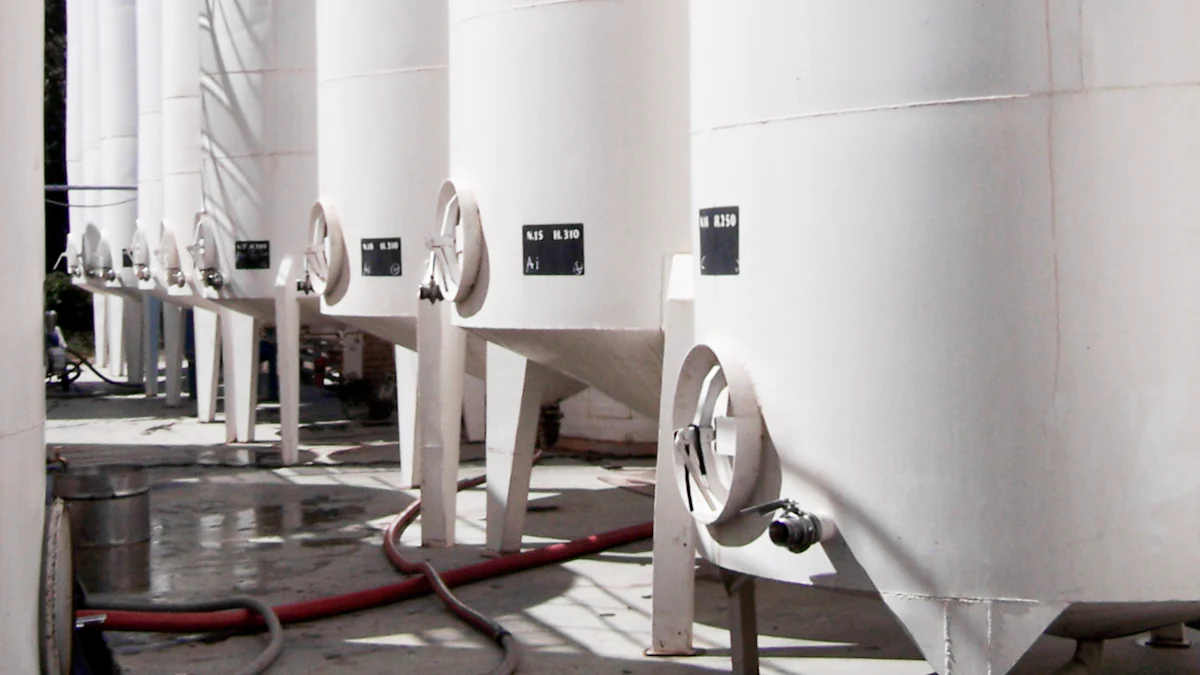
Understanding the price of chemical mixing tanks for sale is essential for making smart purchasing decisions. Prices can range from a few hundred dollars for smaller tanks to tens of thousands for industrial-grade options. You need to evaluate costs carefully to ensure you get the best value. Striking the right balance between cost, quality, and functionality helps you optimize your investment. High-quality tanks may seem expensive initially, but they often provide long-term savings through durability and efficiency. By focusing on value rather than just price, you can achieve both performance and cost-effectiveness.
Price Ranges for Chemical Mixing Tanks for Sale
When exploring chemical mixing tanks for sale, understanding the price ranges across different categories helps you make informed decisions. Tanks are typically classified into three main groups based on their size, capacity, and application: small-scale, mid-range, and industrial-grade. Each category serves unique purposes and comes with distinct price points.
Small-Scale Tanks
Small-scale tanks are ideal for light-duty applications or operations requiring minimal storage capacity. These tanks often range from 10 to 100 gallons in size and are commonly used in laboratories, small businesses, or pilot projects. Their compact design makes them easy to transport and install.
Prices for small-scale tanks typically start at around $120 for basic models made from plastic or polyethylene. Stainless steel options, known for their durability and chemical resistance, can cost upwards of $1,000. While these tanks are budget-friendly, you should carefully evaluate their material and features to ensure they meet your specific needs.
Mid-Range Tanks
Mid-range tanks cater to commercial operations that require moderate storage capacities, usually between 100 and 500 gallons. These tanks strike a balance between affordability and functionality, making them a popular choice for businesses in the food, beverage, and chemical industries.
The price for mid-range tanks varies significantly based on material and additional features. Polyethylene tanks in this category may cost between $900 and $2,300. Stainless steel tanks, which offer superior longevity and safety, can range from $7,500 to $15,000. Investing in mid-range tanks ensures you get reliable performance without overspending.
Industrial-Grade Tanks
Industrial-grade tanks are designed for large-scale operations and specialized applications. These tanks often exceed 500 gallons in capacity and are built to handle demanding environments. They are commonly used in industries like manufacturing, pharmaceuticals, and large-scale chemical processing.
Due to their size and advanced features, industrial-grade tanks come with higher price tags. Basic models may start at $13,000, while high-capacity stainless steel tanks can cost over $21,000. Custom-built tanks with additional features, such as agitators or heating systems, may exceed $45,000. Although these tanks require a significant investment, their durability and efficiency often result in long-term cost savings.
Pro Tip: When comparing tanks, consider not only the upfront cost but also the long-term value. Stainless steel tanks, while more expensive initially, often provide better durability and chemical resistance, reducing maintenance and replacement costs over time.
Key Factors Influencing the Cost of Chemical Mixing Tanks
When purchasing chemical mixing tanks, understanding the factors that influence their cost is crucial. These factors determine not only the price but also the tank’s suitability for your specific needs. By evaluating these aspects, you can make an informed decision and ensure your investment delivers long-term value.
Material Composition
The material used in constructing a chemical mixing tank significantly impacts its cost. Each material offers unique benefits and limitations, which directly affect the price and functionality of the tank.
- Polyethylene and Polypropylene: These materials are cost-effective and lightweight. They work well for basic chemical storage and mixing needs. However, their chemical compatibility is limited, making them unsuitable for handling highly reactive substances.
- Fiberglass-Reinforced Plastic (FRP): FRP tanks fall in the mid-range price category. They provide better chemical resistance than plastic tanks and are more durable. This makes them a popular choice for industries requiring moderate chemical handling capabilities.
- Stainless Steel: Stainless steel tanks are the most expensive option. They offer unmatched durability, chemical resistance, and versatility. These tanks can handle a wide range of chemicals and withstand extreme conditions. While the upfront cost is higher, stainless steel tanks often save money in the long run due to their longevity and low maintenance requirements.
Tip: Choose a material that aligns with the chemicals you plan to store or mix. Investing in the right material ensures safety and reduces the risk of costly replacements.
Size and Capacity
The size and capacity of a chemical mixing tank directly correlate with its price. Larger tanks require more materials and advanced manufacturing processes, which increase their cost.
- Small Tanks: Tanks with capacities under 100 gallons are typically the most affordable. They are ideal for small-scale operations or laboratory use.
- Mid-Range Tanks: Tanks between 100 and 500 gallons strike a balance between size and cost. These are suitable for commercial applications, such as food and beverage production or moderate chemical processing.
- Industrial-Grade Tanks: Tanks exceeding 500 gallons are designed for large-scale operations. Their higher capacity and specialized features, such as agitators or heating systems, make them the most expensive option.
Selecting the right size ensures you avoid overspending on unnecessary capacity while meeting your operational requirements.
Brand and Manufacturer
The brand and manufacturer of a chemical mixing tank also play a significant role in determining its cost. Reputable manufacturers often charge a premium for their products, but this higher price reflects their commitment to quality and reliability.
- Established Brands: Companies with a strong reputation, like those offering certified tanks, provide assurance of durability and compliance with industry standards. Their tanks often come with warranties and after-sales support, adding value to your purchase.
- Custom Manufacturers: Some manufacturers specialize in creating custom tanks tailored to your specific needs. While these tanks may cost more, they ensure optimal performance for unique applications.
- Generic Options: Tanks from lesser-known brands or generic manufacturers may be cheaper. However, they might lack the certifications or quality guarantees provided by established brands.
Pro Tip: Research the manufacturer’s reputation and certifications before purchasing. A reliable brand ensures you receive a high-quality product that meets safety and performance standards.
Additional Features and Customization
When selecting chemical mixing tanks, additional features and customization options can significantly impact both functionality and cost. These enhancements allow you to tailor the tank to your specific operational needs, ensuring optimal performance and efficiency.
Common Additional Features
Many chemical mixing tanks come with optional features that enhance their usability and adaptability. These features often address specific requirements for mixing, heating, or chemical handling. Some of the most common additions include:
- Agitators and Mixers: Agitators improve the mixing process by ensuring uniform blending of chemicals. They are essential for industries requiring precise formulations, such as pharmaceuticals or food production. Tanks equipped with agitators typically cost more due to the added complexity.
- Heating or Cooling Systems: Temperature control systems allow you to maintain specific conditions for chemical reactions. These systems are crucial for processes that require heating or cooling during mixing. Adding these systems increases the tank’s price but provides greater versatility.
- Level Indicators and Sensors: These devices help monitor the tank’s contents, ensuring accurate measurements and preventing overflows. They are particularly useful in automated systems, where precision is critical.
- Vents and Pressure Relief Valves: For tanks handling volatile chemicals, vents and pressure relief valves ensure safety by regulating internal pressure. These features are indispensable for maintaining compliance with safety standards.
Customization Options
Customization allows you to design a tank that perfectly aligns with your operational needs. Manufacturers like Shandong Chenma Machinery Co., Ltd. specialize in creating custom stainless steel tanks tailored to unique applications. Common customization options include:
- Material Selection: While stainless steel is the most durable and versatile option, you can choose other materials like polyethylene or fiberglass-reinforced plastic (FRP) based on your budget and chemical compatibility requirements.
- Size and Capacity Adjustments: Customizing the tank’s size ensures it fits seamlessly into your facility and meets your storage or mixing needs without unnecessary capacity.
- Specialized Coatings: Protective coatings enhance the tank’s resistance to specific chemicals or environmental conditions, extending its lifespan.
- Unique Designs: Some industries require tanks with unique shapes or configurations to accommodate space constraints or specialized processes.
Balancing Cost and Value
While additional features and customization increase the upfront cost, they often provide long-term value by improving efficiency, safety, and durability. For example, investing in a stainless steel tank with an agitator and heating system may seem expensive initially, but it can save you money by reducing maintenance and operational downtime.
Pro Tip: Before finalizing your purchase, assess your operational needs carefully. Identify which features and customizations are essential and which ones you can forego. This approach helps you balance cost and functionality effectively.
By considering these additional features and customization options, you can ensure that your investment in chemical mixing tanks for sale delivers maximum value and meets your specific requirements.
Comparing Types of Chemical Mixing Tanks for Sale
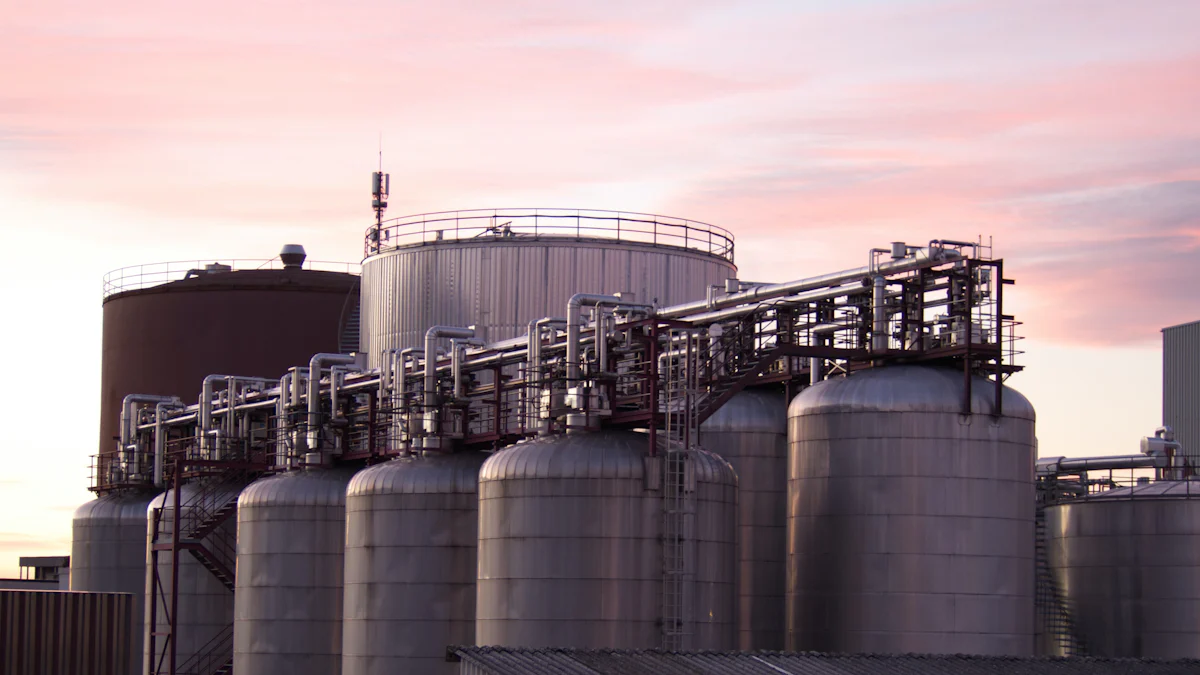
When exploring chemical mixing tanks, understanding the different types available helps you select the best option for your needs. Each type offers unique advantages and is suited for specific applications. Below, we break down the three main categories: portable tanks, stationary tanks, and custom-built tanks.
Portable Tanks
Portable tanks are designed for mobility and convenience. These tanks are ideal for operations requiring frequent relocation or small-scale mixing tasks. Their compact size and lightweight construction make them easy to transport and handle. You can use portable tanks in laboratories, pilot projects, or temporary setups.
Key Features:
- Typically made from materials like polyethylene or stainless steel.
- Equipped with handles, wheels, or skid mounts for easy movement.
- Available in smaller capacities, usually ranging from 10 to 100 gallons.
Applications:
- Ideal for mixing small batches of chemicals.
- Suitable for industries like research, cosmetics, or small-scale food production.
Portable tanks offer flexibility and cost-effectiveness. However, their smaller size limits their use in large-scale operations. If mobility is a priority, these tanks provide an excellent solution.
Stationary Tanks
Stationary tanks are built for stability and durability. These tanks are fixed in place and designed to handle larger volumes of chemicals. They are commonly used in industrial settings where consistent mixing or storage is required.
Key Features:
- Constructed from robust materials like stainless steel or fiberglass-reinforced plastic (FRP).
- Often equipped with additional features such as agitators, heating systems, or level indicators.
- Capacities range from 100 to over 1,000 gallons.
Applications:
- Perfect for continuous mixing processes in industries like pharmaceuticals, food and beverage, or chemical manufacturing.
- Suitable for long-term storage of chemicals.
Stationary tanks provide reliability and efficiency for demanding applications. Their sturdy design ensures safety and compliance with industry standards. If your operation requires high-capacity mixing or storage, stationary tanks are an excellent choice.
Custom-Built Tanks
Custom-built tanks are tailored to meet specific operational requirements. These tanks are designed to address unique challenges, such as space constraints, specialized chemical handling, or advanced mixing needs. Manufacturers like Shandong Chenma Machinery Co., Ltd. specialize in creating custom stainless steel tanks for diverse industries.
Key Features:
- Fully customizable in terms of size, material, and features.
- Options for specialized coatings, unique shapes, or advanced systems like temperature control.
- Built to comply with strict safety and quality standards.
Applications:
- Ideal for industries with unique processes, such as biotechnology, petrochemicals, or large-scale food production.
- Suitable for handling highly reactive or sensitive chemicals.
Custom-built tanks offer unparalleled versatility and precision. While they may require a higher initial investment, they ensure optimal performance and long-term value. If your operation demands a tailored solution, custom-built tanks are the way to go.
Pro Tip: Evaluate your operational needs carefully before choosing a tank type. Consider factors like mobility, capacity, and customization to ensure the tank aligns with your requirements.
By understanding the differences between portable, stationary, and custom-built tanks, you can make an informed decision when exploring chemical mixing tanks for sale. Each type serves a distinct purpose, helping you achieve efficiency and reliability in your operations.
Benefits of Stainless Steel Chemical Mixing Tanks
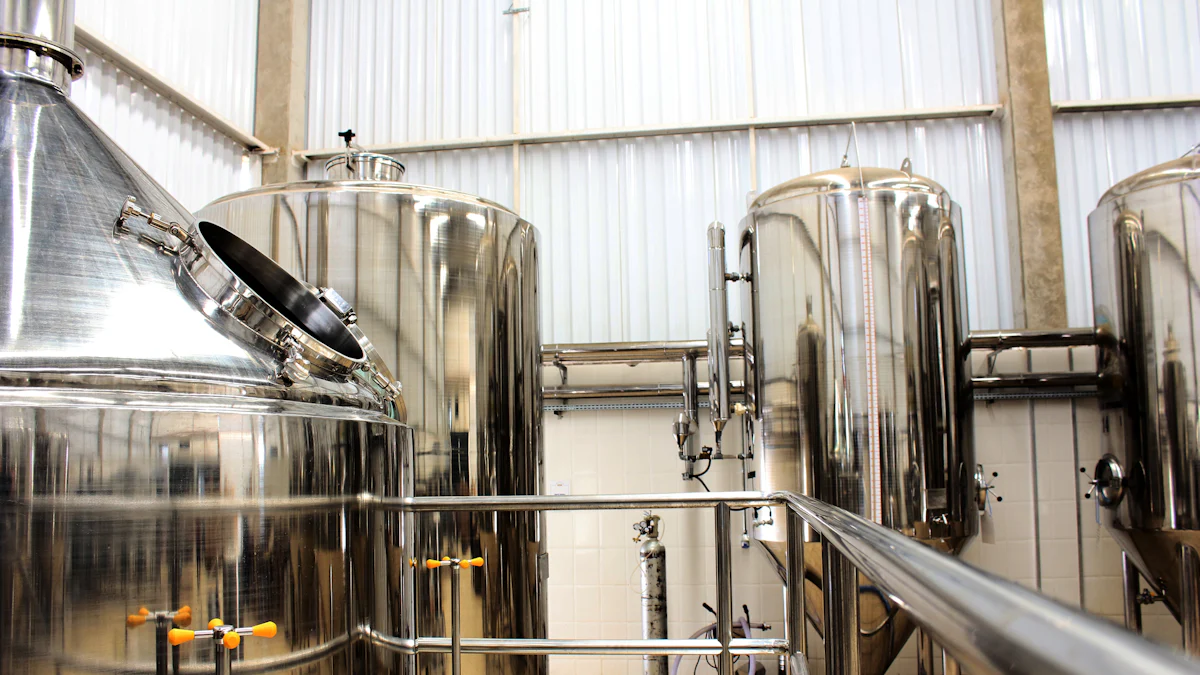
Durability and Longevity
Stainless steel chemical mixing tanks are built to last. The material resists wear and tear, even in demanding environments. Unlike plastic or fiberglass tanks, stainless steel does not crack or degrade over time. This durability ensures that your tank remains functional for years, reducing the need for frequent replacements.
The longevity of stainless steel tanks also makes them a cost-effective choice. While the initial investment may seem higher, the extended lifespan offsets the upfront cost. You save money in the long run by avoiding repairs and replacements. Additionally, stainless steel withstands extreme temperatures and pressures, making it suitable for various industrial applications.
Fact: Many industries prefer stainless steel tanks because they maintain structural integrity under harsh conditions, ensuring reliable performance over time.
Chemical Resistance and Safety
Stainless steel offers exceptional chemical resistance. It can handle a wide range of substances, including corrosive chemicals, without reacting or degrading. This resistance ensures that the tank remains safe and functional, even when exposed to harsh materials.
Safety is another critical advantage. Stainless steel does not leach harmful substances into the chemicals it stores or mixes. This feature is especially important in industries like food, beverage, and pharmaceuticals, where contamination can have serious consequences. The non-porous surface of stainless steel also prevents bacteria and other contaminants from accumulating, ensuring a hygienic environment.
Pro Tip: Always choose stainless steel tanks for applications involving reactive or sensitive chemicals. Their resistance to corrosion and contamination ensures both safety and efficiency.
Cost vs. Value Analysis
When evaluating chemical mixing tanks for sale, stainless steel tanks stand out for their value. Although they come with a higher price tag, the benefits they offer justify the cost. Their durability reduces maintenance expenses, while their chemical resistance minimizes the risk of damage or contamination.
Stainless steel tanks also provide versatility. They can be customized with features like agitators, heating systems, or specialized coatings to meet specific operational needs. This adaptability enhances their functionality, making them a worthwhile investment for various industries.
Key Insight: Investing in a stainless steel tank may seem expensive initially, but the long-term savings and performance benefits make it a smart choice. You get a reliable, durable, and safe solution that delivers consistent results.
By choosing stainless steel chemical mixing tanks, you ensure durability, safety, and value. These tanks offer unmatched performance, making them an excellent option for industries that prioritize quality and reliability.
Tips for Cost-Effective Purchasing of Chemical Mixing Tanks
When purchasing chemical mixing tanks, making cost-effective decisions ensures you get the best value for your investment. By carefully evaluating your needs, researching suppliers, and negotiating prices, you can secure a high-quality tank without overspending.
Assessing Your Needs
Understanding your specific requirements is the first step in making a smart purchase. The type of chemicals you handle, the volume of production, and the operational environment all influence the tank you need. Start by identifying the following:
- Chemical Compatibility: Ensure the tank material aligns with the chemicals you plan to store or mix. Stainless steel tanks are an excellent choice due to their resistance to corrosion and structural integrity. They handle a wide range of substances safely and effectively.
- Capacity Requirements: Determine the size of the tank based on your production scale. Overestimating capacity can lead to unnecessary expenses, while underestimating can disrupt operations.
- Operational Features: Decide if additional features like agitators, heating systems, or level indicators are essential for your processes. These features enhance functionality but may increase the cost.
Pro Tip: Create a checklist of your needs before exploring options. This approach helps you focus on tanks that meet your requirements, saving time and money.
Researching and Comparing Suppliers
Choosing the right supplier is crucial for ensuring quality and reliability. Not all suppliers offer the same level of expertise or product standards, so thorough research is essential. Follow these steps to find the best supplier:
- Evaluate Reputation: Look for suppliers with positive reviews and a proven track record. Companies like Shandong Chenma Machinery Co., Ltd. stand out for their expertise in manufacturing stainless steel tanks and adhering to strict quality standards.
- Compare Product Offerings: Examine the range of tanks available. Check if the supplier offers options for customization to meet your unique needs.
- Verify Certifications: Ensure the supplier complies with industry standards. Certifications like ISO9001 and CE indicate a commitment to quality and safety.
- Request Quotes: Obtain detailed quotes from multiple suppliers. Compare prices, features, and warranties to identify the best deal.
Fact: Reputable suppliers often provide after-sales support, including maintenance services and technical assistance. This added value can save you money in the long run.
Negotiating Prices and Discounts
Negotiation plays a key role in securing a cost-effective deal. Suppliers are often willing to adjust prices or offer discounts, especially for bulk purchases or long-term partnerships. Use these strategies to negotiate effectively:
- Highlight Your Needs: Clearly communicate your requirements and budget constraints. Suppliers may suggest cost-saving alternatives or customized solutions.
- Leverage Competition: Mention quotes from other suppliers to encourage competitive pricing. This tactic often motivates suppliers to offer better deals.
- Ask for Discounts: Inquire about discounts for bulk orders, repeat purchases, or referrals. Many suppliers provide incentives to loyal customers.
- Consider Used Tanks: Explore the option of purchasing refurbished tanks. Used stainless steel tanks, for example, retain their durability and functionality while costing significantly less.
Pro Tip: Build a strong relationship with your supplier. A good rapport can lead to better deals, priority service, and access to exclusive offers.
By assessing your needs, researching suppliers, and negotiating effectively, you can make a cost-effective purchase. This approach ensures you invest in a tank that delivers long-term value and meets your operational demands.
Considering Used or Refurbished Tanks
Exploring used or refurbished chemical mixing tanks can be a smart way to save money while still meeting your operational needs. These tanks often provide the same functionality as new ones but at a fraction of the cost. By carefully evaluating their condition and suitability, you can secure a high-quality tank without overspending.
Benefits of Choosing Used or Refurbished Tanks
Opting for used or refurbished tanks offers several advantages:
- Cost Savings: Pre-owned tanks typically cost significantly less than new ones. This makes them an excellent choice if you have budget constraints or need multiple tanks for your operations.
- Immediate Availability: Unlike custom-built tanks, which may take weeks or months to manufacture, used tanks are often ready for immediate purchase and delivery.
- Sustainability: Reusing tanks reduces waste and promotes environmental responsibility. Stainless steel tanks, in particular, are highly durable and maintain their structural integrity even after years of use.
Fact: Stainless steel tanks resist corrosion and wear, making them ideal for refurbishment. Their long lifecycle ensures they remain effective and safe for extended periods.
Key Considerations When Buying Used Tanks
To ensure you make a wise investment, evaluate the following factors before purchasing a used or refurbished tank:
Material and Condition
Inspect the tank’s material to confirm it suits your chemical handling needs. Stainless steel tanks are often the best choice due to their durability and resistance to corrosion. Check for signs of wear, such as dents, cracks, or rust, which could compromise the tank’s performance.Capacity and Size
Verify that the tank’s size aligns with your operational requirements. Oversized tanks may lead to unnecessary costs, while undersized ones could disrupt your processes.Previous Usage
Understand what the tank was previously used for. Tanks that stored or mixed highly reactive chemicals may require additional cleaning or reconditioning to ensure safety.Certifications and Compliance
Confirm that the tank meets industry standards and certifications. Look for labels or documentation indicating compliance with safety and quality regulations.Supplier Reputation
Purchase from a reputable supplier who specializes in refurbished tanks. Reliable suppliers often provide warranties or guarantees, giving you peace of mind about your purchase.
Tips for Maximizing Value
To get the most out of your investment in a used or refurbished tank, follow these tips:
- Request a Thorough Inspection: Ask the supplier for detailed inspection reports or maintenance records. This helps you assess the tank’s condition and identify any potential issues.
- Consider Refurbishment Options: Some suppliers offer refurbishment services, such as cleaning, re-coating, or adding new features like agitators. These upgrades can enhance the tank’s functionality and extend its lifespan.
- Negotiate Pricing: Used tanks often have flexible pricing. Negotiate with the supplier to secure the best deal, especially if you’re purchasing multiple units.
Pro Tip: Stainless steel tanks retain their value over time due to their durability and versatility. Investing in a refurbished stainless steel tank can provide long-term savings and reliable performance.
By considering used or refurbished tanks, you can achieve a balance between cost and quality. With proper evaluation and careful selection, these tanks can serve as a cost-effective solution for your chemical mixing needs.
How Chenma Machinery Stands Out in the Market
Overview of Chenma’s Expertise in Stainless Steel Tanks
Chenma Machinery has established itself as a leader in the stainless steel tank industry. With a focus on innovation and precision, the company designs and manufactures tanks that cater to diverse industries, including food, beverage, and chemical processing. You benefit from their extensive experience, as Chenma has been at the forefront of creating solutions tailored to meet specific operational challenges.
The company operates a state-of-the-art production facility spanning 20,000 square meters. Over 200 skilled professionals work diligently to ensure every tank meets the highest standards of quality and performance. Chenma’s engineers specialize in adapting tanks to unique requirements, offering both catalog products and fully customized designs. This expertise ensures you receive a product that aligns perfectly with your operational needs.
Fact: Businesses that prioritize quality improvements often see significant returns on investment (ROI). Chenma’s focus on delivering durable and efficient tanks helps you achieve long-term value while maintaining operational excellence.
Customization Options for Unique Applications
Chenma Machinery excels in providing customization options that address your specific needs. Whether you require a tank for a specialized chemical process or a unique production setup, Chenma offers tailored solutions to optimize your operations. Their engineers collaborate closely with you to design tanks that fit seamlessly into your workflow.
Key Customization Features:
- Material Selection: Choose from stainless steel or other materials based on your chemical compatibility and budget.
- Capacity Adjustments: Select the exact size and volume to match your production scale.
- Advanced Features: Add agitators, heating systems, or specialized coatings to enhance functionality.
- Unique Designs: Opt for tanks with custom shapes or configurations to accommodate space constraints or specialized processes.
Chenma’s ability to deliver custom-built tanks ensures you get a product that not only meets but exceeds your expectations. This flexibility allows you to optimize efficiency and achieve strategic objectives without compromising on quality.
Survey Insight: Companies that balance cost and quality considerations often achieve better value and maintain brand standards. Chenma’s customizable tanks help you strike this balance by offering high-quality solutions tailored to your budget.
Certifications and Quality Standards
When you invest in a Chenma Machinery tank, you gain the assurance of industry-leading certifications and compliance with global standards. Chenma’s commitment to quality is evident in its adherence to rigorous safety and environmental protocols. These certifications guarantee that the tanks you purchase meet the highest benchmarks for reliability and performance.
Chenma’s Certifications Include:
- ISO9001-2005: Ensures consistent quality management practices.
- ISO14001-2015: Demonstrates a commitment to environmental sustainability.
- OHSAS18001-2007: Focuses on occupational health and safety management.
- EU CE Certification: Confirms compliance with European safety and quality standards.
These certifications reflect Chenma’s dedication to delivering products that align with your operational and regulatory requirements. By choosing a certified tank, you reduce risks, enhance safety, and ensure compliance with industry norms.
Key Insight: Organizations that prioritize quality enhancements often see improved customer satisfaction and long-term value. Chenma’s certified tanks provide you with the reliability and peace of mind needed to focus on your core operations.
Chenma Machinery stands out in the market by combining expertise, customization, and certified quality. Their stainless steel tanks offer unmatched durability and functionality, making them a trusted choice for businesses seeking cost-effective and high-performing solutions.
Balancing Cost with Quality and Functionality
Long-Term Value of High-Quality Tanks
Investing in high-quality chemical mixing tanks ensures long-term value for your operations. While the initial cost may seem higher, these tanks often deliver significant savings over time. Durable materials like stainless steel resist wear and tear, reducing the need for frequent replacements. This longevity minimizes disruptions to your workflow and lowers overall operational costs.
High-quality tanks also enhance efficiency. Features such as agitators or temperature control systems improve performance, allowing you to achieve consistent results. These benefits translate into better productivity and reduced waste, which directly impact your bottom line. By prioritizing quality, you secure a reliable solution that supports your business growth.
Key Insight: New tanks, though pricier upfront, often come with warranties and assurances. These guarantees protect your investment and provide peace of mind, ensuring you receive a product that meets industry standards.
Maintenance and Operational Cost Considerations
Maintenance plays a crucial role in determining the overall cost of your chemical mixing tanks. High-quality tanks require less frequent repairs, saving you money in the long run. Stainless steel tanks, for example, resist corrosion and damage, making them easier to maintain compared to plastic or fiberglass options.
Operational costs also depend on the tank’s efficiency. Tanks equipped with advanced features, such as automated mixing systems, reduce manual labor and energy consumption. This efficiency lowers utility bills and improves profitability. Additionally, well-maintained tanks prevent leaks or contamination, avoiding costly downtime and product loss.
To optimize maintenance and operational costs, follow these steps:
- Regular Inspections: Check for signs of wear, such as cracks or rust, to address issues early.
- Proper Cleaning: Use appropriate cleaning agents to maintain the tank’s integrity and hygiene.
- Scheduled Servicing: Partner with a reliable supplier for routine maintenance and technical support.
Pro Tip: Used tanks may save costs initially but can entail risks like hidden damages or higher maintenance needs. Evaluate their condition thoroughly before purchase to avoid unexpected expenses.
Ensuring Safety and Compliance with Industry Standards
Safety and compliance should always be a priority when selecting chemical mixing tanks. High-quality tanks adhere to strict industry standards, ensuring they meet safety regulations and minimize risks. Stainless steel tanks, for instance, offer superior chemical resistance, preventing reactions that could compromise safety.
Compliance with certifications, such as ISO9001 or CE, guarantees that the tank meets global quality benchmarks. These certifications not only protect your operations but also enhance your reputation in the market. Customers and partners value businesses that prioritize safety and reliability.
To ensure compliance, consider the following:
- Verify Certifications: Choose tanks from manufacturers with recognized certifications.
- Assess Features: Look for safety features like pressure relief valves or non-reactive coatings.
- Stay Updated: Keep track of changes in industry regulations to maintain compliance.
Fact: Tanks from reputable manufacturers, like those with ISO and CE certifications, provide assurance of quality and safety. These certifications reflect a commitment to delivering reliable and compliant products.
Balancing cost with quality and functionality requires careful evaluation of your needs and priorities. By investing in high-quality tanks, maintaining them effectively, and ensuring compliance, you achieve long-term value and operational excellence.
Common Mistakes to Avoid When Buying Chemical Mixing Tanks
Overlooking Long-Term Costs
Focusing solely on the upfront cost of a chemical mixing tank can lead to costly mistakes. While a cheaper tank may seem like a good deal, it often results in higher expenses over time. Maintenance, repairs, and replacements can quickly add up, especially if the tank is made from low-quality materials. Stainless steel tanks, for example, may have a higher initial price, but their durability and resistance to corrosion reduce long-term costs significantly.
You should also consider operational costs. Tanks with advanced features, such as agitators or temperature control systems, may cost more initially but save money by improving efficiency and reducing energy consumption. Investing in a high-quality tank ensures you avoid frequent repairs and operational disruptions, which can impact your bottom line.
Tip: Always evaluate the total cost of ownership, including maintenance, operational efficiency, and lifespan, before making a purchase. This approach helps you make a cost-effective decision.
Choosing the Wrong Material or Size
Selecting the wrong material or size for your chemical mixing tank can compromise safety and efficiency. The material must be compatible with the chemicals you plan to store or mix. For instance, polyethylene tanks may work for basic applications, but they lack the durability and chemical resistance of stainless steel. Using an incompatible material can lead to leaks, contamination, or even equipment failure.
Size is equally important. A tank that is too small may disrupt your operations, while an oversized tank can result in unnecessary expenses. You need to assess your production scale and storage requirements carefully. Customization options, like those offered by Chenma Machinery, allow you to select the exact size and material that align with your needs.
Pro Tip: Consult with experts or suppliers to determine the best material and size for your application. This ensures safety, efficiency, and cost-effectiveness.
Ignoring Supplier Reputation and Certifications
The supplier you choose plays a critical role in the quality and reliability of your chemical mixing tank. Ignoring a supplier’s reputation or certifications can lead to subpar products that fail to meet industry standards. Reputable suppliers, like Chenma Machinery, adhere to strict quality and safety protocols. Their tanks come with certifications such as ISO9001 and CE, ensuring compliance with global standards.
A reliable supplier also provides follow-up support, including maintenance services and technical assistance. This support ensures your tank remains functional and efficient throughout its lifespan. Choosing a supplier without a proven track record increases the risk of receiving a low-quality product, which can compromise safety and performance.
Key Insight: Always verify the supplier’s certifications and customer reviews. A trusted supplier guarantees a high-quality product and reliable after-sales support.
By avoiding these common mistakes, you can make an informed decision when purchasing chemical mixing tanks. Focus on long-term value, choose the right material and size, and partner with a reputable supplier to ensure your investment delivers optimal results.
Understanding the price ranges and factors influencing costs is essential when exploring chemical mixing tanks for sale. By evaluating these aspects, you can make informed decisions that align with your operational needs. Stainless steel tanks stand out for their durability, chemical resistance, and long-term value. They reduce maintenance costs and ensure safety, making them a reliable choice for various industries. Partnering with reputable suppliers like Chenma Machinery guarantees high-quality products tailored to your requirements. Balancing cost, quality, and functionality ensures a successful purchase that supports efficiency and safety in the long run.
FAQ
What factors should you consider when choosing a chemical mixing tank?
You should evaluate several key factors to ensure the tank meets your needs. Start by considering the material. Stainless steel offers durability and chemical resistance, while polyethylene suits basic applications. Next, assess the tank’s size and capacity. Choose a size that aligns with your production scale to avoid overspending or operational inefficiencies. Finally, look at additional features like agitators or heating systems. These can enhance functionality but may increase the cost.
Tip: Always match the tank material to the chemicals you plan to store or mix. This ensures safety and prevents costly replacements.
Why is stainless steel often recommended for chemical mixing tanks?
Stainless steel stands out for its durability and versatility. It resists corrosion, handles extreme temperatures, and maintains structural integrity over time. Unlike plastic or fiberglass, stainless steel does not degrade or crack, even in demanding environments. This makes it ideal for industries requiring long-term reliability and safety.
Fact: Stainless steel tanks often save money in the long run due to their low maintenance needs and extended lifespan.
How do you maintain a chemical mixing tank effectively?
Regular maintenance ensures your tank operates efficiently and safely. Begin with routine inspections to identify wear or damage. Clean the tank using appropriate cleaning agents to prevent contamination. Schedule professional servicing to address technical issues and prolong the tank’s lifespan.
Pro Tip: Neglecting maintenance can lead to environmental hazards and costly repairs. A well-maintained tank reduces risks and ensures compliance with safety standards.
Can you save money by purchasing a used chemical mixing tank?
Yes, buying a used tank can be cost-effective if done carefully. Used tanks often cost less than new ones while providing similar functionality. However, you must inspect the tank thoroughly for signs of wear or damage. Verify its material, capacity, and previous usage to ensure it meets your needs.
Key Insight: Stainless steel tanks retain their value over time, making them a reliable choice even when purchased pre-owned.
What are the risks of choosing the wrong tank material?
Selecting the wrong material can lead to serious issues. For example, using a plastic tank for highly reactive chemicals may result in leaks or contamination. This not only compromises safety but also increases costs due to repairs or replacements. Always choose a material compatible with your specific chemical requirements.
Warning: Choosing a tank based solely on price can lead to regret and financial burden. Prioritize quality and compatibility over cost.
How do additional features impact the cost of a chemical mixing tank?
Features like agitators, heating systems, or level indicators enhance a tank’s functionality but increase its price. These additions improve efficiency and safety, making them worthwhile for specific applications. However, you should evaluate your operational needs to avoid paying for unnecessary features.
Tip: Identify essential features before purchasing. This helps you balance cost and functionality effectively.
Why is supplier reputation important when buying a chemical mixing tank?
A reputable supplier ensures you receive a high-quality product that meets industry standards. Established manufacturers, like Chenma Machinery, provide certified tanks with warranties and after-sales support. Choosing an unreliable supplier increases the risk of receiving subpar products, which can compromise safety and performance.
Fact: Tanks from certified suppliers often come with guarantees, ensuring reliability and peace of mind.
What mistakes should you avoid when purchasing a chemical mixing tank?
Avoid focusing solely on upfront costs. Cheaper tanks may lead to higher expenses over time due to maintenance or replacements. Ensure the tank material and size align with your needs. Also, research the supplier’s reputation and certifications to avoid substandard products.
Pro Tip: Plan your purchase carefully. Lack of proper planning can result in costly mistakes and operational disruptions.
Are custom-built tanks worth the investment?
Custom-built tanks provide tailored solutions for unique operational needs. They allow you to select specific materials, sizes, and features, ensuring optimal performance. While they may cost more initially, custom tanks often deliver long-term value by improving efficiency and reducing maintenance costs.
Key Insight: Customization ensures the tank fits seamlessly into your workflow, maximizing productivity and safety.
How can you ensure compliance with industry standards?
Choose tanks from manufacturers with recognized certifications, such as ISO9001 or CE. These certifications guarantee the tank meets global quality and safety benchmarks. Additionally, verify that the tank includes safety features like pressure relief valves or non-reactive coatings.
Fact: Compliance with industry standards not only ensures safety but also enhances your reputation in the market.