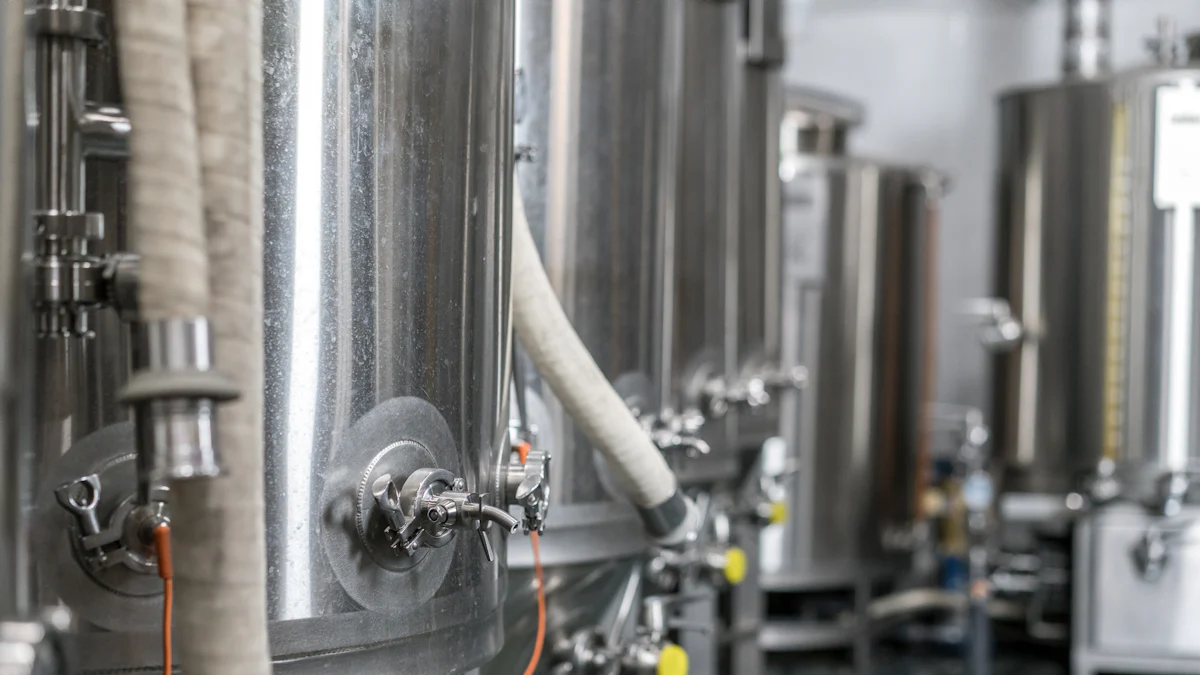
Selecting the right chemical blending tanks system plays a pivotal role in ensuring operational efficiency, safety, and cost-effectiveness. Properly chosen chemical blending tanks allow businesses to optimize production processes, reduce labor costs, and achieve better pricing by enabling bulk material handling. Each tank type offers unique functionalities tailored to specific chemical properties and production needs. Understanding these variations helps organizations make informed decisions, ensuring compatibility with materials and compliance with safety standards. A well-suited chemical blending tanks system not only enhances productivity but also minimizes risks, making it an indispensable asset for any industry relying on chemical processing.
Types of Chemical Blending Tanks and Their Systems
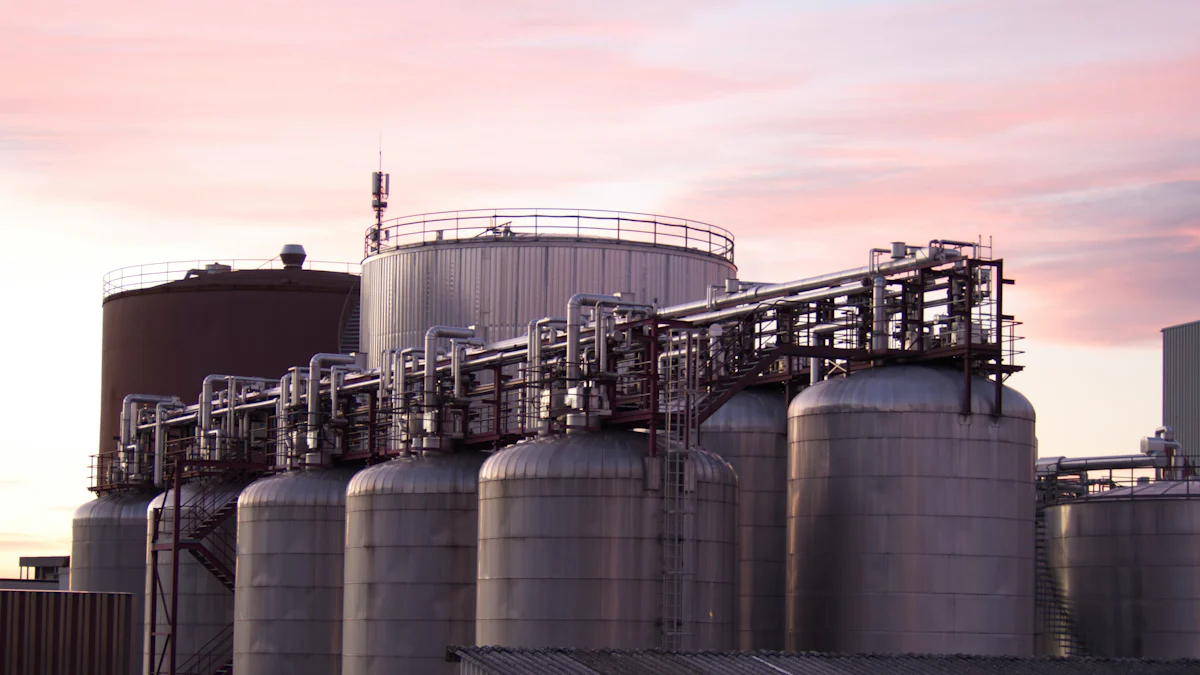
Choosing the right chemical blending tank system requires understanding the various types available. Each system offers unique advantages tailored to specific applications, ensuring efficient and effective mixing processes. Below is an overview of the most common systems used in chemical blending tanks.
Mechanical Mixing Systems
Mechanical mixing systems rely on motorized agitators or mixers to create turbulence within the tank. These systems are highly effective for blending chemicals with varying viscosities or densities. The agitators, often powered by electric motors, ensure consistent mixing by continuously circulating the contents of the tank.
Key Features:
- Active Mixers: These motorized devices provide continuous and powerful circulation, ensuring thorough mixing. For example, PAX Mixers operate on an electric grid and maintain consistent quality in the tank’s contents.
- Tank Geometry Compatibility: Mechanical systems adapt well to tanks with cylindrical or conical designs, enhancing mixing efficiency.
- Versatility: Suitable for industries ranging from specialty chemicals to food and beverage production.
Mechanical mixing systems excel in applications requiring precise control over blending. However, they may demand more space and higher upfront costs compared to other systems.
Bubble Mixing Systems
Bubble mixing systems utilize gas injection to create agitation within the tank. Large bubbles, typically generated by compressed air or gas, rise through the liquid, promoting mixing. This method is particularly effective for low-viscosity liquids or when gentle mixing is required.
Advantages:
- Energy Efficiency: Bubble systems consume less energy compared to mechanical mixers, making them cost-effective for long-term operations.
- Chemical Compatibility: These systems work well with a wide range of chemicals, especially those sensitive to mechanical agitation.
- Low Maintenance: With fewer moving parts, bubble systems require minimal upkeep.
Bubble mixing systems are ideal for applications where maintaining the integrity of delicate chemical compounds is critical. However, they may not be suitable for high-viscosity materials or processes requiring rapid mixing.
Pump Mixing Systems
Pump mixing systems use strategically placed pumps to circulate liquids within the tank. By directing the flow of liquid through nozzles or recirculation loops, these systems achieve uniform mixing without the need for internal agitators.
Notable Benefits:
- Space-Saving Design: Pumps eliminate the need for bulky internal mixers, making them ideal for facilities with limited space.
- Flexibility: Operators can adjust flow rates and nozzle configurations to optimize mixing for specific applications.
- Cost-Effectiveness: Pump systems often have lower initial costs compared to mechanical mixers.
Pump mixing systems are widely used in industries requiring precise control over flow rates and mixing intensity. They are particularly effective for blending low-viscosity liquids or maintaining homogeneity in large tanks.
Hybrid Systems
Hybrid systems combine the strengths of multiple mixing technologies to deliver versatile and efficient blending solutions. These systems integrate features from mechanical, bubble, and pump mixing methods, creating a highly adaptable option for complex chemical blending processes. Industries requiring precise control over mixing parameters often rely on hybrid systems to achieve optimal results.
Key Advantages:
- Enhanced Flexibility: Hybrid systems adapt to a wide range of applications by combining different mixing techniques. For instance, they can handle both high-viscosity materials and delicate compounds without compromising efficiency.
- Improved Efficiency: By leveraging the strengths of multiple systems, hybrid setups ensure thorough mixing while minimizing energy consumption. This makes them ideal for industries prioritizing sustainability and cost-effectiveness.
- Customizable Design: Manufacturers can tailor hybrid systems to meet specific operational needs. Features such as dual-stage inline powder induction and dispersion, as seen in the Alfa Laval Hybrid Powder Mixer, allow for precise blending of powders into liquid streams.
Applications of Hybrid Systems:
- Chemical Processing: Hybrid systems excel in blending chemicals with varying properties. Their ability to combine high-shear mixing with gentle agitation ensures uniformity in complex formulations.
- Food and Beverage Industry: These systems play a crucial role in achieving consistent flavor profiles in products like beverages and sauces. Advanced agitation systems, such as those found in Precision Mixing Tanks, create the ideal turbulence for even distribution of ingredients.
- Pharmaceuticals: Hybrid systems support the production of homogeneous mixtures in pharmaceutical applications, ensuring product quality and compliance with stringent industry standards.
Notable Features:
- Dual-Stage Mixing: Some hybrid systems incorporate dual-stage processes to enhance blending efficiency. This feature is particularly useful for applications requiring high dry matter concentrations.
- Space Optimization: By integrating multiple mixing technologies into a single system, hybrid setups reduce the need for additional equipment, saving valuable floor space.
- Ease of Maintenance: Hybrid systems often feature fewer moving parts compared to standalone mechanical mixers, simplifying maintenance and reducing downtime.
“Hybrid systems represent the future of chemical blending, offering unmatched versatility and efficiency for diverse industrial applications.”
Hybrid systems provide a comprehensive solution for businesses seeking to optimize their blending processes. Their ability to combine the best aspects of various mixing technologies makes them an indispensable asset in industries ranging from specialty chemicals to food production.
Key Features of Chemical Blending Tanks
Material Construction
The material used in constructing chemical blending tanks significantly impacts their durability, chemical resistance, and overall performance. Stainless steel remains a popular choice due to its exceptional resistance to corrosion and ability to withstand extreme temperatures. This material ensures compatibility with a wide range of chemicals, making it ideal for industries such as pharmaceuticals, food processing, and chemical manufacturing.
For applications requiring enhanced hygiene, stainless steel tanks meet stringent sanitary standards. Their smooth surfaces prevent residue buildup, ensuring easy cleaning and maintenance. Additionally, advanced manufacturing techniques allow for the customization of tanks to meet specific operational needs. For instance, tanks designed for high-shear mixing processes often feature reinforced walls to handle the mechanical stress generated during operation.
Other materials, such as polypropylene and thermoplastics, offer cost-effective alternatives for less demanding applications. These materials provide excellent chemical resistance but may lack the structural strength of stainless steel. Selecting the right material depends on the chemical properties of the substances being mixed and the operational environment.
Tank Geometry and Design
The geometry and design of a tank play a crucial role in optimizing the mixing process. Cylindrical tanks are widely used due to their uniform shape, which promotes consistent mixing. Conical and dished-bottom tanks enhance drainage and reduce the risk of residue accumulation, making them suitable for applications requiring frequent cleaning or material changes.
Baffles, strategically placed within the tank, improve mixing efficiency by disrupting the flow patterns of liquids. This prevents vortex formation and ensures thorough blending of all components. Tanks equipped with recirculation nozzles further enhance mixing by directing the flow of liquids in specific patterns. These features are particularly beneficial for high-viscosity materials, where achieving uniformity can be challenging.
Customizable designs allow manufacturers to tailor tanks to specific requirements. For example, dual-stage inline powder induction systems, such as the Alfa Laval Hybrid Powder Mixer, integrate seamlessly into tank designs to facilitate efficient dispersion of powders into liquid streams. This level of customization ensures that tanks meet the unique demands of various industries.
Integral Mixers and Agitators
Integral mixers and agitators form the backbone of any effective mixing system. These components ensure uniform distribution of materials within the tank, enhancing the quality and consistency of the final product. Mechanical agitators, powered by electric motors, provide robust mixing capabilities for high-viscosity substances. Their design often includes adjustable blades to accommodate different mixing intensities.
For applications requiring gentle mixing, bubble systems offer an alternative. By injecting gas into the tank, these systems create agitation without the need for moving parts. This method minimizes wear and tear, reducing maintenance requirements while preserving the integrity of delicate compounds.
Hybrid systems combine multiple mixing technologies to deliver versatile solutions. For instance, tanks equipped with both mechanical agitators and recirculation pumps can handle a broader range of materials. These systems adapt to varying operational needs, making them indispensable for industries with diverse production requirements.
“The integration of advanced mixing technologies, such as dual-stage powder induction, elevates the performance of chemical blending tanks, ensuring efficiency and precision in industrial processes.”
Selecting the right combination of material construction, tank geometry, and integral mixers ensures that chemical blending tanks meet the specific needs of their intended applications. These features collectively enhance operational efficiency, reduce downtime, and maintain product quality.
Safety and Compliance Standards
Safety and compliance standards play a critical role in the selection and operation of chemical blending tank systems. Adhering to these standards ensures the protection of personnel, the environment, and the integrity of the production process. Manufacturers and operators must prioritize safety features and regulatory compliance to mitigate risks and maintain operational excellence.
Importance of Safety Features
Chemical blending tanks often handle hazardous substances, making safety features essential. Tanks must include mechanisms to prevent leaks, spills, and over-pressurization. For example, pressure relief valves and emergency venting systems safeguard against potential accidents caused by excessive pressure buildup. Additionally, tanks designed with secondary containment systems provide an added layer of protection by containing spills and preventing environmental contamination.
“Safety features such as pressure relief valves and secondary containment systems are indispensable for minimizing risks in chemical processing environments.”
Fire and explosion risks also necessitate the use of flame arrestors and explosion-proof components. These features ensure that tanks can safely operate in environments with flammable or volatile chemicals. Furthermore, advanced mixing technologies, such as the Alfa Laval Hybrid Powder Mixer, enhance safety by maintaining process hygiene and reducing the risk of contamination during powder dispersion and mixing.
Compliance with Industry Standards
Compliance with international and industry-specific standards is non-negotiable for chemical blending tank systems. Regulatory bodies such as OSHA (Occupational Safety and Health Administration), EPA (Environmental Protection Agency), and ISO (International Organization for Standardization) establish guidelines to ensure safe and environmentally responsible operations.
Chemical blending tanks must meet stringent quality and safety certifications. For instance, stainless steel tanks manufactured by companies like Chenma Machinery comply with ISO9001-2005 quality standards, ISO14001-2015 environmental management standards, and OHSAS18001-2007 occupational health standards. These certifications demonstrate a commitment to producing equipment that meets global safety and quality benchmarks.
Key Compliance Considerations
- Material Compatibility: Tanks must be constructed from materials compatible with the chemicals they store or mix. Stainless steel, known for its corrosion resistance, is a preferred choice for industries handling aggressive substances.
- Hygiene Standards: Industries such as food, beverage, and pharmaceuticals require tanks that meet strict sanitary standards. Smooth surfaces and easy-to-clean designs prevent contamination and ensure compliance with hygiene regulations.
- Environmental Protection: Tanks should incorporate features that minimize environmental impact, such as vapor recovery systems and eco-friendly designs. Compliance with EPA guidelines ensures that operations remain sustainable and environmentally responsible.
Benefits of Prioritizing Safety and Compliance
Investing in safety and compliance not only protects workers and the environment but also enhances operational efficiency. Tanks equipped with advanced safety features reduce downtime caused by accidents or equipment failure. Compliance with industry standards fosters trust among stakeholders and ensures uninterrupted operations by avoiding regulatory penalties.
“A commitment to safety and compliance reflects a company’s dedication to operational excellence and environmental stewardship.”
By selecting chemical blending tanks that prioritize safety and adhere to compliance standards, businesses can create a secure and efficient production environment.
Factors to Consider When Choosing a Chemical Blending Tank System
Selecting the right chemical blending tank system requires careful evaluation of several critical factors. These considerations ensure that the chosen system aligns with operational needs, enhances efficiency, and maintains safety standards. Below are the key factors to guide this decision-making process.
Chemical Compatibility
The compatibility of the tank material with the chemicals being processed is paramount. Tanks must resist corrosion and maintain structural integrity when exposed to aggressive substances. Stainless steel stands out as a preferred material due to its exceptional resistance to corrosion and its ability to handle a wide range of chemicals. This durability ensures long-term performance and reduces the risk of contamination.
For industries such as pharmaceuticals and food processing, stainless steel tanks meet stringent hygiene requirements. Their smooth surfaces prevent residue buildup, making cleaning and maintenance easier. Additionally, tanks like Precision Mixing Tanks offer advanced features such as temperature regulation, which is essential for maintaining chemical stability during processing. Selecting a tank with the right material ensures safety, product quality, and compliance with industry standards.
“Chemical compatibility directly impacts the lifespan and efficiency of chemical blending tanks. Choosing the right material safeguards both the equipment and the end product.”
Cost and Budget Constraints
Budget plays a significant role in determining the type of chemical blending tank system. While upfront costs are important, businesses must also consider long-term expenses such as maintenance, energy consumption, and potential downtime. Stainless steel tanks, though initially more expensive, often prove cost-effective over time due to their durability and low maintenance requirements.
For cost-conscious buyers, alternative materials like polypropylene or thermoplastics may offer a viable solution for less demanding applications. However, these materials may lack the robustness of stainless steel, leading to higher replacement costs in the long run. Investing in a high-quality system tailored to specific operational needs minimizes unexpected expenses and ensures a better return on investment.
“Balancing initial costs with long-term benefits helps businesses make financially sound decisions when selecting chemical blending tanks.”
Maintenance and Durability
Maintenance requirements and the durability of the tank system significantly influence operational efficiency. Tanks constructed from durable materials, such as stainless steel, require less frequent repairs and replacements. This reduces downtime and ensures uninterrupted production. Features like reinforced walls in tanks designed for high-shear mixing processes enhance their ability to withstand mechanical stress.
Low-maintenance systems, such as those equipped with bubble mixing technologies, offer additional advantages by minimizing wear and tear. Hybrid systems, which combine multiple mixing methods, often feature fewer moving parts, simplifying maintenance. Businesses should prioritize systems that align with their maintenance capabilities while ensuring long-lasting performance.
“Durable and low-maintenance chemical blending tanks contribute to consistent operations and reduced lifecycle costs.”
By evaluating chemical compatibility, cost considerations, and maintenance requirements, businesses can select chemical blending tank systems that meet their unique needs. These factors collectively ensure safety, efficiency, and cost-effectiveness in chemical processing environments.
Space and Facility Requirements
The physical space and facility layout play a crucial role in determining the suitability of a chemical blending tank system. Proper planning ensures seamless integration into existing operations while optimizing workflow and safety.
Tank Dimensions and Facility Layout
The size and shape of the tank must align with the available space in the facility. Tanks such as Precision Mixing Tanks often come in customizable sizes, allowing businesses to select dimensions that fit their operational footprint. Cylindrical tanks, for instance, maximize vertical space, making them ideal for facilities with height constraints. On the other hand, conical or dished-bottom tanks may require additional floor space but offer superior drainage and cleaning efficiency.
Facility layout also influences tank placement. Operators should position tanks to allow easy access for maintenance, inspection, and cleaning. Adequate clearance around the tank ensures that technicians can perform routine tasks without hindrance. For facilities with limited space, compact systems like Mixing Tanks with integrated features can help minimize the need for additional equipment.
Infrastructure Considerations
The facility’s infrastructure must support the tank system’s operational requirements. For example, tanks equipped with heating or cooling systems, such as Precision Mixing Tanks, require connections to temperature control units. These systems regulate the tank’s internal environment, ensuring optimal conditions for chemical reactions or product consistency. Facilities must also provide sufficient power supply for motorized mixers, pumps, or other auxiliary equipment.
Floor strength is another critical factor. Chemical blending tanks, especially those constructed from stainless steel, can be heavy when filled with liquid. Reinforced flooring prevents structural damage and ensures safe operation. Additionally, facilities handling hazardous chemicals should include secondary containment systems to mitigate risks associated with leaks or spills.
Accessibility and Workflow Optimization
Efficient workflows depend on the strategic placement of tanks within the facility. Tanks should be located near raw material storage areas to reduce transport time and improve productivity. Similarly, proximity to downstream processing equipment minimizes delays and streamlines operations. Facilities with multiple tanks can benefit from centralized control systems, which allow operators to monitor and manage processes from a single location.
Accessibility also extends to safety features. Emergency exits, fire suppression systems, and spill containment measures must remain unobstructed. Tanks designed with user-friendly features, such as easy-to-operate valves or quick-connect fittings, further enhance operational efficiency.
“Optimizing space and facility requirements ensures that chemical blending tanks integrate seamlessly into production environments, enhancing both safety and efficiency.”
Operational Efficiency and Energy Consumption
Operational efficiency and energy consumption directly impact the long-term performance and cost-effectiveness of chemical blending tank systems. Selecting energy-efficient designs and optimizing processes can significantly reduce operational expenses.
Energy-Efficient Mixing Technologies
Modern mixing technologies prioritize energy conservation without compromising performance. Systems like Precision Mixing Tanks incorporate advanced agitators and recirculation pumps that minimize energy usage while maintaining thorough mixing. Bubble mixing systems, for example, consume less energy compared to mechanical mixers, making them suitable for applications requiring gentle agitation.
Hybrid systems combine multiple mixing methods to achieve optimal energy efficiency. By leveraging the strengths of mechanical, bubble, and pump technologies, these systems reduce power consumption while delivering consistent results. Facilities aiming to lower their carbon footprint can benefit from such innovative designs.
Temperature Control and Process Optimization
Temperature regulation plays a vital role in maintaining operational efficiency. Tanks equipped with heating and cooling systems, such as Precision Mixing Tanks, ensure that chemical reactions occur under ideal conditions. Accurate temperature control not only improves product quality but also reduces energy waste by preventing overheating or overcooling.
Process optimization further enhances efficiency. For instance, tanks with integrated recirculation nozzles improve mixing dynamics, reducing the time required to achieve homogeneity. Shorter mixing cycles translate to lower energy consumption and increased throughput.
Automation and Smart Systems
Automation enhances operational efficiency by reducing manual intervention. Smart systems equipped with sensors and programmable logic controllers (PLCs) allow operators to monitor and adjust parameters such as mixing speed, temperature, and flow rate in real time. These systems ensure consistent performance while minimizing energy waste.
Facilities adopting automation can also benefit from predictive maintenance features. By analyzing data from sensors, smart systems identify potential issues before they escalate, reducing downtime and maintenance costs. This proactive approach ensures that tanks operate at peak efficiency throughout their lifecycle.
“Energy-efficient designs and process optimization not only reduce operational costs but also contribute to sustainable and environmentally responsible practices.”
By addressing space constraints and prioritizing energy-efficient technologies, businesses can maximize the performance of their chemical blending tank systems. These considerations ensure that operations remain cost-effective, sustainable, and aligned with industry best practices.
Pros and Cons of Different Chemical Blending Tank Systems
Mechanical Mixing Systems
Mechanical mixing systems utilize motorized agitators to create turbulence within the tank, ensuring thorough blending of materials. These systems excel in applications requiring precise control over mixing intensity and consistency. Industries such as pharmaceuticals, food processing, and specialty chemicals often rely on mechanical systems for their versatility and reliability.
Advantages:
- High Efficiency: Mechanical systems deliver consistent results, even when handling materials with varying viscosities or densities. The active agitation ensures uniform distribution of components.
- Versatility: These systems adapt to different tank geometries, including cylindrical and conical designs, making them suitable for a wide range of applications.
- Customizable Features: Adjustable blades and variable-speed motors allow operators to fine-tune the mixing process based on specific requirements.
Disadvantages:
- Energy Consumption: Mechanical systems often require significant power to operate, which can increase energy costs over time.
- Maintenance Needs: The moving parts, such as agitators and motors, demand regular maintenance to prevent wear and tear.
- Space Requirements: These systems may require larger tanks or additional infrastructure to accommodate the equipment.
“Mechanical mixing systems provide unmatched precision and adaptability, but their operational costs and maintenance demands should be carefully considered.”
Bubble Mixing Systems
Bubble mixing systems use gas injection to create agitation within the tank. Large bubbles rise through the liquid, promoting mixing without the need for mechanical components. This method is particularly effective for low-viscosity liquids or processes requiring gentle handling of materials.
Advantages:
- Energy Efficiency: Bubble systems consume less energy compared to mechanical mixers, making them a cost-effective option for long-term operations.
- Low Maintenance: With fewer moving parts, these systems require minimal upkeep, reducing downtime and maintenance expenses.
- Chemical Compatibility: Bubble systems work well with a variety of chemicals, especially those sensitive to mechanical agitation.
Disadvantages:
- Limited Application: These systems may struggle with high-viscosity materials or processes requiring rapid mixing.
- Lower Mixing Intensity: The gentle agitation may not achieve the same level of uniformity as mechanical or pump systems.
- Infrastructure Requirements: Facilities must have access to compressed air or gas supplies to operate bubble systems effectively.
“Bubble mixing systems offer a low-maintenance and energy-efficient solution, but their limitations in handling complex materials should not be overlooked.”
Pump Mixing Systems
Pump mixing systems rely on strategically placed pumps to circulate liquids within the tank. By directing the flow through nozzles or recirculation loops, these systems achieve uniform mixing without the need for internal agitators.
Advantages:
- Space-Saving Design: The absence of internal mixers allows for more compact tank designs, making these systems ideal for facilities with limited space.
- Flexibility: Operators can adjust flow rates and nozzle configurations to optimize mixing for specific applications.
- Cost-Effectiveness: Pump systems often have lower initial costs compared to mechanical mixers, providing a budget-friendly option for many industries.
Disadvantages:
- Dependence on Pumps: The system’s performance relies heavily on the efficiency and durability of the pumps, which may require regular maintenance.
- Limited Viscosity Range: Pump systems are best suited for low-viscosity liquids and may not perform well with thicker materials.
- Potential for Wear: Continuous circulation can cause wear on the pump components, leading to eventual replacement needs.
“Pump mixing systems combine cost-effectiveness and flexibility, but their reliance on pump performance makes regular maintenance essential.”
Hybrid Systems
Hybrid systems combine multiple mixing technologies to deliver versatile and efficient solutions for chemical blending. These systems integrate the strengths of mechanical, bubble, and pump mixing methods, creating a comprehensive approach to handling diverse chemical properties and operational requirements. Industries with complex blending needs often rely on hybrid systems to achieve optimal results.
Key Advantages of Hybrid Systems
Enhanced Versatility
Hybrid systems adapt to a wide range of applications by leveraging different mixing techniques. For example, they can handle high-viscosity materials while maintaining the integrity of delicate compounds. This adaptability makes them suitable for industries such as pharmaceuticals, food processing, and specialty chemicals.Improved Efficiency
By combining technologies, hybrid systems optimize energy consumption and mixing performance. Mechanical agitators ensure thorough blending, while bubble or pump systems reduce energy usage during less intensive processes. This balance enhances productivity without compromising cost-effectiveness.Customizable Design
Manufacturers can tailor hybrid systems to meet specific operational needs. Features like dual-stage mixing processes or integrated powder induction systems allow precise control over blending parameters. These customizations ensure compatibility with unique production requirements.
“Hybrid systems represent a significant advancement in chemical blending technology, offering unmatched flexibility and efficiency for diverse industrial applications.”
Applications of Hybrid Systems
Chemical Processing
Hybrid systems excel in blending chemicals with varying viscosities or densities. Their ability to combine high-shear mixing with gentle agitation ensures uniformity in complex formulations. For instance, tanks equipped with dual-stage inline powder induction systems facilitate the efficient dispersion of powders into liquid streams.Food and Beverage Industry
Consistency is critical in food and beverage production. Hybrid systems help achieve uniform flavor profiles and textures in products like sauces, beverages, and dairy items. Advanced agitation technologies create the ideal turbulence for even ingredient distribution.Pharmaceuticals
Hybrid systems support the production of homogeneous mixtures in pharmaceutical applications. Their precision ensures compliance with stringent industry standards while maintaining product quality.
Notable Features of Hybrid Systems
Dual-Stage Mixing
Some hybrid systems incorporate dual-stage processes to enhance blending efficiency. This feature proves particularly useful for applications requiring high dry matter concentrations or rapid dispersion of powders.Space Optimization
By integrating multiple mixing technologies into a single system, hybrid setups reduce the need for additional equipment. This design saves valuable floor space, making them ideal for facilities with limited room.Ease of Maintenance
Hybrid systems often feature fewer moving parts compared to standalone mechanical mixers. This simplifies maintenance and reduces downtime, ensuring consistent operations.
Compliance and Safety Considerations
Hybrid systems must adhere to strict safety and compliance standards to ensure safe and efficient operation. Features like secondary containment systems, pressure relief valves, and explosion-proof components enhance safety when handling hazardous chemicals. Compliance with API 650, API 620, and NFPA Standards ensures that these systems meet industry regulations for safe storage and mixing.
“Safety features such as double walls and fire monitors are essential for mitigating risks in chemical processing environments.”
By combining advanced technologies, hybrid systems provide a robust solution for businesses seeking to optimize their blending processes. Their ability to adapt to diverse operational needs makes them an indispensable asset in modern chemical processing industries.
Expert Recommendations for Selecting Chemical Blending Tanks
Consult Industry Professionals
Engaging with industry professionals provides valuable insights when selecting chemical blending tanks. Their expertise helps businesses navigate the complexities of tank systems, ensuring compatibility with specific operational needs. Professionals assess factors such as chemical properties, tank material, and mixing requirements to recommend the most suitable solutions.
For example, experts evaluate the chemical compatibility of tank materials to prevent corrosion and contamination. Stainless steel, known for its durability and resistance to aggressive substances, often emerges as a preferred choice. However, for less demanding applications, professionals may suggest cost-effective alternatives like polypropylene or thermoplastics. Their guidance ensures that the selected tank aligns with both performance expectations and budget constraints.
“Consulting with professionals minimizes risks and ensures that businesses invest in systems tailored to their unique requirements.”
Industry specialists also provide advice on compliance with safety and environmental standards. They help businesses adhere to regulations set by organizations such as OSHA, EPA, and ISO. This ensures that the chosen tanks meet global benchmarks for quality and safety, fostering operational excellence.
Conduct Pilot Testing
Pilot testing serves as a critical step in the decision-making process. It allows businesses to evaluate the performance of a chemical blending tank system under real-world conditions. By conducting small-scale trials, operators can identify potential challenges and make informed adjustments before full-scale implementation.
During pilot testing, businesses assess the tank’s ability to handle specific chemicals and mixing processes. For instance, they examine how well the tank material resists corrosion when exposed to aggressive substances. This step ensures that the tank maintains its structural integrity and prevents contamination. Testing also evaluates the efficiency of mixing technologies, such as mechanical agitators or bubble systems, in achieving uniform blending.
“Pilot testing provides a practical approach to identifying the strengths and limitations of a tank system, reducing the likelihood of costly errors.”
Additionally, pilot testing helps businesses optimize operational parameters. Operators can experiment with variables like mixing speed, temperature, and flow rate to achieve desired outcomes. This process not only enhances efficiency but also ensures that the tank system meets production goals.
Prioritize Safety and Compliance
Safety and compliance should remain top priorities when selecting chemical blending tanks. Tanks often handle hazardous substances, making it essential to incorporate features that mitigate risks and protect personnel. Businesses must ensure that tanks include mechanisms such as pressure relief valves, secondary containment systems, and explosion-proof components.
Compliance with industry standards further enhances safety and operational reliability. Tanks must meet certifications such as ISO9001-2005 for quality, ISO14001-2015 for environmental management, and OHSAS18001-2007 for occupational health. These certifications demonstrate a commitment to producing equipment that adheres to global safety benchmarks.
“Prioritizing safety and compliance safeguards workers, protects the environment, and ensures uninterrupted operations.”
Material selection plays a pivotal role in meeting safety and compliance requirements. Stainless steel, for instance, offers exceptional resistance to corrosion and extreme temperatures, making it ideal for industries handling aggressive chemicals. Its smooth surfaces also facilitate easy cleaning, ensuring compliance with hygiene standards in sectors like food processing and pharmaceuticals.
By consulting professionals, conducting pilot tests, and prioritizing safety, businesses can confidently select chemical blending tanks that align with their operational needs and regulatory obligations. These steps collectively ensure efficiency, reliability, and long-term success.
Leverage Customization Options
Customization plays a pivotal role in ensuring that chemical blending tanks meet the unique demands of various industries. Tailored solutions allow businesses to optimize their operations, enhance efficiency, and address specific challenges. By leveraging customization options, companies can align their tank systems with their production goals and operational environments.
Material Selection for Chemical Compatibility
Choosing the right material for a chemical blending tank is essential for maintaining performance and durability. Different chemicals interact with materials in unique ways, making compatibility a critical factor. For instance, stainless steel offers exceptional resistance to corrosion and extreme temperatures, making it ideal for industries handling aggressive substances like acids or solvents. On the other hand, polypropylene or thermoplastics provide cost-effective alternatives for less demanding applications, such as blending non-corrosive liquids.
“Selecting the appropriate tank material prevents contamination and ensures the structural integrity of the system, safeguarding both the equipment and the end product.”
Manufacturers often provide options to customize the tank material based on the specific chemical properties of the substances being processed. This flexibility ensures that the tank performs optimally while adhering to safety and compliance standards.
Tailored Tank Geometry and Design
Tank geometry significantly impacts the mixing process. Customizing the shape and design of a tank allows businesses to achieve better mixing efficiency and operational convenience. Cylindrical tanks, for example, promote uniform mixing due to their symmetrical design, while conical or dished-bottom tanks enhance drainage and reduce residue accumulation.
Customizable features such as baffles, recirculation nozzles, and dual-stage mixing systems further improve performance. For high-viscosity materials, reinforced walls and advanced agitation systems ensure thorough blending without compromising the tank’s structural integrity. These design modifications cater to specific operational needs, making the tank more effective and versatile.
Integration of Advanced Mixing Technologies
Modern chemical blending tanks often incorporate advanced mixing technologies to enhance functionality. Businesses can customize their tanks with integral mixers, agitators, or hybrid systems to suit their production requirements. For example:
- Mechanical Agitators: Ideal for high-viscosity substances, these provide robust mixing capabilities.
- Bubble Systems: Suitable for gentle agitation, preserving the integrity of delicate compounds.
- Hybrid Systems: Combine multiple mixing methods for maximum versatility and efficiency.
Customizing the mixing technology ensures that the tank delivers consistent results, regardless of the complexity of the blending process.
Adaptation to Facility Constraints
Facility-specific constraints, such as space limitations or infrastructure requirements, often necessitate customized tank designs. Compact tanks with integrated features, such as heating or cooling systems, help businesses maximize their available space. Additionally, tanks designed for easy access and maintenance streamline operations and reduce downtime.
Manufacturers also offer options to customize tank dimensions, ensuring seamless integration into existing workflows. For facilities with height restrictions, vertical tanks provide a space-saving solution, while horizontal tanks may be better suited for areas with limited floor space.
Enhanced Safety Features
Safety remains a top priority in chemical processing environments. Customization allows businesses to incorporate advanced safety features into their tanks, such as pressure relief valves, secondary containment systems, and explosion-proof components. These additions mitigate risks associated with hazardous substances and ensure compliance with industry regulations.
“Custom safety features not only protect personnel and the environment but also enhance the reliability and longevity of the tank system.”
Benefits of Customization
- Operational Efficiency: Tailored tanks streamline processes, reducing energy consumption and production time.
- Cost-Effectiveness: Custom solutions minimize waste and downtime, leading to long-term savings.
- Regulatory Compliance: Customized designs ensure adherence to safety and environmental standards.
- Scalability: Tanks can be designed to accommodate future expansions or changes in production requirements.
By leveraging customization options, businesses can create chemical blending tank systems that align perfectly with their operational needs. This approach not only enhances productivity but also ensures long-term reliability and safety.
Common Mistakes to Avoid When Choosing a System
Overlooking Chemical Compatibility
One of the most critical mistakes businesses make is neglecting to evaluate the chemical compatibility of the tank material with the substances it will store or mix. Each chemical has unique properties that can interact differently with various materials. For instance, stainless steel offers exceptional resistance to corrosion and extreme temperatures, making it ideal for aggressive chemicals like acids or solvents. However, for less demanding applications, materials like polypropylene or thermoplastics may suffice. Choosing an incompatible material can lead to corrosion, contamination, or even structural failure, jeopardizing both safety and operational efficiency.
“Chemical compatibility directly impacts the lifespan and performance of a tank mixing system. Selecting the wrong material can result in costly repairs or replacements.”
Businesses should also consider the long-term effects of chemical exposure. For example, XLPE (cross-linked polyethylene) tanks require less maintenance and have lower life cycle costs compared to linear polyethylene tanks, making them a more durable choice for certain applications. Properly assessing chemical compatibility ensures the tank system remains reliable and safe over time.
Focusing Only on Upfront Costs
Prioritizing initial costs over long-term value often leads to poor decision-making. While budget constraints are important, focusing solely on upfront expenses can result in higher operational costs down the line. For example, stainless steel tanks may cost five times more than other storage solutions initially, but their durability and low maintenance requirements often make them more cost-effective in the long run. Conversely, opting for cheaper materials like plastic or fiberglass might save money upfront but could lead to frequent replacements or repairs.
“Investing in high-quality materials and systems reduces unexpected expenses and ensures better performance over time.”
Additionally, businesses should evaluate the total cost of ownership, including maintenance, energy consumption, and potential downtime. For instance, SAFE-Tank systems can cost up to 90% less than traditional concrete containment structures while offering superior performance and safety. By considering long-term benefits, companies can make financially sound decisions that align with their operational goals.
Neglecting Maintenance Planning
Failing to account for maintenance needs can significantly impact the efficiency and lifespan of a tank mixing system. Tanks constructed from durable materials, such as stainless steel, require less frequent repairs, reducing downtime and ensuring uninterrupted production. However, systems with moving parts, like mechanical mixers, demand regular upkeep to prevent wear and tear. Ignoring these requirements can lead to equipment failure and costly disruptions.
“Proactive maintenance planning ensures consistent operations and extends the life of the tank system.”
Hybrid systems, which combine multiple mixing technologies, often feature fewer moving parts, simplifying maintenance and reducing downtime. Similarly, slope-bottom IMFO tanks require less maintenance compared to cone-bottom tanks, making them a more efficient choice for certain applications. Businesses should prioritize systems that align with their maintenance capabilities while ensuring long-lasting performance.
Incorporating a comprehensive maintenance plan not only minimizes operational risks but also enhances the overall efficiency of the tank system. Regular inspections, timely repairs, and proper cleaning protocols ensure the system operates at peak performance, safeguarding both productivity and safety.
Ignoring Space and Facility Constraints
Overlooking space and facility constraints often leads to inefficiencies and operational challenges. Chemical blending tanks must integrate seamlessly into the available space while meeting production demands. Proper planning ensures that tanks fit within the facility layout and align with infrastructure capabilities.
Tank Dimensions and Layout Optimization
The size and shape of a tank significantly impact its compatibility with the facility. Cylindrical tanks, for instance, maximize vertical space, making them ideal for facilities with height restrictions. Conversely, conical or dished-bottom tanks require more floor space but offer superior drainage and cleaning efficiency. Selecting the appropriate geometry ensures optimal use of the available area.
Facilities with limited space benefit from compact systems. Tanks with integrated features, such as heating or cooling systems, reduce the need for additional equipment. For example, slope-bottom IMFO tanks provide efficient drainage and require less maintenance compared to cone-bottom tanks, making them a practical choice for space-constrained environments.
Infrastructure Compatibility
The facility’s infrastructure must support the tank system’s operational requirements. Tanks equipped with advanced features, such as temperature control units or recirculation pumps, demand adequate power supply and structural reinforcement. Stainless steel tanks, known for their durability, can be heavy when filled. Reinforced flooring prevents structural damage and ensures safe operation.
Secondary containment systems are essential for facilities handling hazardous chemicals. Double-wall tanks, for example, provide an added layer of protection by containing spills and preventing environmental contamination. These systems also accommodate refrigerated liquids, offering insulation space that enhances safety and efficiency.
Workflow and Accessibility
Efficient workflows depend on strategic tank placement. Tanks should be positioned near raw material storage areas to minimize transport time and improve productivity. Proximity to downstream processing equipment further streamlines operations. Centralized control systems allow operators to monitor and manage multiple tanks from a single location, enhancing workflow efficiency.
Accessibility plays a crucial role in maintenance and safety. Tanks must have sufficient clearance for routine inspections, cleaning, and repairs. Features like easy-to-operate valves and quick-connect fittings simplify these tasks. Emergency exits, fire suppression systems, and spill containment measures should remain unobstructed to ensure a safe working environment.
“Optimizing space and facility constraints ensures that chemical blending tanks integrate seamlessly into production environments, enhancing both safety and operational efficiency.”
By addressing space limitations and aligning tank systems with facility requirements, businesses can avoid costly disruptions and maximize productivity. Proper planning creates a harmonious balance between operational needs and spatial constraints, ensuring long-term success.
Future Trends in Chemical Blending Tanks
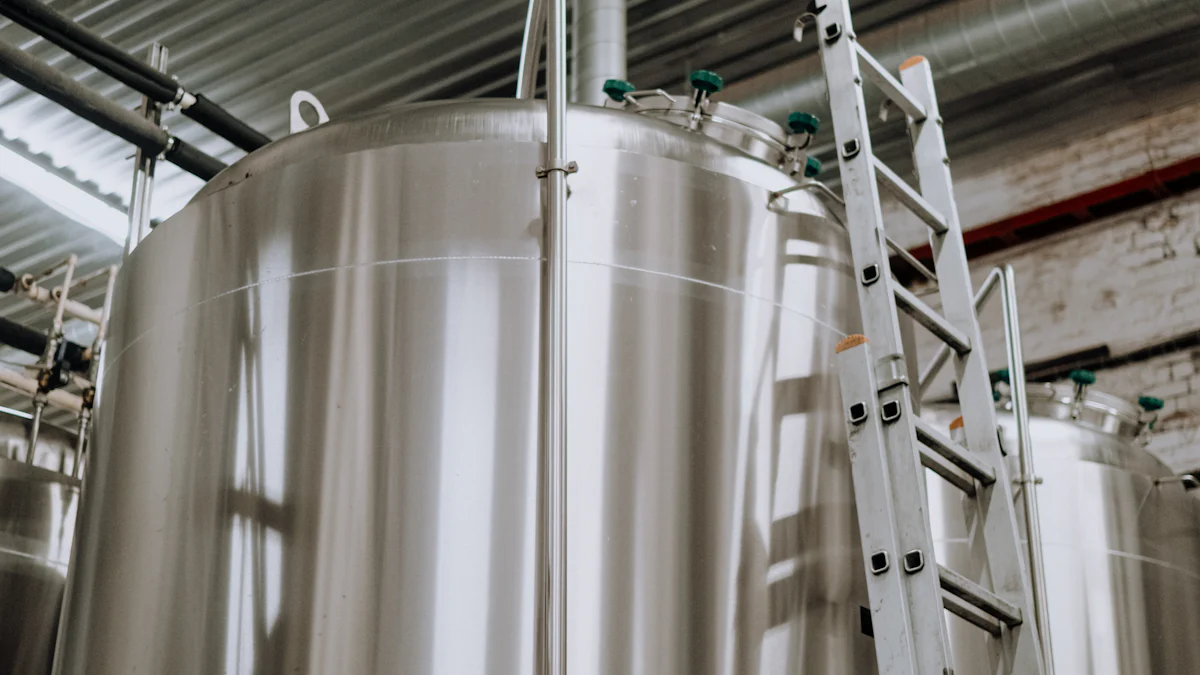
Automation and Smart Systems
Automation is revolutionizing the chemical blending industry by enhancing precision, efficiency, and safety. Modern chemical blending tanks now integrate smart systems equipped with sensors and programmable logic controllers (PLCs). These systems monitor critical parameters such as temperature, pressure, and mixing speed in real time. Operators can adjust these variables remotely, ensuring consistent results and reducing the risk of human error.
Smart systems also enable predictive maintenance. By analyzing data from sensors, these systems identify potential issues before they escalate. For example, they can detect wear in agitators or pumps, allowing timely repairs and minimizing downtime. This proactive approach not only extends the lifespan of the equipment but also ensures uninterrupted operations.
“Automation in chemical blending tanks reduces manual intervention, enhances accuracy, and optimizes energy consumption.”
Additionally, automated tanks often feature advanced mixing technologies. Precision mixing tanks, for instance, utilize sensor-controlled pumps and agitators to achieve thorough blending. These systems ensure even distribution of components, which is crucial for chemical reactions and maintaining product quality in industries like food and beverage production.
Sustainable Materials and Eco-Friendly Designs
Sustainability is becoming a key focus in the design of chemical blending tanks. Manufacturers are increasingly using eco-friendly materials such as recyclable plastics and stainless steel. These materials not only offer durability and chemical resistance but also reduce environmental impact. For example, stainless steel tanks are highly recyclable and have a long service life, making them a sustainable choice for industries handling aggressive chemicals.
Eco-friendly designs also incorporate features that minimize energy consumption. Tanks equipped with insulation reduce heat loss during temperature-controlled processes, enhancing energy efficiency. Some systems include vapor recovery mechanisms to capture and reuse emissions, further reducing their environmental footprint.
“Sustainable chemical blending tanks align with global efforts to reduce waste and promote eco-conscious manufacturing practices.”
In addition to material selection, manufacturers are adopting modular designs. These designs allow for easy upgrades and scalability, reducing the need for complete replacements. Modular systems also simplify maintenance, as individual components can be replaced without disrupting the entire setup.
Advanced Mixing Technologies
The evolution of mixing technologies is shaping the future of chemical blending tanks. Hybrid systems, which combine mechanical, bubble, and pump mixing methods, are gaining popularity for their versatility and efficiency. These systems adapt to a wide range of applications, from blending high-viscosity materials to handling delicate compounds.
Advanced agitation systems are another significant development. Precision mixing tanks now feature dual-stage mixing processes, which enhance blending efficiency. These systems use strategically placed nozzles and recirculation loops to optimize flow patterns, ensuring uniform mixing. For example, large bubble mixing technology employs sequential bursts of compressed air to create agitation, reducing the need for heavy mixer mounts and motors.
“Innovative mixing technologies improve blending efficiency while minimizing energy consumption and maintenance requirements.”
Automation further enhances these technologies. Smart systems adjust mixing parameters based on real-time data, ensuring optimal performance. For instance, tanks with integrated temperature control systems maintain ideal conditions for chemical reactions, improving product consistency and quality.
As industries demand greater efficiency and sustainability, the adoption of advanced mixing technologies will continue to grow. These innovations not only improve operational performance but also align with environmental and economic goals.
Modular and Scalable Systems
Modular and scalable systems have become essential in modern chemical blending tank designs. These systems offer flexibility, efficiency, and adaptability, making them ideal for industries with evolving production needs or space constraints. By incorporating modular components, businesses can expand or modify their operations without significant disruptions or costly overhauls.
Key Features of Modular Systems
Customizable Components
Modular systems allow businesses to tailor tanks with specific features such as pumps, agitators, heating coils, and insulation. For example, tanks equipped with advanced agitation systems ensure thorough blending, which is critical for chemical reactions or achieving consistent product quality in industries like breweries and distilleries. Customization enhances operational efficiency by aligning the tank’s functionality with unique production requirements.Ease of Expansion
Modular designs enable seamless scalability. Businesses can add new components, such as additional storage units or mixing technologies, as production demands increase. This eliminates the need to replace entire systems, saving time and resources. For instance, integrating sensor-controlled pumps or temperature control units into existing tanks enhances performance without requiring a complete redesign.Space Optimization
Modular systems maximize the use of available space. Compact designs with integrated features, such as level sensors and structural elements, reduce the need for additional equipment. Vertical tanks, for example, optimize height in facilities with limited floor space, while horizontal tanks cater to operations requiring easy access and maintenance.
“Modular systems provide a future-proof solution, allowing businesses to adapt to changing demands without compromising efficiency.”
Advantages of Scalable Systems
Cost-Effectiveness
Scalable systems minimize upfront investment by allowing businesses to start with a basic setup and expand as needed. This approach reduces initial costs while ensuring that the system remains adaptable to future growth. For example, adding precision mixing tanks to an existing setup improves blending efficiency without requiring a complete overhaul.Reduced Downtime
Expanding or modifying scalable systems involves minimal disruption to ongoing operations. Modular components can be installed or replaced quickly, ensuring continuous production. This is particularly beneficial for industries with high demand, where downtime can result in significant losses.Environmental Benefits
Scalable systems support sustainable practices by reducing waste. Instead of discarding outdated equipment, businesses can upgrade specific components to meet new requirements. Additionally, features like insulation and vapor recovery mechanisms enhance energy efficiency, aligning with eco-friendly manufacturing goals.
Applications of Modular and Scalable Systems
Chemical Processing
Modular systems excel in handling diverse chemical properties. Tanks with interchangeable components, such as dual-stage mixing systems or recirculation nozzles, adapt to varying viscosities and densities. This versatility ensures consistent performance across different formulations.Food and Beverage Industry
Scalable systems support the production of a wide range of products. For instance, breweries can start with basic mixing tanks and gradually incorporate advanced agitation technologies to achieve precise flavor profiles. Modular designs also simplify cleaning and maintenance, ensuring compliance with hygiene standards.Pharmaceuticals
The pharmaceutical industry benefits from the precision and adaptability of modular systems. Tanks equipped with pressure management devices and safety sensors maintain product integrity while adhering to stringent regulatory requirements. Scalable designs accommodate changes in production volume or formulation needs.
Future Outlook
The demand for modular and scalable systems continues to grow as industries prioritize flexibility and efficiency. Innovations such as smart systems with predictive maintenance capabilities further enhance the appeal of these designs. By integrating automation and advanced mixing technologies, businesses can achieve greater operational control and sustainability.
“Modular and scalable systems represent the future of chemical blending, offering unmatched adaptability and efficiency for dynamic industrial environments.”
These systems empower businesses to stay competitive in a rapidly changing market. Their ability to evolve alongside production needs ensures long-term reliability and cost-effectiveness, making them a valuable investment for any industry.
How Chenma Machinery Can Help
Custom Stainless Steel Tank Solutions
Chenma Machinery specializes in crafting stainless steel tanks tailored to meet the unique needs of various industries. These tanks offer exceptional durability, corrosion resistance, and compatibility with a wide range of chemicals. Stainless steel remains a preferred material for industries such as pharmaceuticals, food processing, and chemical manufacturing due to its ability to withstand extreme temperatures and maintain structural integrity.
Chenma’s engineering team works closely with clients to design tanks that align with specific operational requirements. Whether the need involves high-shear mixing, temperature regulation, or advanced agitation systems, Chenma delivers solutions that enhance efficiency and reliability. For example, tanks designed for high-viscosity materials often feature reinforced walls and precision mixing technologies to ensure uniform blending.
“Custom stainless steel tanks from Chenma Machinery provide businesses with the flexibility to optimize their processes while maintaining compliance with industry standards.”
Additionally, Chenma offers options for integrating advanced features such as dual-stage mixing systems, recirculation nozzles, and secondary containment mechanisms. These customizations not only improve performance but also ensure safety and environmental protection. By leveraging Chenma’s expertise, businesses can achieve long-term reliability and cost-effectiveness in their operations.
Turnkey System Design and Installation
Chenma Machinery provides comprehensive turnkey solutions, simplifying the process of implementing chemical blending systems. From initial process design to final installation, Chenma manages every aspect of the project. This approach ensures seamless integration of equipment into existing workflows, minimizing disruptions and maximizing productivity.
The turnkey services include:
- Process Design: Chenma’s experts analyze operational needs to develop efficient and sustainable system designs. This includes selecting the appropriate tank geometry, mixing technology, and auxiliary components.
- Equipment Manufacturing: Utilizing state-of-the-art machinery, Chenma produces high-quality tanks and processing equipment. The production facility spans 20,000 m² and employs over 200 skilled professionals, ensuring precision and consistency in every product.
- Installation and Commissioning: Chenma’s team handles on-site installation, ensuring that all components function optimally. They also provide technical training to operators, enabling smooth transitions and efficient system operation.
“Turnkey solutions from Chenma Machinery eliminate the complexities of system implementation, allowing businesses to focus on their core operations.”
These services cater to diverse industries, including food and beverage, pharmaceuticals, and specialty chemicals. By offering end-to-end support, Chenma ensures that clients receive fully operational systems tailored to their specific needs.
Compliance with International Standards
Chenma Machinery prioritizes safety and quality by adhering to stringent international standards. The company has achieved certifications such as ISO9001-2005 for quality management, ISO14001-2015 for environmental management, and OHSAS18001-2007 for occupational health and safety. These certifications demonstrate Chenma’s commitment to producing equipment that meets global benchmarks.
Stainless steel tanks from Chenma comply with industry-specific regulations, ensuring compatibility with hazardous substances and maintaining hygiene in sensitive applications. For example, tanks designed for the food and beverage industry feature smooth surfaces that prevent residue buildup, facilitating easy cleaning and compliance with sanitary standards.
“Chenma Machinery’s adherence to international standards reflects its dedication to delivering safe, reliable, and environmentally responsible solutions.”
In addition to meeting regulatory requirements, Chenma incorporates sustainable practices into its manufacturing processes. The use of recyclable materials and energy-efficient designs aligns with global efforts to reduce waste and minimize environmental impact. By choosing Chenma, businesses can enhance their operational efficiency while contributing to sustainability goals.
Chenma Machinery’s expertise in custom tank solutions, turnkey system implementation, and compliance with international standards positions it as a trusted partner for industries seeking reliable and innovative chemical blending systems.
Expertise in Diverse Industries
Chenma Machinery demonstrates unparalleled expertise across a wide range of industries, offering tailored solutions that address unique operational challenges. The company’s ability to adapt its chemical blending tank systems to meet the specific needs of diverse sectors highlights its commitment to innovation and customer satisfaction.
Chemical Processing
In the chemical processing industry, precision and safety are paramount. Chenma Machinery designs tanks that handle aggressive substances with ease, ensuring chemical compatibility and structural integrity. Stainless steel tanks, known for their corrosion resistance, play a vital role in maintaining product quality and operational efficiency. Advanced features, such as dual-stage mixing systems and recirculation nozzles, enhance blending performance, even for complex formulations.
“Our ‘Hybrid Unit’ Mixing Plant allows customers to maximize chemical performance while reducing equipment costs. This innovative approach surpasses traditional methods, offering unmatched efficiency and cost-effectiveness.”
Chenma’s expertise extends to integrating safety mechanisms, such as pressure relief valves and secondary containment systems, which protect both personnel and the environment. These features ensure compliance with stringent industry regulations, fostering trust and reliability.
Food and Beverage Industry
The food and beverage sector demands strict adherence to hygiene and quality standards. Chenma Machinery excels in crafting tanks with smooth, easy-to-clean surfaces that prevent residue buildup and contamination. These tanks meet the rigorous sanitary requirements essential for producing beverages, sauces, and other consumables.
Customizable designs, such as cylindrical tanks for uniform mixing or conical tanks for efficient drainage, cater to the specific needs of food manufacturers. Advanced agitation systems ensure consistent flavor profiles and textures, enhancing product quality. By incorporating temperature control units, Chenma enables precise regulation of conditions, critical for processes like fermentation or pasteurization.
Pharmaceuticals
Pharmaceutical production requires precision and compliance with stringent regulatory standards. Chenma Machinery provides tanks equipped with advanced mixing technologies, ensuring homogeneous mixtures and consistent product quality. Features like pressure management devices and explosion-proof components enhance safety when handling volatile substances.
Chenma’s stainless steel tanks meet international certifications, such as ISO9001-2005 and OHSAS18001-2007, ensuring compatibility with pharmaceutical-grade materials. These tanks also support clean-in-place (CIP) systems, streamlining maintenance and minimizing downtime.
Construction and Mining
In construction and mining, reliable fuel and chemical storage solutions are essential. Chenma designs tanks that withstand harsh environments while maintaining operational efficiency. Durable materials and robust construction ensure longevity, even under extreme conditions. These tanks provide a dependable supply of chemicals or fuels, reducing downtime and enhancing productivity.
“The advantages of employing construction fuel tanks extend beyond functionality, encompassing cost savings, heightened efficiency, and a reliable fuel supply—particularly valuable in sectors like construction and mining.”
Sustainability-Focused Industries
As environmental concerns grow, industries increasingly prioritize sustainable practices. Chenma Machinery supports these efforts by offering eco-friendly tank designs. Features like insulation reduce energy consumption, while vapor recovery systems minimize emissions. Modular and scalable systems allow businesses to expand operations without unnecessary waste, aligning with global sustainability goals.
“With sustainable optimization, businesses can achieve up to 80% energy savings and 90% water savings, while minimizing waste. Good for people. Good for the planet. Good for profitability.”
Chenma’s expertise in diverse industries underscores its ability to deliver innovative, reliable, and sustainable solutions. By addressing the unique demands of each sector, the company ensures that its chemical blending tanks remain indispensable assets for businesses worldwide.
Selecting the right chemical blending tanks requires a thorough understanding of system types, their advantages, and limitations. Businesses must evaluate critical factors such as chemical compatibility, cost, maintenance needs, and spatial constraints to ensure optimal performance. Consulting industry professionals and conducting pilot testing can provide valuable insights, reducing risks and enhancing decision-making. Customization options further allow businesses to align tank systems with specific operational needs. Begin by assessing your requirements and partner with trusted manufacturers like Chenma Machinery to implement tailored solutions that prioritize safety, efficiency, and compliance.
FAQ
What are the main types of chemical blending tank systems?
Chemical blending tank systems primarily include mechanical mixing systems, bubble mixing systems, pump mixing systems, and hybrid systems. Each type serves specific purposes:
- Mechanical Mixing Systems: Use motorized agitators for consistent mixing, ideal for high-viscosity materials.
- Bubble Mixing Systems: Employ gas injection for gentle agitation, suitable for low-viscosity liquids.
- Pump Mixing Systems: Circulate liquids through nozzles, ensuring uniform mixing without internal agitators.
- Hybrid Systems: Combine multiple technologies to handle diverse chemical properties and operational needs.
These systems cater to various industries, including pharmaceuticals, food processing, and specialty chemicals.
How do I determine the right material for my chemical blending tank?
The choice of material depends on the chemical properties of the substances being processed. Stainless steel is a popular option due to its corrosion resistance and durability, making it suitable for aggressive chemicals like acids or solvents. For less demanding applications, polypropylene or thermoplastics may suffice.
“Some ways we adapt the tank to suit a chemical include using a heavier polymer shot weight and wall thickness for higher gravity chemicals,” explains Tuffa, an expert in chemical storage tanks. Ensuring compatibility with seals, pipework, and third-party equipment is also critical.
Selecting the correct material ensures safety, longevity, and compliance with industry standards.
What factors should I consider when choosing a tank system?
When selecting a chemical blending tank system, consider the following:
- Chemical Compatibility: Ensure the tank material resists corrosion and maintains integrity.
- Operational Needs: Assess mixing requirements, such as viscosity and flow rates.
- Space Constraints: Choose a design that fits your facility layout.
- Safety Standards: Prioritize tanks with features like pressure relief valves and secondary containment.
- Budget: Balance upfront costs with long-term maintenance and operational efficiency.
These factors collectively ensure the system aligns with your production goals.
Can chemical blending tanks be customized?
Yes, chemical blending tanks can be tailored to meet specific operational needs. Customization options include:
- Material Selection: Adapted for chemical compatibility.
- Tank Geometry: Cylindrical, conical, or dished-bottom designs for optimal mixing and drainage.
- Advanced Features: Integration of dual-stage mixing systems, temperature control units, or recirculation nozzles.
“The ability to modify the tank to suit a huge variety of applications is one of the greater benefits of chemical tanks,” notes Tuffa. This flexibility ensures compatibility with complex processes like neutralizing, diluting, and mixing.
Customization enhances efficiency and ensures the tank meets unique production requirements.
How do hybrid systems improve chemical blending?
Hybrid systems combine the strengths of mechanical, bubble, and pump mixing technologies. This integration offers:
- Versatility: Handles both high-viscosity materials and delicate compounds.
- Efficiency: Reduces energy consumption while maintaining thorough mixing.
- Customizability: Adapts to specific operational needs with advanced features.
Industries like pharmaceuticals and food processing benefit from the precision and adaptability of hybrid systems, making them a preferred choice for complex blending tasks.
What safety features should chemical blending tanks include?
Safety features are essential for handling hazardous substances. Key components include:
- Pressure Relief Valves: Prevent over-pressurization.
- Secondary Containment Systems: Contain spills and protect the environment.
- Explosion-Proof Components: Ensure safe operation with volatile chemicals.
“Ensuring all seals, pipework, hoses, and outlets are compatible is critical for safety,” emphasizes Tuffa. These measures safeguard personnel and maintain compliance with industry regulations.
Prioritizing safety features minimizes risks and enhances operational reliability.
How does automation benefit chemical blending tanks?
Automation improves precision, efficiency, and safety in chemical blending. Features include:
- Real-Time Monitoring: Sensors track parameters like temperature and mixing speed.
- Predictive Maintenance: Identifies potential issues before they escalate.
- Remote Control: Allows operators to adjust settings from a centralized system.
Automated tanks reduce manual intervention, optimize energy consumption, and ensure consistent results, making them indispensable for modern industries.
What are the advantages of modular and scalable tank systems?
Modular and scalable systems offer flexibility and efficiency. Benefits include:
- Customizable Components: Tailored features like pumps and agitators.
- Ease of Expansion: Add new components as production demands grow.
- Space Optimization: Compact designs maximize facility space.
These systems adapt to evolving operational needs, ensuring long-term reliability and cost-effectiveness.
How can Chenma Machinery assist with chemical blending tanks?
Chenma Machinery provides comprehensive solutions, including:
- Custom Stainless Steel Tanks: Designed for durability and chemical compatibility.
- Turnkey System Design: From process design to installation, ensuring seamless integration.
- Compliance with Standards: Adheres to ISO9001-2005, ISO14001-2015, and OHSAS18001-2007 certifications.
Chenma’s expertise spans diverse industries, offering tailored solutions that prioritize safety, efficiency, and sustainability.
Why is pilot testing important before full-scale implementation?
Pilot testing evaluates the performance of a chemical blending tank system under real-world conditions. It helps:
- Identify potential challenges.
- Optimize operational parameters like mixing speed and temperature.
- Ensure compatibility with specific chemicals and processes.
“Pilot testing provides a practical approach to identifying the strengths and limitations of a tank system,” ensuring informed decision-making and reducing costly errors.
This step ensures the chosen system aligns with production goals and operational needs.