repair costs.”
By adopting these practices, you can maintain the reliability and durability of your mixing tank and agitator.
Troubleshooting Common Issues
Even with proper maintenance, you may encounter occasional issues with your mixing tank and agitator. Here are some common problems and their solutions:
Uneven Mixing
If the agitator fails to mix materials uniformly, check the blade alignment and speed settings. Adjust the blade angle or increase the speed to improve mixing efficiency. Ensure the tank is not overloaded, as this can hinder agitation.Excessive Noise or Vibration
Unusual noises or vibrations often indicate loose components or misalignment. Tighten all bolts and ensure the agitator is properly aligned with the tank. Inspect the motor and bearings for damage.Overheating Motor
An overheating motor may result from excessive friction or inadequate lubrication. Check the bearings and apply lubricant as needed. Reduce the agitator speed if the motor is under excessive strain.Leaking Seals
Leaks around the agitator shaft can compromise the mixing process. Replace damaged seals immediately to prevent contamination or material loss. Use high-quality seals compatible with your tank’s material.Agitator Blade Damage
Damaged blades can reduce mixing efficiency and cause uneven blending. Inspect the blades regularly and replace them if necessary. Choose blades designed for your specific application to ensure optimal performance.
“Addressing issues promptly prevents minor problems from escalating into major disruptions.”
By troubleshooting effectively, you can keep your mixing tank and agitator running smoothly and maintain consistent results.
Environmental and Sustainability Benefits of Chemical Mixing Tanks with Agitators
Energy Efficiency in Mixing Processes
Energy efficiency is a critical factor in modern industrial operations. A chemical mixing tank equipped with an agitator optimizes energy use by ensuring precise and effective mixing. The advanced design of agitators minimizes the power required to achieve uniform blending. For instance, agitators in baffled tanks reduce vortex formation, which enhances mixing efficiency while consuming less energy.
Agitators also allow you to adjust speed settings based on the viscosity and density of the materials being mixed. This adaptability ensures that no excess energy is wasted during the process. For example, low-viscosity liquids require less agitation, which reduces power consumption. By using an agitator tailored to your specific needs, you can significantly lower your energy costs.
“Precision mixing tanks are equipped with advanced agitation systems that facilitate thorough and efficient blending.” This efficiency not only saves energy but also reduces the environmental impact of your operations.
By incorporating energy-efficient agitators into your mixing tank, you contribute to sustainable practices while maintaining high productivity.
Reduction of Waste and Resource Usage
Chemical mixing tanks with agitators play a vital role in reducing waste and optimizing resource usage. The precise mixing capabilities of agitators ensure that every particle of raw material is utilized effectively. This thorough blending minimizes material loss, which is especially important when working with expensive or sensitive ingredients.
Agitators prevent sedimentation and uneven distribution of materials. This feature ensures that no portion of the mixture goes unused or discarded due to poor quality. For example, in industries like pharmaceuticals or cosmetics, agitators maintain the consistency of high-viscosity products, reducing the need for reprocessing or disposal.
Additionally, the dual-purpose design of chemical mixing tanks—serving as both storage and mixing units—eliminates the need for separate equipment. This consolidation reduces the overall resource footprint of your operations. By using fewer tanks and agitators, you save on materials, space, and maintenance costs.
“Agitator tanks in water treatment systems improve the quality of treated water while reducing operational costs and environmental impact.” This demonstrates how efficient mixing processes can lead to sustainable outcomes across industries.
By reducing waste and maximizing resource utilization, you not only lower operational expenses but also support environmentally responsible practices.
Compliance with Environmental Regulations
Meeting environmental regulations is essential for any industrial operation. Chemical mixing tanks with agitators help you achieve compliance by ensuring controlled and efficient processes. Agitators prevent spills, leaks, and emissions during mixing, which reduces the risk of environmental contamination.
The use of corrosion-resistant materials, such as stainless steel, further enhances compliance. These materials prevent chemical reactions between the tank and its contents, ensuring that no harmful substances are released into the environment. For example, in water treatment facilities, agitators ensure the safe and effective mixing of neutralizing agents, which helps meet regulatory standards for effluent discharge.
Automation systems integrated into mixing tanks also play a crucial role in compliance. Sensors monitor parameters like temperature, pressure, and mixing speed, providing real-time data to ensure that processes remain within safe limits. This level of control minimizes the chances of regulatory violations.
“Proper integration of pumps, valves, and sensors not only improves efficiency but also enhances safety and compliance with industry standards.” This highlights the importance of using advanced technologies in achieving environmental goals.
By using chemical mixing tanks with agitators, you can align your operations with environmental regulations while maintaining efficiency and quality.
Customization Options for Chemical Mixing Tanks with Agitators
Key Factors to Consider When Selecting a Tank
Choosing the right chemical mixing tank with an agitator requires careful evaluation. The tank must align with your specific operational needs to ensure optimal performance. Several factors play a critical role in this decision-making process:
Material Compatibility: The tank material must resist corrosion and maintain compatibility with the chemicals you process. Stainless steel, for instance, is a popular choice due to its durability and resistance to chemical reactions. It also ensures hygiene, making it suitable for industries like pharmaceuticals and food production.
Tank Size and Capacity: The size of the tank should match your production volume. Oversized tanks may lead to inefficiencies, while undersized ones can cause bottlenecks. Assess your current and future production needs to select the appropriate capacity.
Agitator Type: Different agitators serve different purposes. For low-viscosity liquids, propeller agitators work well. High-viscosity materials, on the other hand, require anchor or helical ribbon agitators. Choosing the right agitator ensures efficient mixing and consistent results.
Operational Environment: Consider the conditions under which the tank will operate. Factors like temperature, pressure, and exposure to external elements influence the tank’s design and material requirements.
“Precision mixing tanks are crucial for achieving consistent mixtures in chemical reactions and maintaining high-quality production,” as noted by experts in chemical manufacturing. This highlights the importance of selecting a tank tailored to your specific processes.
By focusing on these key factors, you can ensure that your tank meets both operational and industry standards.
Customization Options for Specific Needs
Every industry has unique requirements, and customization allows you to tailor your mixing tank to meet those needs. Modern manufacturers offer a wide range of customization options to enhance functionality and efficiency:
Tank Design Adjustments
You can modify the tank’s shape, size, and configuration to suit your space and production demands. For example, vertical tanks save floor space, while horizontal tanks provide easier access for cleaning and maintenance.Agitator Blade Designs
Advanced blade designs improve mixing precision. You can choose from options like turbine blades for high-speed mixing or paddle blades for gentle agitation. These designs ensure thorough blending, even for challenging materials.Additional Features
Custom features like heating or cooling jackets, insulation, and pressure-resistant designs enhance the tank’s versatility. These features are particularly useful in industries requiring precise temperature control, such as chemical processing or brewing.Automation and Monitoring Systems
Integrating automation systems allows you to monitor and control the mixing process with precision. Sensors for temperature, pressure, and liquid levels provide real-time data, ensuring consistent results.Hygienic Finishes
For industries like pharmaceuticals and food production, hygienic finishes are essential. Polished interiors and smooth welds prevent contamination and simplify cleaning.
Experts in brewery and distillery operations emphasize the importance of hygiene and precision in maintaining consistent flavor profiles. Customizing your tank with these features ensures high-quality production.
Customization transforms a standard mixing tank into a specialized tool that meets your exact requirements. This flexibility enhances efficiency and ensures reliable performance across various applications.
Partnering with Reliable Manufacturers Like Chenma
Selecting the right manufacturer is as important as choosing the right tank. A reliable partner ensures that your equipment meets the highest standards of quality and performance. Shandong Chenma Machinery Co., Ltd. stands out as a trusted name in the industry.
Expertise in Stainless Steel Tanks
Chenma specializes in manufacturing stainless steel tanks designed for durability and efficiency. Their tanks are compatible with a wide range of chemicals and processes, making them ideal for diverse industries.Customization and Turnkey Solutions
Chenma offers extensive customization options to meet your specific needs. From tank design to agitator selection, their engineers work closely with you to create a solution tailored to your operations. They also provide turnkey projects, including process design, installation, and technical training.Certifications and Quality Standards
Chenma products comply with international safety and quality standards. Certifications like ISO9001, ISO14001, and EU CE ensure that their tanks meet stringent industry requirements.
“Our talented engineers adapt tanks to your unique situation daily,” states Chenma. This commitment to customization and innovation sets them apart as a reliable partner.
By partnering with Chenma, you gain access to high-quality, customized mixing tanks that enhance your operational efficiency. Their expertise and dedication to customer satisfaction make them a valuable ally in achieving your production goals.
Why Choose Chenma for Your Chemical Mixing Tank with Agitator
Expertise in Stainless Steel Tank Manufacturing
Chenma stands out as a leader in stainless steel tank manufacturing. With years of experience, the company has perfected the art of creating durable and efficient tanks. Stainless steel offers unmatched strength and resistance to wear, making it ideal for industrial applications. Chenma’s tanks are designed to handle the rigorous demands of mixing processes, ensuring long-lasting performance.
The company’s production facility spans over 20,000 square meters and houses state-of-the-art machinery. This advanced setup allows Chenma to produce even the most technically demanding designs. Whether you need a standard tank or a custom solution, Chenma’s expertise ensures that your equipment meets the highest standards of quality and reliability.
“Stainless steel tanks provide a smooth, non-porous surface that prevents contamination and ensures hygiene,” making them indispensable for industries like pharmaceuticals and food production.
By choosing Chenma, you gain access to tanks that not only meet but exceed industry expectations.
Customization and Turnkey Solutions
Every industry has unique requirements, and Chenma excels at providing tailored solutions. The company offers extensive customization options to ensure that your mixing tank aligns perfectly with your operational needs. From tank dimensions to agitator types, every detail can be adjusted to suit your specific processes.
Chenma also provides turnkey solutions, simplifying the entire process for you. These solutions include process design, equipment manufacturing, installation, and technical training. This comprehensive approach ensures that you receive a fully functional system ready for immediate use. For example, if your operation requires precise temperature control, Chenma can integrate heating or cooling jackets into your tank design.
“Our talented engineers adapt tanks to your unique situation daily,” says Chenma, highlighting their commitment to delivering personalized solutions.
By partnering with Chenma, you can streamline your operations and achieve greater efficiency with a system designed specifically for your needs.
Certifications and Quality Standards
Chenma prioritizes quality and safety in every product. The company’s tanks comply with international standards, ensuring reliable performance and peace of mind. Chenma holds certifications such as ISO9001 for quality management, ISO14001 for environmental management, and EU CE certification. These credentials demonstrate the company’s dedication to maintaining the highest standards in manufacturing.
The use of certified materials and processes guarantees that your mixing tank will perform consistently under demanding conditions. For instance, stainless steel tanks from Chenma resist corrosion, ensuring compatibility with a wide range of chemicals. This durability reduces maintenance costs and extends the lifespan of your equipment.
“Certifications like ISO9001 and CE ensure that products meet stringent industry requirements,” reinforcing Chenma’s reputation as a trusted manufacturer.
By choosing Chenma, you invest in equipment that adheres to global standards, ensuring both safety and efficiency in your operations.
A chemical mixing tank with agitator offers unmatched benefits, including uniform mixing, enhanced efficiency, and improved safety. These tanks ensure precise blending, which is essential for maintaining consistent product quality across industries like pharmaceuticals, food production, and chemical manufacturing. Their advanced agitation systems reduce processing time and optimize resource utilization, making them indispensable for industrial processes. By choosing Chenma, you gain access to high-quality, customizable solutions tailored to your specific needs. With their expertise and commitment to excellence, Chenma ensures your operations achieve maximum efficiency and reliability.
FAQ
What is the primary purpose of a chemical mixing tank with an agitator?
A chemical mixing tank with an agitator ensures uniform blending of materials. It prevents sedimentation and guarantees consistent product quality. These tanks are essential for industries requiring precise mixing, such as pharmaceuticals, food production, and chemical manufacturing.
“Chemical mixing tanks are primarily used for mixing or dipping chemical materials,” as noted by Filson Filters. This highlights their role in achieving homogeneity in various processes.
Why is stainless steel a preferred material for mixing tanks?
Stainless steel offers excellent corrosion resistance and durability. It withstands exposure to harsh chemicals and maintains compatibility with a wide range of substances. Its smooth, crevice-free surface prevents residue buildup, ensuring hygiene and easy cleaning. This makes it ideal for industries like food, beverage, and pharmaceuticals.
Cedarstone Industry emphasizes that stainless steel ensures high hygiene standards and prevents contamination, which is critical in sensitive applications.
How do agitators improve mixing efficiency?
Agitators create controlled motion within the tank, ensuring thorough blending of all components. They prevent sedimentation and keep particles suspended. Advanced designs, such as turbine or paddle blades, enhance mixing precision and reduce processing time.
According to industry insights, agitators equipped with advanced automation systems allow precise control over parameters like speed and chemical dosing, optimizing efficiency.
Can chemical mixing tanks be customized for specific needs?
Yes, chemical mixing tanks can be tailored to meet unique operational requirements. Customization options include tank size, agitator type, material selection, and additional features like heating jackets or automation systems. These adjustments ensure the tank aligns perfectly with your production goals.
Mass Tank specializes in custom tank solutions, offering flexibility to cater to diverse industries, from chemical processing to power plants.
What industries benefit most from chemical mixing tanks with agitators?
Chemical mixing tanks with agitators are versatile and serve various industries, including:
- Chemical Manufacturing: For blending raw materials and creating stable emulsions.
- Food and Beverage: For ensuring consistent flavors and textures.
- Pharmaceuticals: For precise formulation of medicines and sterile mixing.
- Water Treatment: For dispersing chemicals like coagulants and disinfectants.
Mass Tank highlights their use across industries like food service, water treatment, and pharmaceuticals, showcasing their adaptability.
How do these tanks contribute to environmental sustainability?
Chemical mixing tanks with agitators enhance energy efficiency by reducing power consumption during mixing. They minimize waste by ensuring thorough blending, which maximizes raw material usage. Their durable construction reduces the need for frequent replacements, lowering the environmental footprint.
Cedarstone Industry notes that precision mixing tanks optimize resource usage and maintain compliance with environmental standards.
What maintenance practices ensure the longevity of these tanks?
Regular cleaning after each use prevents residue buildup. Inspecting agitator blades, seals, and motor components ensures consistent performance. Lubricating moving parts reduces friction and wear. Scheduling professional servicing identifies hidden issues and keeps the tank in optimal condition.
Routine maintenance not only extends the lifespan of the equipment but also ensures reliable operation over time.
Are these tanks compatible with automation systems?
Yes, modern chemical mixing tanks integrate seamlessly with automation systems. Features like programmable logic controllers (PLCs) allow precise control over mixing speed, temperature, and duration. Sensors provide real-time data, enabling adjustments for consistent results.
Automation enhances scalability and precision, making these tanks suitable for both small-scale and large-scale operations.
How do agitators ensure safety when handling hazardous materials?
Agitators provide controlled mixing, reducing the risk of spills or dangerous reactions. Enclosed systems prevent exposure to harmful fumes, protecting operators and the environment. Corrosion-resistant materials like stainless steel further enhance safety by preventing chemical reactions with the tank.
Properly designed tanks and agitators ensure safe handling of volatile substances, meeting industry safety standards.
Why should you choose Chenma for your chemical mixing tank needs?
Chenma offers expertise in stainless steel tank manufacturing and provides extensive customization options. Their tanks meet international quality standards, including ISO9001 and EU CE certifications. With turnkey solutions, Chenma ensures a seamless process from design to installation.
“Our talented engineers adapt tanks to your unique situation daily,” states Chenma, emphasizing their commitment to delivering tailored solutions for your operations.