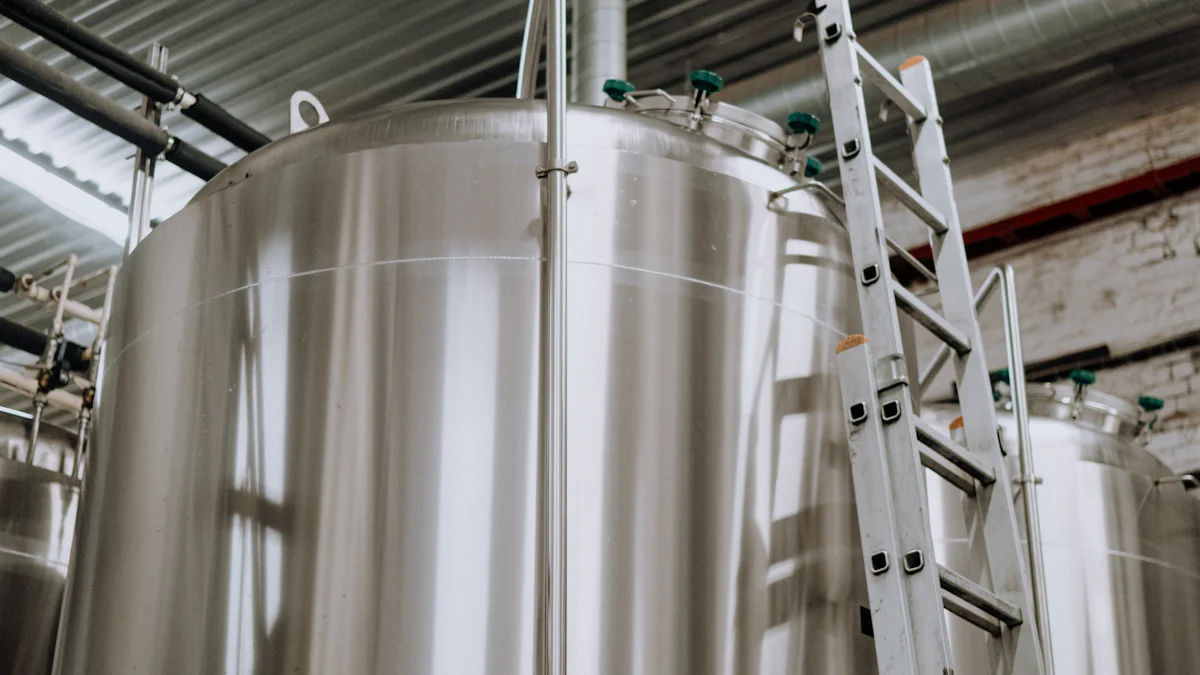
A chemical mixing tank with agitator is an essential tool in industries requiring accurate chemical blending. This equipment ensures uniform mixing and safety when managing chemical formulations, making it a vital component of industrial operations. The integration of the right chemical mixing tank with agitator boosts efficiency, lowers operational expenses, and ensures consistent product quality. Industries such as pharmaceuticals, food processing, and petrochemicals depend on these systems to optimize their processes. Choosing the ideal chemical mixing tank with agitator involves assessing factors like material compatibility, production capacity, and long-term reliability to meet both present demands and future goals.
Understanding Chemical Mixing Tanks and Industrial Agitators
What Are Chemical Mixing Tanks with Agitators?
Chemical mixing tanks with agitators are specialized equipment designed to blend, mix, or homogenize chemical substances efficiently. These tanks serve as controlled environments where industrial processes like fluid mixing, emulsification, and chemical reactions occur. The tank structure often includes a robust vessel paired with an agitator, which is a mechanical device that stirs or mixes the contents.
Industries such as pharmaceuticals, petrochemicals, and food processing rely heavily on these systems to ensure uniformity in their products. The agitator’s design and placement within the tank play a pivotal role in achieving the desired mixing outcomes. For instance, top-mounted agitators are common for general mixing, while side-entry agitators are preferred for specific applications like blending viscous fluids. The versatility of these tanks makes them indispensable in modern industrial operations.
The Importance of Industrial Agitators in Mixing Processes
Industrial agitators are the driving force behind efficient mixing processes. They ensure that all components within the tank are evenly distributed, preventing issues like sedimentation or uneven chemical reactions. By maintaining consistency, these devices enhance product quality and safety, which are critical in industries like pharmaceuticals and food production.
Agitators also optimize processing times by accelerating the blending of ingredients. For example, in chemical manufacturing, the right agitator can reduce reaction times, leading to faster production cycles. Additionally, they contribute to cost efficiency by minimizing energy consumption and reducing waste. A study on the Significance of Agitators in Industrial Mixers highlights how the correct agitator selection can lower operational costs while maintaining high-quality standards.
The adaptability of industrial agitators allows them to handle a wide range of tasks, from gentle mixing of delicate materials to vigorous agitation for heavy-duty applications. This flexibility ensures that businesses can meet diverse production requirements without compromising efficiency.
How the Right Tank and Agitator Combination Impacts Efficiency
The combination of a well-designed tank and an appropriate agitator significantly impacts operational efficiency. Tanks constructed from materials like stainless steel or fiberglass-reinforced plastic (FRP) provide durability and chemical resistance, ensuring longevity and safety. Pairing these tanks with the right agitator enhances their performance by addressing specific mixing needs.
For instance, paddle agitators are ideal for blending liquids with low viscosity, while turbine agitators excel in handling high-viscosity materials. The Importance of Choosing the Right Agitator for Processing Operations emphasizes that ingredient miscibility and process requirements should guide agitator selection. This tailored approach ensures optimal mixing, reduces downtime, and minimizes maintenance costs.
Moreover, the geometry of the tank, such as its shape and size, influences the agitator’s effectiveness. Cylindrical tanks with conical bottoms, for example, promote better flow patterns, allowing the agitator to work more efficiently. By aligning the tank design with the agitator type, industries can achieve consistent results, lower energy consumption, and improved product quality.
Types of Chemical Mixing Tank Models
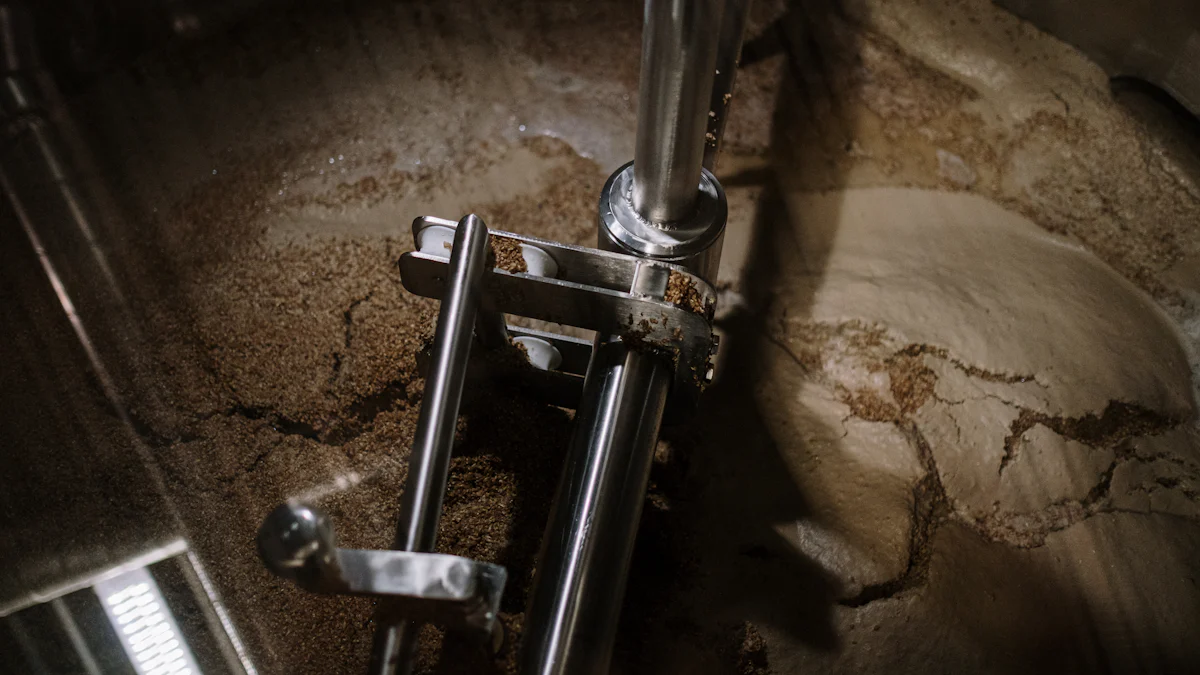
Chemical mixing tanks come in various designs and configurations, each tailored to specific industrial needs. Selecting the right model depends on factors such as the type of chemical being processed, the desired mixing outcome, and operational requirements. Below is an exploration of the different models based on tank design, agitator type, and material of construction.
Based on Tank Design
Cylindrical Tanks
Cylindrical tanks are among the most commonly used designs in industrial mixing. Their round shape promotes efficient fluid dynamics, ensuring uniform mixing throughout the tank. These tanks are ideal for processes requiring consistent agitation, such as emulsification or homogenization. The cylindrical structure also minimizes dead zones, allowing industrial agitators to operate at peak efficiency. Industries like pharmaceuticals and food processing often rely on cylindrical tanks for their versatility and ease of cleaning.
Conical Tanks
Conical tanks feature a cone-shaped bottom, which facilitates the complete drainage of contents. This design is particularly advantageous for applications involving viscous fluids or solids that settle during mixing. The conical bottom ensures that no residue remains, reducing waste and simplifying maintenance. These tanks pair well with high-quality agitators, which can handle the challenges of mixing thick or sediment-prone materials. Conical tanks are widely used in water treatment and chemical manufacturing due to their practicality and efficiency.
Rectangular Tanks
Rectangular tanks offer a unique solution for space-constrained environments. Their flat surfaces and angular design make them suitable for specific mixing tasks, such as blending powders or handling batch processes. While less common than cylindrical or conical tanks, rectangular tanks provide excellent adaptability for custom installations. Industrial agitators in these tanks often require precise placement to ensure thorough mixing. Industries with specialized requirements, such as adhesives or coatings production, frequently utilize rectangular tanks.
Based on Agitator Type
Paddle Agitators
Paddle agitators are simple yet effective tools for mixing low-viscosity liquids. Their flat blades create a gentle stirring motion, making them ideal for applications where minimal shear is required. These agitators excel in processes like blending water-based solutions or maintaining uniformity in large volumes. Paddle agitators are a cost-effective choice for industries seeking reliable performance without complex machinery.
Turbine Agitators
Turbine agitators are designed for moderate to high-viscosity fluids. Their radial blades generate intense mixing action, ensuring thorough dispersion of ingredients. These agitators are highly versatile, capable of handling tasks ranging from gas dispersion to emulsification. Turbine agitators are a staple in industries requiring robust mixing solutions, such as petrochemicals and paints. Their efficiency and adaptability make them a popular choice for demanding applications.
Helical Agitators
Helical agitators are engineered for high-viscosity materials and delicate processes. Their spiral-shaped blades create a smooth, continuous flow, reducing the risk of product degradation. These agitators are particularly effective in temperature-sensitive operations, such as pharmaceutical production or food processing. Helical agitators combine precision with power, delivering consistent results even in challenging conditions.
Based on Material of Construction
Stainless Steel Tanks
Stainless steel tanks are renowned for their durability and resistance to corrosion. They are the preferred choice for industries handling aggressive chemicals or requiring strict hygiene standards. Stainless steel’s non-reactive surface ensures product purity, making these tanks indispensable in pharmaceuticals, food processing, and biotechnology. Additionally, stainless steel tanks can withstand high temperatures and pressures, enhancing their versatility.
Polyethylene Tanks
Polyethylene tanks offer a lightweight and cost-effective alternative to metal tanks. Their resistance to corrosion makes them suitable for storing and mixing a wide range of chemicals. Polyethylene tanks are also compliant with regulatory standards, ensuring safe and secure operations. These tanks are commonly used in water treatment and sanitation industries, where chemical compatibility and ease of maintenance are critical.
Fiberglass-Reinforced Plastic (FRP) Tanks
FRP tanks combine strength with chemical resistance, making them ideal for harsh environments. Their lightweight construction simplifies installation and transportation, while their durability ensures long-term performance. FRP tanks are particularly effective in applications involving corrosive substances, such as acids or alkalis. Industries like petrochemicals and wastewater management benefit from the reliability and cost-efficiency of FRP tanks.
“The choice of tank design, agitator type, and material of construction directly impacts the efficiency and safety of chemical mixing processes.”
By understanding the unique features of each model, businesses can select the most suitable chemical mixing tank for their specific needs. Pairing the right tank with industrial agitators ensures optimal performance, reduced operational costs, and consistent product quality.
Based on Application
Batch Mixing Tanks
Batch mixing tanks are designed for processes that require precise control over mixing parameters. These tanks operate by processing a fixed quantity of materials in each cycle, making them ideal for industries where consistency and accuracy are critical. Industries such as pharmaceuticals, food production, and specialty chemicals often rely on batch mixing tanks to ensure uniformity in their products.
The design of batch mixing tanks allows operators to adjust variables like mixing speed, temperature, and duration for each batch. This flexibility ensures that the final product meets specific quality standards. For example, in pharmaceutical manufacturing, batch mixing tanks enable the precise blending of active ingredients to achieve the desired formulation. Similarly, in food processing, these tanks help maintain flavor consistency across different production cycles.
Batch mixing tanks often feature advanced agitator systems, such as paddle or turbine agitators, to handle a wide range of viscosities. Paddle agitators work well for low-viscosity liquids, while turbine agitators excel in dispersing high-viscosity materials. The ability to customize the agitator type based on the application enhances the tank’s versatility and efficiency.
“Batch mixing tanks provide unparalleled control over mixing processes, ensuring consistent results and high-quality outputs.”
These tanks also support compliance with industry-specific regulations. For instance, stainless steel batch mixing tanks meet stringent hygiene standards required in food and pharmaceutical industries. Their non-reactive surfaces prevent contamination, ensuring product safety and purity. Additionally, batch mixing tanks are easy to clean and maintain, reducing downtime and operational costs.
Continuous Mixing Tanks
Continuous mixing tanks are engineered for high-volume production environments where uninterrupted operation is essential. Unlike batch mixing tanks, these systems process materials continuously, allowing for a steady output of mixed products. Industries such as petrochemicals, water treatment, and large-scale chemical manufacturing benefit significantly from the efficiency of continuous mixing tanks.
The design of continuous mixing tanks focuses on maintaining a consistent flow of materials through the system. This approach minimizes variations in the final product, ensuring uniformity even in large-scale operations. For example, in water treatment facilities, continuous mixing tanks blend chemicals like coagulants and disinfectants to maintain water quality standards. Similarly, in petrochemical plants, these tanks facilitate the seamless mixing of additives into fuel or lubricants.
Continuous mixing tanks often incorporate high-efficiency agitators, such as helical or turbine designs, to handle demanding applications. Helical agitators are particularly effective for high-viscosity materials, creating a smooth and consistent flow. Turbine agitators, on the other hand, deliver robust mixing action for moderate to high-viscosity fluids, ensuring thorough dispersion of ingredients.
“Continuous mixing tanks streamline production processes, enabling businesses to meet high-demand requirements without compromising quality.”
These tanks also offer significant cost advantages. By eliminating the need for frequent stops and starts, continuous mixing tanks reduce energy consumption and operational expenses. Their durable construction, often using materials like stainless steel or fiberglass-reinforced plastic (FRP), ensures long-term reliability and resistance to corrosion. This durability makes them a practical choice for industries handling aggressive chemicals or operating in harsh environments.
Both batch and continuous mixing tanks play vital roles in industrial processes. The choice between the two depends on factors such as production volume, process requirements, and the need for flexibility or consistency. By selecting the appropriate tank type, businesses can optimize their operations, reduce costs, and achieve superior product quality.
Key Factors to Consider When Choosing a Chemical Mixing Tank with Agitator
Chemical Compatibility and Material Selection
Selecting the right chemical mixing tank with agitator begins with understanding the chemical properties of the materials involved. Chemicals vary in their reactivity, viscosity, and corrosiveness, which directly impacts the choice of tank material. For instance, stainless steel tanks are ideal for handling aggressive chemicals due to their corrosion resistance and durability. On the other hand, polyethylene tanks offer a cost-effective solution for less reactive substances, while fiberglass-reinforced plastic (FRP) tanks excel in environments with highly corrosive materials.
Material compatibility ensures the safety and longevity of the equipment. Using incompatible materials can lead to chemical reactions that compromise the tank’s structure or contaminate the product. For example, industries like pharmaceuticals and food processing prioritize stainless steel tanks to maintain product purity and comply with hygiene standards. Additionally, industrial agitators must also align with the chemical properties to avoid wear and ensure efficient mixing. Paddle agitators, for example, work well with low-viscosity liquids, while turbine agitators handle more viscous substances effectively.
“Choosing the right material for both the tank and agitator is critical to ensuring operational safety and product integrity.”
Tank Size, Capacity, and Agitator Power
The size and capacity of the tank play a pivotal role in determining its suitability for specific applications. Industries must assess their production volume and batch requirements to select an appropriately sized tank. For small-scale operations, compact tanks with lower capacities suffice, while large-scale industries require tanks capable of handling significant volumes. Headspace allowance is another crucial factor, as it prevents overflow during fluid mixing and ensures efficient agitation.
Agitator power must complement the tank size and the viscosity of the materials being mixed. Insufficient power can result in uneven mixing, while excessive power may damage delicate materials. For example, helical agitators are suitable for high-viscosity materials, providing smooth and consistent mixing without degrading the product. Conversely, paddle agitators are ideal for low-viscosity liquids, offering gentle yet effective agitation.
Industrial agitators must also be positioned correctly within the tank to maximize efficiency. Top-mounted agitators are versatile and commonly used for general mixing, while side-entry agitators are better suited for specific tasks like blending viscous fluids. The combination of the right tank size, capacity, and agitator power ensures optimal performance and minimizes energy consumption.
Temperature and Pressure Requirements
Temperature and pressure conditions significantly influence the choice of a chemical mixing tank with agitator. Certain processes, such as emulsification or gas-liquid dispersion, require tanks that can withstand extreme temperatures or pressures. Stainless steel tanks are often preferred for high-temperature applications due to their heat resistance and structural integrity. FRP tanks, on the other hand, are better suited for moderate temperature ranges and corrosive environments.
Pressure requirements also dictate the tank’s design and construction. Tanks used in high-pressure environments must feature reinforced walls and secure seals to prevent leaks or structural failure. For example, continuous mixing tanks in petrochemical plants often operate under high pressure to ensure consistent blending of additives into fuels. Industrial agitators must also be designed to function efficiently under these conditions, maintaining consistent mixing without compromising safety.
“Understanding the temperature and pressure requirements of your process ensures the longevity and reliability of the mixing system.”
By carefully evaluating these factors—chemical compatibility, tank size and capacity, and temperature and pressure requirements—industries can select a chemical mixing tank with agitator that meets their specific needs. This tailored approach enhances operational efficiency, reduces maintenance costs, and ensures consistent product quality.
Maintenance, Durability, and Long-Term Costs
Maintenance plays a critical role in ensuring the longevity and efficiency of chemical mixing tanks with agitators. Regular upkeep minimizes downtime and prevents costly repairs. Tanks constructed from durable materials, such as stainless steel or fiberglass-reinforced plastic (FRP), require less frequent maintenance due to their resistance to corrosion and wear. For example, stainless steel tanks excel in environments with aggressive chemicals, maintaining structural integrity over extended periods.
Durability directly impacts operational reliability. Tanks designed for high-pressure or high-temperature applications must withstand extreme conditions without compromising performance. FRP tanks, known for their lightweight yet robust construction, offer excellent durability in corrosive environments. Similarly, polyethylene tanks provide a cost-effective option for less demanding applications, though they may require more frequent inspections to ensure safety.
“Investing in durable materials reduces long-term costs by extending the lifespan of the equipment and lowering maintenance frequency.”
Long-term costs encompass more than just initial purchase expenses. Factors such as energy efficiency, repair frequency, and replacement intervals significantly influence overall expenditures. For instance, industrial agitators with energy-efficient designs reduce power consumption, leading to lower operational costs. Paddle agitators, ideal for low-viscosity liquids, consume less energy compared to turbine or helical agitators used for high-viscosity materials. Selecting the appropriate agitator type based on application needs ensures cost efficiency without sacrificing performance.
Businesses must also consider the ease of cleaning and maintenance when evaluating long-term costs. Tanks with smooth surfaces, such as those made from stainless steel, simplify cleaning processes and reduce labor requirements. Conical tanks, with their self-draining design, further enhance maintenance efficiency by preventing residue buildup. These features not only save time but also contribute to compliance with industry hygiene standards, particularly in sectors like food processing and pharmaceuticals.
Budget Considerations and Cost Efficiency
Budget constraints often dictate the choice of chemical mixing tanks and agitators. However, focusing solely on upfront costs can lead to higher expenses in the long run. A cost-efficient approach involves balancing initial investment with operational and maintenance costs. For example, while stainless steel tanks may have a higher purchase price, their durability and low maintenance requirements make them a more economical choice over time.
Polyethylene tanks offer a budget-friendly alternative for industries with less demanding chemical compatibility needs. These tanks provide adequate performance for applications like water treatment or sanitation, where cost efficiency is a priority. However, businesses must weigh the trade-offs, as polyethylene tanks may lack the durability required for aggressive chemicals or high-pressure environments.
“Cost efficiency stems from selecting equipment that aligns with both current needs and future scalability.”
Customization also influences budget considerations. Industries with unique mixing requirements often benefit from tailored solutions, such as tanks with specific agitator configurations or material enhancements. While custom designs may increase initial costs, they optimize performance and reduce inefficiencies, ultimately saving money in the long term. For instance, continuous mixing tanks with high-efficiency agitators streamline production processes, lowering energy consumption and labor costs.
Additionally, businesses should evaluate the total cost of ownership (TCO) when planning their budgets. TCO includes factors such as energy usage, maintenance expenses, and potential downtime. Tanks with advanced features, like IoT-enabled monitoring systems, may have higher upfront costs but provide significant savings through predictive maintenance and real-time performance optimization. By adopting a holistic view of costs, industries can make informed decisions that maximize value and ensure sustainable operations.
Common Applications of Chemical Mixing Tanks with Agitators
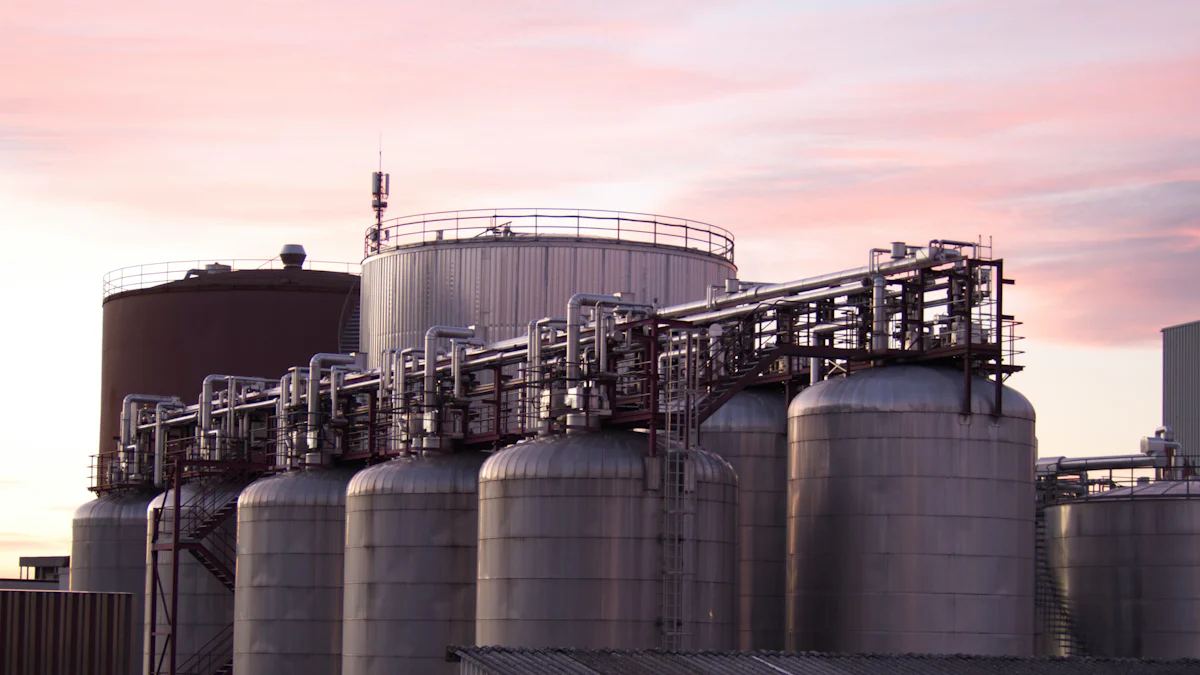
Food and Beverage Processing
Chemical mixing tanks with agitators play a vital role in food and beverage production. These tanks ensure the uniform blending of ingredients, which is essential for maintaining product consistency and quality. For example, in dairy processing, agitators help mix milk with additives like vitamins or flavoring agents. Similarly, in beverage manufacturing, they facilitate the even distribution of carbonation or syrups in soft drinks.
The use of stainless steel tanks dominates this industry due to their non-reactive surfaces and compliance with hygiene standards. These tanks prevent contamination and ensure the safety of consumable products. Additionally, the smooth interior surfaces of stainless steel tanks simplify cleaning and sterilization, reducing downtime between production cycles. Paddle agitators are often employed in this sector because they provide gentle mixing, preserving the texture and integrity of delicate ingredients.
“The food and beverage industry relies on chemical mixing tanks to achieve precise formulations and meet stringent regulatory requirements.”
The versatility of these tanks extends to applications like emulsifying sauces, homogenizing dairy products, and fermenting beverages such as wine or beer. Their ability to handle both low and high-viscosity materials makes them indispensable in this sector.
Pharmaceutical and Biotech Industries
In pharmaceutical and biotech industries, chemical mixing tanks with agitators ensure the precise formulation of medicines and biological products. These tanks support critical processes such as mixing active pharmaceutical ingredients (APIs), preparing suspensions, and creating emulsions. The accuracy and consistency provided by these systems are crucial for meeting stringent quality standards.
Stainless steel tanks are the preferred choice in this field due to their resistance to corrosion and ability to maintain product purity. The non-reactive nature of stainless steel prevents contamination, ensuring the safety and efficacy of pharmaceutical products. Helical agitators are commonly used in these applications because they provide smooth and consistent mixing, which is essential for handling high-viscosity materials like creams or gels.
Pharmaceutical mixing tanks often feature advanced temperature and pressure controls to support sensitive processes. For instance, the production of vaccines or biologics requires precise temperature regulation to preserve the stability of active ingredients. These tanks also comply with Good Manufacturing Practices (GMP), ensuring that they meet the industry’s rigorous safety and hygiene standards.
“Chemical mixing tanks with agitators are indispensable in pharmaceutical manufacturing, where precision and compliance are non-negotiable.”
Their applications extend to the preparation of intravenous solutions, the blending of cosmetic products, and the development of biotechnological innovations.
Water Treatment and Waste Management
Chemical mixing tanks with agitators are essential in water treatment and waste management processes. These tanks facilitate the blending of chemicals like coagulants, disinfectants, and pH adjusters, which are critical for treating water and wastewater. The even distribution of these chemicals ensures the removal of contaminants and the maintenance of water quality standards.
Polyethylene and fiberglass-reinforced plastic (FRP) tanks are widely used in this sector due to their resistance to corrosion and cost-effectiveness. These materials can withstand the harsh chemicals often used in water treatment, such as chlorine or sulfuric acid. Turbine agitators are frequently employed in these applications because they provide robust mixing action, ensuring thorough dispersion of chemicals in large volumes of water.
“Efficient chemical mixing is the backbone of wastewater treatment, enabling industries to meet environmental regulations and protect public health.”
In wastewater treatment, these tanks support processes like sludge conditioning, nutrient removal, and odor control. Continuous mixing tanks are particularly valuable in this field because they allow for uninterrupted operation, which is essential for handling high-volume treatment facilities. The durability and efficiency of these systems make them a cornerstone of modern water treatment and waste management practices.
Paints, Coatings, and Adhesives
Chemical mixing tanks with agitators play a pivotal role in the production of paints, coatings, and adhesives. These industries demand precise blending to achieve uniform consistency, color, and texture in their products. The tanks ensure that pigments, binders, solvents, and additives are thoroughly mixed, resulting in high-quality formulations that meet industry standards.
Stainless steel tanks dominate this sector due to their durability and resistance to corrosion. Their non-reactive surfaces maintain the integrity of chemical components, ensuring product stability. For example, in paint manufacturing, turbine agitators excel at dispersing pigments evenly, preventing clumping and sedimentation. This ensures that the final product delivers consistent coverage and color when applied.
Conical tanks also find extensive use in adhesive production. Their design facilitates complete drainage, which is essential for handling viscous materials like glues and sealants. Helical agitators, with their spiral blades, provide smooth and efficient mixing for these high-viscosity substances. This combination of tank design and agitator type enhances operational efficiency and minimizes material waste.
“The success of paints, coatings, and adhesives production hinges on the precision and reliability of chemical mixing systems.”
The versatility of these tanks extends to various applications, including the creation of water-based paints, solvent-based coatings, and industrial adhesives. By selecting the appropriate tank and agitator configuration, manufacturers can optimize their processes, reduce production costs, and deliver superior products to the market.
Petrochemical and Oil Refining
In petrochemical and oil refining industries, chemical mixing tanks with agitators are indispensable for blending additives, stabilizers, and other compounds into fuels and lubricants. These tanks ensure that the final products meet stringent performance and safety standards required in this sector.
Continuous mixing tanks are particularly valuable in large-scale petrochemical operations. Their ability to process materials without interruption supports high-volume production while maintaining consistency. Turbine agitators, known for their robust mixing action, effectively disperse additives in fuels, ensuring uniformity and stability. For example, in gasoline production, these agitators help blend octane enhancers seamlessly, improving fuel efficiency and performance.
Stainless steel tanks are the preferred choice for handling aggressive chemicals and high-temperature processes in oil refining. Their resistance to corrosion and structural integrity make them ideal for demanding environments. Additionally, fiberglass-reinforced plastic (FRP) tanks offer a lightweight yet durable alternative for specific applications, such as wastewater treatment within refineries. These tanks withstand harsh chemicals while providing cost-effective solutions for managing byproducts.
“The petrochemical and oil refining industries rely on advanced mixing systems to enhance product quality and operational efficiency.”
Temperature and pressure requirements often dictate the design of mixing tanks in this sector. Tanks equipped with reinforced walls and secure seals ensure safe operation under extreme conditions. By integrating the right tank material, agitator type, and operational features, businesses in this industry can achieve optimal performance, reduce downtime, and comply with environmental regulations.
Benefits of Using the Right Chemical Mixing Tank with Agitator
Enhanced Product Quality and Consistency
The right chemical mixing tank with an agitator ensures superior product quality by delivering uniform and precise mixing. Industrial agitators play a critical role in achieving this consistency. They evenly distribute components, preventing issues like sedimentation or uneven chemical reactions. For example, in fluid mixing processes, the agitator ensures that all ingredients are thoroughly blended, resulting in a homogeneous mixture. This uniformity is essential in industries like pharmaceuticals, where even minor inconsistencies can compromise product efficacy.
The tank’s material also impacts product quality. Stainless steel tanks, for instance, maintain the purity of sensitive materials due to their non-reactive surfaces. This feature is particularly valuable in food and beverage production, where contamination must be avoided. Additionally, the tank’s design, such as cylindrical or conical shapes, minimizes dead zones, allowing the agitator to perform efficiently. By selecting the right combination of tank and agitator, businesses can consistently produce high-quality outputs that meet industry standards.
“Consistency in mixing processes directly translates to enhanced product reliability and customer satisfaction.”
Improved Operational Efficiency
Operational efficiency improves significantly when the correct chemical mixing tank and agitator are used. Industrial agitators reduce processing times by accelerating blending and ensuring even distribution of materials. For instance, turbine agitators excel in high-viscosity applications, enabling faster mixing without compromising quality. This efficiency allows industries to meet production deadlines while maintaining cost-effectiveness.
The tank’s material and design also contribute to smoother operations. Tanks made from durable materials like fiberglass-reinforced plastic (FRP) resist corrosion, reducing the risk of equipment failure. Conical tanks, with their self-draining design, simplify cleaning and maintenance, minimizing downtime between production cycles. These features ensure that processes run seamlessly, even in demanding environments like chemical processing plants.
Moreover, advanced agitator designs, such as energy-efficient models, lower power consumption. This reduction in energy usage not only cuts operational costs but also aligns with sustainability goals. By investing in the right equipment, businesses can optimize their workflows, reduce waste, and achieve long-term operational success.
Reduced Maintenance and Downtime
The durability of the tank and agitator directly impacts maintenance requirements and operational downtime. Tanks constructed from robust materials, such as stainless steel or FRP, withstand harsh conditions and resist wear over time. This durability reduces the frequency of repairs and replacements, ensuring uninterrupted operations. For example, in chemical processing, tanks resistant to corrosion handle aggressive substances without degrading, extending their lifespan.
Industrial agitators designed for specific applications also minimize maintenance needs. Paddle agitators, ideal for low-viscosity liquids, operate with minimal strain, reducing wear and tear. Similarly, helical agitators handle high-viscosity materials smoothly, preventing mechanical stress. Proper alignment of the agitator with the tank’s design further enhances performance and reduces the likelihood of breakdowns.
Efficient maintenance practices, supported by the tank’s design, also play a role in reducing downtime. Tanks with smooth surfaces and easy-access features simplify cleaning and inspections. This ease of maintenance ensures that equipment remains in optimal condition, allowing businesses to focus on production rather than repairs.
“Investing in durable and efficient equipment reduces long-term costs and ensures consistent productivity.”
Compliance with Industry Standards and Regulations
Compliance with industry standards and regulations ensures the safety, efficiency, and reliability of chemical mixing tanks with agitators. Industries must adhere to these guidelines to maintain operational integrity and meet legal requirements. Regulatory bodies establish these standards to safeguard workers, protect the environment, and ensure product quality.
Chemical mixing tanks must meet material specifications outlined by organizations such as the American Society of Mechanical Engineers (ASME) or the Food and Drug Administration (FDA). For example, stainless steel tanks used in food and pharmaceutical industries must comply with FDA standards to prevent contamination. These tanks feature non-reactive surfaces that maintain product purity, ensuring consumer safety. Similarly, tanks designed for petrochemical applications must meet ASME pressure vessel codes to handle high-pressure environments safely.
“Adhering to material and design standards minimizes risks and enhances operational reliability.”
Ventilation systems also play a critical role in compliance. Tanks storing volatile chemicals, such as liquid fertilizers or pesticides, require proper ventilation to control air quality. Poor ventilation can lead to hazardous conditions, including the buildup of toxic fumes. Regulatory guidelines mandate the installation of advanced ventilation systems to mitigate these risks. Businesses that prioritize compliance reduce the likelihood of accidents and maintain a safer working environment.
Operational standards extend to the performance of industrial agitators. Agitators must meet specific criteria to ensure consistent mixing and prevent process failures. For instance, turbine agitators used in high-viscosity applications must demonstrate robust performance under varying conditions. Regulatory inspections often evaluate whether the agitator’s design aligns with the tank’s intended use, ensuring optimal functionality.
“Regulatory compliance in agitator design guarantees efficient mixing and reduces the risk of operational disruptions.”
Environmental regulations further influence tank and agitator selection. Industries handling corrosive chemicals must use materials like fiberglass-reinforced plastic (FRP) to prevent leaks and contamination. Compliance with environmental standards, such as those set by the Environmental Protection Agency (EPA), ensures that businesses minimize their ecological impact. For example, wastewater treatment facilities rely on FRP tanks to safely store and mix chemicals without harming surrounding ecosystems.
To achieve compliance, businesses should implement regular inspections and maintenance schedules. Tanks and agitators must undergo routine checks to identify wear, corrosion, or other issues that could compromise safety. Proactive maintenance not only ensures compliance but also extends the lifespan of the equipment, reducing long-term costs.
“Meeting industry standards is not just a legal obligation; it is a commitment to safety, quality, and sustainability.”
By adhering to these regulations, businesses enhance their reputation, avoid penalties, and build trust with stakeholders. Compliance serves as a foundation for operational excellence, ensuring that chemical mixing tanks with agitators perform reliably across diverse industrial applications.
Recommendations for Selecting the Best Chemical Mixing Tank with Agitator
Assessing Your Specific Needs and Applications
Selecting the right chemical mixing tank with agitator begins with a thorough evaluation of your operational requirements. Industries such as pharmaceuticals, food processing, and water treatment rely on these tanks to ensure product uniformity and safety. Each application demands specific features, including tank size, material, and agitator type. For instance, pharmaceutical processes often require stainless steel tanks to meet stringent hygiene standards, while water treatment facilities may benefit from polyethylene tanks due to their resistance to corrosive chemicals.
Understanding the nature of the materials being mixed is critical. Viscosity, chemical reactivity, and temperature sensitivity influence the choice of both the tank and the agitator. Paddle agitators work well for low-viscosity liquids, while helical agitators handle high-viscosity substances with precision. Additionally, industries must consider whether batch or continuous mixing suits their production needs. Batch mixing offers precise control over formulations, whereas continuous mixing supports high-volume operations with consistent output.
“The success of industrial processes hinges on selecting equipment tailored to specific applications.”
By aligning the tank and agitator features with operational goals, businesses can enhance efficiency, reduce waste, and maintain product quality.
Consulting with Manufacturers Like Chenma Machinery
Collaborating with experienced manufacturers ensures access to expert guidance and high-quality equipment. Companies like Chenma Machinery specialize in designing and producing chemical mixing tanks with agitators that cater to diverse industrial needs. Their expertise spans industries such as food and beverage, pharmaceuticals, and petrochemicals, making them a reliable partner for customized solutions.
Manufacturers provide valuable insights into material selection, tank design, and agitator configurations. For example, Chenma Machinery offers stainless steel tanks engineered to withstand high temperatures and pressures, ensuring durability and safety. Their team of skilled engineers adapts tank designs to meet unique requirements, whether for blending delicate pharmaceutical ingredients or mixing viscous adhesives.
“Partnering with reputable manufacturers guarantees access to cutting-edge technology and tailored solutions.”
Additionally, manufacturers often assist with installation, commissioning, and technical training. This support streamlines the integration of new equipment into existing processes, minimizing downtime and ensuring optimal performance. Businesses can also benefit from after-sales services, including maintenance and troubleshooting, to extend the lifespan of their investment.
Testing and Prototyping for Optimal Performance
Testing and prototyping play a crucial role in selecting the best chemical mixing tank with agitator. These processes allow businesses to evaluate equipment performance under real-world conditions, ensuring compatibility with specific applications. For instance, pharmaceutical companies may test tanks to verify their ability to maintain sterile environments, while chemical manufacturers assess agitator efficiency in blending reactive substances.
Prototyping provides an opportunity to identify potential issues and make adjustments before full-scale implementation. Manufacturers like Chenma Machinery often offer prototyping services, enabling clients to test various tank and agitator configurations. This approach ensures that the final product meets operational requirements and delivers consistent results.
“Prototyping reduces risks and enhances confidence in equipment performance.”
Testing also helps determine the energy efficiency and durability of the equipment. For example, energy-efficient agitators lower operational costs, while durable materials like stainless steel or fiberglass-reinforced plastic (FRP) ensure long-term reliability. By investing in testing and prototyping, businesses can make informed decisions, optimize their processes, and achieve superior outcomes.
Prioritizing Long-Term Value Over Initial Cost
Investing in a chemical mixing tank with an agitator requires careful consideration of long-term benefits rather than focusing solely on the initial purchase price. While upfront costs may seem like the most pressing factor, prioritizing long-term value ensures better operational efficiency, reduced maintenance expenses, and consistent product quality over time.
1. Durability and Material Selection
The choice of materials significantly impacts the lifespan and reliability of a mixing tank. Stainless steel tanks, for instance, offer exceptional durability and resistance to corrosion, making them ideal for industries handling aggressive chemicals or requiring strict hygiene standards. Fiberglass-reinforced plastic (FRP) tanks provide a lightweight yet robust alternative for environments with corrosive substances. Although these materials may come with a higher initial cost, their longevity minimizes the need for frequent replacements, reducing overall expenses.
“Mixing tanks play a key role in the pharmaceutical process by mixing and reacting drug raw materials, solutions, and preparations.” – Micet Craft
Industries like pharmaceuticals and food processing rely on stainless steel tanks to meet stringent quality and safety requirements. These tanks maintain product purity and ensure compliance with regulatory standards, offering long-term value that outweighs their initial investment.
2. Energy Efficiency and Operational Savings
Energy-efficient agitators contribute to significant cost savings over time. Advanced designs, such as turbine or helical agitators, optimize mixing processes while consuming less power. For example, turbine agitators excel in high-viscosity applications, ensuring thorough mixing without excessive energy use. This efficiency not only reduces operational costs but also aligns with sustainability goals, making it a valuable investment for environmentally conscious businesses.
“Agitator tanks play a huge role in various industries, simplifying processes like mixing, blending, and chemical reactions.” – Allwin Grinding
By selecting energy-efficient equipment, industries can streamline their operations and achieve consistent results while minimizing their environmental footprint.
3. Reduced Maintenance and Downtime
Durable materials and well-designed agitators reduce the frequency of maintenance and repairs. Tanks constructed from stainless steel or FRP resist wear and corrosion, ensuring reliable performance even in demanding environments. Paddle agitators, ideal for low-viscosity liquids, operate with minimal strain, while helical agitators handle high-viscosity materials smoothly, preventing mechanical stress.
“Chemical mixing tanks are fundamental in the production of sanitation detergents, medicines, or water treatment chemicals in any industries.” – Ace Stills
Efficient maintenance practices, supported by durable equipment, minimize downtime and extend the lifespan of the system. This reliability translates into uninterrupted production cycles and lower long-term costs.
4. Scalability and Future-Proofing
Investing in a mixing tank that accommodates future growth ensures scalability and adaptability. Continuous mixing tanks, for example, support high-volume production environments, making them suitable for industries anticipating increased demand. Customizable features, such as advanced agitator configurations or IoT-enabled monitoring systems, enhance the tank’s versatility and performance.
“Mixing tanks are used in chemical process systems to mix multiple liquid components together to create new compounds or products.” – Applied Chemical Technology
By planning for future needs, businesses can avoid the expense of replacing or upgrading equipment prematurely, maximizing the return on their investment.
5. Total Cost of Ownership (TCO)
Evaluating the total cost of ownership provides a comprehensive understanding of long-term value. TCO includes factors such as energy consumption, maintenance expenses, and potential downtime. While a lower-cost tank may seem appealing initially, it often incurs higher operational and repair costs over time. Conversely, investing in high-quality equipment reduces these hidden expenses, ensuring cost efficiency in the long run.
“The success of industrial processes hinges on selecting equipment tailored to specific applications.”
By prioritizing long-term value over initial cost, businesses can achieve sustainable operations, enhance productivity, and maintain consistent product quality. This strategic approach ensures that the investment in a chemical mixing tank with an agitator delivers lasting benefits across diverse industrial applications.
Common Mistakes to Avoid When Choosing a Model
Overlooking Material Compatibility and Agitator Design
Material compatibility plays a critical role in the performance and longevity of chemical mixing tanks. Many businesses fail to consider how the tank material interacts with the chemicals being processed. For example, stainless steel tanks are highly durable and resistant to corrosion, making them ideal for aggressive chemicals. However, polyethylene tanks offer a cost-effective alternative for less reactive substances and excel in environments with sudden temperature changes. Poly tanks, known for their non-reactive properties, are particularly effective when handling acids with high corrosive potential.
“Poly tanks are excellent choices for storing chemicals. They do not react with acids with high corroding potential, demonstrate exceptional durability, and resist sudden temperature changes.”
Ignoring the importance of agitator design can also lead to inefficiencies. Paddle agitators work well for low-viscosity liquids, while turbine agitators handle moderate to high-viscosity materials. Helical agitators, with their spiral blades, are better suited for delicate or high-viscosity processes. Selecting an incompatible agitator can result in uneven mixing, increased energy consumption, or even damage to the tank. Businesses must align the agitator type with the specific requirements of their application to ensure optimal performance.
Underestimating Capacity and Power Requirements
Choosing a tank with insufficient capacity often disrupts production processes. Businesses must evaluate their current and future production needs to select a tank that accommodates both. For instance, small-scale operations may require compact tanks, while large-scale industries benefit from high-capacity models. Failing to account for headspace allowance can also lead to overflow issues during mixing, reducing efficiency and increasing waste.
Agitator power is another commonly underestimated factor. The power of the agitator must match the viscosity of the materials being mixed. Low-power agitators may struggle with high-viscosity substances, leading to incomplete mixing. Conversely, overpowered agitators can damage delicate materials or increase operational costs unnecessarily. Properly assessing the power requirements ensures consistent mixing and prevents equipment strain.
“Most often than not, the walls of a chemical tank mixer are made of stainless steel material, which is strong, non-corrosive, and simple in terms of cleaning. However, depending on the use of the tank, polyethylene and other specialized materials may be used.”
Businesses should also consider scalability when evaluating capacity and power requirements. Tanks designed for future growth reduce the need for frequent upgrades, saving time and resources in the long term.
Focusing Solely on Cost Without Considering Long-Term Value
Many businesses prioritize upfront costs when selecting a chemical mixing tank, overlooking the long-term value of their investment. While lower-cost options like polyethylene tanks may seem appealing initially, they may lack the durability required for demanding applications. Stainless steel tanks, though more expensive, offer superior longevity and resistance to corrosion, reducing maintenance and replacement costs over time.
“Plastic tanks are often preferred for chemical mixing due to their compliance with regulatory requirements and safety standards.”
Energy efficiency is another aspect often ignored when focusing solely on cost. Advanced agitator designs, such as turbine or helical models, optimize mixing processes while consuming less power. This reduces operational expenses and aligns with sustainability goals. Businesses committed to reducing their environmental footprint often find energy-efficient equipment a compelling choice.
“Businesses that are committed to sustainable practices and reducing their environmental footprint are likely to find plastic tanks a compelling choice for chemical mixing.”
Additionally, neglecting the total cost of ownership (TCO) can lead to unforeseen expenses. TCO includes factors like energy consumption, maintenance, and downtime. Investing in high-quality equipment with durable materials and efficient designs minimizes these hidden costs, ensuring long-term savings and operational reliability.
Key Takeaway: Prioritizing long-term value over initial cost ensures better performance, reduced maintenance, and consistent product quality.
Ignoring Maintenance and Durability Factors
Overlooking maintenance and durability considerations often leads to increased operational costs and unexpected downtime. Chemical mixing tanks and agitators must endure harsh conditions, including exposure to corrosive chemicals, extreme temperatures, and high pressures. Neglecting these factors can compromise the equipment’s performance and lifespan, ultimately affecting production efficiency.
Importance of Durable Materials
The choice of tank material significantly impacts its durability and maintenance requirements. Stainless steel remains a popular option due to its strength, corrosion resistance, and ease of cleaning. Its non-reactive surface ensures compatibility with aggressive chemicals, making it ideal for industries like pharmaceuticals and food processing.
“Most often than not, the walls of a chemical tank mixer are made of stainless steel material, which is strong, non-corrosive, and simple in terms of cleaning.”
Polyethylene tanks, on the other hand, offer a lightweight and cost-effective alternative. These tanks resist sudden temperature changes and do not react with highly corrosive acids, ensuring long-term reliability in less demanding applications. Businesses committed to sustainability often favor polyethylene tanks for their environmental benefits and compliance with safety standards.
“Poly tanks are excellent choices for storing chemicals. They do not react with acids with high corroding potential, demonstrate exceptional durability, and resist sudden temperature changes.”
Fiberglass-reinforced plastic (FRP) tanks provide another durable option, particularly for environments involving highly corrosive substances. Their lightweight construction simplifies installation, while their robust design ensures longevity in challenging conditions.
Role of Maintenance in Longevity
Regular maintenance is essential to preserve the functionality and safety of chemical mixing tanks. Tanks constructed from durable materials, such as stainless steel or FRP, require less frequent repairs, reducing downtime and operational disruptions. Smooth surfaces, like those found in stainless steel tanks, simplify cleaning processes, ensuring compliance with hygiene standards in industries like food and beverage production.
“Plastic tanks are often preferred for chemical mixing due to their compliance with regulatory requirements and safety standards.”
Ignoring maintenance schedules can lead to issues such as material degradation, leaks, or contamination. For example, failing to inspect seals and joints in high-pressure tanks may result in structural failures, posing safety risks and halting production. Proactive maintenance practices, including routine inspections and timely repairs, mitigate these risks and extend the equipment’s lifespan.
Balancing Cost and Durability
While initial costs may influence purchasing decisions, prioritizing durability reduces long-term expenses. Tanks made from high-quality materials withstand wear and tear, minimizing the need for replacements. Energy-efficient agitators also contribute to cost savings by reducing power consumption during operation.
“Businesses that are committed to sustainable practices and reducing their environmental footprint are likely to find plastic tanks a compelling choice for chemical mixing.”
Investing in durable equipment ensures consistent performance, lowers maintenance costs, and enhances operational reliability. By addressing maintenance and durability factors, businesses can optimize their processes, safeguard their investments, and achieve long-term success.
Trends and Innovations in Chemical Mixing Tanks and Industrial Agitators
Smart Tanks with IoT Integration for Real-Time Monitoring
The integration of IoT (Internet of Things) technology into chemical mixing tanks has revolutionized industrial operations. Smart tanks equipped with IoT sensors provide real-time monitoring of critical parameters such as temperature, pressure, and mixing speed. This innovation allows operators to track performance remotely, ensuring precise control over the mixing process.
IoT-enabled tanks enhance operational efficiency by identifying potential issues before they escalate. For instance, sensors can detect irregularities in agitator performance or fluctuations in tank pressure, prompting immediate corrective actions. This proactive approach minimizes downtime and reduces maintenance costs. Additionally, real-time data collection supports predictive maintenance, extending the lifespan of equipment and improving overall reliability.
“IoT integration transforms chemical mixing tanks into intelligent systems, enabling businesses to optimize processes and maintain consistent product quality.”
Industries benefit from the ability to customize IoT features based on specific needs. For example, pharmaceutical manufacturers can monitor sterile conditions, while petrochemical plants can track the blending of volatile substances. The adaptability of smart tanks ensures their relevance across diverse applications, making them a cornerstone of modern industrial practices.
Energy-Efficient Agitator Designs for Sustainability
Energy efficiency has become a priority in the design of industrial agitators. Manufacturers now focus on creating agitators that deliver optimal performance while consuming less power. This shift aligns with global sustainability goals and helps industries reduce operational costs.
Advanced agitator designs, such as turbine and helical models, maximize mixing efficiency with minimal energy input. Turbine agitators excel in high-viscosity applications, ensuring thorough blending without excessive power usage. Helical agitators, with their spiral blades, create smooth and consistent flows, reducing mechanical strain and energy consumption. These innovations cater to industries seeking to balance productivity with environmental responsibility.
“Energy-efficient agitators not only lower operational expenses but also contribute to a greener and more sustainable future.”
Variable speed drives further enhance energy efficiency by allowing operators to adjust mixing speeds based on product viscosity. This flexibility ensures that the agitator operates at optimal levels, preventing energy wastage. For example, low-viscosity liquids require gentle stirring, while high-viscosity materials demand more robust agitation. By tailoring the speed to specific needs, industries achieve better quality control and versatility in processing.
Advanced Materials for Corrosion Resistance
The development of advanced materials has significantly improved the durability and performance of chemical mixing tanks. Corrosion-resistant materials, such as stainless steel and fiberglass-reinforced plastic (FRP), ensure the longevity of tanks exposed to harsh chemicals and extreme conditions.
Stainless steel remains a popular choice due to its strength and non-reactive properties. It resists corrosion, maintains structural integrity, and complies with hygiene standards, making it ideal for industries like pharmaceuticals and food processing. FRP tanks offer a lightweight yet robust alternative, excelling in environments with highly corrosive substances. Their durability simplifies maintenance and reduces long-term costs.
“The use of advanced materials enhances the safety and reliability of chemical mixing tanks, ensuring consistent performance in demanding environments.”
Recent advancements in plastic tank design have also expanded their applications. Modern plastic tanks demonstrate exceptional durability and versatility, making them suitable for a wide range of chemical mixing processes. These tanks resist sudden temperature changes and maintain stability under challenging conditions, providing a cost-effective solution for industries with less aggressive chemical requirements.
By leveraging these material innovations, businesses can select tanks that align with their operational needs, ensuring efficiency and safety across various applications.
Modular and Customizable Tank Designs for Versatility
Modular and customizable tank designs have revolutionized the chemical mixing industry by offering unparalleled flexibility and adaptability. These tanks cater to the diverse needs of industries such as pharmaceuticals, food processing, and petrochemicals, where unique operational requirements demand tailored solutions. By integrating modular components and customizable features, businesses can optimize their processes, reduce costs, and enhance efficiency.
Advantages of Modular Tank Designs
Modular tank designs allow industries to adapt their equipment to evolving production demands. These tanks consist of interchangeable components, enabling operators to modify or expand the system without replacing the entire unit. This approach provides several key benefits:
- Scalability: Modular tanks support future growth by allowing businesses to increase capacity or add new features as production needs evolve. For example, a company can integrate additional mixing chambers or agitator configurations to handle higher volumes.
- Ease of Maintenance: Interchangeable parts simplify repairs and replacements, reducing downtime and maintenance costs. Operators can replace worn components without disrupting the entire system.
- Cost Efficiency: Modular designs minimize initial investment by enabling businesses to purchase only the necessary components. As needs change, additional modules can be added incrementally, spreading out costs over time.
“Modular tanks provide a cost-effective solution for industries anticipating growth or requiring frequent adjustments to their processes.”
The Role of Customization in Enhancing Efficiency
Customization plays a critical role in meeting industry-specific requirements. Different sectors have unique mixing needs based on product characteristics, regulatory standards, and operational goals. Customizable tanks address these challenges by offering tailored solutions that improve efficiency and product quality.
Tailored Agitator Configurations
Custom agitator designs ensure optimal mixing for specific applications. Paddle agitators work well for low-viscosity liquids, while turbine agitators handle high-viscosity materials with precision. Helical agitators, known for their spiral blades, excel in delicate processes requiring smooth and consistent flows.Material Selection
Custom tanks allow businesses to choose materials that align with their chemical compatibility needs. Stainless steel tanks offer durability and corrosion resistance, making them ideal for aggressive chemicals. Polyethylene tanks provide a lightweight and cost-effective option for less reactive substances, while fiberglass-reinforced plastic (FRP) tanks excel in highly corrosive environments.Variable Speed Drives
Tanks equipped with variable speed drives enhance versatility by allowing operators to adjust mixing speeds based on product viscosity. This feature ensures better quality control and efficiency across a wide range of materials. For instance, low-viscosity liquids require gentle stirring, while high-viscosity substances demand robust agitation.
“Custom chemical mixing tanks enable industries to advance efficiency and reduce operational costs while adhering to client-specific regulatory guidelines.”
Applications of Modular and Customizable Tanks
Industries benefit significantly from the versatility of modular and customizable tank designs. These tanks simplify processes like mixing, blending, and chemical reactions, ensuring consistency, quality, and safety. Key applications include:
- Pharmaceuticals: Custom tanks meet stringent hygiene standards and support precise formulations of medicines and biologics.
- Food Processing: Modular designs accommodate varying batch sizes and ingredient combinations, ensuring consistent product quality.
- Petrochemicals: Customizable tanks handle high-pressure and high-temperature environments, blending additives seamlessly into fuels and lubricants.
Future Trends in Modular and Customizable Tanks
The demand for modular and customizable tanks continues to grow as industries prioritize flexibility and efficiency. Advancements in design and production have led to more durable and versatile tanks. For example, modern plastic tanks demonstrate exceptional durability and adaptability, making them suitable for a wide range of chemical mixing processes.
IoT integration further enhances the functionality of these tanks. Smart sensors monitor parameters like temperature, pressure, and mixing speed in real-time, enabling operators to make data-driven adjustments. This innovation supports predictive maintenance, reduces downtime, and ensures consistent performance.
“The increasing demand for customization reflects the need for mixing tanks that align with specific process requirements and improve production efficiency.”
By investing in modular and customizable tank designs, businesses can future-proof their operations, achieve superior results, and maintain a competitive edge in their industries.
Selecting the right chemical mixing tank with agitator ensures operational efficiency and product quality across industries. Businesses must evaluate application-specific needs, including material compatibility and production requirements, to make informed decisions. Custom designs tailored to unique processes enhance efficiency and reduce costs, while compliance with regulatory standards guarantees safety and reliability. Collaborating with trusted manufacturers like Chenma Machinery provides access to expert guidance and high-quality solutions. By prioritizing long-term value and adaptability, industries can optimize their operations and achieve consistent results.
FAQ
What factors should industries consider when selecting a chemical mixing tank with an agitator?
Industries should evaluate their specific needs, including the type of chemicals being processed, production volume, and operational goals. Material compatibility is critical. For example, stainless steel suits aggressive chemicals, while polyethylene works well for less reactive substances. Tank size and agitator type must align with the viscosity of materials and mixing requirements. Cost-effectiveness and long-term durability also play a significant role in decision-making.
“Selecting the right tank and agitator ensures operational efficiency and product quality,” emphasizes Chenma Machinery, a leading manufacturer in the field.
How does the choice of agitator impact mixing efficiency?
The agitator type directly influences the mixing process. Paddle agitators provide gentle stirring for low-viscosity liquids. Turbine agitators handle moderate to high-viscosity materials with robust action. Helical agitators excel in high-viscosity or delicate processes, ensuring smooth and consistent mixing. Choosing the correct agitator ensures uniform blending, reduces energy consumption, and prevents product degradation.
Why is material compatibility important for chemical mixing tanks?
Material compatibility ensures the safety and longevity of the tank. Incompatible materials can lead to chemical reactions, structural damage, or contamination. Stainless steel offers corrosion resistance and durability for aggressive chemicals. Polyethylene provides a cost-effective option for less reactive substances. Fiberglass-reinforced plastic (FRP) excels in environments with highly corrosive chemicals. Selecting the right material protects both the equipment and the product.
What are the advantages of stainless steel tanks?
Stainless steel tanks offer exceptional durability, corrosion resistance, and compliance with hygiene standards. These tanks maintain product purity, making them ideal for industries like pharmaceuticals and food processing. They withstand high temperatures and pressures, ensuring reliability in demanding environments. Additionally, their smooth surfaces simplify cleaning and maintenance, reducing downtime.
How do batch and continuous mixing tanks differ?
Batch mixing tanks process a fixed quantity of materials per cycle, offering precise control over mixing parameters. These tanks suit industries requiring consistency, such as pharmaceuticals and specialty chemicals. Continuous mixing tanks operate without interruption, supporting high-volume production. They ensure steady output and uniformity, making them ideal for petrochemicals and water treatment facilities.
What role does tank size play in the selection process?
Tank size determines the system’s capacity to meet production demands. Small-scale operations benefit from compact tanks, while large-scale industries require high-capacity models. Adequate headspace prevents overflow during mixing. Selecting the right size ensures efficient operations and accommodates future growth.
How can businesses ensure long-term cost efficiency when choosing a tank?
Long-term cost efficiency involves balancing initial investment with operational and maintenance expenses. Durable materials like stainless steel reduce repair and replacement costs. Energy-efficient agitators lower power consumption. Modular designs allow for scalability, minimizing the need for frequent upgrades. Evaluating the total cost of ownership (TCO) ensures sustainable operations.
What maintenance practices extend the lifespan of chemical mixing tanks?
Regular inspections and cleaning prevent material degradation and contamination. Tanks with smooth surfaces, such as stainless steel, simplify maintenance. Proactive practices, including checking seals and joints, reduce the risk of leaks or structural failures. Durable materials like FRP and stainless steel require less frequent repairs, ensuring consistent performance.
How do IoT-enabled tanks improve industrial operations?
IoT-enabled tanks provide real-time monitoring of parameters like temperature, pressure, and mixing speed. This technology allows operators to track performance remotely and identify potential issues early. Predictive maintenance reduces downtime and extends equipment lifespan. IoT integration enhances efficiency and ensures consistent product quality.
Why should businesses consult manufacturers like Chenma Machinery?
Collaborating with experienced manufacturers ensures access to tailored solutions and expert guidance. Chenma Machinery specializes in designing chemical mixing tanks with agitators for diverse industries. Their expertise includes material selection, tank customization, and agitator configurations. They also provide installation, commissioning, and technical support, ensuring seamless integration into existing processes.
“Partnering with trusted manufacturers guarantees high-quality equipment and long-term reliability,” advises Chenma Machinery.