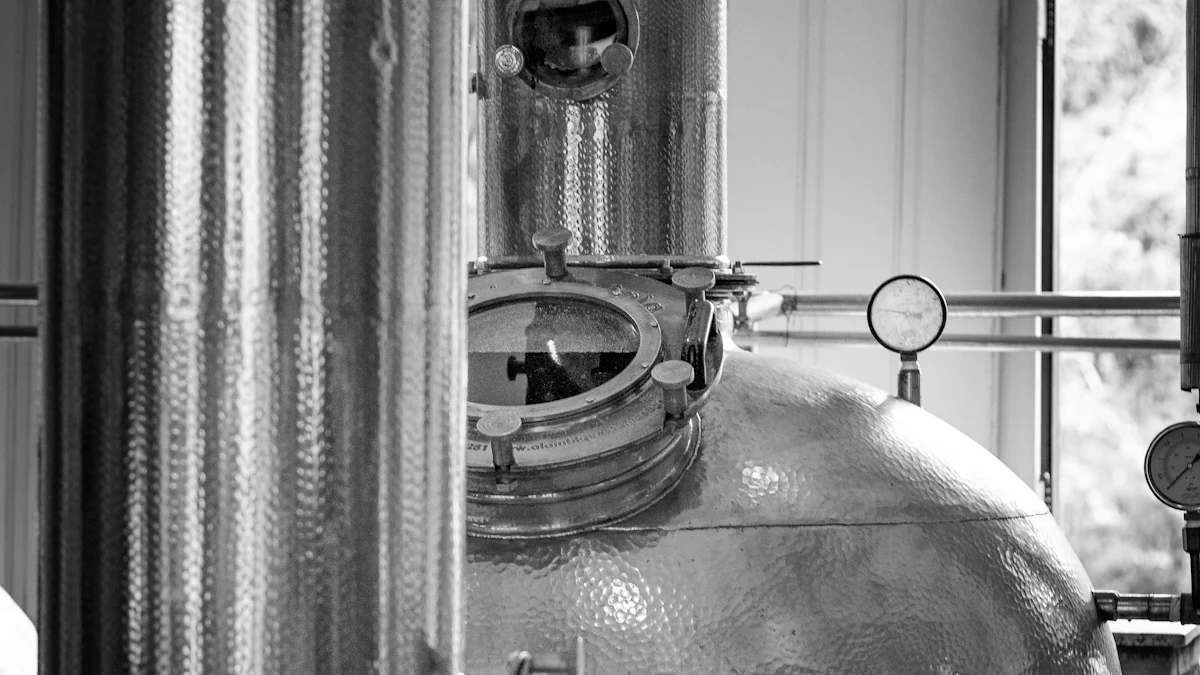
Choosing the right chemical mix tank is vital for ensuring smooth and safe operations in any chemical dispensing process. A well-suited tank enhances efficiency by optimizing mixing performance and reducing operational costs. It also safeguards against potential hazards by ensuring compatibility with the chemicals being handled. Tanks designed for specific needs improve product uniformity and extend service life, making them indispensable for industries like sanitation, medicine, and water treatment. By selecting the right tank, you can prevent costly errors, maintain compliance with safety standards, and achieve consistent results in your chemical dispensing process.
Understanding the Role of a Chemical Mix Tank
Chemical mix tanks play a pivotal role in various industrial processes. These tanks are designed to ensure precise and efficient mixing of chemicals, which is essential for maintaining product quality and operational safety. By understanding their purpose and significance, you can make informed decisions when selecting the right tank for your needs.
What is a Chemical Mix Tank?
A chemical mix tank is specialized equipment used to blend, dilute, or process chemical substances. These tanks are engineered to handle a wide range of chemical compounds, ensuring uniformity and consistency in the final mixture. They often feature separate inputs for different components, allowing controlled addition and precise blending.
Industries such as water treatment, pharmaceuticals, and manufacturing rely heavily on these tanks. For example, in the chemical industry, mix tanks are used to create products like detergents, adhesives, and paints. Their design ensures that the mixing process occurs in a controlled environment, preventing contamination and ensuring high-quality results.
Why is it Essential for Chemical Processing?
Chemical mix tanks are indispensable for achieving efficiency and safety in chemical processing. They ensure that chemicals are mixed accurately, which is critical for creating new compounds or products. Precision in mixing not only guarantees uniformity but also prevents adverse reactions that could compromise product quality or safety.
These tanks also play a vital role in compliance with industry standards. Properly designed chemical dilution systems, for instance, help industries meet regulatory requirements while maintaining operational efficiency. Additionally, the use of durable and compatible materials in tank construction minimizes risks associated with corrosion or chemical incompatibility.
By using a chemical mix tank, you can optimize your processes, reduce waste, and enhance productivity. Whether you are blending liquids for industrial applications or preparing solutions for sanitation, these tanks provide the reliability and precision needed for successful operations.
Identifying Your Needs for Batch Mixing Equipment
Selecting batch mixing equipment requires a clear understanding of your operational needs. By identifying the right specifications, you can ensure efficiency, safety, and cost-effectiveness in your processes. This section will guide you through the critical factors to consider when determining the best equipment for your application.
Determining the Required Capacity
The capacity of your batch mixing equipment is one of the most important factors to evaluate. You need to match the tank size to your production volume to avoid inefficiencies. Tanks range from small-scale units with capacities of 1 gallon to industrial systems that hold up to 25,000 gallons. For smaller operations, compact tanks may suffice, but large-scale production often demands bulk storage solutions.
Consider the frequency of your mixing cycles. If you process chemicals in high volumes or require continuous mixing, a larger tank will reduce downtime and improve productivity. On the other hand, overestimating your capacity needs can lead to unnecessary costs and wasted space. Always align the tank size with your current and projected production requirements.
Evaluating Chemical Compatibility
Chemical compatibility is crucial when selecting batch mixing equipment. The materials used in the tank must withstand the chemical properties of the substances being mixed. For example, stainless steel is a popular choice due to its strength, corrosion resistance, and ease of cleaning. It works well with many chemicals, including acids and solvents. However, for highly reactive or corrosive substances, polyethylene or polypropylene tanks may be more suitable.
You should also consider the concentration levels of the chemicals. Some materials, like carbon steel, may degrade when exposed to high concentrations of certain compounds. Using incompatible materials can lead to contamination, equipment failure, or safety hazards. Always consult chemical compatibility charts or manufacturers to ensure the tank material matches your specific needs.
Defining the Application Requirements
Your application requirements will dictate the design and features of your batch mixing equipment. Start by identifying the type of mixing process you need. For instance, batch mixing involves processing a set amount of material at a time, making it ideal for applications requiring precise formulations. Industries like pharmaceuticals, food processing, and water treatment often rely on this method for consistent results.
Next, assess the viscosity of the liquids you plan to mix. High-viscosity substances may require specialized mixers with greater power and advanced agitation systems. Additionally, consider whether your process involves heating, cooling, or pressurization. Tanks designed for these functions often include insulation, jackets, or reinforced walls to handle extreme conditions.
Finally, think about the level of automation you need. Some batch mixing systems come with programmable controls, allowing you to monitor and adjust parameters like speed and temperature. These features can enhance precision and reduce manual intervention, especially in complex processes.
By carefully evaluating these factors, you can select batch mixing equipment that aligns with your operational goals and ensures long-term reliability.
Key Features of the Right Chemical Dilution System
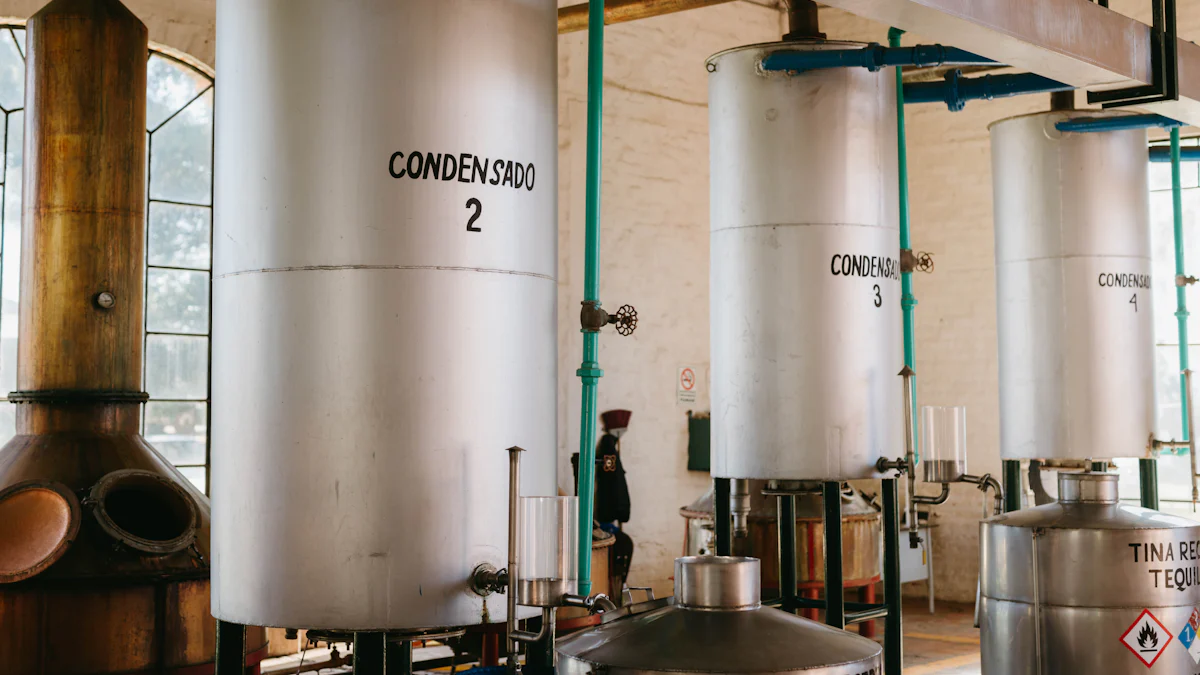
Material Selection for Durability and Safety
The material of your chemical dilution system plays a critical role in ensuring durability and safety. Selecting the right material depends on the chemicals you plan to process. For example, stainless steel is a popular choice due to its corrosion resistance and compatibility with a wide range of substances. It provides long-term reliability and withstands high temperatures and pressures, making it ideal for demanding batch mixing applications.
For highly reactive or corrosive chemicals, alternative materials like polyethylene or polypropylene may be more suitable. These materials resist chemical degradation and offer a cost-effective solution for specific applications. Always verify the compatibility of the tank material with the chemicals you use to prevent contamination, equipment failure, or safety risks. Consulting chemical compatibility charts or working with manufacturers ensures you make the best choice for your needs.
Safety features also enhance the integrity of the system. Modern tanks often include double walls, pressure relief valves, and insulation to protect against leaks, temperature fluctuations, and environmental hazards. These features not only safeguard your operations but also help you comply with industry regulations.
Design and Construction for Optimal Mixing
The design and construction of a chemical dilution system significantly impact its performance. Cylindrical tanks are commonly used for batch mixing because they promote uniform mixing and efficient drainage. Adding baffles to these tanks improves agitation and prevents vortex formation, ensuring consistent results. For all-liquid mixtures, rectangular tanks may be more appropriate due to their ability to handle specific mixing dynamics.
Advanced systems often incorporate heating or cooling jackets, insulation, or pressurization to support specialized processes. These features allow you to maintain precise temperature control, which is essential for certain chemical reactions. Additionally, agitators installed within the tanks ensure uniform mixing of liquids, even for high-viscosity substances.
Construction quality is equally important. Tanks built with precision and adherence to safety standards minimize risks and extend service life. Features like reinforced walls and programmable controls enhance the system’s reliability and adaptability. By choosing a well-designed system, you can optimize your batch mixing operations and achieve consistent results.
Operational Features for Efficiency
Efficiency is a key consideration when selecting the best dilution system for your operations. Modern chemical dilution systems come equipped with advanced operational features that streamline processes and reduce manual intervention. For instance, programmable controls allow you to monitor and adjust parameters like mixing speed, temperature, and pressure. These automated features improve precision and ensure consistent outcomes in batch mixing.
Flow meters and sensors are other valuable additions. They provide real-time data on chemical flow rates and tank levels, helping you maintain accuracy and avoid overflows or shortages. Systems with automatic shut-off valves and safety sensors further enhance operational efficiency by preventing accidents and minimizing downtime.
Consider the scalability of your system as well. If your production needs grow, having a system that can be easily upgraded or customized will save you time and resources. Features like interlinked tanks, modular designs, and additional outlets or gauges allow you to adapt the system to your evolving requirements.
By focusing on these operational features, you can maximize the efficiency of your chemical dilution system while maintaining safety and reliability.
Location and Installation Considerations for a Chemical Mix Tank
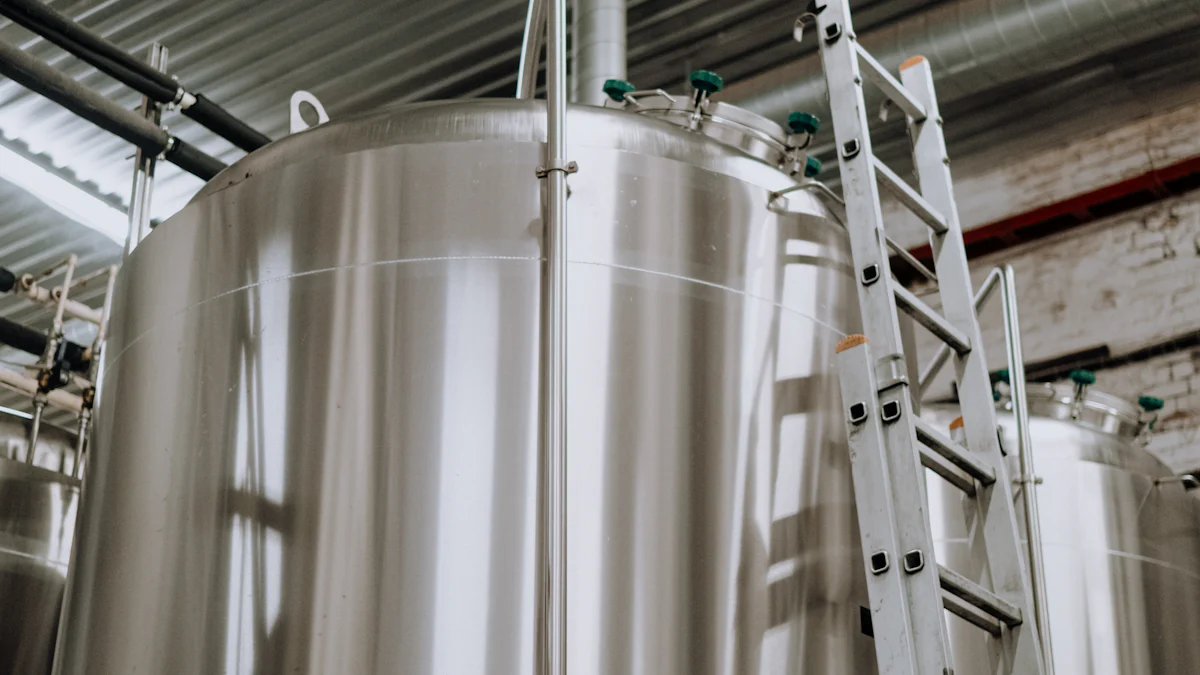
When choosing a chemical mix tank, you must carefully evaluate the location and installation requirements. Proper planning ensures smooth operations, minimizes downtime, and enhances safety. This section will guide you through the critical aspects of space, maintenance, and setup.
Assessing Available Space and Accessibility
The first step in planning your tank’s location is assessing the available space. Measure the area where you intend to install the tank. Ensure the dimensions of the tank fit comfortably within the allocated space. Leave enough room around the tank for movement and additional equipment. Crowded spaces can hinder operations and create safety hazards.
Accessibility is equally important. You need to position the tank in a location that allows easy access for operators and technicians. This is especially crucial for batch mixing processes, which often require frequent monitoring and adjustments. Tanks placed in hard-to-reach areas can lead to inefficiencies and delays.
Consider the proximity of the tank to other equipment. For example, placing the tank near mixing stations or chemical storage areas can streamline workflows. Avoid locations with extreme temperatures or high humidity, as these conditions may affect the tank’s performance and longevity.
Planning for Maintenance and Inspections
Regular maintenance and inspections are essential for keeping your chemical mix tank in optimal condition. When planning the installation, prioritize a location that facilitates these activities. Tanks used for batch mixing often require cleaning, calibration, and part replacements. A well-planned setup reduces the time and effort needed for these tasks.
Ensure the tank’s design allows for easy access to critical components. Features like removable lids, inspection ports, and drain valves simplify maintenance. Position the tank in a way that technicians can safely perform inspections without disrupting operations. For example, elevated platforms or walkways can provide better access to larger tanks.
You should also account for emergency scenarios. In case of leaks or spills, the tank’s location should allow for quick containment and cleanup. Installing the tank on a spill containment platform or within a designated safety zone can help mitigate risks.
Understanding Setup Requirements
Setting up a chemical mix tank involves more than just placing it in the desired location. You need to understand the specific requirements for installation to ensure proper functionality. Start by reviewing the manufacturer’s guidelines. These documents provide detailed instructions on assembling and connecting the tank.
Pay attention to the tank’s foundation. A stable and level surface is crucial for maintaining the integrity of the tank during batch mixing. Concrete pads or steel frames are common choices for supporting industrial tanks. Verify that the foundation can handle the tank’s weight, including the chemicals it will hold.
Next, consider the utility connections. Tanks often require access to power, water, or compressed air for their operation. Plan the installation near these resources to avoid complications. For example, if your tank includes an agitator or heating system, ensure the power supply meets the equipment’s specifications.
Finally, think about ventilation and drainage. Proper ventilation prevents the buildup of harmful fumes, while adequate drainage allows for safe disposal of waste materials. Incorporating these features into the setup ensures compliance with safety standards and enhances operational efficiency.
By addressing these considerations, you can create a well-organized and functional setup for your chemical mix tank. This not only improves the efficiency of your batch mixing processes but also ensures long-term reliability and safety.
Ensuring Safety and Compliance in Your Chemical Dilution System
Safety and compliance are critical when operating a chemical dilution system. By adhering to industry standards and implementing essential safety features, you can protect your workforce, maintain operational efficiency, and avoid costly penalties. This section will guide you through the key aspects of ensuring safety and compliance in your batch mixing processes.
Meeting Industry Standards and Certifications
Industry standards and certifications provide a framework for maintaining quality and safety in chemical dilution systems. These certifications ensure that your equipment meets rigorous testing and performance benchmarks, giving you confidence in its reliability.
Several certifications are essential for chemical mix tanks. For example, ISO 9001 ensures that the manufacturing process follows strict quality management principles. NSF/ANSI/CAN 61 certification guarantees that the materials used in the tank are safe for handling chemicals, especially in applications like water treatment. Additionally, ASTM D 1998 sets standards for the design and construction of polyethylene tanks, ensuring durability and chemical resistance.
Compliance with regulatory bodies is equally important. Organizations like OSHA enforce workplace safety standards to prevent injuries during batch mixing operations. Local fire departments may also impose specific guidelines to mitigate fire hazards associated with chemical storage and mixing. Adhering to these regulations not only ensures safety but also helps you avoid legal complications.
When selecting a chemical dilution system, always verify that the manufacturer complies with these certifications and standards. This step ensures that your equipment aligns with industry requirements and operates safely under various conditions.
Implementing Essential Safety Features
Safety features play a vital role in protecting both personnel and the environment during batch mixing. Modern chemical dilution systems incorporate advanced safety mechanisms to minimize risks and enhance operational reliability.
One critical feature is the use of corrosion-resistant materials. Stainless steel, for instance, offers excellent durability and compatibility with a wide range of chemicals. For highly corrosive substances, tanks made from polyethylene or polypropylene provide an effective alternative. These materials prevent leaks and contamination, ensuring the integrity of your dilution process.
Pressure relief valves are another essential component. These valves regulate internal pressure within the tank, preventing potential explosions or structural damage. Double-walled tanks add an extra layer of protection by containing leaks and reducing the risk of environmental contamination.
Ventilation systems are crucial for managing fumes generated during batch mixing. Proper ventilation prevents the buildup of hazardous gases, protecting workers from exposure. Additionally, spill containment platforms safeguard against accidental leaks, ensuring quick and efficient cleanup.
Automation enhances safety by reducing manual intervention. Features like programmable controls allow you to monitor and adjust parameters such as mixing speed and temperature. Sensors and alarms provide real-time alerts for issues like overflows or equipment malfunctions, enabling prompt corrective action.
By incorporating these safety features into your chemical dilution system, you create a secure and compliant environment for your operations. These measures not only protect your team but also ensure the long-term reliability of your batch mixing processes.
Cost Considerations for Batch Mixing Equipment
Balancing Initial Investment with Long-Term Value
When investing in batch mixing equipment, you must evaluate both the upfront cost and the long-term value it provides. The initial investment often depends on the tank’s material, size, and features. For example, stainless steel tanks are among the most durable and versatile options available. However, they come with a higher price tag—up to five times more expensive than alternatives like polyethylene tanks. This premium cost reflects their superior corrosion resistance, strength, and ability to handle high temperatures and pressures.
If your operations involve less corrosive chemicals, budget-friendly materials like linear polyethylene may be a better choice. These tanks are cost-effective and well-suited for storing acids with low corrosive properties. By selecting the right material for your specific needs, you can avoid overpaying for features that may not be necessary for your application.
The size of the tank also plays a significant role in determining the cost. Storage systems typically range from $100 to $300 per cubic meter for capacities between 10 and 10,000 cubic meters. However, costs can increase by two to ten times for tanks designed to handle corrosive chemicals, cryogenic storage, or extreme sizes. To balance your investment, consider your current production needs and future scalability. Overspending on a larger tank than required can tie up resources unnecessarily, while underestimating your capacity needs may lead to inefficiencies and additional expenses later.
Long-term value comes from durability, efficiency, and adaptability. Tanks made from high-quality materials and equipped with advanced features, such as programmable controls or heating systems, often deliver better performance over time. While these options may require a higher initial investment, they reduce maintenance costs, minimize downtime, and extend the equipment’s lifespan, ultimately saving you money in the long run.
Estimating Maintenance and Operating Costs
Maintenance and operating costs are critical factors to consider when choosing batch mixing equipment. These ongoing expenses can significantly impact your budget over the equipment’s lifecycle. Understanding these costs upfront helps you make an informed decision and avoid unexpected financial burdens.
The material of the tank directly influences maintenance requirements. Stainless steel tanks, while more expensive initially, require less frequent maintenance due to their resistance to corrosion and wear. On the other hand, tanks made from polyethylene or polypropylene may need more regular inspections and repairs, especially when used with highly reactive chemicals. Choosing a material that aligns with your chemical dilution system’s demands can help you control maintenance costs.
Operating costs include energy consumption, cleaning, and replacement parts. Tanks equipped with agitators or heating systems may consume more energy, so it’s essential to evaluate their efficiency. Modern systems with energy-saving features can reduce these costs without compromising performance. Additionally, consider the ease of cleaning and maintenance. Tanks with removable lids, inspection ports, or self-cleaning mechanisms simplify these tasks, saving time and labor costs.
Another factor to account for is the cost of compliance. Ensuring your batch mixing equipment meets industry standards and safety regulations may involve additional expenses, such as certifications or upgrades. However, these investments protect your operations from fines, legal issues, and potential accidents, making them worthwhile in the long term.
By carefully estimating maintenance and operating costs, you can choose a chemical dilution system that fits your budget while delivering reliable performance. This approach ensures that your investment remains cost-effective throughout its lifecycle.
Customization Options for Your Chemical Mix Tank
Tailoring the Tank to Your Specific Needs
Customizing a chemical mix tank allows you to address the unique demands of your operations. Every industry has specific requirements, and a one-size-fits-all approach often falls short. By tailoring the tank to your needs, you can enhance efficiency, safety, and overall performance.
Start by identifying the key factors that influence your tank’s design. Consider the type of chemicals you handle. For hazardous or highly reactive substances, manufacturers can incorporate special coatings or corrosion-resistant materials like stainless steel or polyethylene. These features ensure durability and prevent chemical degradation.
Evaluate the size and capacity requirements of your operations. Manufacturers offer tanks in a wide range of sizes, from compact units for small-scale applications to large tanks for industrial-scale production. Customizing the tank’s dimensions ensures it fits seamlessly into your workspace while meeting your production goals.
Think about the specific features your process demands. For example, if your application involves high-pressure mixing, you can request reinforced walls or pressure-resistant designs. If temperature control is critical, manufacturers can add heating or cooling jackets to maintain precise conditions. These tailored features optimize the tank for your unique processes.
Customization also extends to operational convenience. You can request additional ports, inspection windows, or automated controls to simplify monitoring and maintenance. These adjustments not only improve functionality but also reduce downtime and labor costs.
By working closely with manufacturers, you can design a tank that aligns perfectly with your operational needs. This approach ensures that every aspect of the tank contributes to the success of your chemical mixing processes.
Collaborating with Manufacturers for Custom Solutions
Partnering with manufacturers opens the door to innovative and practical solutions for your chemical mix tank. Experienced manufacturers bring expertise and resources to create tanks that meet your exact specifications. Collaboration ensures that your tank is not only functional but also cost-effective and compliant with industry standards.
Manufacturers often provide guidance throughout the design process. They help you select the right materials, features, and configurations based on your requirements. For instance, if you need a tank for long-term storage, they might recommend adding protective coatings to extend its lifespan. If scalability is a concern, they can design a system that accommodates future growth.
“Our engineering team works closely with clients to develop custom tanks that address their unique challenges,” says a leading manufacturer. This hands-on approach ensures that your tank performs reliably under real-world conditions.
Customization also allows you to explore advanced options. Manufacturers can integrate specialized mixers, such as top-mounted or side-mounted agitators, to suit your mixing dynamics. They can also include modular designs, enabling you to expand or modify the system as your needs evolve.
Budget considerations play a significant role in customization. Manufacturers offer flexibility to align the tank’s design with your financial constraints. Whether you need a high-end solution with advanced features or a more economical option, they can tailor the tank to fit your budget without compromising quality.
Collaborating with manufacturers ensures that your chemical mix tank is a perfect match for your operations. Their expertise, combined with your input, results in a solution that enhances productivity, safety, and long-term value.
Making the Final Decision on the Right Chemical Dilution System
Comparing Options and Evaluating Suppliers
Choosing the right chemical dilution system requires careful evaluation of available options and suppliers. Start by comparing the features of different systems. Look for tanks that meet your specific needs, such as capacity, material compatibility, and operational features. Assess whether the system includes essential safety mechanisms like pressure relief valves or corrosion-resistant materials. These features ensure reliability and compliance with industry standards.
Evaluate the reputation of potential suppliers. Research their experience in manufacturing chemical dilution systems. A supplier with a proven track record often delivers high-quality products. Check for certifications like ISO 9001 or CE marking, which indicate adherence to strict quality and safety standards. Customer reviews and case studies can also provide valuable insights into the supplier’s reliability and service quality.
Request detailed product specifications and quotes from multiple suppliers. Compare these documents to identify differences in design, materials, and pricing. Pay attention to warranty terms and after-sales support. A supplier offering comprehensive support ensures smooth installation and long-term maintenance of your chemical mix tank.
Ask suppliers about customization options. Some manufacturers provide tailored solutions to meet unique operational requirements. For example, they may offer tanks with additional ports, specialized coatings, or advanced automation features. Collaborating with a supplier who understands your needs can result in a system that enhances efficiency and safety.
Aligning the Choice with Your Operational Goals
Your operational goals should guide your final decision. Begin by identifying your primary objectives, such as improving efficiency, reducing costs, or ensuring safety. Match these goals with the features of the chemical dilution system you are considering. For instance, if your goal is to minimize downtime, choose a system with automated controls and easy maintenance access.
Consider the scalability of the system. If you anticipate growth in production, select a tank that can accommodate increased capacity. Modular designs or expandable systems provide flexibility for future upgrades. This approach prevents the need for costly replacements as your operations evolve.
Think about the environmental impact of your choice. Systems made from eco-friendly materials or those designed for energy efficiency align with sustainability goals. Features like proper ventilation and spill containment also contribute to environmental safety.
Finally, ensure the system aligns with your budget without compromising quality. Balance the initial investment with long-term value. A durable and efficient system may cost more upfront but saves money through reduced maintenance and extended service life. By aligning the system with your operational goals, you create a solution that supports both immediate and future needs.
Common Mistakes to Avoid When Choosing a Chemical Mix Tank
Overlooking Material Compatibility
Choosing the wrong material for your chemical mix tank can lead to serious issues. The tank material must withstand the properties of the chemicals you plan to mix. For example, stainless steel works well with many chemicals due to its corrosion resistance and durability. However, it may not be suitable for highly reactive substances like strong acids or alkalis. In such cases, materials like polyethylene or polypropylene might be better options.
Ignoring material compatibility can result in contamination, equipment failure, or even safety hazards. For instance, if a tank’s material reacts with the chemicals inside, it could compromise the mixture’s quality or cause leaks. Always consult chemical compatibility charts or seek advice from manufacturers to ensure the tank material aligns with your specific needs. This step not only protects your investment but also ensures the reliability of your chemical dilution systems.
Ignoring Future Scalability
Failing to plan for future growth is another common mistake. Many businesses focus solely on their current needs when selecting a chemical mix tank, overlooking the potential for increased production demands. This short-sighted approach can lead to inefficiencies and additional costs down the line.
For example, if your operations expand and your tank cannot handle the increased capacity, you may need to purchase a new system. This not only disrupts workflows but also adds unnecessary expenses. To avoid this, consider your long-term goals when choosing a tank. Opt for a system that offers scalability, such as modular designs or larger capacity options. Planning ahead ensures your tank remains functional and cost-effective as your business grows.
Skipping Safety Features
Neglecting safety features can have severe consequences for both personnel and the environment. Essential safety mechanisms, such as pressure relief valves, spill containment platforms, and proper ventilation, play a critical role in preventing accidents during dilution processes. Without these features, you risk exposing workers to hazardous fumes or dealing with costly chemical spills.
Additionally, tanks made from incompatible or low-quality materials may corrode or fail under pressure, leading to leaks or structural damage. Regular maintenance and inspections are also vital for ensuring safety. Tank owners who neglect basic upkeep often face environmental hazards, financial losses, and legal issues that could have been avoided. Prioritize safety by selecting a tank with robust features and adhering to a strict maintenance schedule. This approach not only protects your team but also ensures compliance with industry regulations.
Choosing the right chemical dilution system requires a clear understanding of your operational needs. By evaluating key features like material compatibility, capacity, and safety mechanisms, you ensure that your system aligns with your goals. Prioritizing safety and compliance protects your team and enhances efficiency. Thorough research helps you avoid costly mistakes and select a solution tailored to your requirements. Consulting experts like Chenma Machinery provides valuable insights and customized options. The right chemical dilution system not only optimizes your processes but also ensures long-term cost-effectiveness and reliability.
FAQ
What are the advantages of utilizing chemical mixing tanks?
Chemical mixing tanks offer several benefits that enhance your operations. They ensure precise blending of chemical compounds, which improves product consistency and quality. These tanks also optimize efficiency by reducing manual labor and minimizing waste. With proper maintenance, you can extend their service life and maintain optimal functionality, saving costs in the long run.
What are chemical mixing tanks, and how are they related to chemical storage tanks?
Chemical mixing tanks are a specialized type of chemical storage tank. While both store chemicals, mixing tanks include integrated systems designed for blending, diluting, or processing chemical substances. This dual functionality makes them essential for industries requiring uniform mixtures, such as water treatment, pharmaceuticals, and manufacturing.
What are tank mixers used for in chemical processing?
Tank mixers play a crucial role in chemical processing. They blend various chemical compounds, including adhesives, paints, coatings, resins, and polymers. These mixers also dissolve solids into liquids and combine liquids with varying viscosities. Their versatility ensures efficient and consistent results across diverse applications.
How do I determine the right material for my chemical mix tank?
The choice of material depends on the chemicals you plan to handle. Stainless steel is ideal for its corrosion resistance and durability, especially with acids and solvents. For highly reactive or corrosive substances, polyethylene or polypropylene may be more suitable. Always consult chemical compatibility charts or manufacturers to ensure the material aligns with your specific needs.
Can chemical mix tanks be customized for specific applications?
Yes, chemical mix tanks can be tailored to meet your unique requirements. Manufacturers can adjust the size, capacity, and features based on your operational needs. For example, you can request additional ports, reinforced walls, or heating and cooling jackets. Customization ensures the tank aligns perfectly with your processes and enhances efficiency.
What safety features should I look for in a chemical mix tank?
Safety features are essential for protecting personnel and the environment. Look for tanks with pressure relief valves, spill containment platforms, and proper ventilation systems. Materials like stainless steel or polyethylene provide corrosion resistance, reducing the risk of leaks. Automation features, such as sensors and alarms, further enhance safety by providing real-time monitoring.
How do I maintain my chemical mix tank for long-term use?
Regular maintenance is key to extending the lifespan of your tank. Clean the tank thoroughly after each use to prevent residue buildup. Inspect critical components, such as valves and seals, for wear and tear. Schedule routine checks to ensure the tank remains in optimal condition. Following the manufacturer’s guidelines helps you avoid costly repairs and downtime.
What factors should I consider when choosing the capacity of a chemical mix tank?
Capacity depends on your production volume and operational needs. Smaller tanks suit low-volume applications, while larger tanks handle industrial-scale production. Consider the frequency of your mixing cycles and future scalability. Choosing the right capacity ensures efficiency without unnecessary costs or space usage.
Are chemical mix tanks compliant with industry standards?
Reputable manufacturers design chemical mix tanks to meet industry standards and certifications. Look for certifications like ISO 9001 for quality management and NSF/ANSI/CAN 61 for chemical safety. Compliance ensures the tank operates safely and aligns with regulatory requirements, protecting your operations from legal and safety risks.
Why is it important to choose a reliable manufacturer for chemical mix tanks?
A reliable manufacturer ensures you receive high-quality equipment tailored to your needs. Experienced manufacturers offer durable materials, advanced features, and customization options. They also provide after-sales support, including installation guidance and maintenance services. Partnering with a trusted supplier guarantees long-term value and operational success.