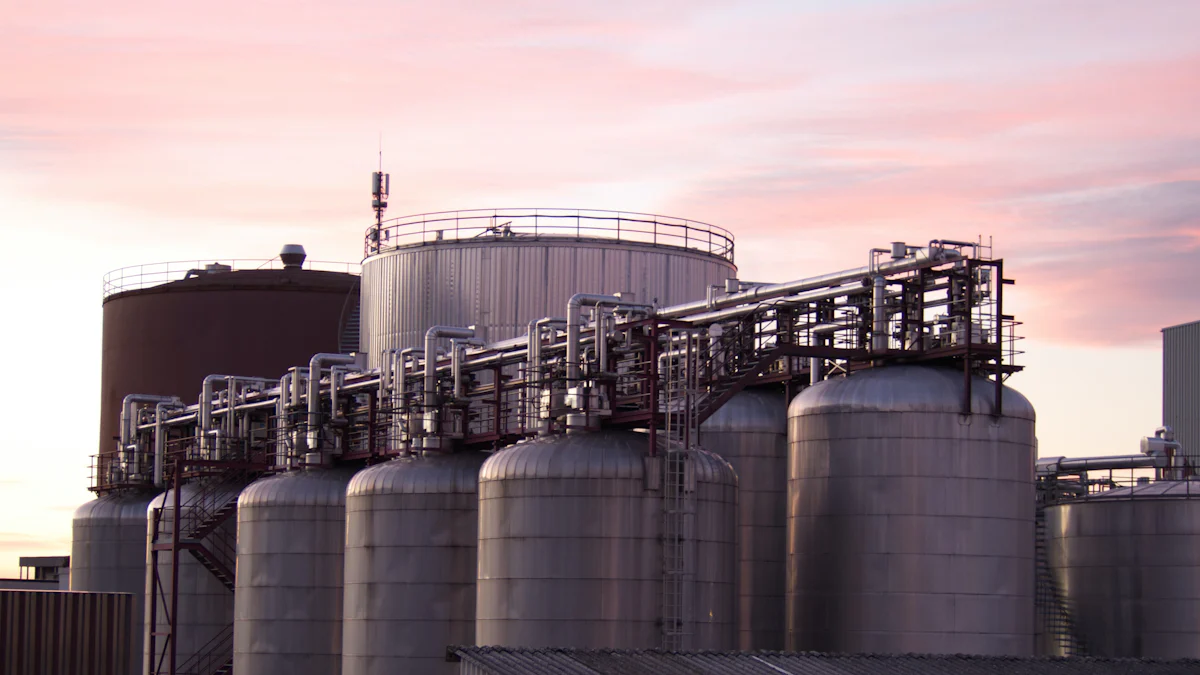
Agitators play a vital role in industrial processes by ensuring efficient chemical mixing in chemical mixing tanks with agitators. They create uniform mixing, which is essential for achieving consistent product quality. By optimizing reaction rates and maintaining stable temperature and pressure, agitators enhance the performance of chemical mixing tanks. The global demand for these devices reflects their importance, with the industrial agitators market projected to grow from USD 3.10 billion in 2024 to USD 3.99 billion by 2029. This growth highlights their necessity in meeting strict manufacturing standards for precision and efficiency.
Understanding Agitators in Chemical Mixing Tanks
What Is an Agitator?
An agitator is a mechanical device designed to mix, stir, or blend materials within a tank or vessel. It ensures that liquids, solids, or gases combine uniformly, creating a consistent mixture. You can think of it as the engine behind the mixing process, driving the movement of materials to achieve the desired outcome.
Agitators come in various designs, each tailored to specific applications. For instance, propeller agitators resemble boat propellers and are ideal for mixing low-viscosity liquids quickly. They create a high-flow environment, ensuring gentle yet effective mixing. On the other hand, anchor agitators handle highly viscous materials. These heavy-duty devices scrape the tank walls, ensuring even blending of thick mixtures. Between these two extremes, turbine agitators strike a balance. They combine centrifugal and rotational motion, making them suitable for emulsification and dispersion processes. Their versatility allows them to handle a wide range of viscosities while maintaining high efficiency.
By selecting the right type of agitator, you can optimize your mixing process and achieve consistent results, regardless of the material’s properties.
The Role of Agitators in Industrial Processes
Agitators play a critical role in industrial operations by ensuring efficient and uniform mixing. In chemical mixing tanks, they facilitate the blending of reactants, which is essential for achieving the desired chemical reactions. Without proper mixing, you risk inconsistent product quality and reduced process efficiency.
In addition to blending, agitators help maintain temperature and pressure equilibrium within the tank. This is particularly important in processes where heat transfer is required. For example, during exothermic reactions, agitators distribute heat evenly, preventing localized overheating. Similarly, they ensure that cooling systems work effectively by circulating the liquid throughout the tank.
Agitators also enhance productivity by reducing the time required for mixing. High-speed options, such as turbine agitators, create rapid flow, making them suitable for processes that demand quick emulsification or dispersion. For industries dealing with thick or sticky materials, anchor agitators ensure that no residue remains on the tank walls, minimizing waste and improving efficiency.
By incorporating agitators into your chemical mixing tanks, you can streamline your operations, improve product quality, and meet the demands of modern industrial standards.
Key Functions of Agitators in Chemical Mixing Tanks
Homogenization for Uniform Mixtures
Achieving uniform mixtures is one of the most critical functions of an agitator. When you mix different substances, whether liquids, solids, or gases, inconsistencies can arise without proper blending. Agitators ensure that every component disperses evenly throughout the tank, creating a homogeneous mixture. This uniformity is essential in chemical processes where precise formulations determine the final product’s quality.
For example, in the production of emulsions, such as those used in cosmetics or pharmaceuticals, agitators play a pivotal role. They prevent separation by continuously mixing the components, ensuring stability and consistency. Without this function, the end product could fail to meet industry standards, leading to inefficiencies and potential waste. By using an agitator, you can maintain high-quality results and meet the demands of industrial applications.
Suspension of Solid Particles
In many chemical processes, solid particles need to remain suspended within a liquid medium. Agitators excel at this task by generating the necessary turbulence to keep solids from settling at the bottom of the tank. This function is particularly important in industries like mining and metal extraction, where suspending ore particles ensures efficient processing.
When you use an agitator for suspension, it prevents sedimentation, which can disrupt the mixing process and reduce efficiency. For instance, in the paint industry, agitators keep pigments evenly distributed, ensuring consistent color and texture. This capability makes agitators indispensable for maintaining the integrity of mixtures in various industrial settings.
Dissolution of Substances
Agitators also facilitate the dissolution of substances, enabling you to combine materials that might not naturally mix. Whether dissolving powders into liquids or blending immiscible liquids, agitators create the conditions necessary for effective solubility. This function is vital in chemical manufacturing, where precise reactions depend on the complete dissolution of reactants.
For example, in the food and beverage industry, agitators help dissolve sugar or other additives into liquids, ensuring a smooth and uniform product. Similarly, in pharmaceutical production, they assist in creating solutions with exact concentrations, meeting stringent quality standards. By promoting dissolution, agitators enhance the efficiency and reliability of your mixing processes.
Heat Transfer and Temperature Control
Efficient heat transfer is a critical function of an agitator in chemical mixing tanks. When you mix substances, maintaining a consistent temperature throughout the tank ensures optimal conditions for reactions and prevents localized overheating or cooling. Agitators achieve this by continuously circulating the materials, allowing heat to distribute evenly across the mixture.
For example, in processes involving exothermic reactions, where heat is released during chemical interactions, an agitator prevents hotspots from forming. These hotspots can compromise the quality of the final product or even pose safety risks. By promoting uniform heat distribution, agitators help you maintain control over the reaction environment.
Temperature control also plays a vital role in industries like food production and pharmaceuticals. In these sectors, precise temperature regulation ensures that products meet stringent quality standards. An industrial agitator, designed for high efficiency, enhances the heat exchange between the tank walls and the mixture. This capability is especially useful when cooling or heating systems are integrated into the tank. Whether you need to cool a heated emulsion or maintain a stable temperature for sensitive chemical reactions, an agitator ensures the process runs smoothly.
Agitators also reduce energy consumption by optimizing heat transfer. Instead of relying on excessive heating or cooling, you can achieve the desired temperature more efficiently. This not only lowers operational costs but also supports sustainable practices in industrial processes.
Facilitating Chemical Reactions
Agitators play a pivotal role in facilitating chemical reactions by ensuring that reactants mix thoroughly and interact effectively. In chemical processes, the success of a reaction often depends on the uniform distribution of reactants. An agitator creates the necessary turbulence to bring these substances into contact, increasing the reaction rate and improving overall efficiency.
For instance, in the production of polymers or other complex compounds, agitators ensure that all components blend seamlessly. This uniformity prevents incomplete reactions, which can lead to inconsistent product quality. By using an agitator, you can achieve the desired chemical composition with precision, meeting the high standards required in industrial applications.
Agitators also enhance mass transfer, a key factor in many chemical reactions. When you mix liquids, gases, or solids, the agitator increases the surface area of contact between reactants. This promotes faster and more efficient reactions, saving time and resources. In addition, agitators maintain the stability of the reaction environment by controlling factors like temperature and pressure.
In industries like pharmaceuticals, where precision is paramount, agitators ensure that reactions occur under controlled conditions. This guarantees the consistency and safety of the final product. Whether you are producing medicines, adhesives, or specialty chemicals, an agitator helps you achieve reliable and repeatable results.
By incorporating agitators into your chemical mixing tanks, you can optimize reaction conditions, improve product quality, and enhance the overall efficiency of your processes.
Benefits of Chemical Mixing Tanks with Agitators
Enhanced Product Quality
Agitators ensure thorough mixing, which directly improves the consistency and reliability of your final product. By blending ingredients uniformly, they eliminate inconsistencies that could compromise the quality of your output. For example, in chemical manufacturing, agitators prevent uneven distribution of reactants, ensuring that every batch meets the required standards. This uniformity is essential for industries where precision defines success, such as pharmaceuticals or food production.
Without an agitator, you risk producing mixtures with lumps, sediments, or uneven textures. These defects can lead to product rejection or customer dissatisfaction. An industrial agitator helps you avoid these issues by maintaining a consistent mixture throughout the process. Whether you are creating emulsions, suspensions, or solutions, the use of chemical mixing tanks with agitators guarantees superior product quality.
Reduced Material Waste
Agitators play a crucial role in minimizing material waste during the mixing process. By preventing the formation of lumps, sediments, or crusts, they ensure that all materials are utilized effectively. This efficiency reduces the amount of raw material wasted, which can significantly lower production costs. For instance, in industries like paint manufacturing, agitators keep pigments evenly distributed, preventing sedimentation at the bottom of the tank.
When you use an agitator, you also reduce the likelihood of residue sticking to the tank walls. This feature is particularly beneficial when working with viscous or sticky substances. By ensuring complete mixing and minimizing leftover material, agitators help you maximize product yield. This not only saves resources but also supports sustainable practices in industrial operations.
Improved Safety in Mixing Processes
Safety is a top priority in any industrial setting, and agitators contribute significantly to safer mixing processes. They maintain a controlled environment by ensuring uniform temperature and pressure distribution within the tank. This control is vital in chemical reactions, where uneven conditions could lead to dangerous outcomes, such as overheating or pressure buildup.
Agitators also reduce the need for manual intervention during mixing. By automating the process, they minimize the risk of accidents caused by human error. For example, in chemical industries, handling hazardous substances becomes safer when an agitator ensures proper mixing without requiring direct contact. Additionally, the consistent operation of an agitator prevents sudden surges or imbalances, further enhancing workplace safety.
By incorporating agitators into your chemical mixing tanks, you create a safer, more efficient, and reliable production environment. This not only protects your workforce but also ensures compliance with industrial safety standards.
Increased Operational Efficiency
Agitators significantly enhance operational efficiency in chemical mixing tanks by streamlining processes and reducing production time. When you use an agitator, it ensures that materials mix uniformly and consistently, eliminating the need for repeated cycles. This efficiency allows you to meet production targets faster while maintaining high-quality standards.
The design of an industrial agitator optimizes energy consumption. By promoting effective mixing, it reduces the need for excessive power usage. For example, agitators with advanced designs create efficient flow patterns, ensuring thorough blending without overloading the system. This energy-saving feature not only lowers operational costs but also supports sustainable manufacturing practices.
Agitators also minimize downtime during production. Their ability to prevent sedimentation and residue buildup means you spend less time on cleaning and maintenance. For instance, in industries handling viscous or sticky materials, agitators keep the tank walls clean by continuously scraping and mixing. This feature ensures uninterrupted operations and maximizes productivity.
The growing demand for chemical mixing tanks with agitators reflects their role in improving efficiency. The global industrial agitators market is projected to grow from USD 3.10 billion in 2024 to USD 3.99 billion by 2029, with a compound annual growth rate (CAGR) of 5.2%. This growth highlights how industries increasingly rely on agitators to meet strict requirements for precision and consistency in manufacturing.
By incorporating agitators into your processes, you can achieve faster production cycles, lower energy costs, and reduced waste. These benefits translate into higher profitability and a competitive edge in the market.
Types of Agitators and Their Applications
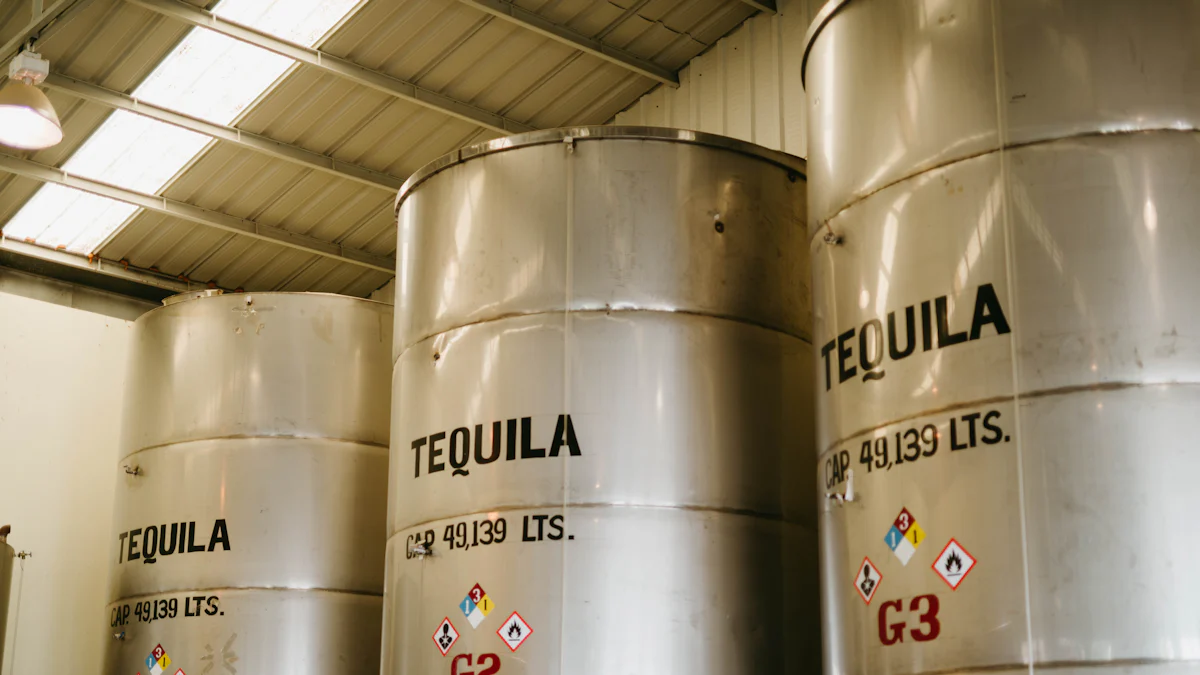
Paddle Agitators for Low-Viscosity Liquids
Paddle agitators are among the simplest and most effective tools for mixing low-viscosity liquids. These agitators feature paddle-shaped blades that extend across the tank, ensuring a uniform laminar flow. This design minimizes shearing, making paddle agitators ideal for applications where gentle mixing is required. You will often find them in industries like food, pharmaceuticals, and chemicals, where maintaining the integrity of the mixture is crucial.
For example, in the food industry, paddle agitators help blend syrups or other liquid ingredients without altering their texture. In chemical processes, they ensure even distribution of reactants, promoting consistent results. Their straightforward design also makes them easy to maintain, reducing downtime and operational costs. If you need reliable and efficient mixing for low-viscosity liquids, paddle agitators provide a practical solution.
Turbine Agitators for High-Speed Mixing
Turbine agitators are the go-to choice when high-speed mixing is essential. These agitators combine centrifugal and rotational motion, creating a powerful flow that ensures thorough blending. Their larger blade diameters allow them to handle a wide range of viscosities, making them versatile for various industrial applications. You can rely on turbine agitators for processes like emulsification and dispersion, where achieving a uniform mixture quickly is critical.
In the pharmaceutical industry, turbine agitators play a key role in creating stable emulsions for creams or ointments. In chemical manufacturing, they excel at dispersing solid particles into liquids, ensuring homogeneity. Their ability to balance flow and shear makes them suitable for both delicate and demanding tasks. By using turbine agitators, you can achieve efficient mixing while maintaining high product quality.
Helical Agitators for High-Viscosity Materials
Helical agitators are specifically designed to handle high-viscosity materials. Their unique helical blade structure allows them to move through thick mixtures with ease, ensuring even blending. These agitators are particularly effective in industries that deal with dense or sticky substances, such as adhesives, resins, or heavy creams.
For instance, in the cosmetics industry, helical agitators mix lotions or gels, ensuring a smooth and consistent texture. In industrial applications, they prevent sedimentation by continuously moving the material, even in challenging conditions. Their robust design ensures durability, making them a reliable choice for heavy-duty mixing tasks. When working with high-viscosity materials, helical agitators deliver the performance you need to maintain efficiency and quality.
Anchor Agitators for Specialized Applications
Anchor agitators excel in handling specialized mixing tasks, especially when working with highly viscous or shear-sensitive materials. Their unique design, featuring anchor-shaped blades that closely follow the contours of the tank, ensures thorough and consistent mixing. This makes them indispensable in industries where precision and care are paramount.
You can rely on anchor agitators for processes requiring gentle agitation. Their low-shear mixing capability prevents damage to delicate materials, preserving the integrity of your product. For example, in the cosmetics industry, they blend creams and lotions without compromising texture or quality. Similarly, in the food sector, they mix viscous sauces or syrups while maintaining their desired consistency.
Anchor agitators also prevent material buildup on tank walls. Their blades scrape the sides as they rotate, ensuring no residue remains. This feature not only enhances mixing efficiency but also reduces waste. In applications involving adhesives or resins, this scraping action ensures even distribution and prevents hardening along the tank’s surface.
These agitators are ideal for processes requiring minimal turbulence. Their controlled motion ensures uniform blending without introducing excessive air or foam into the mixture. This is particularly valuable in pharmaceutical production, where maintaining a stable and contamination-free environment is critical.
By choosing anchor agitators, you gain a reliable solution for challenging mixing tasks. Their robust design and specialized functionality make them a valuable asset in achieving consistent, high-quality results across various industries.
How to Choose the Right Agitator for Your Chemical Mixing Tank
Considering Tank Size and Shape
The size and shape of your tank play a critical role in determining the right agitator. Larger tanks require agitators with higher power to ensure thorough mixing across the entire volume. Smaller tanks, on the other hand, benefit from compact agitators that provide efficient mixing without overloading the system.
The tank’s shape also influences the agitator’s performance. Cylindrical tanks often pair well with vertical agitators, which create uniform flow patterns. Tanks with irregular shapes or flat bottoms may require specialized agitators, such as anchor or helical designs, to ensure consistent mixing. By matching the agitator to your tank’s dimensions, you can achieve optimal results and avoid inefficiencies.
Tip: Always measure your tank’s dimensions accurately before selecting an agitator. This ensures compatibility and prevents operational challenges.
Matching Agitator Type to Mixture Viscosity
Viscosity is one of the most important factors to consider when choosing an agitator. Low-viscosity liquids, like water or thin oils, mix easily and require agitators designed for high-speed operation. Paddle or propeller agitators work well in these scenarios, as they generate sufficient flow without excessive energy consumption.
For medium-viscosity mixtures, turbine agitators strike the perfect balance. Their design allows them to handle a range of viscosities while maintaining efficiency. High-viscosity materials, such as adhesives or creams, demand robust solutions. Helical or anchor agitators excel in these cases, as their unique blade structures ensure even blending of thick substances.
Key Insight: Matching the agitator type to the viscosity of your mixture ensures consistent results and prevents issues like incomplete mixing or material buildup.
Aligning Agitator Selection with Desired Outcomes
Your desired outcomes should guide your choice of agitator. If you aim to achieve rapid mixing, high-speed agitators like turbines are ideal. For processes requiring gentle agitation, such as blending delicate materials, paddle or anchor agitators offer better control.
Consider the specific goals of your operation. Are you looking to homogenize a mixture, suspend solids, or facilitate chemical reactions? Each task demands a different agitator design. For example, achieving uniform heat transfer in temperature-sensitive processes may require an agitator with advanced circulation capabilities.
Pro Tip: Clearly define your process objectives before selecting an agitator. This ensures that the equipment aligns with your operational needs and delivers the desired results.
By evaluating tank size, mixture viscosity, and your specific goals, you can confidently choose the right agitator for your chemical mixing tank. This careful selection process not only enhances efficiency but also ensures consistent product quality in every batch.
Challenges in Chemical Mixing Without Agitators
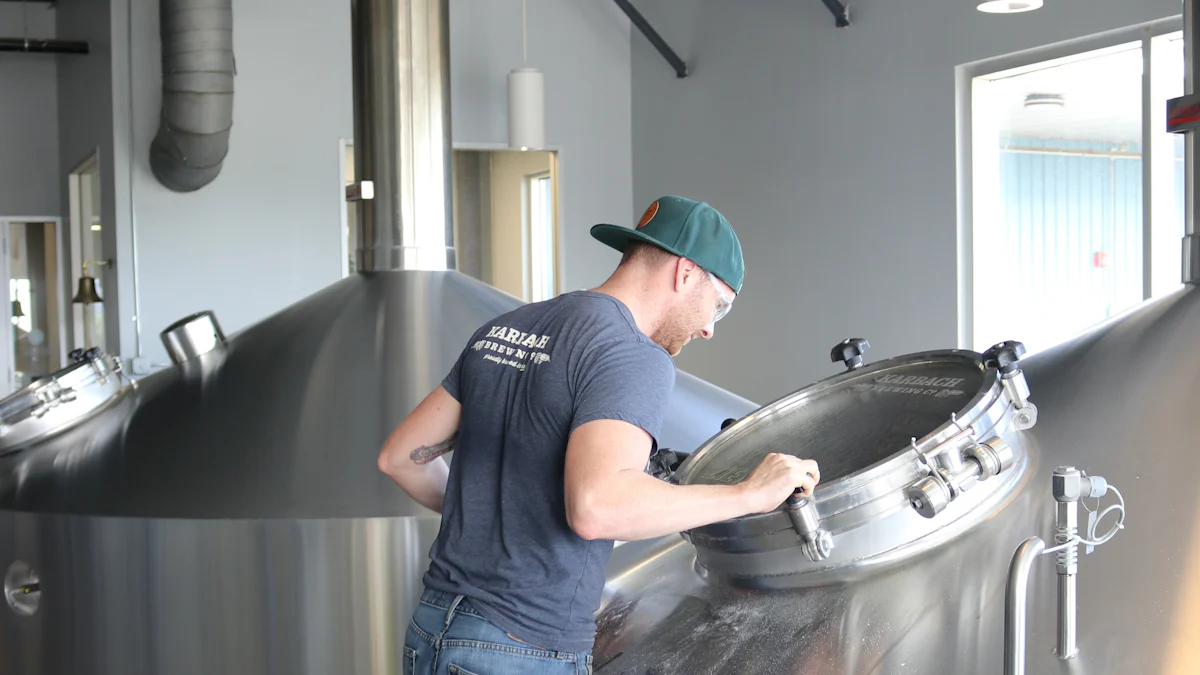
Inconsistent Mixtures and Poor Quality
Without an agitator, achieving a uniform mixture becomes nearly impossible. When you rely on natural diffusion or manual stirring, the components in your tank fail to blend evenly. This inconsistency leads to poor-quality products that do not meet industrial standards. For example, in chemical manufacturing, uneven mixing can result in products with varying concentrations, which compromises their effectiveness and reliability.
Agitators methodically transfer kinetic energy to the fluid, ensuring every particle moves and interacts. This process eliminates the risk of separation or sedimentation. Without this mechanical assistance, you face challenges like clumping in powders or uneven distribution of reactants. These issues not only reduce product quality but also increase waste, as batches may need to be discarded due to defects.
Key Insight: Uniform mixing is critical for industries like pharmaceuticals, food production, and chemicals. Agitators ensure consistency, which is essential for meeting strict quality standards.
Inefficient Heat Distribution
In chemical processes, maintaining a stable temperature is vital for success. Without an agitator, heat distribution within the tank becomes uneven. Hotspots form in certain areas, while other sections remain cooler. This imbalance disrupts chemical reactions, leading to incomplete or undesirable results. For instance, in exothermic reactions, localized overheating can damage the product or even pose safety risks.
Agitators play a crucial role in circulating materials, ensuring heat spreads evenly throughout the tank. This circulation prevents temperature fluctuations and maintains optimal conditions for reactions. Without this function, you may need to rely on excessive heating or cooling, which increases energy consumption and operational costs.
Did You Know? Modern agitator designs focus on energy efficiency. They optimize heat transfer, reducing the need for additional energy inputs and supporting sustainable practices.
Reduced Reaction Efficiency
Chemical reactions depend on the thorough interaction of reactants. Without an agitator, these substances fail to mix effectively, slowing down reaction rates and reducing efficiency. Incomplete reactions result in wasted materials and lower yields, which directly impact your production output.
Agitators enhance reaction efficiency by creating turbulence and increasing the surface area of contact between reactants. This movement ensures that every molecule participates in the reaction, maximizing output. Without this mechanical intervention, you risk producing subpar products that fail to meet industrial requirements.
Additionally, agitators improve mass transfer, a critical factor in many chemical processes. By continuously moving the mixture, they facilitate the exchange of heat, gases, or solutes, which accelerates reactions. Without this capability, your operations become less productive and more resource-intensive.
Takeaway: Incorporating an agitator into your chemical mixing tank boosts reaction efficiency, reduces waste, and ensures consistent results. Without one, you face significant challenges in maintaining productivity and quality.
Maintenance Tips for Agitators in Chemical Mixing Tanks
Regular Maintenance Practices
Regular maintenance ensures your agitator operates efficiently and lasts longer. Start by cleaning the agitator and its components frequently. This prevents material buildup, which can hinder performance. Lubricate moving parts, such as bearings and seals, to reduce friction and wear. Proper lubrication also minimizes the risk of overheating during operation.
Create a maintenance schedule to inspect the agitator at consistent intervals. During these checks, monitor vibration levels. Excessive vibrations often indicate misalignment or worn-out components. Addressing these issues early prevents further damage and costly repairs. Additionally, check for loose bolts or connections. Tighten them as needed to maintain stability and safety.
Pro Tip: Keep a detailed log of all maintenance activities. This helps you track patterns and identify recurring issues, making future troubleshooting more efficient.
Identifying Signs of Wear and Tear
Recognizing early signs of wear and tear can save you from unexpected downtime. Look for unusual noises during operation. Grinding or squealing sounds often signal problems with bearings or other internal components. Inspect the agitator blades for cracks, bends, or corrosion. Damaged blades reduce mixing efficiency and may compromise product quality.
Pay attention to changes in performance. If the agitator struggles to mix materials evenly or operates at inconsistent speeds, it may need immediate attention. Check for leaks around seals or gaskets. Leaks not only waste materials but also indicate potential seal failure.
Key Insight: Addressing minor issues promptly prevents them from escalating into major problems. This proactive approach extends the lifespan of your agitator and ensures uninterrupted operations.
Importance of Proper Installation
Proper installation lays the foundation for optimal agitator performance. Ensure the agitator aligns correctly with the tank. Misalignment causes uneven mixing and accelerates wear on components. Verify that the mounting structure is secure and stable. A poorly mounted agitator can vibrate excessively, leading to mechanical failures.
Choose the right agitator size and type for your tank and application. An undersized agitator struggles to perform, while an oversized one consumes unnecessary energy. Follow the manufacturer’s guidelines during installation to avoid errors. After installation, test the agitator to confirm it operates at the correct speed and performs as expected.
Did You Know? Improper installation accounts for a significant percentage of agitator failures. Taking the time to install it correctly ensures long-term reliability and efficiency.
By following these maintenance tips, you can keep your agitator in excellent condition. Regular care, early detection of issues, and proper installation not only enhance performance but also reduce operational costs. A well-maintained agitator ensures consistent mixing, helping you meet industrial standards and achieve production goals.
Innovations in Agitator Technology for Chemical Mixing Tanks
Energy-Efficient Agitator Designs
Energy efficiency has become a top priority in modern industrial processes. Agitator designs now focus on reducing energy consumption while maintaining optimal performance. Manufacturers have introduced advanced blade geometries that minimize drag and maximize fluid movement. These designs ensure efficient mixing with less power, helping you lower operational costs.
Variable-speed agitators offer another energy-saving solution. By adjusting the speed to match the specific requirements of your process, you can avoid unnecessary energy use. For example, low-viscosity liquids may require slower speeds, while high-viscosity materials benefit from higher speeds. This flexibility allows you to optimize energy usage without compromising mixing quality.
Fact: Studies highlight that applying proper agitation techniques not only improves energy efficiency but also supports sustainable practices in industrial operations.
Energy-efficient agitators also reduce heat generation during operation. Excessive heat can damage sensitive materials or increase cooling costs. By using designs that minimize friction and turbulence, you can maintain stable temperatures and protect your products. These innovations make energy-efficient agitators an essential choice for industries aiming to balance performance with sustainability.
Smart Agitators with Advanced Sensors
Smart technology has revolutionized agitator functionality. Modern agitators now come equipped with advanced sensors that monitor key parameters like speed, torque, and temperature. These sensors provide real-time data, allowing you to make informed decisions and maintain precise control over your mixing process.
For instance, sensors can detect changes in viscosity or flow patterns, alerting you to potential issues before they escalate. This proactive approach minimizes downtime and ensures consistent product quality. In addition, smart agitators can integrate with automated systems, enabling remote monitoring and control. You can adjust settings or troubleshoot problems without being physically present, saving time and resources.
Insight: Smart agitators enhance safety by detecting irregularities such as excessive vibrations or overheating. Early warnings help you address these issues promptly, preventing accidents and equipment damage.
Predictive maintenance is another advantage of smart agitators. By analyzing sensor data, you can identify wear and tear on components and schedule maintenance before failures occur. This reduces unexpected breakdowns and extends the lifespan of your equipment. Smart agitators combine efficiency, reliability, and convenience, making them a valuable asset in modern chemical mixing tanks.
Use of Durable, Corrosion-Resistant Materials
Durability is crucial for agitators operating in demanding industrial environments. Manufacturers now use high-quality materials like stainless steel and corrosion-resistant alloys to ensure long-lasting performance. These materials withstand harsh conditions, including extreme temperatures, high pressure, and exposure to aggressive chemicals.
Corrosion-resistant materials prevent damage caused by chemical reactions, preserving the integrity of your agitator. This is especially important in industries like pharmaceuticals and food production, where contamination risks must be minimized. By choosing agitators made from durable materials, you can maintain a clean and safe mixing environment.
Key Finding: Research shows that using corrosion-resistant materials reduces maintenance costs and downtime, ensuring reliable operation even under challenging conditions.
Durable materials also enhance the structural strength of agitators. This allows them to handle heavy loads and high-viscosity materials without deforming or breaking. Whether you are mixing adhesives, resins, or other dense substances, robust agitators deliver consistent performance. Investing in durable, corrosion-resistant agitators ensures long-term efficiency and reliability for your chemical mixing tanks.
Why Chenma Machinery Is a Leader in Chemical Mixing Tanks with Agitators
Expertise in Custom Stainless Steel Tanks
Chenma Machinery stands out as a leader in the industry due to its unmatched expertise in designing and manufacturing custom stainless steel tanks. With over 15 years of experience, Chenma has developed a deep understanding of the unique requirements of various industries, including chemical processing, food and beverage, and fermentation. This expertise allows you to receive tanks tailored precisely to your operational needs, ensuring optimal performance and efficiency.
The company’s engineers work closely with you to create solutions that align with your specific processes. Whether you need tanks for high-viscosity materials or specialized applications, Chenma delivers designs that meet your exact specifications. By incorporating advanced features like corrosion-resistant materials and precision-engineered agitators, Chenma ensures that your chemical mixing tanks with agitators perform reliably under demanding conditions.
Chenma’s commitment to customization extends beyond design. The company also adapts its tanks to fit seamlessly into your existing systems, minimizing downtime and maximizing productivity. This level of flexibility makes Chenma a trusted partner for businesses seeking high-quality, bespoke solutions.
Advanced Manufacturing Capabilities
Chenma Machinery operates a state-of-the-art production facility spanning 20,000 square meters. Equipped with cutting-edge machinery, this facility enables the company to produce even the most technically demanding designs. You benefit from tanks that are not only durable but also engineered with precision to meet the highest industry standards.
The company collaborates with world-renowned brands like Siemens, Schneider, ABB, and IFM to integrate high-quality components into its products. These partnerships ensure that your tanks come equipped with reliable motors, valves, pumps, and control systems. By leveraging these advanced technologies, Chenma enhances the functionality and efficiency of its chemical mixing tanks with agitators.
Chenma’s manufacturing capabilities also include rigorous quality control processes. Every tank undergoes thorough testing to ensure it meets safety and performance standards. This attention to detail guarantees that you receive a product that delivers consistent results and withstands the challenges of industrial operations.
Commitment to Quality and Safety Standards
Chenma Machinery prioritizes quality and safety in every aspect of its operations. The company has earned multiple certifications, including ISO9001-2005 for quality management, ISO14001-2015 for environmental management, and OHSAS18001-2007 for occupational health and safety. These certifications reflect Chenma’s dedication to providing you with products that meet stringent global standards.
The company’s stainless steel tanks are designed to ensure safe and efficient mixing processes. By using corrosion-resistant materials and precision-engineered components, Chenma minimizes the risk of contamination and equipment failure. This focus on safety is particularly important in industries like pharmaceuticals and food production, where maintaining product integrity is critical.
Chenma also offers comprehensive technical support to help you maintain the performance of your tanks. From installation to routine maintenance, the company provides guidance to ensure your equipment operates safely and efficiently. This commitment to customer satisfaction reinforces Chenma’s reputation as a reliable provider of chemical mixing tanks with agitators.
Turnkey Solutions for Chemical Mixing Needs
Turnkey solutions simplify the process of acquiring and implementing chemical mixing systems by providing you with a comprehensive, ready-to-use package. These solutions address every stage of the process, from design and manufacturing to installation and technical support. By choosing a turnkey approach, you eliminate the need to coordinate multiple vendors or manage complex integrations, saving time and reducing operational challenges.
Shandong Chenma Machinery Co., Ltd. excels in delivering turnkey solutions for chemical mixing tanks with agitators. With over 15 years of experience, Chenma has developed a deep understanding of diverse industrial needs. The company offers end-to-end services that ensure your mixing system is tailored to your specific requirements. Here’s how Chenma’s turnkey solutions stand out:
Custom Design and Engineering
Chenma’s team of skilled engineers works closely with you to design tanks and agitators that align with your operational goals. Whether you need a system for high-viscosity materials or precise temperature control, Chenma creates solutions that meet your exact specifications. The company’s expertise in stainless steel tank manufacturing ensures durability and reliability, even in demanding environments.State-of-the-Art Manufacturing
Chenma operates a 20,000 m² production facility equipped with advanced machinery. This allows the company to produce technically demanding designs with precision. By integrating high-quality components from trusted brands like Siemens, Schneider, ABB, and IFM, Chenma ensures that your system performs efficiently and reliably. Every tank undergoes rigorous testing to meet global safety and quality standards.Seamless Installation and Commissioning
Chenma’s turnkey solutions include professional installation and commissioning services. The company’s experts ensure that your chemical mixing tanks with agitators are installed correctly and integrated seamlessly into your existing processes. This minimizes downtime and allows you to start operations quickly.Comprehensive Technical Support
After installation, Chenma provides ongoing technical support to help you maintain optimal performance. The company offers training for your team, ensuring they understand how to operate and maintain the equipment effectively. Regular maintenance services and prompt troubleshooting further enhance the reliability of your system.Adaptability Across Industries
Chenma’s turnkey solutions cater to a wide range of industries, including chemical processing, food and beverage, and pharmaceuticals. The company’s ability to customize tanks and agitators for specific applications makes it a trusted partner for businesses with unique requirements.
By choosing Chenma’s turnkey solutions, you gain access to a complete package that simplifies your operations and enhances efficiency. From initial design to ongoing support, Chenma ensures that every aspect of your chemical mixing system meets the highest standards of quality and performance.
Agitators are indispensable for achieving efficient and effective chemical mixing. They ensure uniformity in mixtures, optimize chemical reactions, and maintain consistent heat transfer. These functions directly enhance product quality, reduce material waste, and improve safety in industrial processes. By selecting the right agitator and committing to regular maintenance, you can ensure long-term operational efficiency and reliability.
Key Insight: Choosing the right equipment for your mixing needs is vital for maintaining consistency and optimizing resources.
Chenma Machinery provides innovative solutions tailored to meet diverse industrial requirements. Their expertise in custom stainless steel tanks and advanced manufacturing ensures you receive reliable and high-performing equipment.
FAQ
How do I know which agitator I need for my mixing process?
To choose the right agitator, you need to consider three key factors: the viscosity of your mixture, the size and shape of your tank, and your desired outcomes. For low-viscosity liquids like water or thin oils, paddle or propeller agitators work best. For medium-viscosity mixtures, turbine agitators provide a balance of speed and efficiency. High-viscosity materials, such as adhesives or creams, require helical or anchor agitators for effective blending. Always match the agitator type to your specific application to ensure consistent results.
Tip: Consult with an expert or manufacturer to evaluate your tank dimensions and process requirements before making a decision.
What are the main benefits of using agitators in chemical mixing tanks?
Agitators offer several advantages that improve your mixing processes. They ensure uniform mixtures, enhance heat transfer, and facilitate chemical reactions. By preventing sedimentation and residue buildup, agitators reduce material waste and improve product quality. Additionally, they increase operational efficiency by speeding up mixing times and minimizing energy consumption. These benefits make agitators indispensable for industries like pharmaceuticals, food production, and chemical manufacturing.
Can agitators handle high-viscosity materials effectively?
Yes, agitators can handle high-viscosity materials when you choose the right type. Helical and anchor agitators are specifically designed for thick or sticky substances. Their robust blades move through dense mixtures with ease, ensuring even blending. These agitators also prevent material buildup on tank walls, which is common with viscous materials. By selecting the appropriate agitator, you can maintain efficiency and achieve consistent results, even with challenging substances.
How do agitators improve safety in industrial processes?
Agitators enhance safety by maintaining controlled conditions during mixing. They ensure uniform temperature and pressure distribution, which prevents dangerous situations like overheating or pressure buildup. Automated agitators reduce the need for manual intervention, minimizing the risk of accidents caused by human error. Additionally, their consistent operation prevents sudden surges or imbalances, creating a safer working environment for your team.
What maintenance practices keep agitators running efficiently?
Regular maintenance is essential for optimal agitator performance. Clean the agitator and its components frequently to prevent material buildup. Lubricate moving parts, such as bearings and seals, to reduce wear and overheating. Inspect the agitator for signs of damage, like cracks or corrosion on the blades. Monitor vibration levels and tighten any loose connections. Following a maintenance schedule ensures your agitator operates efficiently and lasts longer.
Pro Tip: Keep a maintenance log to track inspections and identify recurring issues.
Are there energy-efficient agitators available?
Yes, modern agitators feature energy-efficient designs that reduce power consumption. Advanced blade geometries minimize drag while maximizing fluid movement, ensuring effective mixing with less energy. Variable-speed agitators allow you to adjust the speed based on your process needs, further optimizing energy usage. These innovations not only lower operational costs but also support sustainable practices in industrial operations.
How do smart agitators benefit industrial processes?
Smart agitators come equipped with advanced sensors that monitor key parameters like speed, torque, and temperature. These sensors provide real-time data, helping you maintain precise control over your mixing process. Smart technology enables predictive maintenance by identifying wear and tear early, reducing unexpected downtime. Additionally, smart agitators integrate with automated systems, allowing remote monitoring and adjustments for greater convenience and efficiency.
What materials are used to make durable agitators?
Manufacturers use high-quality materials like stainless steel and corrosion-resistant alloys to ensure agitators withstand harsh industrial conditions. These materials resist damage from extreme temperatures, high pressure, and aggressive chemicals. Corrosion-resistant materials also prevent contamination, making them ideal for industries like pharmaceuticals and food production. Durable agitators maintain their structural integrity, even under heavy loads, ensuring reliable performance over time.
How does Chenma Machinery support custom agitator solutions?
Chenma Machinery specializes in designing and manufacturing custom stainless steel tanks with agitators tailored to your specific needs. Their engineers collaborate with you to create solutions that align with your operational goals. Whether you need tanks for high-viscosity materials or specialized applications, Chenma delivers precision-engineered designs. Their turnkey solutions include design, manufacturing, installation, and ongoing technical support, ensuring seamless integration into your processes.
Key Insight: Chenma’s expertise in customization ensures you receive equipment that meets the highest standards of quality and performance.
Why should I invest in a chemical mixing tank with an agitator?
Investing in a chemical mixing tank with an agitator enhances your production efficiency and product quality. Agitators ensure uniform mixing, optimize chemical reactions, and maintain consistent heat transfer. These functions reduce material waste, improve safety, and lower operational costs. By choosing the right agitator and maintaining it properly, you can achieve long-term reliability and meet the demands of modern industrial standards.