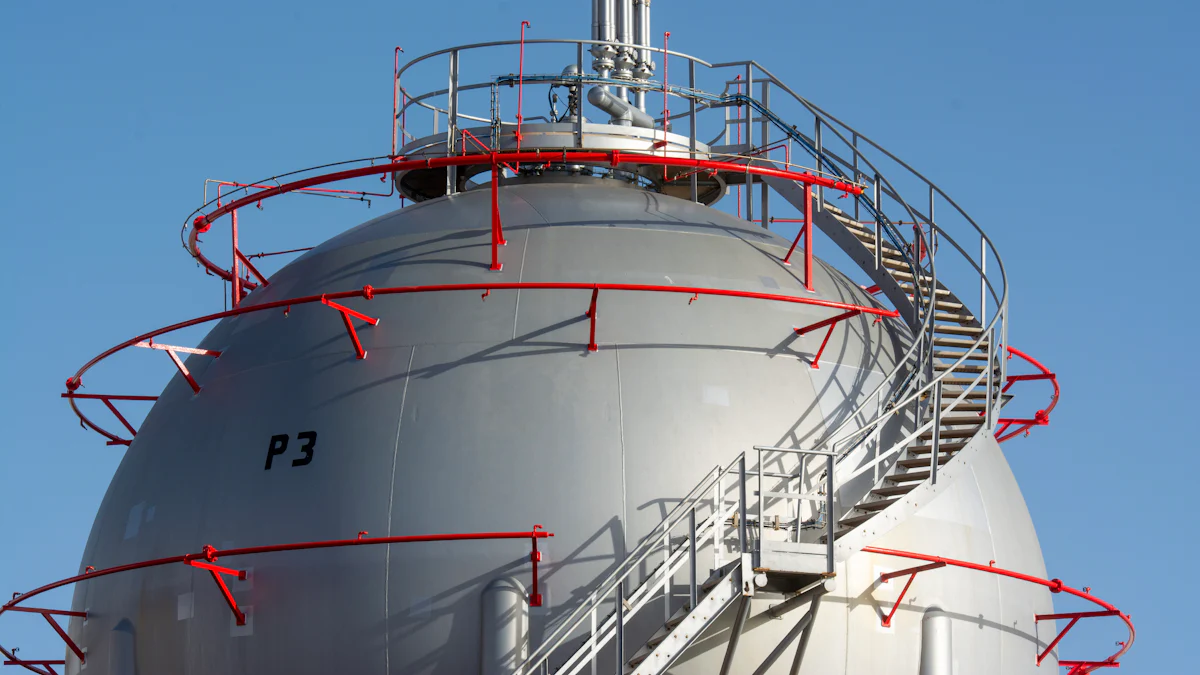
Selecting the right agricultural chemical mixing tanks plays a vital role in ensuring operational safety and efficiency. Tanks must withstand the corrosive nature of chemicals while maintaining durability. The global agrochemical tank market, valued at $1.3 billion in 2022, highlights the growing demand for reliable solutions. Proper tank selection prevents costly maintenance issues and ensures compliance with environmental regulations. By focusing on material compatibility, size, and safety features, you can achieve long-term value and seamless mixing processes. A well-chosen tank not only protects your investment but also enhances productivity.
Material Compatibility for Agricultural Chemical Mixing Tanks
Choosing the right tank material ensures safe and efficient handling of your chemical product. Not all materials can withstand the corrosive nature of agricultural chemicals, so understanding material compatibility is essential. A mismatch between the tank material and the chemicals you use can lead to leaks, contamination, or even structural failure. To avoid these risks, you must carefully evaluate the properties of the tank material and its resistance to the specific chemical product you plan to store or mix.
Understanding Chemical Resistance
Chemical resistance refers to a material’s ability to withstand exposure to chemicals without degrading. Some materials, like stainless steel, excel in resisting corrosion caused by harsh substances. For example, stainless steel plays a critical role in industrial applications, such as UASB reactors, due to its durability and resistance to chemical reactions. On the other hand, thermoplastics and composites are also widely used for their chemical-resistant properties, especially in environments where lighter materials are preferred. When selecting a tank, you need to ensure that its material can handle the chemical product you use without compromising safety or performance.
Matching Tank Material to Your Chemicals
To achieve proper tank mix compatibility, you must match the tank material to the specific chemicals you handle. Start by reviewing the chemical’s properties, including its pH level, temperature requirements, and reactivity. Always read the label of the chemical product to identify any warnings or recommendations regarding storage and mixing. For instance, acidic chemicals may require tanks made from high-grade stainless steel, while less reactive substances might be compatible with polyethylene or fiberglass tanks. By aligning the tank material with the chemical’s characteristics, you can prevent costly damage and ensure long-term reliability.
Why Stainless Steel is a Reliable Option
Stainless steel stands out as a reliable choice for agricultural chemical mixing tanks. Its corrosion resistance minimizes the risk of leaks and extends the tank’s lifespan. Unlike some materials, stainless steel maintains its structural integrity even under extreme conditions, such as high temperatures or exposure to aggressive chemicals. Additionally, stainless steel tanks meet stringent safety and quality standards, making them a trusted option for industries that prioritize durability and compliance. Investing in stainless steel ensures that your tank can handle a wide range of chemical products while delivering consistent performance over time.
Determining the Right Size and Capacity
Selecting the correct size and capacity for your agricultural chemical mixing tank is essential for optimizing efficiency and ensuring smooth operations. A properly sized tank prevents unnecessary expenses, maximizes productivity, and supports long-term scalability. By carefully evaluating your current needs and future requirements, you can make an informed decision that aligns with your operational goals.
Assessing Your Current Usage Needs
Understanding your current usage is the first step in determining the right tank size. Start by analyzing the volume of chemicals you handle daily or seasonally. Consider the frequency of your mixing processes and the amount of product required for each batch. For example, if you are mixing for a full tank, you need to calculate the amount of product needed to avoid overflows or shortages. Additionally, evaluate the available space in your facility to ensure the tank fits without causing logistical challenges. Tanks come in various sizes, ranging from small units for limited operations to large tanks capable of holding thousands of gallons. Matching the tank size to your immediate needs ensures efficient operations and minimizes waste.
Planning for Future Growth and Scalability
While addressing current needs is crucial, planning for future growth is equally important. Agricultural operations often expand over time, requiring larger capacities to meet increased demand. Investing in a tank that accommodates future scalability saves you from costly upgrades later. For instance, aboveground storage tanks can hold up to 12 million gallons, making them suitable for large-scale operations. If you anticipate growth, choose a tank with a capacity slightly higher than your current requirements. This approach provides flexibility and ensures your tank remains functional as your business evolves.
Avoiding Over- or Under-Sizing Issues
Choosing the wrong tank size can lead to operational inefficiencies and financial losses. An oversized tank may result in wasted resources, as unused capacity increases costs unnecessarily. On the other hand, an undersized tank can disrupt workflows by requiring frequent refills or causing delays. To avoid these issues, calculate your exact volume needs based on your application. Consider factors such as the type of chemicals stored, the mixing process, and the tank’s design constraints. For example, fiberglass tanks, which range from 4-foot to 12-foot diameters, can store up to 50,000 gallons, making them ideal for specific applications. Selecting the right size ensures optimal space usage and enhances productivity.
Safety Considerations for Agricultural Chemical Mixing Tanks
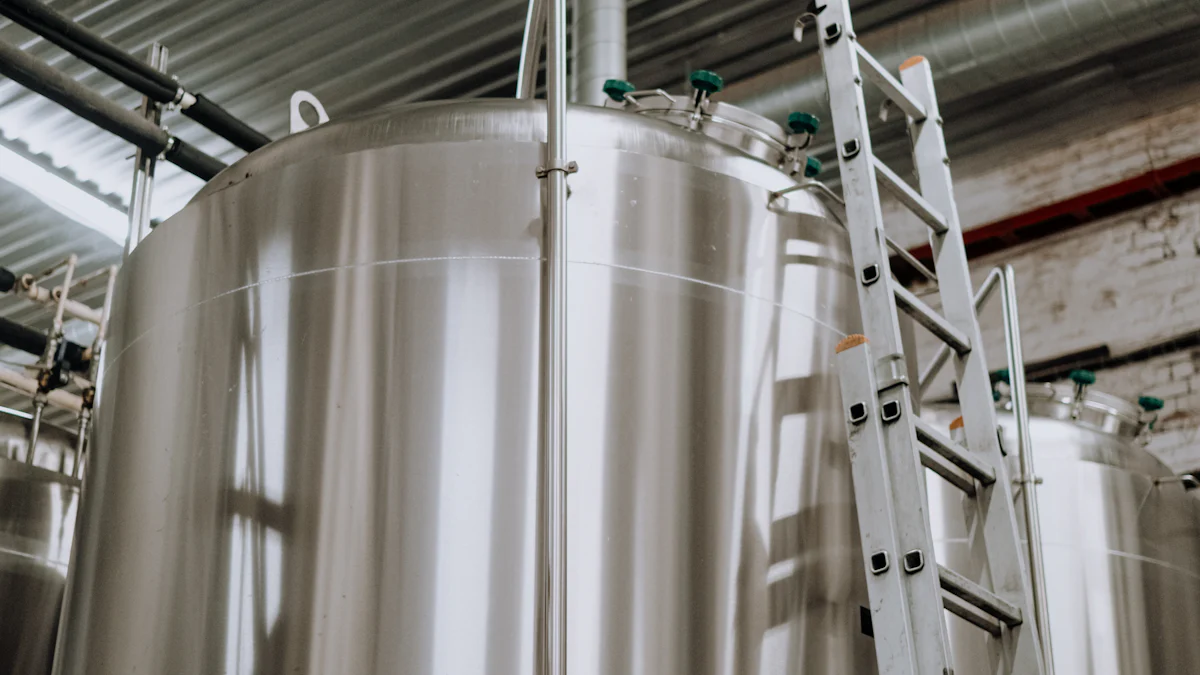
When working with agricultural chemical mixing tanks, prioritizing safety is essential. Proper safety considerations protect not only your equipment but also the environment and individuals involved in the process. By understanding the critical safety features, implementing spill prevention systems, and managing fumes effectively, you can minimize risks and ensure smooth operations.
Essential Safety Features
Agricultural chemical mixing tanks must include essential safety features to prevent accidents and maintain operational integrity. One of the most important aspects is ensuring that tanks are constructed with durable materials that can withstand the corrosive nature of pesticides and other chemicals. Tanks should also have secure lids or covers to prevent accidental spills during mixing or storage.
In addition, incorporating clear measurement markings on the tank helps you avoid overfilling, which could lead to leaks or spills. Tanks equipped with emergency shut-off valves provide an added layer of protection by allowing you to quickly stop the flow of chemicals in case of an emergency. Using personal protective equipment while handling these tanks further reduces the risk of accidental human pesticide exposure. Gloves, goggles, and chemical-resistant clothing act as barriers between you and harmful substances.
Spill Prevention and Containment Systems
Spill prevention is a critical component of safety considerations for agricultural chemical mixing tanks. Even a small spill can cause significant environmental damage and pose health risks. To address this, tanks should be designed with built-in containment systems. Secondary containment basins or bunds can catch any leaks or spills, preventing them from spreading to the surrounding area.
Installing anti-siphon devices on your tanks can also help prevent backflow, which might contaminate water sources. Regularly inspecting your tanks for cracks, corrosion, or other signs of wear ensures that potential issues are identified and resolved before they lead to spills. Additionally, always store tanks on stable, level surfaces to reduce the risk of tipping or accidental damage.
Venting Systems for Pressure and Fume Management
Proper venting systems play a vital role in managing pressure and fumes within agricultural chemical mixing tanks. When chemicals are mixed or stored, they can release vapors that build up pressure inside the tank. Without adequate venting, this pressure could lead to structural damage or even explosions.
Venting systems allow gases to escape safely, maintaining the tank’s structural integrity. These systems also help manage fumes, which can pose health risks if inhaled. For example, installing carbon filters on venting outlets can reduce the release of harmful vapors into the air. Always ensure that venting systems are compatible with the specific chemicals you handle to maximize their effectiveness.
By addressing these safety considerations, you can create a safer working environment while protecting your investment in agricultural chemical mixing tanks. Implementing these measures not only reduces risks but also ensures compliance with industry standards and environmental regulations.
Durability and Longevity of Tanks
When selecting agricultural chemical mixing tanks, durability and longevity are critical factors. A tank that withstands harsh conditions and maintains its structural integrity over time ensures a better return on investment. By focusing on UV resistance, impact resistance, and certifications, you can choose a tank that delivers reliable performance for years.
UV Resistance for Outdoor Use
If you plan to use your tank outdoors, UV resistance becomes essential. Prolonged exposure to sunlight can degrade materials, causing cracks, discoloration, or weakening of the tank’s structure. UV-resistant tanks are specifically designed to withstand these conditions, ensuring they remain functional even under constant sunlight.
Stainless steel tanks excel in outdoor environments due to their natural resistance to UV damage. Unlike plastic tanks, which may require additional coatings or treatments, stainless steel maintains its durability without extra maintenance. For regions with intense sunlight, investing in UV-resistant tanks prevents premature wear and reduces replacement costs.
Impact Resistance and Structural Integrity
Agricultural operations often involve rough handling, transportation, and exposure to external forces. Tanks with high impact resistance can endure these challenges without cracking or deforming. Structural integrity ensures the tank remains safe and functional, even in demanding conditions.
Stainless steel tanks offer superior impact resistance compared to other materials. Their robust construction minimizes the risk of dents or punctures, making them ideal for heavy-duty applications. Additionally, tanks with reinforced walls or ribbed designs provide extra strength, ensuring they can handle the weight of chemicals and external pressures effectively.
Certifications and Standards for Quality Assurance
Certifications and adherence to industry standards guarantee that your tank meets safety, environmental, and quality requirements. Tanks manufactured according to recognized standards undergo rigorous testing to ensure they perform reliably under various conditions.
Look for tanks certified by organizations such as ISO, CE, or ASME. These certifications indicate that the tank complies with international safety and quality benchmarks. For example, Chenma Machinery Co., Ltd. produces tanks that meet ISO9001-2005 quality system certification and EU CE certification. Choosing certified tanks ensures you receive a product that aligns with the latest industry standards, providing peace of mind and long-term value.
By prioritizing UV resistance, impact resistance, and certified quality, you can select a tank that offers exceptional durability and longevity. This approach not only protects your investment but also ensures consistent performance in your agricultural operations.
Maintenance and Cleaning of Mixing and Loading Spray Tanks
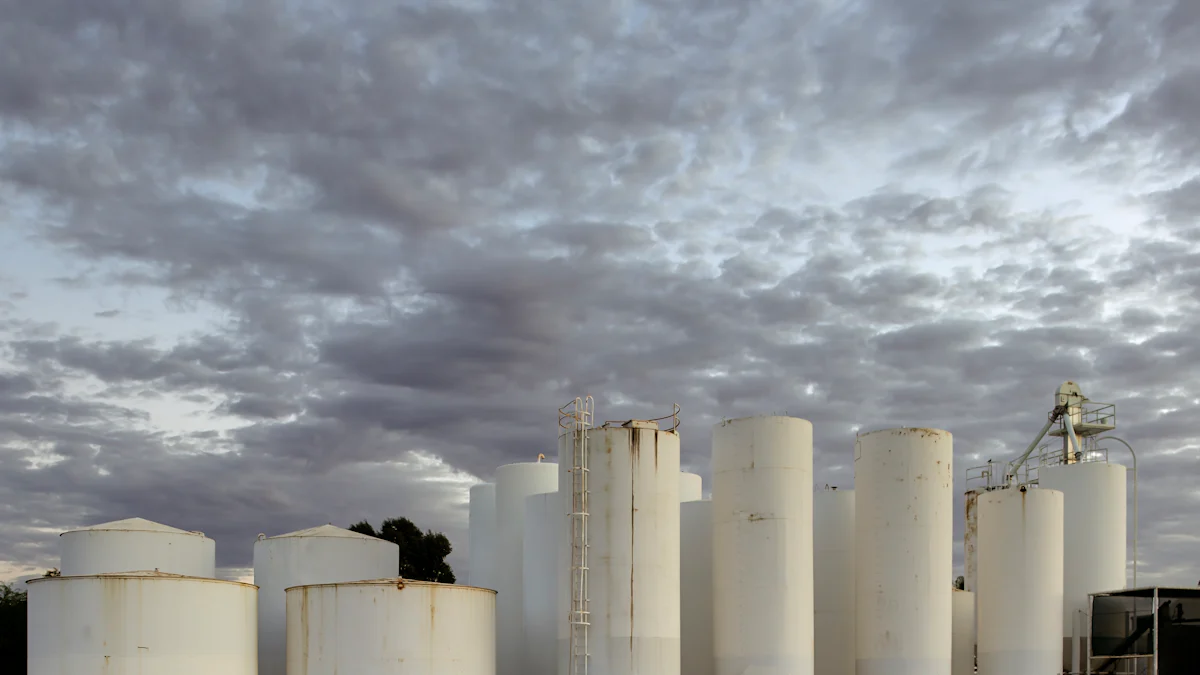
Proper maintenance and cleaning of mixing and loading spray tanks are essential for ensuring their longevity and maintaining their efficiency. By adopting the right practices, you can prevent contamination, reduce downtime, and ensure that your tanks remain in optimal condition for years.
Features That Simplify Maintenance
When selecting a spray tank, look for features that make maintenance easier. Tanks with smooth interior surfaces reduce residue buildup, making cleaning faster and more effective. Removable lids or access ports allow you to inspect and clean the tank thoroughly without difficulty.
Tanks equipped with self-draining designs ensure that no liquid remains trapped inside after use. This feature minimizes the risk of chemical residue hardening, which can complicate cleaning. Additionally, tanks with integrated measurement markings help you properly mix chemicals, reducing the chances of overuse or spillage during operations.
Some modern tanks also come with automated cleaning systems. These systems use rotating spray heads to clean the interior without requiring manual scrubbing. Investing in tanks with such features saves time and effort while ensuring consistent cleanliness.
Cleaning Best Practices for Different Materials
Cleaning methods vary depending on the material of your mixing and loading spray tanks. Understanding these differences ensures that you use the most effective approach without damaging the tank.
Stainless Steel Tanks: Use warm water and a mild detergent to clean stainless steel tanks. Avoid abrasive tools that could scratch the surface. For stubborn residues, a soft brush or non-corrosive cleaning agent works best. Rinse thoroughly to remove any cleaning solution.
Plastic Tanks: Plastic tanks require gentle cleaning to prevent scratches or cracks. Use a soft cloth or sponge with a mild soap solution. Avoid using harsh chemicals that could degrade the plastic over time. Always rinse the tank multiple times to ensure no residue remains.
Fiberglass Tanks: Fiberglass tanks are durable but can be sensitive to certain chemicals. Use a non-abrasive cleaner and a soft brush to remove residues. Inspect the tank for any signs of wear or damage during cleaning, as fiberglass can develop small cracks over time.
Before cleaning, always empty the tank completely and dispose of any leftover chemicals according to local regulations. Pre-cleaning preparation, such as removing fittings or hoses, ensures that every part of the tank is accessible for cleaning.
Tips for Prolonging Tank Lifespan
Regular maintenance not only keeps your spray tank clean but also extends its lifespan. Follow these tips to maximize the durability of your tank:
Inspect Regularly: Conduct routine inspections to identify cracks, leaks, or signs of corrosion. Addressing these issues early prevents further damage.
Store Properly: When not in use, store your tank in a shaded, dry area. UV rays and extreme weather conditions can weaken the tank material over time.
Use Compatible Chemicals: Always ensure that the chemicals you use are compatible with the tank material. Incompatible chemicals can cause degradation or structural failure.
Flush After Each Use: After every mixing session, flush the tank with clean water to remove any remaining chemicals. This practice prevents residue buildup and contamination.
Follow Manufacturer Guidelines: Adhere to the maintenance and cleaning instructions provided by the tank manufacturer. These guidelines are tailored to the specific design and material of your tank.
By implementing these practices, you can ensure that your mixing and loading spray tanks remain reliable and efficient. Proper care not only protects your investment but also helps you properly mix chemicals for consistent results.
Cost and Budget Considerations
When selecting agricultural chemical mixing tanks, understanding cost and budget considerations is essential. A well-informed decision ensures you balance quality with affordability while minimizing long-term expenses.
Balancing Quality and Affordability
Finding the right balance between quality and affordability requires careful evaluation. High-quality tanks often come with a higher price tag, but they provide better durability and performance. For example, stainless steel tanks, known for their corrosion resistance and structural integrity, may cost more upfront. However, their longevity and reliability make them a cost-effective choice over time.
You should also consider the type of chemicals you handle. Tanks designed for corrosive substances, such as those with specialized linings or double-wall construction, typically cost 3-5 times more than standard tanks. While these options may seem expensive initially, they prevent leaks and reduce maintenance costs, saving you money in the long run.
To make an informed choice, compare the features of different tanks within your budget. Look for options that meet your operational needs without compromising on safety or quality. Investing in a durable tank ensures fewer replacements and repairs, ultimately lowering your overall expenses.
Evaluating Total Cost of Ownership
The total cost of ownership (TCO) goes beyond the initial purchase price. It includes maintenance, repairs, downtime, and potential upgrades. While a cheaper tank might seem appealing, it could lead to higher long-term costs if it requires frequent repairs or fails prematurely.
For instance, tanks made from materials like carbon steel or stainless steel offer long-lasting performance. These materials withstand harsh conditions, reducing the likelihood of damage. By choosing a tank with a longer lifespan, you minimize replacement costs and operational disruptions.
Consider the maintenance requirements of the tank. Tanks with smooth surfaces and self-draining designs simplify cleaning, saving you time and labor costs. Additionally, tanks with certifications, such as ISO or CE, ensure compliance with safety standards, reducing the risk of fines or penalties.
By evaluating TCO, you gain a clearer picture of the tank’s value over its lifetime. This approach helps you prioritize options that deliver consistent performance and cost savings.
Comparing Quotes and Warranties
Comparing quotes from multiple manufacturers allows you to identify the best value for your investment. Request detailed quotes that outline the tank’s specifications, materials, and included features. Pay attention to any additional costs, such as shipping or installation fees, to avoid surprises.
Warranties play a crucial role in your decision-making process. A comprehensive warranty reflects the manufacturer’s confidence in their product. Look for warranties that cover defects, material failures, and workmanship for an extended period. For example, some manufacturers offer warranties of up to 10 years, providing peace of mind and protection for your investment.
When comparing quotes, consider the reputation and expertise of the manufacturer. Companies like Chenma Machinery Co., Ltd., known for their high-quality stainless steel tanks, offer customizable solutions tailored to your needs. Their adherence to international safety and quality standards ensures reliable performance.
By thoroughly comparing quotes and warranties, you can select a tank that aligns with your budget while meeting your operational requirements. This step ensures you receive a product that delivers long-term value and reliability.
Customization Options for Tank Mixing Procedures
Tailoring Tanks to Your Specific Needs
Every agricultural operation has unique requirements, and your tank should reflect those needs. Customizing your tank ensures it aligns perfectly with your processes, whether you handle specific chemicals, require precise mixing capabilities, or need a tank that fits within a limited space. By tailoring the design, you can enhance efficiency and reduce operational challenges.
Custom tanks allow you to select features such as size, shape, and material. For example, if you work with highly corrosive chemicals, stainless steel tanks provide superior resistance and durability. You can also choose additional features like integrated measurement markings, self-draining designs, or automated mixing systems to streamline your workflow. These customizations not only improve functionality but also ensure compliance with safety and environmental standards.
When designing a tank, consider your current and future needs. A tank built for scalability can accommodate growth, saving you from costly upgrades later. Tailoring your tank to your specific requirements ensures it becomes a valuable asset in your operations.
Working with Manufacturers for Custom Designs
Collaborating with experienced manufacturers is essential when creating a custom tank. Manufacturers with expertise in tank mixing procedures can guide you through the design process, ensuring the final product meets your exact specifications. Their knowledge of materials, construction techniques, and industry standards guarantees a high-quality tank that performs reliably.
Manufacturers like Chenma Machinery Co., Ltd. specialize in engineering tanks tailored to unique applications. With advanced machinery and skilled engineers, they can modify existing designs or create entirely new ones to suit your needs. For instance, they can incorporate features like reinforced walls for added strength or venting systems for pressure management. Their ability to adapt tanks to specific chemical properties ensures compatibility and safety.
Effective communication with the manufacturer is key. Share detailed information about your operational requirements, including the type of chemicals used, mixing processes, and storage conditions. This collaboration ensures the tank integrates seamlessly into your operations and delivers long-term value.
Benefits of Chenma’s Custom Stainless Steel Tanks
Chenma Machinery Co., Ltd. offers exceptional custom stainless steel tanks designed to meet the demands of agricultural operations. These tanks provide unmatched durability, corrosion resistance, and structural integrity, making them ideal for handling a wide range of chemicals. Their stainless steel construction ensures longevity, reducing the need for frequent replacements and minimizing maintenance costs.
Chenma’s tanks stand out for their adherence to international safety and quality standards, including ISO9001-2005 and EU CE certifications. These certifications guarantee that the tanks meet rigorous testing requirements, ensuring reliable performance under various conditions. Additionally, Chenma’s advanced manufacturing capabilities allow for precise customization, from size and capacity to specialized features like automated mixing systems or UV-resistant coatings.
By choosing Chenma’s custom tanks, you gain access to a product tailored to your specific needs. Their expertise in tank mixing procedures ensures compatibility with your chemicals and processes, enhancing efficiency and safety. Investing in a Chenma tank provides long-term value, protecting your operations and supporting your growth.
Environmental and Regulatory Compliance
Ensuring environmental and regulatory compliance is a critical aspect of selecting agricultural chemical mixing tanks. By choosing eco-friendly options, adhering to local safety standards, and implementing efficient mixing practices, you can protect the environment while meeting legal requirements.
Eco-Friendly Tank Options
Eco-friendly tanks play a significant role in reducing environmental impact. These tanks are designed with materials and features that minimize chemical leakage and contamination. For example, stainless steel tanks are highly durable and resistant to corrosion, which prevents harmful substances from seeping into the soil or water sources. Their long lifespan also reduces waste by eliminating the need for frequent replacements.
Some tanks come with secondary containment systems, such as built-in basins, to catch spills and leaks. These systems act as an additional barrier, ensuring that chemicals do not escape into the environment. Tanks with self-draining designs further enhance eco-friendliness by preventing residue buildup, which can lead to improper disposal of leftover chemicals.
When selecting a tank, consider options that meet environmental certifications, such as ISO14001-2015. These certifications indicate that the tank has been manufactured with sustainable practices and complies with environmental management standards. By choosing eco-friendly tanks, you contribute to a safer and cleaner environment.
Meeting Local Safety and Environmental Standards
Compliance with local safety and environmental standards is essential for avoiding legal issues and ensuring safe operations. Regulatory bodies, such as the Environmental Protection Agency (EPA), establish guidelines for the storage and handling of chemicals. These guidelines often include requirements for tank materials, design, and maintenance.
For instance, underground storage tanks must meet specific codes, such as those outlined by the American Petroleum Institute (API) and the American Society of Mechanical Engineers (ASME). These codes ensure that tanks are constructed to withstand pressure, prevent leaks, and maintain structural integrity. Regular inspections and routine maintenance are also mandated to identify potential risks and address them promptly.
To comply with these standards, familiarize yourself with the regulations in your area. Ensure that your tank meets all necessary certifications and undergoes periodic inspections. By adhering to these requirements, you not only avoid penalties but also create a safer working environment.
Reducing Chemical Waste Through Efficient Mixing
Efficient mixing practices significantly reduce chemical waste, benefiting both your operations and the environment. Properly designed tanks ensure that chemicals are mixed thoroughly, minimizing the risk of overuse or spillage. For example, tanks with integrated measurement markings help you achieve precise chemical ratios, reducing excess usage.
Automated mixing systems further enhance efficiency by delivering consistent results without manual intervention. These systems prevent uneven mixing, which can lead to wasted chemicals or ineffective applications. Additionally, tanks with smooth interior surfaces make it easier to clean and remove residues, ensuring that no leftover chemicals contaminate future batches.
By investing in tanks that support efficient mixing, you optimize resource usage and reduce waste. This approach not only lowers operational costs but also aligns with environmental sustainability goals.
Common Mistakes to Avoid When Choosing a Tank
Overlooking Material Compatibility
Failing to consider material compatibility can lead to serious issues when selecting a tank. Each chemical has unique properties, such as pH levels, reactivity, and temperature requirements. If the tank material cannot withstand these properties, it may degrade, leak, or even fail entirely. For example, using a plastic tank for highly acidic chemicals could result in corrosion or structural damage over time.
To avoid this mistake, always review the chemical’s label for storage and mixing recommendations. Match the tank material to the chemical’s characteristics. Stainless steel tanks, for instance, are highly resistant to corrosion and are ideal for handling aggressive substances. By ensuring compatibility, you protect your investment and maintain safety during operations.
“I mixed up a batch of MCPA 500 A and Glyphosate at ¾ recommended label rate, but then got delayed on application with a stuck drill. I came back to the sprayer and found a nasty chemical precipitate – like waxy chunks. Agitation didn’t break them down. I dumped the tank out as I didn’t want to pump it through the booms.”
— Anonymous Contributor
This real-life example highlights the consequences of overlooking compatibility. Improper mixing or storage can lead to chemical reactions, causing clogs or residues that are difficult to clean. Always prioritize material compatibility to prevent such costly mistakes.
Underestimating Size Requirements
Choosing the wrong tank size can disrupt your workflow and increase expenses. An undersized tank may require frequent refills, leading to delays and inefficiencies. Conversely, an oversized tank wastes resources and occupies unnecessary space. Both scenarios can hinder productivity and inflate costs.
To determine the right size, assess your daily or seasonal chemical usage. Consider the volume required for each mixing session and the available space in your facility. For instance, if you handle large-scale operations, a tank with a higher capacity ensures uninterrupted processes. Planning for future growth is equally important. A slightly larger tank can accommodate increased demand, saving you from costly upgrades later.
Avoid the temptation to guess your size requirements. Precise calculations based on your operational needs ensure you select a tank that optimizes efficiency and minimizes waste.
Ignoring Maintenance Needs
Neglecting maintenance considerations can shorten the lifespan of your tank and compromise its performance. Tanks that are difficult to clean or inspect often accumulate residues, leading to contamination or structural damage. Over time, this neglect increases repair costs and reduces the tank’s reliability.
When choosing a tank, prioritize features that simplify maintenance. Smooth interior surfaces, self-draining designs, and removable lids make cleaning easier and more effective. Regular inspections are also crucial. Look for signs of wear, such as cracks or corrosion, and address them promptly to prevent further damage.
Follow the manufacturer’s maintenance guidelines to ensure proper care. For example, stainless steel tanks require gentle cleaning with non-abrasive tools to preserve their surface integrity. By adopting these practices, you extend the tank’s lifespan and maintain its efficiency.
Ignoring maintenance needs not only risks equipment failure but also impacts safety and compliance. A well-maintained tank ensures consistent performance and protects your investment.
Choosing the right agricultural chemical mixing tanks is essential for ensuring safety, efficiency, and long-term value. You need to evaluate factors like material compatibility, size, safety features, durability, and maintenance requirements. Consulting with experts, such as storage tank specialists, can help you select a tank that aligns with your operational needs. A reputable supplier, like Chenma Machinery Co., Ltd., offers high-quality, customizable stainless steel tanks designed to meet the latest safety and quality standards. By making informed decisions, you can enhance productivity, reduce costs, and protect your investment.
FAQ
What is tank mixing?
Tank mixing involves combining multiple registered agricultural products in a single sprayer tank. This method allows you to apply various chemicals, such as fertilizers, herbicides, or pesticides, in one pass. It saves time and reduces labor while ensuring efficient application across your fields.
Why is material compatibility important for tank mixing?
Material compatibility ensures that the tank can safely handle the chemicals you mix. Some chemicals are highly corrosive and can damage tanks made from incompatible materials. For example, stainless steel tanks resist corrosion and maintain structural integrity, making them a reliable choice for handling aggressive substances.
What are the key considerations for tank mixing?
Tank mixing requires careful planning to avoid incompatibility issues. Incompatible chemicals can cause clogs, residues, or even chemical reactions that reduce effectiveness. Always check the product labels for compatibility information and conduct a jar test to ensure the chemicals mix well before adding them to the tank.
How can I prevent tank mixing incompatibility?
To prevent incompatibility, follow these steps:
- Review the labels of all products you plan to mix.
- Conduct a small-scale jar test to observe how the chemicals interact.
- Add products to the tank in the correct order, typically starting with water-soluble products.
- Use agitation to ensure thorough mixing.
These practices help you avoid costly mistakes and ensure effective application.
Is there a general label statement regarding tank mixing?
Yes, many agricultural products now include a general label statement about tank mixing. This statement consolidates tank mixing guidelines in one place, offering greater flexibility in choosing compatible products. Always read and follow the label instructions to ensure safe and effective mixing.
What safety measures should I follow during tank mixing?
Safety is crucial when handling chemicals. Use personal protective equipment (PPE) such as gloves, goggles, and chemical-resistant clothing. Ensure proper ventilation in the mixing area to avoid inhaling fumes. Always add chemicals to water, not the other way around, to minimize splashing or reactions.
How do I clean my tank after mixing chemicals?
Cleaning your tank after each use prevents contamination and extends its lifespan. Follow these steps:
- Empty the tank completely and dispose of leftover chemicals according to local regulations.
- Rinse the tank with clean water to remove residues.
- Use a mild detergent or non-corrosive cleaning agent for stubborn residues.
- Rinse thoroughly to ensure no cleaning solution remains.
Regular cleaning keeps your tank in optimal condition and ensures accurate mixing in future applications.
Can I customize my tank for specific mixing needs?
Yes, many manufacturers offer customizable tanks to meet your unique requirements. You can choose features like size, material, and additional components such as automated mixing systems or self-draining designs. Custom tanks enhance efficiency and ensure compatibility with your specific chemicals and processes.
What are the benefits of using stainless steel tanks for mixing?
Stainless steel tanks provide excellent durability and corrosion resistance. They handle a wide range of chemicals without degrading, ensuring long-term reliability. These tanks also meet stringent safety and quality standards, making them a trusted choice for agricultural operations.
How can I ensure environmental compliance when using mixing tanks?
To ensure environmental compliance, choose tanks with eco-friendly features like secondary containment systems to prevent leaks. Follow local regulations for chemical storage and disposal. Efficient mixing practices, such as using precise chemical ratios, reduce waste and minimize environmental impact.