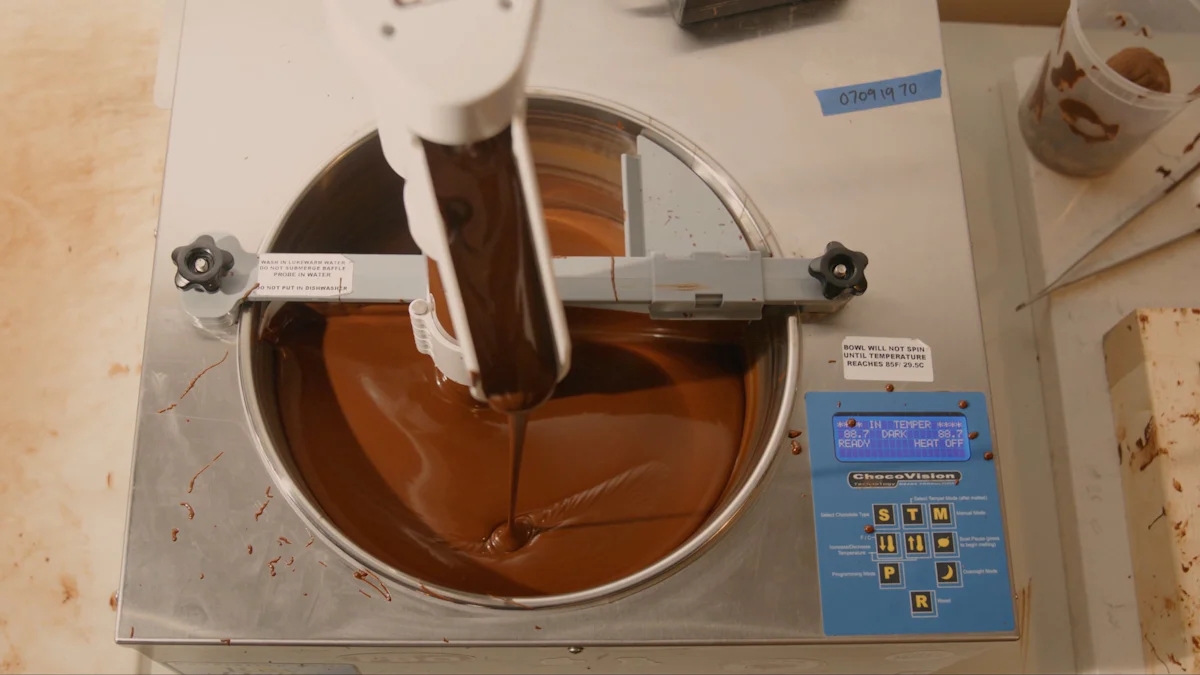
Chemical mixing tanks with agitators play a vital role in modern industries. These tanks ensure that materials mix uniformly, creating consistent and high-quality products. You rely on them for processes like blending, homogenizing, and chemical reactions. Their ability to handle diverse chemicals makes them indispensable in achieving efficient industrial mixing. Whether in pharmaceuticals, food processing, or chemical manufacturing, these tanks simplify operations and enhance productivity. By maintaining uniformity and safety, they help you meet industry standards and deliver reliable results every time.
What Are Chemical Mixing Tanks with Agitators?
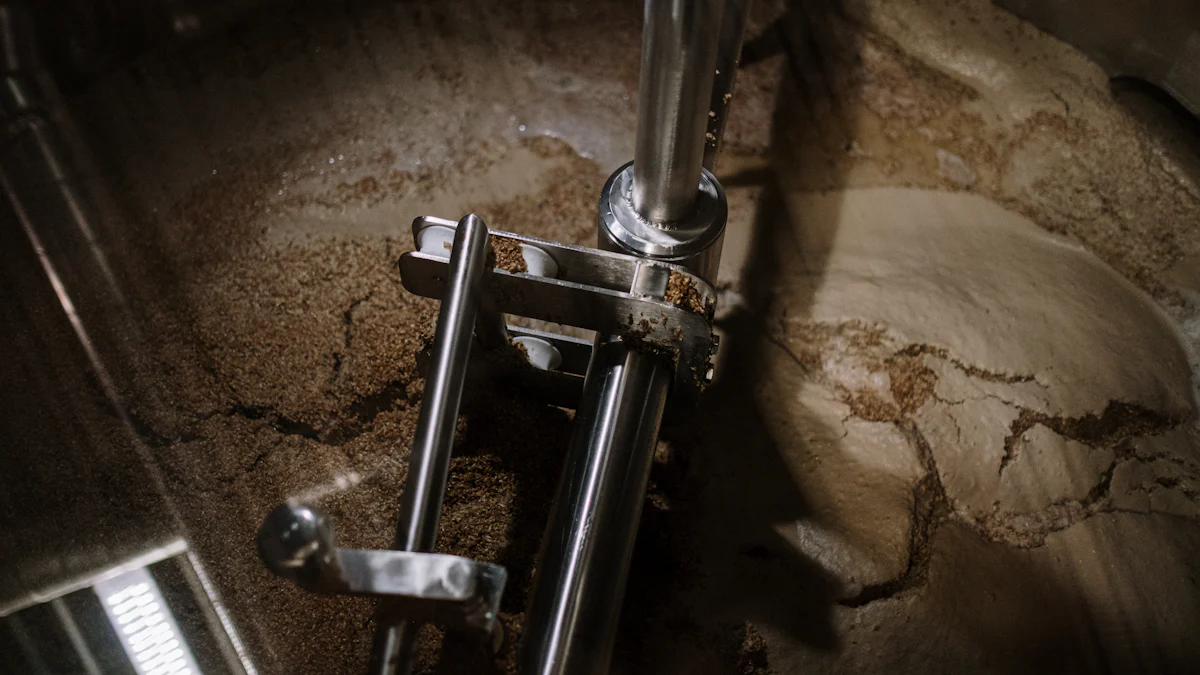
Chemical mixing tanks with agitators are essential tools in industrial processes. They serve as vessels where you can blend, homogenize, or mix various substances, ensuring uniformity and consistency. These tanks are designed to handle liquids, powders, and even gases, making them versatile for a wide range of applications. By using an agitator tank, you can achieve efficient mixing, which is crucial for producing high-quality products.
Definition and Purpose
A chemical mixing tank with an agitator is a specialized container equipped with a mechanical device that stirs or mixes the contents inside. The primary purpose of these tanks is to create a homogeneous mixture by combining different materials. Whether you need to dissolve solids into liquids, emulsify immiscible liquids, or maintain a suspension, these tanks provide the solution. Their design ensures that the mixing process is efficient, reducing time and energy consumption while delivering consistent results.
“Agitators operate by rotating immersed impellers at a controlled speed, which helps to homogenize the media inside a tank.”
These tanks are indispensable in industries like pharmaceuticals, food processing, and chemical manufacturing. For example, in the food industry, they help you mix ingredients uniformly, ensuring product quality. In chemical manufacturing, they enable precise reactions by thoroughly blending reactants.
Key Components and Features
Understanding the main components of an agitator tank helps you appreciate its functionality. These tanks typically consist of:
- Tank Body: The container that holds the materials to be mixed. It can vary in size and shape depending on your needs.
- Agitator: The mechanical device responsible for mixing. It includes impellers, which rotate to create movement within the tank.
- Motor and Drive System: These power the agitator, allowing you to control the speed and intensity of mixing.
- Baffles: Internal structures that prevent the contents from spinning in a vortex, ensuring effective mixing.
- Seals and Bearings: These components maintain the integrity of the system, preventing leaks and ensuring smooth operation.
Some tanks also feature additional elements like heating or cooling jackets, which allow you to regulate the temperature during mixing. Food-grade mixing tanks, for instance, often include built-in scrapers to remove debris from the tank walls, ensuring thorough mixing and easy cleaning.
Materials Used in Construction
The materials used to construct chemical mixing tanks play a critical role in their performance and durability. Stainless steel is the most common choice due to its strength, corrosion resistance, and ease of cleaning. This makes it ideal for industries like food processing and pharmaceuticals, where hygiene is paramount.
Other materials include:
- Plastic: Lightweight and cost-effective, suitable for less demanding applications.
- Glass: Offers excellent chemical resistance but is less durable than metal.
- Rubber and Alloys: Used for specific applications requiring unique properties, such as flexibility or enhanced corrosion resistance.
When selecting a tank, you must consider the chemical compatibility of the materials with the substances you plan to mix. For example, stainless steel is often preferred for its ability to withstand harsh chemicals without degrading. However, for certain applications, polyethylene or other specialized materials may be more appropriate.
By choosing the right materials and understanding chemical mixing tanks, you can ensure optimal performance and longevity for your equipment.
Common Designs and Configurations
Chemical mixing tanks come in various designs and configurations to meet the diverse needs of industrial processes. Each design serves a specific purpose, ensuring optimal performance based on the materials being mixed and the desired outcomes. Understanding these configurations helps you select the right tank for your application.
1. Cylindrical Tanks
Cylindrical tanks are among the most common designs. Their round shape promotes efficient mixing by minimizing dead zones where materials might settle. These tanks often feature flat, dished, or cone-shaped bottoms. Cone-bottomed tanks, for instance, allow for easy drainage and are ideal for applications requiring complete material discharge.
2. Square Tanks
Square tanks provide a compact solution for facilities with limited space. Their angular design makes them suitable for processes where baffles are necessary to prevent vortex formation. While less common than cylindrical tanks, square tanks can be customized to fit specific operational requirements.
3. Cone-Bottom Tanks
Cone-bottom tanks are designed for applications requiring thorough mixing and complete drainage. The conical base ensures that all materials flow toward the outlet, reducing waste and simplifying cleaning. These tanks are particularly useful in industries like water treatment and chemical manufacturing, where residue-free discharge is essential.
4. Vertical vs. Horizontal Tanks
Vertical tanks are the standard choice for most mixing applications. Their upright design allows for efficient use of space and effective mixing of large volumes. Horizontal tanks, on the other hand, are better suited for processes involving lower volumes or when height restrictions exist in your facility.
5. Specialized Configurations
Some tanks are tailored for specific industries or processes. For example:
- Jacketed Tanks: These tanks include an outer layer for heating or cooling, making them ideal for temperature-sensitive processes.
- Sanitary Tanks: Designed for the food and pharmaceutical industries, these tanks feature smooth surfaces and easy-to-clean components to maintain hygiene.
- Pressurized Tanks: Used in applications requiring controlled pressure, such as chemical reactions or fermentation.
“Mixing tanks for the chemical industry should be made of chemically neutral components to avoid reactions with substances.”
When choosing a configuration, consider factors like the type of material being mixed, the required volume, and the chemical properties involved. For instance, cylindrical tanks with baffles are excellent for blending liquids, while cone-bottom tanks work well for handling viscous or sediment-prone materials.
By understanding these common designs and configurations, you can ensure that your mixing tank aligns with your operational needs, enhancing efficiency and product quality.
Understanding Agitators and Their Role in Mixing
Agitators are essential components in mixing systems, ensuring that materials combine effectively to achieve uniformity. Whether you work in chemical manufacturing, food processing, or pharmaceuticals, understanding how agitators function and their various types can help you optimize your processes.
What Are Agitators?
An agitator is a mechanical device designed to mix, blend, or stir substances within a tank or vessel. It operates by rotating impellers, which create movement in the tank’s contents. This motion ensures that materials—whether liquids, solids, or gases—combine evenly. Agitators play a critical role in industrial processes, as they help maintain consistency, enhance reaction rates, and prevent sedimentation.
“Agitation helps dissolve solids, emulsify immiscible liquids, and maintain suspensions, making it indispensable in industrial mixing.”
Industrial agitators are engineered to handle a wide range of applications. For example, in chemical manufacturing, they enable precise reactions by thoroughly blending reactants. In the food industry, they ensure that ingredients mix uniformly, resulting in consistent product quality. By using an agitator, you can achieve efficient fluid mixing, which is vital for producing high-quality outputs.
Types of Agitators
Different processes require specific types of agitators to meet their unique mixing needs. Below are the most common agitator types and their applications:
Paddle Agitators
Paddle agitators feature flat blades attached to a central shaft. These blades move through the tank’s contents, creating a gentle mixing action. Paddle agitators are ideal for mixing liquids with low viscosity or for processes where minimal shear is required. They are commonly used in water treatment and food processing.
Propeller Agitators
Propeller agitators use blades shaped like a ship’s propeller to create axial flow. This design moves materials vertically, ensuring thorough mixing. These agitators work well for low-viscosity liquids and are often found in industries like chemical manufacturing and wastewater treatment.
Turbine Agitators
Turbine agitators consist of multiple blades mounted on a central hub. These blades generate both radial and axial flow, making them suitable for medium- to high-viscosity fluids. Turbine agitators are versatile and widely used in industries requiring efficient mixing, such as pharmaceuticals and paints.
Helical Agitators
Helical agitators feature spiral-shaped blades that create a smooth, continuous flow. These agitators excel at mixing highly viscous materials, such as creams, gels, and pastes. Their design minimizes energy consumption while ensuring effective mixing, making them a popular choice in the cosmetics and food industries.
Anchor Agitators
Anchor agitators have a large, anchor-shaped blade that moves slowly through the tank. This design is particularly effective for mixing thick, viscous materials. Anchor agitators scrape the tank walls, preventing material buildup and ensuring uniform mixing. They are commonly used in processes involving adhesives, resins, and other heavy substances.
How Agitators Enhance Efficient Industrial Mixing
Agitators improve mixing efficiency by creating controlled movement within the tank. This movement ensures that all materials interact, eliminating dead zones and preventing sedimentation. By optimizing the mixing process, agitators reduce production time and energy consumption.
Modern agitation systems incorporate advanced designs to maximize performance. For instance, research on blade optimization has shown that specific shapes and configurations can enhance mixing efficiency. Studies using tools like FEM (Finite Element Method) have demonstrated how design improvements can increase agitation performance while minimizing energy costs.
“Automated agitation systems with optimized agitators save energy and reduce mixing time, making them essential for modern industrial processes.”
Agitators also allow you to customize mixing parameters, such as speed and impeller type, to suit your specific needs. For example, high-speed agitators work well for low-viscosity liquids, while low-speed options are better for viscous materials. By selecting the right agitator and adjusting its settings, you can achieve consistent results and improve overall productivity.
Understanding the types of industrial agitators and their role in mixing helps you make informed decisions for your operations. Whether you need to blend liquids, dissolve solids, or maintain suspensions, choosing the right agitator ensures efficient and reliable performance.
Industrial Applications of Chemical Mixing Tanks with Agitators
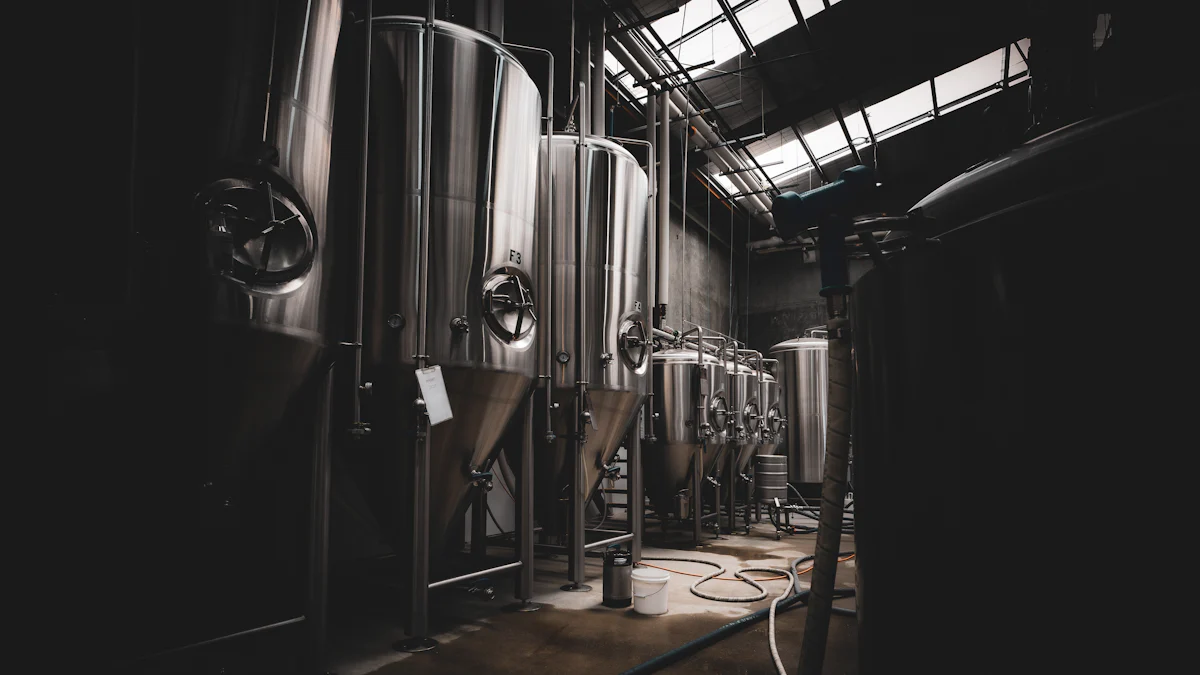
Chemical mixing tanks with agitators are indispensable across various industries. They ensure the efficient mixing of materials, enabling you to achieve uniformity, consistency, and safety in your processes. These tanks support large-scale operations by handling diverse substances, from liquids to solids, while preventing contamination. Below, you’ll explore how these tanks play a pivotal role in three key sectors.
Pharmaceuticals and Biotechnology
In pharmaceuticals and biotechnology, precision and consistency are non-negotiable. Chemical mixing tanks with agitators help you meet these demands by ensuring thorough mixing during drug formulation, vaccine production, and other critical processes. For example, when producing liquid medications or suspensions, these tanks allow you to blend active ingredients uniformly, ensuring each dose meets quality standards.
Biotechnology applications often involve sensitive biological materials. Agitator tanks maintain controlled environments for processes like fermentation and cell culture. By regulating temperature, pH, and agitation speed, you can optimize conditions for microbial growth or biochemical reactions. This precision ensures high yields and product purity, which are essential in this industry.
Key takeaway: These tanks enable you to maintain strict quality control, ensuring compliance with regulatory standards like GMP (Good Manufacturing Practices).
Food and Beverage Processing
In the food and beverage industry, chemical mixing tanks with agitators streamline production and enhance product quality. Whether you’re blending sauces, mixing beverages, or preparing dairy products, these tanks ensure uniformity in texture, flavor, and appearance. For instance, when producing carbonated drinks, agitators help dissolve gases evenly, creating a consistent product.
Sanitary-grade tanks are particularly valuable in this sector. Their smooth surfaces and easy-to-clean designs prevent bacterial growth, ensuring food safety. Additionally, agitators equipped with scrapers can handle viscous materials like syrups or pastes, preventing residue buildup on tank walls. This feature reduces waste and simplifies cleaning, saving you time and resources.
Pro tip: Using jacketed tanks allows you to control temperatures during processes like pasteurization or cooling, ensuring optimal results.
Water and Wastewater Treatment
Water and wastewater treatment facilities rely heavily on chemical mixing tanks with agitators to manage purification processes. These tanks help you mix chemicals like coagulants, flocculants, and disinfectants into water, ensuring even distribution and effective treatment. For example, during coagulation, agitators disperse chemicals that bind impurities, making them easier to remove.
In wastewater treatment, agitator tanks play a crucial role in biological processes. They maintain oxygen levels in aeration tanks, supporting microbial activity that breaks down organic matter. Additionally, these tanks prevent sedimentation by keeping solids suspended, ensuring efficient treatment and reducing operational issues.
Did you know? Properly designed agitators can reduce energy consumption while maintaining effective mixing, making your operations more sustainable.
By understanding the diverse applications of chemical mixing tanks with agitators, you can appreciate their value in achieving efficiency and quality across industries. Whether you’re producing pharmaceuticals, processing food, or treating water, these tanks simplify your operations and enhance outcomes.
Chemical Manufacturing
Chemical manufacturing relies heavily on chemical mixing tanks equipped with agitators to ensure efficient and precise production processes. These tanks allow you to mix raw materials uniformly, creating consistent products that meet industry standards. Whether you are producing detergents, dyes, or water treatment chemicals, the role of an agitator in achieving homogeneity cannot be overstated.
Agitators in chemical manufacturing help you blend materials with varying viscosities and densities. For example, when combining pigments and solvents to create paints or coatings, industrial agitators ensure even dispersion, preventing clumps or inconsistencies. Additionally, these tanks support chemical reactions by maintaining uniform conditions, such as temperature and concentration, throughout the process.
“Mixing tanks are essential equipment for businesses where substances need to be mixed together.”
The versatility of industrial agitators makes them indispensable in this sector. You can use them for emulsifying immiscible liquids, dissolving solids into liquids, or maintaining suspensions. By selecting the right type of agitator, such as a turbine or propeller design, you can optimize your mixing process and reduce operational costs. This efficiency not only enhances productivity but also ensures compliance with regulatory guidelines specific to the chemical industry.
Paints, Coatings, and Adhesives
In the production of paints, coatings, and adhesives, chemical mixing tanks with agitators play a pivotal role. These tanks allow you to achieve the perfect consistency and texture required for high-quality products. For instance, when manufacturing adhesives, agitators ensure that all components, including polymers and additives, mix thoroughly to create a strong and reliable bond.
Industrial agitators are particularly effective in dispersing pigments and fillers in paint production. They prevent sedimentation and ensure that the final product has a uniform color and finish. For coatings, agitators help you achieve the desired viscosity, making the application process smoother and more efficient. Anchor agitators, known for their ability to handle viscous materials, are often used in these applications to scrape tank walls and prevent material buildup.
“Mixing tanks are widely used in chemical production processes for efficient mixing of materials with different components.”
By using advanced agitation systems, you can also reduce energy consumption and mixing time. This not only lowers production costs but also minimizes environmental impact, aligning with sustainable manufacturing practices. Whether you are producing water-based paints or solvent-based adhesives, the right agitator ensures consistent quality and performance.
Alcohol and Fermentation Processes (Chenma’s Expertise)
Alcohol and fermentation processes demand precision and consistency, making chemical mixing tanks with agitators essential in this field. At Chenma, we specialize in designing and manufacturing stainless steel tanks tailored for alcohol production, including wine, cider, and liquors. Our expertise ensures that you achieve optimal fermentation conditions, resulting in high-quality products.
Agitators in fermentation tanks help you maintain uniformity in temperature and nutrient distribution. This consistency is crucial for microbial activity, which drives the fermentation process. For example, in wine production, agitators ensure that yeast and sugar mix evenly, promoting efficient fermentation and enhancing flavor profiles.
“Mixing tanks for the chemical industry should be made of chemically neutral components to avoid reactions with substances.”
Chenma’s tanks feature advanced designs, such as jacketed configurations, to regulate temperature during fermentation. Our industrial agitators are engineered to handle the unique challenges of alcohol production, including mixing viscous musts or maintaining gentle agitation to preserve delicate flavors. By choosing Chenma’s solutions, you benefit from customized equipment that meets your specific needs while adhering to the highest safety and quality standards.
How to Select the Right Agitator Tank for Your Needs
Choosing the right agitator tank is essential for achieving efficient and reliable mixing in your industrial processes. By focusing on key factors like chemical compatibility, tank size, and agitator type, you can ensure that your equipment meets your specific needs. Below, you’ll find a detailed guide to help you make an informed decision.
Chemical Compatibility and Material Selection
The materials used in your agitator tank must align with the chemical properties of the substances you plan to mix. This ensures durability and prevents unwanted reactions. For example, stainless steel is a popular choice due to its corrosion resistance and strength. It works well for industries like food processing and pharmaceuticals, where hygiene and chemical neutrality are critical.
Other material options include:
- Plastic: Lightweight and cost-effective, suitable for non-corrosive and less demanding applications.
- Rubber-lined tanks: Ideal for handling abrasive or corrosive substances.
- Glass-lined tanks: Excellent for highly reactive chemicals but less durable than metal options.
“Mixing tanks for the chemical industry should be made of chemically neutral components to avoid reactions with substances.”
When selecting materials, always consider the long-term impact. For instance, if you work with acidic or alkaline substances, prioritize materials that resist corrosion to extend the tank’s lifespan. Matching the material to your process requirements ensures safety, efficiency, and cost-effectiveness.
Tank Size and Volume Considerations
The size and volume of your agitator tank directly influence its performance and suitability for your operations. Start by evaluating the volume of materials you need to mix. Oversized tanks may lead to inefficient mixing, while undersized ones can cause overflow or inadequate blending.
Key factors to consider include:
- Process Volume: Determine the maximum and minimum volumes your process requires. This helps you select a tank that accommodates fluctuations in production.
- Liquid Level to Diameter Ratio: Aim for a ratio close to 1-to-1 or 0.8 for optimal mixing. This ensures uniform agitation and minimizes dead zones.
- Space Constraints: Assess the available space in your facility. Vertical tanks save floor space, while horizontal tanks fit better in height-restricted areas.
“Cylindrical tanks with baffles are excellent for blending liquids, while cone-bottom tanks work well for handling viscous or sediment-prone materials.”
By carefully analyzing these factors, you can choose a tank size that balances efficiency and practicality, ensuring smooth operations without unnecessary costs.
Choosing the Right Agitator Type and Power
Selecting the right industrial agitator is crucial for achieving the desired mixing results. The type of agitator and its power must align with your process requirements and the properties of the materials being mixed.
Steps to Choose the Right Agitator:
- Identify Material Properties: Consider viscosity, density, and solid content. For example, low-viscosity liquids work well with propeller agitators, while high-viscosity materials require helical or anchor agitators.
- Determine Mixing Goals: Define whether you need blending, suspension, or emulsification. Each goal requires a specific agitator configuration based on process requirements.
- Calculate Power Needs: The power requirement depends on factors like impeller speed, tank size, and material properties. Ensure the motor provides sufficient power to achieve uniform mixing without overloading.
“Automated agitation systems with optimized agitators save energy and reduce mixing time, making them essential for modern industrial processes.”
By selecting the right agitator type and power, you can enhance efficiency, reduce energy consumption, and achieve consistent results. For example, turbine agitators offer versatility for medium-viscosity fluids, while anchor agitators excel in handling thick, viscous materials.
Making the right choices when selecting an agitator tank involves understanding your process needs, material compatibility, and operational goals. By following these guidelines, you can ensure that your equipment delivers optimal performance and supports your industrial objectives.
Process-Specific Requirements (e.g., temperature, pressure)
Understanding the specific requirements of your process is essential when selecting an agitator tank. Factors like temperature, pressure, and mixing conditions directly impact the tank’s design and performance. By tailoring your equipment to meet these needs, you can ensure efficient and reliable operations.
Temperature Control
Temperature plays a critical role in many industrial processes. Whether you need to heat, cool, or maintain a specific temperature, your tank must support these requirements. For example:
Heating Needs: If your process involves heating, consider tanks with built-in heating jackets or coils. These features allow you to regulate the temperature of the contents efficiently. Industries like food processing and chemical manufacturing often rely on this capability for processes like pasteurization or chemical reactions.
Cooling Applications: For processes requiring cooling, tanks with cooling jackets or external chillers are ideal. These systems help maintain low temperatures, which is crucial for applications like fermentation or preserving sensitive biological materials.
Temperature Uniformity: Agitators enhance temperature uniformity by circulating the contents. This prevents hot or cold spots, ensuring consistent results throughout the tank.
“Jacketed tanks with integrated heating or cooling systems provide precise temperature control, making them indispensable for temperature-sensitive processes.”
When evaluating temperature requirements, consider the range and stability needed for your process. For instance, high-temperature applications may require tanks made from materials like stainless steel, which can withstand extreme heat without degrading.
Pressure Considerations
Pressure is another vital factor to address when selecting an agitator tank. Some processes operate under atmospheric pressure, while others require pressurized or vacuum conditions. Here’s how pressure impacts your choice:
Pressurized Tanks: If your process involves high-pressure conditions, choose tanks designed to handle these demands. Pressurized tanks are common in industries like chemical manufacturing, where reactions occur under controlled pressure to enhance efficiency or safety.
Vacuum Applications: For processes requiring a vacuum, such as distillation or solvent recovery, opt for tanks with vacuum-rated designs. These tanks prevent air infiltration and maintain the desired vacuum level.
Safety Features: Tanks operating under pressure or vacuum must include safety features like pressure relief valves or vacuum breakers. These components protect against overpressure or implosion, ensuring safe operation.
“Pressurized and vacuum-rated tanks are essential for processes requiring controlled pressure conditions, such as chemical reactions or distillation.”
When assessing pressure requirements, consider the maximum and minimum operating pressures of your process. Ensure that the tank’s design and materials can withstand these conditions without compromising performance or safety.
Agitation Under Specific Conditions
Certain processes demand agitation under unique conditions, such as high viscosity, extreme temperatures, or varying pressure levels. In these cases, you must select an agitator capable of meeting these challenges. For example:
High-Viscosity Materials: Use anchor or helical agitators for mixing thick substances like adhesives or pastes. These agitators provide the necessary torque to handle viscous materials effectively.
Extreme Temperatures: Choose agitators with materials and seals designed to withstand high or low temperatures. This ensures durability and prevents equipment failure.
Pressure-Resistant Agitators: For pressurized or vacuum conditions, select agitators with reinforced designs. These agitators maintain performance without compromising the tank’s integrity.
By addressing these process-specific requirements, you can optimize your mixing operations and achieve consistent, high-quality results.
Budget and Cost Factors
Budget considerations play a significant role in selecting the right agitator tank. While it’s tempting to focus solely on upfront costs, evaluating the total cost of ownership ensures long-term value and efficiency. Here’s how to approach budget and cost factors:
Initial Investment
The initial cost of an agitator tank depends on factors like size, material, and design complexity. For example:
Material Choice: Stainless steel tanks typically cost more than plastic or rubber-lined options. However, their durability and corrosion resistance often justify the higher price in demanding applications.
Customization: Custom-designed tanks tailored to your specific needs may have a higher upfront cost. However, they often deliver better performance and efficiency, reducing operational expenses over time.
“Investing in high-quality materials and designs ensures durability and reduces maintenance costs, offering long-term savings.”
When planning your budget, balance the initial investment with the expected lifespan and performance of the tank. A higher upfront cost may lead to lower maintenance and replacement expenses in the future.
Operating Costs
Operating costs include energy consumption, maintenance, and downtime. To minimize these expenses:
Energy Efficiency: Choose agitators with optimized designs that reduce energy consumption. For example, modern impeller shapes and automated control systems can lower power requirements while maintaining effective mixing.
Maintenance Needs: Tanks with simple, robust designs often require less maintenance. Features like easy-to-clean surfaces and durable seals reduce the frequency and cost of repairs.
Downtime Reduction: Reliable equipment minimizes downtime, ensuring uninterrupted operations. Investing in high-quality tanks and agitators reduces the risk of unexpected failures.
“Energy-efficient agitators and low-maintenance designs help you save on operating costs while maintaining productivity.”
By considering these factors, you can select equipment that aligns with your budget while delivering long-term value.
Long-Term Value
While upfront costs are important, focus on the total cost of ownership. A tank with a higher initial price may offer better durability, efficiency, and performance, resulting in lower overall expenses. For example:
- Durable Materials: Stainless steel tanks last longer and resist corrosion, reducing replacement costs.
- Advanced Features: Tanks with automation or temperature control systems enhance efficiency, saving time and resources.
“Prioritizing long-term value over short-term savings ensures that your investment supports your operational goals effectively.”
By evaluating both initial and ongoing costs, you can make informed decisions that maximize your return on investment.
Maintenance Best Practices for Chemical Mixing Tanks with Agitators
Proper maintenance of chemical mixing tanks with agitators ensures their longevity and optimal performance. By following best practices, you can prevent costly repairs, maintain product quality, and ensure safe operations. Below are essential steps to keep your equipment in excellent condition.
Routine Cleaning and Inspection
Regular cleaning and inspection are vital for maintaining the efficiency of your mixing tanks and agitators. Residue buildup inside the tank can compromise the quality of your products and reduce the effectiveness of the agitator. To avoid these issues, establish a consistent cleaning schedule.
- Daily Cleaning: After each use, rinse the tank thoroughly to remove any leftover materials. Use appropriate cleaning agents that are compatible with the tank’s material, such as stainless steel.
- Deep Cleaning: Perform a more thorough cleaning weekly or monthly, depending on the frequency of use. This includes scrubbing the tank walls and inspecting hard-to-reach areas.
- Inspection Checklist:
- Examine the agitator blades for signs of wear or damage.
- Check seals and bearings for leaks or deterioration.
- Inspect the motor and drive system for unusual noises or vibrations.
Pro Tip: Train all personnel involved in cleaning and maintenance to follow proper procedures. Well-trained staff ensure that cleaning is thorough and equipment remains undamaged.
Routine cleaning not only preserves the tank’s integrity but also prevents contamination, ensuring the safety and quality of your products.
Preventive Maintenance for Agitators
Preventive maintenance minimizes downtime and extends the lifespan of your agitators. By addressing potential issues early, you can avoid unexpected failures and maintain smooth operations.
- Lubrication: Regularly lubricate moving parts, such as bearings and seals, to reduce friction and wear. Use lubricants recommended by the manufacturer to ensure compatibility.
- Alignment Checks: Misaligned agitators can cause uneven mixing and strain on the motor. Periodically check the alignment of the agitator shaft and adjust as needed.
- Blade Maintenance:
- Inspect the agitator blades for cracks, corrosion, or deformation.
- Replace damaged blades promptly to maintain mixing efficiency.
- Electrical Components: Test the motor and control systems to ensure they operate correctly. Look for loose connections or signs of overheating.
- Calibration: Verify that the agitator operates at the correct speed and power settings for your process. Adjustments may be necessary to optimize performance.
Key Takeaway: Preventive maintenance reduces the risk of operational issues and ensures that your agitators perform at their best.
By implementing these measures, you can enhance the reliability and efficiency of your mixing equipment.
Troubleshooting Common Issues
Even with regular maintenance, you may encounter occasional issues with your mixing tanks and agitators. Knowing how to troubleshoot these problems can save time and prevent disruptions.
- Uneven Mixing: If materials are not blending uniformly, check the agitator blades for damage or improper positioning. Ensure that baffles are installed correctly to prevent vortex formation.
- Excessive Noise or Vibration: Unusual sounds often indicate loose components or misalignment. Tighten bolts, realign the agitator shaft, and inspect the motor for issues.
- Leaking Seals: Leaks around the agitator shaft can result from worn seals. Replace seals promptly to prevent contamination and maintain pressure integrity.
- Overheating Motor: An overheating motor may signal excessive load or poor ventilation. Reduce the agitator speed, clean the motor housing, and ensure adequate airflow.
- Sedimentation: If solids settle at the bottom of the tank, increase the agitator speed or adjust the blade angle to improve circulation.
Did You Know? Regular inspections and prompt troubleshooting can prevent minor issues from escalating into major problems.
By addressing these common challenges, you can maintain consistent mixing performance and avoid costly downtime.
Ensuring Compliance with Safety Standards
Ensuring compliance with safety standards is essential when using chemical mixing tanks with agitators. Adhering to these standards protects your workers, maintains product quality, and prevents environmental hazards. By following established guidelines, you can create a safer and more efficient working environment.
Understand Industry-Specific Regulations
Each industry has unique safety requirements for mixing tanks. For example, food processing and beverage production demand strict hygiene standards to prevent contamination. Tanks used in these industries must meet Good Manufacturing Practices (GMP) and include easy-to-clean surfaces. In contrast, chemical manufacturing often requires tanks that comply with ASME (American Society of Mechanical Engineers) or API (American Petroleum Institute) standards to handle high-pressure or hazardous materials safely.
“Mixing tanks designed to meet ASME or API standards ensure safety, quality, and compliance in critical applications.”
You should familiarize yourself with the specific regulations governing your industry. This knowledge helps you select tanks that meet the necessary criteria, ensuring both safety and operational efficiency.
Choose the Right Materials and Design
The materials and design of your mixing tank play a significant role in meeting safety standards. Stainless steel tanks are a popular choice due to their non-corrosive properties and ease of cleaning. These features make them ideal for industries like pharmaceuticals and food processing, where cleanliness is critical. For hazardous chemicals, portable mixing tanks with spill-prevention features minimize risks such as leaks or fires.
“Portable mixing tanks are recommended for hazardous liquids to prevent spills and fires.”
Additionally, tanks with built-in safety features, such as pressure relief valves and baffles, enhance operational safety. These components prevent accidents by maintaining stability during mixing processes.
Implement Proper Training and Monitoring
Training your staff on proper handling and maintenance procedures is crucial for maintaining safety. Workers should understand how to operate the agitators, monitor the mixing process, and respond to emergencies. Regular monitoring ensures that the equipment functions correctly and meets safety standards.
- Conduct Routine Inspections: Check for wear and tear on agitator blades, seals, and motors.
- Monitor Chemical Reactions: Ensure that the mixing process remains stable and does not exceed temperature or pressure limits.
- Provide Emergency Protocols: Train employees to handle spills, leaks, or equipment malfunctions effectively.
“Proper training and monitoring are crucial to prevent accidents and ensure safe handling of chemicals in mixing tanks.”
By prioritizing training and monitoring, you can reduce the risk of accidents and maintain a safe working environment.
Maintain Regular Maintenance and Safety Checks
Regular maintenance ensures that your mixing tanks remain compliant with safety standards. Cleaning the tanks after each use prevents residue buildup, which could compromise product quality or cause contamination. Inspecting components like seals, bearings, and agitators helps you identify potential issues before they escalate.
“Chemical mixing tanks play a crucial role in maintaining product quality and safety in various industries.”
Incorporating preventive maintenance practices not only extends the lifespan of your equipment but also ensures that it continues to meet regulatory requirements. This proactive approach minimizes downtime and enhances overall safety.
Stay Updated on Evolving Standards
Safety standards evolve to address new challenges and technologies. Staying informed about these changes helps you maintain compliance and adopt best practices. For instance, advancements in automation and smart tank technology have introduced new safety features, such as real-time monitoring and automated shutoff systems. Incorporating these innovations into your operations can further enhance safety and efficiency.
By understanding and implementing these measures, you can ensure that your chemical mixing tanks with agitators meet all safety standards. This commitment to safety protects your team, preserves product integrity, and supports sustainable operations.
Optimizing the Performance of Chemical Mixing Tanks
Proper Installation and Setup
Proper installation and setup of your agitator tank are critical for achieving optimal liquid mixing. A well-installed system ensures efficient operation, minimizes downtime, and extends the lifespan of your equipment. Begin by selecting a suitable location for the tank. Ensure the surface is level and sturdy enough to support the tank’s weight when filled. Uneven surfaces can lead to instability, affecting the agitator’s performance.
Position the agitator correctly within the tank. The placement of the impeller plays a significant role in mixing optimization. For most applications, placing the impeller slightly off-center prevents vortex formation, which can reduce mixing efficiency. Additionally, installing baffles along the tank walls helps disrupt circular flow patterns, ensuring thorough fluid mixing.
Secure all components, including the motor, drive system, and seals. Loose connections can cause vibrations, leading to wear and tear. Verify that the agitator’s shaft alignment is precise. Misalignment can strain the motor and reduce mixing efficiency. Regularly inspect the setup during installation to ensure all parts are functioning as intended.
Tip: Follow the manufacturer’s guidelines for installation to avoid common pitfalls. Proper setup not only enhances performance but also reduces maintenance needs.
Adjusting Agitator Speed and Position
Adjusting the speed and position of the agitator is essential for achieving mixing optimization. The speed of the agitator determines the intensity of mixing. High speeds work well for low-viscosity liquids, while slower speeds are better suited for viscous materials. Use variable-speed drives to fine-tune the agitator’s rotation based on your specific process requirements.
The position of the agitator within the tank also impacts performance. For example, placing the impeller too close to the tank bottom can lead to sedimentation, while positioning it too high may leave unmixed zones. Aim to position the impeller at a height that promotes even circulation throughout the tank. Studies on impeller optimization have shown that adjusting blade angles can further enhance mixing efficiency. Tools like finite element modeling (FEM) have been used to design impellers that maximize agitation performance.
“Agitators improve mixing by creating controlled movement, ensuring uniformity and preventing sedimentation.”
Experiment with different configurations to find the optimal setup for your process. Small adjustments in speed and position can significantly improve the quality of mixing, reducing energy consumption and production time.
Monitoring and Controlling Process Variables
Monitoring and controlling process variables ensure consistent performance and product quality. Key variables include temperature, pressure, and mixing time. Install sensors to track these parameters in real-time. For instance, temperature sensors help maintain the ideal conditions for chemical reactions or fermentation processes.
Control systems integrated with the agitator allow you to adjust settings automatically. Automated systems can regulate agitator speed, ensuring consistent fluid mixing even as material properties change. For example, as viscosity increases during a process, the system can increase the agitator’s power to maintain efficiency.
Regularly monitor the tank’s contents for signs of uneven mixing or sedimentation. If issues arise, adjust the agitator’s speed or position to address the problem. Advanced technologies, such as differential agitators, have been developed to tackle challenges like vortex formation and cavitation. These innovations use optimized designs to enhance performance while minimizing energy use.
Did You Know? Automated control systems not only improve efficiency but also reduce operational costs by optimizing energy consumption.
By actively monitoring and controlling these variables, you can ensure your agitator tank operates at peak performance. This approach enhances productivity, reduces waste, and supports consistent results across your processes.
Upgrading or Retrofitting Existing Systems
Upgrading or retrofitting your existing chemical mixing tanks with agitators can significantly enhance their performance and extend their lifespan. Instead of replacing the entire system, you can make targeted improvements to meet evolving process requirements, reduce energy consumption, and improve efficiency. Below are key considerations and steps to guide you through the process.
Assessing Current System Performance
Start by evaluating the performance of your current system. Identify areas where the tank or agitator falls short in meeting your operational goals. Common issues include uneven mixing, excessive energy use, or difficulty handling new materials.
- Mixing Efficiency: Check if the agitator achieves uniform mixing. Uneven results may indicate outdated impeller designs or improper positioning.
- Energy Consumption: Measure the energy usage of your system. Older agitators often consume more power due to inefficient motors or impellers.
- Material Compatibility: Ensure the tank and agitator materials align with the chemicals or substances you now handle. Changes in your process may require upgrades to prevent corrosion or wear.
“Sulzer’s research in the fertilizer industry demonstrated that upgrading to highly efficient hydrofoil impellers reduced motor power requirements to just 132 kW, showcasing the potential for energy savings.”
By thoroughly assessing your system, you can pinpoint specific areas for improvement and prioritize upgrades that deliver the most value.
Upgrading Agitator Components
Modernizing the agitator is one of the most impactful upgrades you can make. Advanced impeller designs, such as hydrofoil impellers, improve mixing efficiency while reducing energy consumption. These impellers create smoother fluid movement, minimizing turbulence and power loss.
Consider replacing the motor with a more energy-efficient model. Variable-speed drives (VSDs) allow you to adjust the agitator speed based on the viscosity and volume of the materials being mixed. This flexibility enhances performance and reduces operational costs.
- Impeller Replacement: Upgrade to impellers designed for your specific application. For example, turbine impellers work well for medium-viscosity fluids, while anchor agitators handle highly viscous materials.
- Motor Efficiency: Install motors with higher energy ratings. Modern motors paired with VSDs optimize power usage and adapt to changing process conditions.
- Seals and Bearings: Replace worn seals and bearings to prevent leaks and ensure smooth operation.
Pro Tip: Upgrading to hydrofoil impellers not only improves mixing but also reduces energy consumption, as demonstrated in industrial applications like fertilizer production.
Enhancing Tank Features
Retrofitting the tank itself can further optimize your system. Adding baffles, for instance, prevents vortex formation and ensures thorough mixing. Installing heating or cooling jackets allows you to regulate temperature, which is essential for processes like fermentation or chemical reactions.
- Baffle Installation: Improve mixing by adding baffles to disrupt circular flow patterns. This upgrade is especially useful for cylindrical tanks.
- Temperature Control: Equip the tank with heating or cooling systems to maintain optimal conditions for your process.
- Material Upgrades: If your tank material no longer meets chemical compatibility requirements, consider lining it with corrosion-resistant coatings or replacing it with stainless steel.
“Mixing tanks with enhanced features, such as temperature control and baffles, deliver better performance and adapt to diverse industrial needs.”
Integrating Automation and Smart Technology
Automation and smart technology upgrades can revolutionize your mixing operations. Automated control systems monitor and adjust variables like agitator speed, temperature, and pressure in real-time. These systems improve consistency, reduce human error, and save energy.
- Sensors and Monitoring: Install sensors to track key parameters, such as temperature and viscosity. Real-time data helps you maintain optimal conditions.
- Automated Controls: Use programmable logic controllers (PLCs) to automate adjustments. For example, the system can increase agitator speed as viscosity rises during a process.
- Remote Access: Enable remote monitoring and control to manage your system from anywhere, improving flexibility and response times.
Did You Know? Automated systems with optimized agitators can cut mixing time and energy use, making them essential for modern industrial processes.
Benefits of Retrofitting
Upgrading or retrofitting your system offers numerous advantages:
- Cost Savings: Avoid the expense of purchasing a new tank by improving your existing equipment.
- Enhanced Efficiency: Modern components and designs boost mixing performance and reduce energy consumption.
- Adaptability: Tailor your system to handle new materials or meet updated industry standards.
- Sustainability: Reduce waste and energy use, aligning with environmental goals.
By investing in targeted upgrades, you can transform your existing system into a high-performing, cost-effective solution. Whether you need better mixing, energy efficiency, or process adaptability, retrofitting provides a practical path forward.
Common Challenges and How to Overcome Them
Mixing Viscous or Corrosive Materials
Handling viscous or corrosive materials presents unique challenges during the mixing process. Viscous substances resist movement, making it difficult to achieve uniform blending. Corrosive materials, on the other hand, can damage equipment, leading to inefficiencies and safety risks. To address these issues, you need to select the right equipment and techniques.
For viscous materials, slow agitation with a heavier unit is essential. Agitators like anchor or helical designs work effectively in these scenarios. These agitators create scraping and sweeping motions, ensuring that even thick substances mix uniformly. For example, adhesives or resins require this type of motion to prevent material buildup on tank walls. Additionally, using tanks with baffles can disrupt circular flow patterns, further enhancing the mixing process.
When dealing with corrosive substances, material selection becomes critical. Stainless steel tanks with corrosion-resistant coatings or rubber-lined interiors offer durability and safety. Glass-lined tanks also provide excellent chemical resistance for highly reactive substances. Regular maintenance, such as inspecting seals and bearings, ensures that your equipment remains intact and operational.
Pro Tip: Always match the agitator type and tank material to the properties of the substances you handle. This approach minimizes wear and ensures efficient fluid mixing.
Preventing Sedimentation and Dead Zones
Sedimentation and dead zones occur when materials settle at the bottom of the tank or remain unmixed in certain areas. These issues compromise the quality of your product and reduce the efficiency of your operations. To overcome this challenge, you must optimize the tank design and agitator setup.
Positioning the impeller correctly is crucial. Placing it slightly off-center prevents vortex formation, which can lead to dead zones. Adding baffles along the tank walls further disrupts stagnant flow patterns, ensuring thorough mixing. For materials prone to sedimentation, increasing the agitator speed or adjusting the blade angle can improve circulation and keep solids suspended.
Modern impeller designs, such as hydrofoil impellers, enhance mixing efficiency by creating smoother fluid movement. These designs reduce turbulence and ensure uniform distribution of materials. Automated control systems also help by adjusting the agitator speed in real-time based on the viscosity or density of the contents.
Did You Know? Studies show that proper impeller placement and baffle installation significantly reduce dead zones, improving overall mixing performance.
Addressing Energy Efficiency Concerns
Energy consumption is a major concern in industrial mixing processes. Inefficient systems not only increase operational costs but also impact sustainability. To address this challenge, you need to focus on optimizing equipment and processes.
Start by selecting energy-efficient agitators. Modern designs, like hydrofoil or turbine impellers, require less power while maintaining effective mixing. Variable-speed drives (VSDs) allow you to adjust the agitator speed based on the specific needs of your process, reducing unnecessary energy use. For example, low-viscosity liquids require less agitation, so you can lower the speed to save energy.
Automated control systems further enhance efficiency. These systems monitor key variables, such as viscosity and temperature, and adjust the agitator settings accordingly. By maintaining optimal conditions, you minimize energy waste and improve productivity. Regular maintenance also plays a role in energy efficiency. Clean and well-maintained equipment operates more smoothly, reducing power requirements.
Key Takeaway: Investing in energy-efficient agitators and automation not only lowers costs but also supports sustainable operations.
By addressing these common challenges with the right strategies and equipment, you can optimize your mixing operations, improve product quality, and reduce costs.
Avoiding Operational Issues with Agitators
Operational issues with agitators can disrupt your processes, reduce efficiency, and lead to costly repairs. Understanding common problems and implementing preventive measures ensures smooth operations and extends the lifespan of your equipment. Below are practical strategies to help you avoid these challenges.
1. Addressing Vibrations and Imbalances
Vibrations in agitators often result from imbalanced impellers, loose components, or misaligned parts. These vibrations not only affect performance but also cause mechanical stress, which can damage the agitator over time.
- Inspect Impellers Regularly: Check for wear, cracks, or deformation. Replace damaged impellers promptly to maintain balance.
- Tighten Loose Components: Secure bolts, nuts, and other fasteners during routine maintenance to prevent unnecessary movement.
- Ensure Proper Alignment: Misaligned shafts strain the motor and reduce efficiency. Use alignment tools to verify and correct the positioning of the agitator shaft.
Prolonged vibrations can shorten the lifespan of your agitator. Regular inspections and timely adjustments prevent this issue.
2. Selecting the Right Agitator Design
Choosing an agitator suited to your specific application minimizes operational issues. A well-designed agitator operates efficiently under the required conditions and reduces maintenance needs.
- Consider Operating Conditions: Evaluate factors like temperature, pressure, and pH levels. Select an agitator that can withstand these conditions without compromising performance.
- Opt for Heavy-Duty Designs: For demanding applications, invest in robust agitators. These designs handle high loads and last longer, reducing downtime and repair costs.
- Match the Agitator to the Material: High-viscosity materials require specialized designs, such as anchor or helical agitators. These agitators ensure thorough mixing without overloading the motor.
“A correctly designed agitator will have a longer lifetime and need fewer spare parts than, for example, a pump.”
3. Preventing Overloading and Motor Strain
Overloading occurs when the agitator operates beyond its capacity, leading to motor strain and potential failure. Avoid this by monitoring and controlling operational parameters.
- Monitor Agitator Speed: Use variable-speed drives to adjust the speed based on material viscosity and volume. This prevents excessive strain on the motor.
- Avoid Starting Under Load: Ensure the agitator is not buried in solids before starting. Starting under load increases torque requirements and damages the motor.
- Install Overload Protection: Equip the motor with overload protection devices. These systems shut down the agitator when it exceeds safe operating limits.
Preventing motor strain not only protects your equipment but also reduces energy consumption.
4. Maintaining Clean and Efficient Operations
Residue buildup inside the tank can hinder agitator performance and lead to contamination. Regular cleaning and maintenance keep your system running efficiently.
- Clean After Each Use: Rinse the tank thoroughly to remove leftover materials. Use cleaning agents compatible with the tank’s material.
- Inspect Seals and Bearings: Check for leaks or wear. Replace damaged components to maintain the integrity of the system.
- Lubricate Moving Parts: Apply manufacturer-recommended lubricants to reduce friction and wear on bearings and seals.
Routine cleaning and maintenance ensure consistent mixing quality and prolong the life of your equipment.
5. Monitoring for Early Warning Signs
Detecting issues early allows you to address them before they escalate. Regular monitoring helps you identify potential problems and take corrective action.
- Watch for Unusual Noises: Grinding or rattling sounds often indicate loose components or misalignment.
- Check for Uneven Mixing: If materials are not blending uniformly, inspect the impeller and baffles for damage or improper positioning.
- Track Energy Usage: A sudden increase in energy consumption may signal inefficiencies or mechanical issues.
Early detection saves time and money by preventing major breakdowns.
By implementing these strategies, you can avoid operational issues with agitators and ensure reliable performance. Regular maintenance, proper design selection, and proactive monitoring keep your equipment running smoothly, supporting efficient and uninterrupted operations.
Innovations and Trends in Chemical Mixing Technology
Advances in Agitator Design
The evolution of agitator design has significantly enhanced the efficiency and performance of mixing processes. Modern industrial agitators now incorporate advanced engineering principles to address specific challenges in chemical mixing. For instance, differential agitators represent a breakthrough in design. These systems use two shafts—one for the bearing axis and another for the agitating group. This configuration creates a pressure differential that improves fluid movement within the tank. The liquid flows from low-pressure areas to high-pressure zones, ensuring thorough mixing and reducing dead zones.
Parametric studies and shape optimization have further refined agitator designs. Using tools like Finite Element Method (FEM), engineers can optimize the geometry of impellers and other components. This approach ensures that agitators deliver maximum performance while minimizing energy consumption. For example, hydrofoil impellers have become popular due to their ability to create smooth fluid motion with reduced turbulence. These designs not only improve mixing efficiency but also lower operational costs.
Scientific Insight: Research on differential agitators has demonstrated their ability to achieve high agitation performance, particularly in applications like lime-water mixing. Laboratory experiments validated their effectiveness in optimizing fluid dynamics within tanks.
By adopting these advanced designs, you can achieve better mixing results, reduce energy usage, and extend the lifespan of your equipment. Whether you work with viscous materials or delicate substances, modern agitators provide tailored solutions to meet your needs.
Smart Tanks and Automation
The integration of smart technology into chemical mixing tanks has revolutionized how you manage and monitor mixing processes. Smart tanks equipped with sensors and automated control systems allow you to track key variables like temperature, pressure, and viscosity in real time. These systems adjust agitator speed and power automatically, ensuring optimal performance under varying conditions.
For example, automated control systems can detect changes in material properties during mixing. If viscosity increases, the system adjusts the agitator’s speed to maintain consistent mixing. This level of precision reduces human error and enhances product quality. Remote monitoring capabilities also enable you to oversee operations from anywhere, providing flexibility and quick response times.
“Automated agitation systems with optimized agitators save energy and reduce mixing time, making them essential for modern industrial processes.”
Smart tanks also support predictive maintenance. By analyzing data from sensors, these systems can identify potential issues before they escalate. For instance, if an agitator motor shows signs of strain, the system alerts you to perform maintenance, preventing costly downtime. This proactive approach ensures that your equipment operates efficiently and reliably.
Embracing smart technology in your mixing operations not only improves efficiency but also aligns with the growing demand for digital transformation in industries. These innovations empower you to optimize processes, reduce waste, and achieve consistent results.
Sustainable and Energy-Efficient Solutions
Sustainability has become a key focus in chemical mixing technology. Modern industrial agitators are designed to minimize energy consumption while maintaining high performance. For example, hydrofoil impellers require less power to achieve effective mixing, making them an energy-efficient choice for many applications. Variable-speed drives (VSDs) further enhance efficiency by allowing you to adjust agitator speed based on process requirements.
Sustainable solutions also include the use of eco-friendly materials in tank construction. Stainless steel remains a popular choice due to its durability and recyclability. Additionally, advancements in coating technologies have introduced corrosion-resistant materials that extend the lifespan of tanks, reducing the need for frequent replacements.
Did You Know? Upgrading to energy-efficient agitators can significantly lower your operational costs while reducing your carbon footprint.
Automation plays a crucial role in sustainability efforts. Automated systems optimize mixing parameters, ensuring that you use only the energy required for each process. This precision reduces waste and supports environmentally responsible practices. For example, in wastewater treatment, agitators designed for low-energy consumption help facilities meet sustainability goals without compromising performance.
By adopting these sustainable and energy-efficient solutions, you contribute to environmental conservation while improving your bottom line. These innovations demonstrate that efficiency and sustainability can go hand in hand, offering long-term benefits for your operations.
Chenma’s Role in Driving Innovation
Chenma stands at the forefront of innovation in chemical mixing technology. By combining advanced engineering with a deep understanding of industrial needs, Chenma delivers solutions that redefine efficiency and performance in mixing processes. You benefit from their commitment to creating cutting-edge equipment tailored to meet diverse industrial challenges.
Customized Solutions for Optimal Mixing
Chenma specializes in designing custom chemical mixing tanks that cater to your specific requirements. Each tank is engineered to ensure uniform blending and efficient operation. Whether you need to mix liquids, powders, or gases, Chenma’s tanks provide the precision and reliability you demand. The company considers critical factors like scale, viscosity, and reaction requirements to create bespoke solutions. This approach guarantees maximum efficiency and safety, surpassing the capabilities of standard mixing tanks.
“Optimized Mixing: Our chemical mixing tanks are engineered for optimal mixing performance, ensuring uniform blending and efficient operation.”
By choosing Chenma, you gain access to equipment that not only meets but exceeds industry standards. Their tanks are indispensable for large-scale chemical production, enabling you to produce bigger quantities while maintaining product quality and avoiding contamination.
Driving Efficiency in Chemical Production
Chenma’s mixing tanks play a pivotal role in industries like chemical manufacturing, coatings, and water treatment. These tanks ensure that materials of different components mix evenly, which is essential for producing high-quality products. For example, in the production of detergents or dyes, Chenma’s tanks provide the consistent mixing required to achieve uniformity and stability in the final product.
The company’s focus on efficiency extends to every aspect of its designs. Features like advanced impeller systems and optimized tank configurations reduce energy consumption while enhancing mixing performance. This ensures that you can achieve your production goals without compromising on sustainability or cost-effectiveness.
Commitment to Innovation and Quality
Chenma continuously invests in research and development to stay ahead of industry trends. Their engineers use state-of-the-art tools and methodologies to refine tank designs and improve performance. For instance, they incorporate advanced materials like stainless steel to enhance durability and chemical resistance. These innovations ensure that your equipment remains reliable even under demanding conditions.
Chenma also prioritizes safety and compliance. All products adhere to the latest industry standards, giving you peace of mind that your operations meet regulatory requirements. By integrating modern technologies, such as automated control systems, Chenma enables you to monitor and optimize your mixing processes with ease.
Supporting Your Growth and Success
Chenma understands the challenges you face in scaling up production. Their mixing tanks are designed to support large-scale operations, allowing you to expand your capabilities without sacrificing quality. Whether you are producing medicines, paints, or water treatment chemicals, Chenma’s solutions help you achieve consistent results and maintain competitive advantages.
“Mixing tanks are a must-have for large-scale chemical industry companies. By using them, it is possible to produce bigger quantities, mix liquids with solids, and avoid possible product contamination.”
With Chenma as your partner, you gain more than just equipment. You gain a trusted ally dedicated to driving innovation and ensuring your success in an ever-evolving industrial landscape.
Chemical mixing tanks with agitators are indispensable in industrial processes, ensuring uniform blending and efficient operation. Their ability to handle diverse materials enhances product quality and accelerates production. Selecting the right tank design and materials, such as stainless steel, is vital for durability and performance. Proper maintenance extends the lifespan of these tanks, optimizing their functionality and reliability. By choosing customized solutions tailored to your industry’s needs, you can achieve superior results. Chenma’s expertise in innovative technologies and bespoke designs ensures you have the tools to meet your mixing challenges effectively.
FAQ
What is the importance of selecting the right agitator tank for an industry?
Choosing the correct agitator tank is essential for ensuring smooth industrial operations. It guarantees proper mixing, which directly impacts product quality and operational efficiency. The right tank simplifies processes like blending, chemical reactions, and homogenization. By selecting the appropriate tank, you can achieve consistent results, reduce waste, and enhance productivity across various applications.
Key takeaway: The right agitator tank ensures uniform mixing, saves time, and improves overall process efficiency.
What factors should you consider when selecting an agitator tank?
When choosing an agitator tank, you need to evaluate several critical factors:
- Material Compatibility: Ensure the tank material aligns with the chemical properties of the substances being mixed.
- Volume and Size: Match the tank size to your production requirements to avoid inefficiencies.
- Agitation Type: Select the appropriate agitator type (e.g., paddle, turbine) based on the viscosity and nature of the materials.
- Power and Speed: Consider the motor power and speed settings to achieve optimal mixing.
- Process-Specific Needs: Account for temperature, pressure, and other unique requirements of your operation.
Pro Tip: Tailoring the tank to your specific needs ensures durability, safety, and consistent performance.
What are chemical mixing tanks used for?
Chemical mixing tanks serve as vital tools in industrial processes. They ensure uniform quality and safety when handling chemicals. These tanks are used for blending liquids, dissolving solids, maintaining suspensions, and facilitating chemical reactions. From laboratory-scale experiments to large-scale industrial production, these tanks play a pivotal role in achieving precise and efficient mixing.
“Chemical mixing tanks are indispensable for creating consistent and high-quality products in industries like pharmaceuticals, food processing, and water treatment.”
What industries rely on chemical mixing tanks?
Chemical mixing tanks are widely used across various industries, including:
- Pharmaceuticals: For drug formulation and vaccine production.
- Food and Beverage: To blend ingredients and maintain product consistency.
- Water Treatment: For mixing coagulants, flocculants, and disinfectants.
- Chemical Manufacturing: To produce detergents, dyes, and adhesives.
- Paints and Coatings: For dispersing pigments and achieving uniform textures.
Did You Know? Industries like sanitation detergents and alcohol production also depend heavily on these tanks for their processes.
What role do agitator tanks play in various industries?
Agitator tanks simplify complex industrial processes by ensuring thorough mixing and blending. They play a crucial role in maintaining product consistency, quality, and safety. For example:
- In the food industry, they ensure uniform flavor and texture.
- In pharmaceuticals, they help achieve precise formulations.
- In chemical manufacturing, they enable efficient reactions and emulsifications.
Key Insight: Agitator tanks are the backbone of industries that demand precision and uniformity in their products.
How do you maintain chemical mixing tanks with agitators?
Proper maintenance ensures the longevity and efficiency of your mixing tanks. Follow these steps:
- Routine Cleaning: Rinse the tank after each use to prevent residue buildup.
- Inspection: Regularly check agitator blades, seals, and bearings for wear or damage.
- Lubrication: Apply recommended lubricants to moving parts to reduce friction.
- Calibration: Verify that the agitator operates at the correct speed and power settings.
Pro Tip: Preventive maintenance reduces downtime and ensures consistent mixing performance.
What types of agitators are commonly used in mixing tanks?
Agitators come in various designs to suit different mixing needs:
- Paddle Agitators: Ideal for gentle mixing of low-viscosity liquids.
- Propeller Agitators: Suitable for vertical flow and low-viscosity applications.
- Turbine Agitators: Versatile for medium- to high-viscosity fluids.
- Helical Agitators: Effective for highly viscous materials like creams and pastes.
- Anchor Agitators: Best for thick substances, preventing material buildup on tank walls.
Did You Know? Each agitator type is designed to optimize mixing for specific materials and processes.
How do chemical mixing tanks ensure product safety?
Chemical mixing tanks are designed with features that prioritize safety:
- Material Selection: Tanks made from stainless steel or glass-lined materials resist corrosion and contamination.
- Seals and Bearings: Prevent leaks and maintain system integrity.
- Temperature Control: Jacketed tanks regulate heat, ensuring safe chemical reactions.
- Compliance Standards: Tanks adhere to industry regulations like GMP or ASME, ensuring safe operations.
Key takeaway: Properly designed tanks protect both the product and the environment, ensuring safe and efficient processes.
Can chemical mixing tanks handle corrosive materials?
Yes, chemical mixing tanks can handle corrosive materials when constructed with the right materials. Stainless steel tanks with corrosion-resistant coatings or rubber-lined interiors are ideal for such applications. Glass-lined tanks also provide excellent resistance to highly reactive chemicals. Regular maintenance ensures the tank remains durable and safe for handling corrosive substances.
Pro Tip: Always choose tanks with materials compatible with the chemicals you plan to mix to prevent damage and ensure safety.
Why should you invest in customized mixing tanks?
Customized mixing tanks offer tailored solutions for your specific industrial needs. They ensure optimal performance by addressing unique factors like material properties, process requirements, and production scale. Custom tanks also enhance efficiency, reduce waste, and improve product quality. By investing in a customized solution, you gain equipment that aligns perfectly with your operational goals.
“Customized tanks deliver superior results by adapting to the exact demands of your industry.”