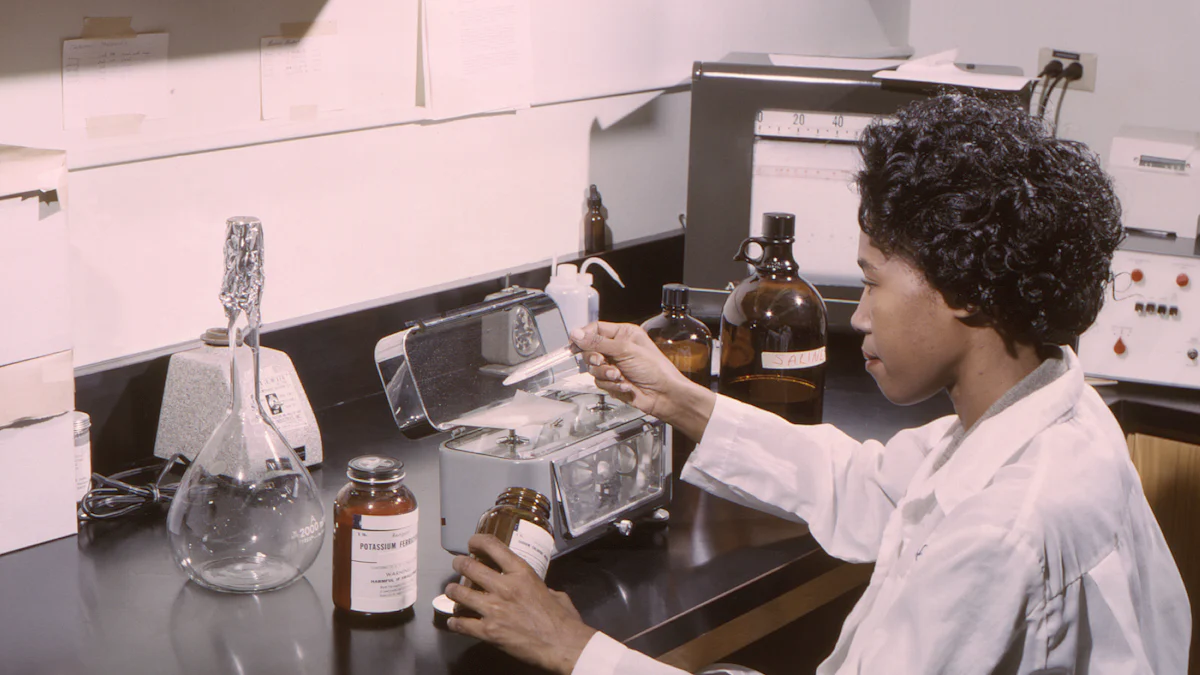
Selecting the right chemical mixers plays a pivotal role in optimizing industrial processes. These devices ensure efficiency, enhance safety, and reduce operational costs. The global chemical mixer market, valued at approximately USD 3.5 billion in 2023, is projected to grow at a CAGR of about 7%, reaching USD 6.2 billion by 2032. This growth reflects the rising demand for high-performance chemical mixers that improve production outcomes. Technological advancements and innovations in manufacturing have further propelled this market, offering solutions tailored to diverse industries. A well-chosen chemical mixer aligns with specific material properties, ensuring seamless operations and long-term value.
Overview of Chemical Mixers
What Are Chemical Mixers?
Definition and purpose of chemical mixers.
Chemical mixers are specialized machines designed to blend, combine, or homogenize various materials. These devices play a critical role in ensuring uniformity and consistency in chemical processes. By facilitating precise mixing, they help achieve desired chemical reactions, improve product quality, and enhance production efficiency. Their purpose extends beyond simple blending; they also enable the dispersion of solids, emulsification of liquids, and even gas incorporation into mixtures. This versatility makes them indispensable in modern manufacturing and industrial operations.
Key components and how they work.
Chemical mixers consist of several essential components that work together to achieve optimal mixing. The primary elements include:
- Mixing blades or impellers: These are responsible for creating motion within the material, ensuring thorough blending. Different blade designs cater to specific applications, such as high-shear mixing or gentle agitation.
- Mixing tanks: These vessels hold the materials being mixed. Tanks vary in size, shape, and material, depending on the type of chemical process and volume requirements.
- Drive systems: Motors and gearboxes power the mixing blades, providing the necessary speed and torque for effective operation.
- Control systems: Advanced mixers often feature programmable controls, allowing operators to adjust speed, pressure, and mixing time for precise results.
The working principle involves the rotation of blades or impellers within the tank, creating turbulence and shear forces. These forces break down particles, disperse materials, and ensure uniform distribution. The design and configuration of the mixer depend on the properties of the materials being processed, such as viscosity, density, and chemical reactivity.
Common Applications of Chemical Mixers
Industries served (e.g., pharmaceuticals, food processing, chemicals, cosmetics).
Chemical mixers find applications across a wide range of industries due to their adaptability and efficiency. Key sectors that rely on these machines include:
- Pharmaceuticals: Mixers ensure the uniform blending of active ingredients, excipients, and other components in drug formulations. They are essential for producing tablets, syrups, and ointments.
- Food processing: In this industry, mixers are used to create consistent textures and flavors in products like sauces, dressings, and baked goods.
- Chemical manufacturing: Mixers play a pivotal role in producing fine chemicals, adhesives, and coatings. They handle complex processes involving liquids, solids, and gases.
- Cosmetics: These machines help achieve the desired consistency and stability in products such as creams, lotions, and shampoos.
Typical use cases (e.g., blending, emulsifying, homogenizing).
Chemical mixers support a variety of processes tailored to specific industrial needs. Common use cases include:
- Blending: Combining multiple ingredients to create a homogeneous mixture. This is crucial in industries like food processing and pharmaceuticals.
- Emulsifying: Mixing immiscible liquids, such as oil and water, to form stable emulsions. This process is widely used in cosmetics and chemical manufacturing.
- Homogenizing: Reducing particle size and ensuring uniform distribution throughout the mixture. Homogenization is vital in producing high-quality products in the pharmaceutical and food industries.
- Gas dispersion: Incorporating gases into liquids for applications like aeration or carbonation in beverages.
- Solid suspension: Keeping solid particles evenly distributed in a liquid medium, often required in wastewater treatment and chemical production.
These applications highlight the versatility and importance of chemical mixers in achieving precise and efficient processing across diverse industries.
Types of Chemical Mixers and Their Features
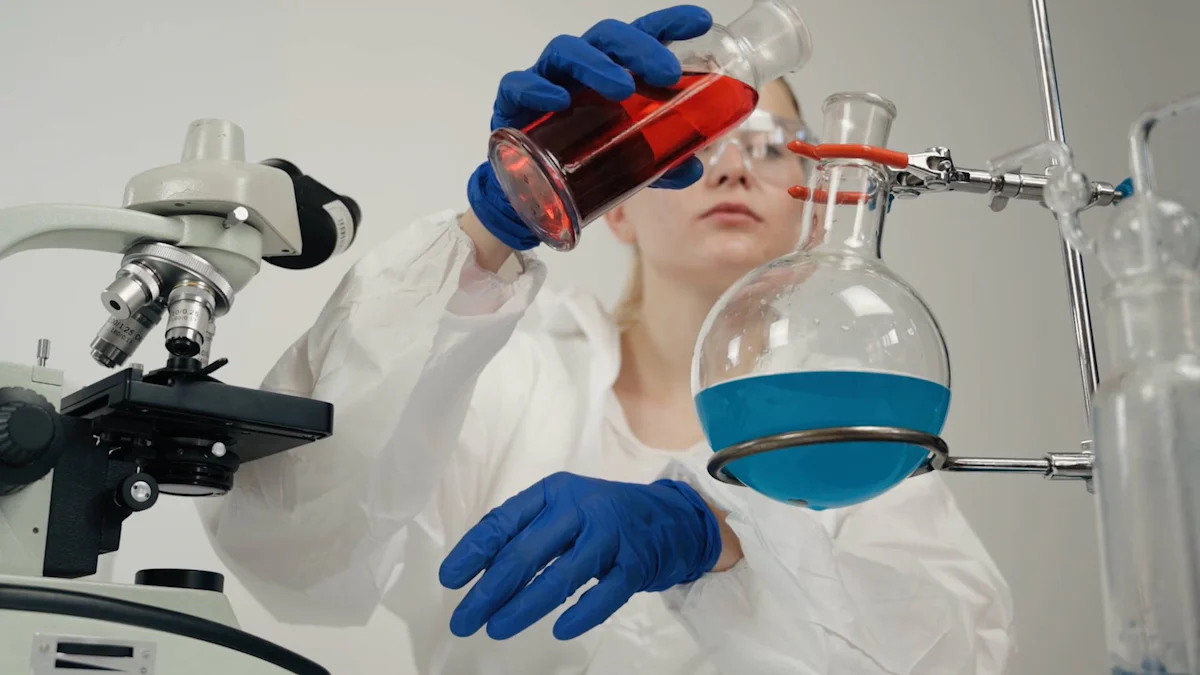
Vertical Agitation Mixers
Features (e.g., high-speed mixing, adjustable blades).
Vertical agitation mixers are designed to handle a wide range of mixing tasks with precision and efficiency. These mixers feature high-speed mixing capabilities, which ensure rapid blending of materials, even those with varying viscosities. Adjustable blades allow operators to customize the mixing process based on specific requirements, such as achieving uniform consistency or breaking down solid particles. The vertical design optimizes space utilization, making these mixers suitable for facilities with limited floor space. Additionally, advanced models often include programmable controls, enabling precise adjustments to speed and mixing duration.
Benefits and ideal applications.
Vertical agitation mixers excel in applications requiring thorough blending and homogenization. Their high-speed operation makes them ideal for industries such as pharmaceuticals, where uniform distribution of active ingredients is critical. In the food processing sector, these mixers ensure consistent textures in products like sauces and dressings. The adjustable blades enhance versatility, allowing the equipment to handle both delicate emulsions and robust chemical reactions. These mixers are also widely used in chemical manufacturing for processes like pH regulation and solid suspension, ensuring consistent quality in the final product.
Side-Mounted Mixers
Features (e.g., space-saving design, easy maintenance).
Side-mounted mixers offer a compact and efficient solution for mixing tasks. Their space-saving design allows them to be installed on the side of tanks or vessels, freeing up valuable floor space in industrial facilities. These mixers are engineered for easy maintenance, with components that can be accessed and serviced without dismantling the entire unit. Many models include features such as variable speed drives, which provide flexibility in adjusting the mixing intensity. The robust construction ensures durability, even in demanding environments.
Benefits and ideal applications.
Side-mounted mixers are particularly beneficial in industries where space constraints are a concern. They are commonly used in wastewater treatment plants for processes like flocculation and sludge production. In the chemical industry, these mixers facilitate efficient blending of raw materials and ensure uniform distribution of ingredients. Their ease of maintenance reduces downtime, making them a cost-effective choice for continuous operations. These mixers are also suitable for applications involving temperature regulation and gas dispersion, where precise control is essential.
Emulsifiers
Features (e.g., high shear force, fine particle dispersion).
Emulsifiers are specialized mixing devices designed to create stable emulsions by combining immiscible liquids, such as oil and water. These mixers generate high shear force, which breaks down particles into fine sizes and ensures even dispersion throughout the mixture. The advanced design of emulsifiers includes features like rotor-stator systems, which enhance the efficiency of the emulsification process. Many models also offer adjustable settings, allowing operators to control the shear intensity based on the specific application.
Benefits and ideal applications.
Emulsifiers are indispensable in industries requiring precise and stable emulsions. In the cosmetics sector, they produce smooth and consistent creams, lotions, and gels. The pharmaceutical industry relies on emulsifiers for creating suspensions and emulsions used in drug formulations. These mixers are also widely used in food processing to produce products like mayonnaise and salad dressings. Their ability to achieve fine particle dispersion makes them ideal for applications involving homogenization and viscosity control, ensuring high-quality results in every batch.
Industrial Blenders
Features (e.g., large capacity, robust construction).
Industrial blenders are engineered to handle high-volume mixing tasks with precision and reliability. These machines boast large capacity tanks, making them ideal for processing substantial quantities of materials in a single batch. Their robust construction, often crafted from stainless steel, ensures durability and resistance to corrosion, even when exposed to harsh chemicals or abrasive substances. Many models incorporate advanced drive systems that deliver consistent torque, enabling efficient blending of materials with varying viscosities. Additionally, industrial blenders often feature programmable controls, allowing operators to fine-tune speed, mixing duration, and other parameters for optimal results.
Some models also include high-shear mixing capabilities, which enhance their ability to disperse solids, emulsify liquids, and homogenize mixtures. This versatility makes them suitable for a wide range of applications. The inclusion of easy-to-clean designs further simplifies maintenance, reducing downtime and ensuring compliance with stringent hygiene standards in industries like food processing and pharmaceuticals.
Benefits and ideal applications.
Industrial blenders provide significant advantages in industries requiring consistent and efficient mixing of large quantities. Their high capacity reduces the need for multiple batches, saving time and labor costs. The robust design ensures longevity, even under demanding conditions, making them a cost-effective investment for long-term use. These machines excel in blending raw materials, facilitating chemical reactions, and ensuring uniform distribution of ingredients, which is critical for maintaining product quality.
Ideal applications include:
- Chemical manufacturing: Industrial blenders play a pivotal role in producing adhesives, coatings, and fine chemicals. They ensure uniformity and consistency in the final product.
- Food and beverage processing: These machines handle tasks like mixing dough, blending sauces, and creating emulsions for dressings and condiments.
- Pharmaceuticals: Industrial blenders ensure the even distribution of active ingredients in formulations, enhancing the efficacy and safety of medications.
- Cosmetics: They produce smooth and stable products such as creams, gels, and lotions by achieving precise mixing and emulsification.
The versatility and efficiency of industrial blenders make them indispensable in modern manufacturing processes.
Laboratory Mixers
Features (e.g., compact design, precision mixing).
Laboratory mixers are designed for small-scale mixing tasks that demand high precision. Their compact design allows them to fit seamlessly into laboratory environments with limited space. These mixers often feature variable speed controls, enabling operators to adjust the mixing intensity based on the specific requirements of the experiment or process. Many models include interchangeable mixing heads, which provide flexibility for handling a variety of materials, from low-viscosity liquids to high-viscosity gels.
Precision is a hallmark of laboratory mixers. Advanced models incorporate digital displays and programmable settings, ensuring accurate replication of mixing conditions. The use of durable materials, such as stainless steel or chemically resistant plastics, enhances their longevity and compatibility with a wide range of substances. Additionally, laboratory mixers are typically lightweight and portable, making them easy to move and operate.
Benefits and ideal applications.
Laboratory mixers offer unparalleled precision and control, making them essential tools for research and development. Their compact size and adaptability allow scientists and technicians to perform a wide range of mixing tasks without occupying excessive workspace. The ability to fine-tune mixing parameters ensures reproducibility, which is critical for experimental accuracy.
Ideal applications include:
- Pharmaceutical research: Laboratory mixers facilitate the development of new drug formulations by ensuring uniform blending of active ingredients and excipients.
- Chemical testing: These mixers support small-scale chemical reactions and material testing, providing insights into process feasibility and optimization.
- Food science: Laboratory mixers help create prototypes of new food products, enabling researchers to test textures, flavors, and stability.
- Cosmetic formulation: They assist in developing innovative cosmetic products, such as serums and emulsions, by achieving precise mixing and particle dispersion.
Laboratory mixers bridge the gap between experimentation and production, offering the precision and flexibility needed for innovation.
Cost Analysis of Chemical Mixers
Understanding the cost structure of chemical mixers is essential for making informed purchasing decisions. Prices vary significantly based on several factors, including material quality, capacity, and advanced features. This section provides a detailed analysis of these factors and typical price ranges for different types of mixers.
Factors Influencing Mixer Prices
Material and build quality.
The material and build quality of a mixer directly impact its price. High-quality materials, such as stainless steel, enhance durability and resistance to corrosion, especially in industrial environments. Mixers designed for handling hazardous chemicals or abrasive substances often require specialized coatings or reinforced components, which increase costs. Manufacturers prioritize robust construction to ensure long-term reliability, particularly for heavy-duty applications.
Size and capacity.
The size and capacity of a mixer significantly affect its pricing. Larger mixers, capable of processing substantial volumes, command higher prices due to the increased material and engineering requirements. For example, industrial mixers designed for large-scale production often feature expansive tanks and powerful motors, making them suitable for high-volume operations. Conversely, smaller mixers, such as laboratory models, cater to precise, small-scale tasks and are typically more affordable.
Advanced features (e.g., automation, programmability).
Advanced features elevate the functionality and efficiency of chemical mixers but also contribute to higher costs. Automation capabilities, such as programmable controls and variable speed settings, allow operators to achieve precise mixing conditions. These features enhance productivity and reduce manual intervention, making them valuable for industries requiring consistent results. High-shear mixers, known for their intensive mixing capabilities, often include such advanced technologies, justifying their premium pricing.
Typical Price Ranges by Mixer Type
Vertical agitation mixers: $930–$6,000.
Vertical agitation mixers offer versatility and efficiency, making them a popular choice across industries. Their price range reflects variations in capacity, blade design, and additional features. Entry-level models cater to basic mixing needs, while high-end options include programmable settings and adjustable blades for specialized applications.
Side-mounted mixers: $275–$1,900.
Side-mounted mixers provide a cost-effective solution for facilities with limited space. Their compact design and ease of maintenance make them an economical choice for industries like wastewater treatment and chemical manufacturing. Prices vary based on motor power, tank compatibility, and additional features like variable speed drives.
Emulsifiers: $1,420–$48,000.
Emulsifiers, designed for creating stable emulsions, exhibit a broad price range due to their specialized nature. Basic models handle standard emulsification tasks, while high-end versions, equipped with rotor-stator systems and adjustable shear intensity, cater to demanding applications in cosmetics and pharmaceuticals.
Industrial blenders: $2,500–$35,000.
Industrial blenders, known for their large capacity and robust construction, fall within a wide price spectrum. Lower-priced models suit general-purpose mixing, while premium options, featuring advanced drive systems and high-shear capabilities, address complex industrial processes. These machines excel in blending viscous fluids, powders, and other challenging materials.
Laboratory mixers: $13.99–$393.59.
Laboratory mixers represent the most affordable category, designed for precision and small-scale tasks. Their compact size and interchangeable mixing heads make them ideal for research and development. Prices depend on features like digital displays, variable speed controls, and material compatibility.
Pro Tip: When evaluating chemical mixers, consider the total cost of ownership, including maintenance, energy consumption, and potential downtime. A higher upfront investment in durable and feature-rich equipment often translates to long-term savings.
By analyzing these factors and price ranges, buyers can identify the most cost-effective solution tailored to their specific needs. Whether prioritizing advanced features or seeking a competitive price, understanding the market landscape ensures a well-informed decision.
Comparing Chemical Mixers: Features vs. Cost
Key Features to Consider
Mixing speed and efficiency
Mixing speed directly impacts the efficiency of chemical mixers. High-speed mixers, such as vertical agitation mixers, excel in blending materials with varying viscosities. They ensure uniform distribution and reduce processing time. However, slower mixers may suit applications requiring gentle agitation to preserve material integrity. Efficiency also depends on impeller power and torque, which vary across mixer types. For instance, industrial blenders often require significant energy input to handle large volumes effectively. Selecting a mixer with the right speed and power ensures optimal outcomes for specific processes.
Durability and maintenance requirements
Durability plays a critical role in determining the long-term value of chemical mixers. Machines constructed from high-quality materials, such as stainless steel, resist corrosion and withstand harsh chemicals. This durability reduces the frequency of repairs and replacements. Maintenance requirements also influence operational costs. Side-mounted mixers, for example, feature accessible components that simplify servicing. Choosing a mixer with robust construction and minimal maintenance needs ensures consistent performance and lowers downtime.
Compatibility with specific materials or chemicals
The compatibility of a mixer with the materials it processes is essential for achieving desired results. Different mixers cater to specific applications based on material properties like viscosity, density, and chemical reactivity. Emulsifiers, for instance, specialize in creating stable emulsions by combining immiscible liquids. Laboratory mixers, on the other hand, handle small-scale tasks requiring precision. Understanding the chemical and physical characteristics of the materials ensures the selected mixer aligns with production goals.
Creating a Cost-Effectiveness Matrix
Balancing upfront cost with long-term value
Evaluating the total cost of ownership helps balance upfront expenses with long-term benefits. While budget-friendly options like laboratory mixers may suit small-scale operations, investing in durable and feature-rich equipment often yields greater value over time. For example, industrial blenders with advanced drive systems may have higher initial costs but offer efficiency and reliability for large-scale production. Factoring in energy consumption, maintenance, and potential downtime ensures a comprehensive cost analysis.
Pro Tip: Prioritize mixers with programmable controls and automation features to enhance productivity and reduce manual intervention.
Prioritizing features based on application needs
Identifying essential features ensures the mixer meets specific application requirements. For instance, high-shear mixers excel in processes demanding fine particle dispersion, while side-mounted mixers suit facilities with limited space. Creating a matrix that ranks features by importance helps streamline decision-making. Consider factors like mixing speed, capacity, and cleaning requirements. This approach ensures the selected mixer delivers both performance and a competitive price.
Example Models and Recommendations
Popular Models in Each Category
Vertical agitation mixers: Intsupermai 100L Liquid Mixer Machine Agitator
The Intsupermai 100L Liquid Mixer Machine Agitator stands out as a reliable choice for vertical agitation mixing. This model features a robust design with adjustable blades, allowing users to customize the mixing process for various viscosities. Its high-speed motor ensures efficient blending, making it suitable for industries like food processing and pharmaceuticals. The 100-liter capacity provides ample space for medium-scale operations, while its stainless steel construction enhances durability and resistance to corrosion. This mixer is ideal for achieving uniform consistency in emulsions, suspensions, and other complex mixtures.
Side-mounted mixers: FlowServe IBC Mixer
The FlowServe IBC Mixer offers a compact and efficient solution for side-mounted mixing needs. Designed for intermediate bulk containers (IBCs), this mixer excels in blending liquids and maintaining homogeneity in storage tanks. Its space-saving design makes it a practical choice for facilities with limited floor space. The FlowServe IBC Mixer includes variable speed settings, enabling precise control over mixing intensity. Industries such as wastewater treatment and chemical manufacturing benefit from its ease of maintenance and reliable performance. This model ensures consistent results while minimizing operational downtime.
Emulsifiers: Ultrasonic Chemical Mixing Machine from Sharpertek USA
The Ultrasonic Chemical Mixing Machine by Sharpertek USA represents a high-end option for emulsification tasks. This emulsifier employs advanced ultrasonic technology to generate high shear forces, ensuring fine particle dispersion and stable emulsions. Its rotor-stator system enhances efficiency, making it suitable for demanding applications in cosmetics and pharmaceuticals. With programmable settings, operators can adjust shear intensity to meet specific requirements. This machine excels in producing high-quality emulsions for products like creams, lotions, and suspensions. Its premium price reflects its specialized capabilities and cutting-edge design.
Industrial blenders: IS-199 Chemical Mixer from Newco Inc.
The IS-199 Chemical Mixer from Newco Inc. is a versatile industrial blender designed for large-scale mixing tasks. Its robust construction and large capacity make it suitable for handling substantial volumes of materials. This model features advanced drive systems that deliver consistent torque, ensuring efficient blending of viscous fluids and powders. The IS-199 excels in industries like chemical manufacturing, where uniformity and precision are critical. Its stainless steel build enhances durability, while its user-friendly controls simplify operation. This industrial mixer provides a cost-effective solution for high-volume production needs.
Laboratory mixers: Dayton 32V142 Laboratory Drum Mixer
The Dayton 32V142 Laboratory Drum Mixer is a compact and precise tool for small-scale mixing tasks. Its lightweight design and portability make it an excellent choice for laboratory environments. This mixer includes variable speed controls, allowing operators to fine-tune the mixing process for different materials. The Dayton 32V142 is compatible with a wide range of substances, from low-viscosity liquids to high-viscosity gels. Its durable construction ensures longevity, even with frequent use. Researchers and technicians rely on this model for developing prototypes and conducting experiments with accuracy.
Summary Comparison Table
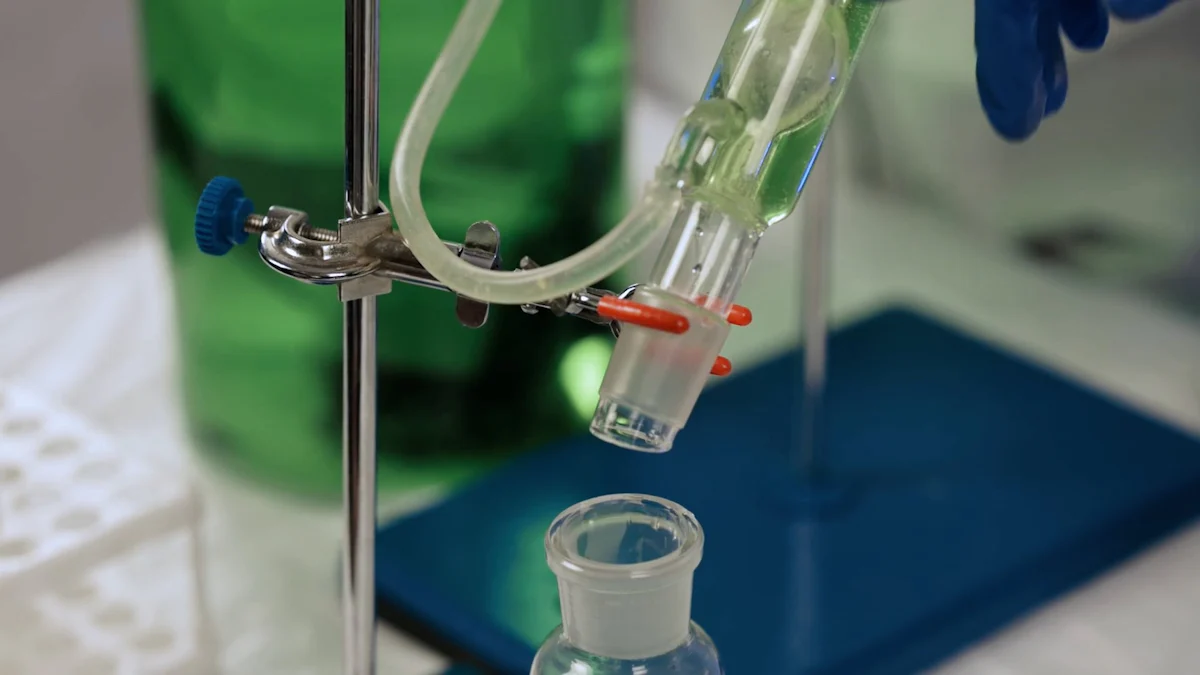
Features and Costs at a Glance
Table summarizing key features and price ranges for each mixer type.
The following table provides a concise overview of the key features and price ranges for various types of chemical mixers. This comparison aims to assist buyers in identifying the most suitable mixer based on their specific requirements and budget constraints.
| Mixer Type | Key Features | Price Range | Ideal Applications |
|——————————-|———————————————————————————–|————————-|———————————————————————————————————–|
| Vertical Agitation Mixers | – High-speed mixing
– Adjustable blades
– Space-efficient vertical design | $930–$6,000 | Pharmaceuticals, food processing, chemical manufacturing |
| Side-Mounted Mixers | – Compact, space-saving design
– Easy maintenance
– Variable speed drives | $275–$1,900 | Wastewater treatment, chemical blending, temperature regulation |
| Emulsifiers | – High shear force
– Fine particle dispersion
– Rotor-stator systems | $1,420–$48,000 | Cosmetics, pharmaceuticals, food emulsions |
| Industrial Blenders | – Large capacity
– Robust stainless steel construction
– Programmable controls | $2,500–$35,000 | Chemical manufacturing, food and beverage processing, pharmaceuticals |
| Laboratory Mixers | – Compact and portable
– Precision mixing
– Interchangeable mixing heads | $13.99–$393.59 | Research and development, small-scale testing, prototype creation |
| Planetary Mixers | – Unique planetary mixing action
– Ideal for high-viscosity products | $1,500–$10,000 (varies) | Dough, creams, pastes in food and cosmetics industries |
| Powder Induction Systems | – Efficient powder-to-liquid mixing
– Faster mixing times
– Easy cleaning | $5,000–$50,000 | Food and beverage applications requiring uniform powder dispersion |
| High-Performance Blenders | – Timers with automatic shutoff
– One-touch blending
– Super-creamy results | $300–$1,200 | Restaurants, bars, and beverage preparation |
Pro Tip: When selecting a mixer, prioritize features that align with your operational needs. For example, Powder Induction Systems offer faster mixing times and improved safety, making them ideal for food and beverage industries. Similarly, Planetary Mixers excel in applications requiring uniformity in high-viscosity products like dough or creams.
This table highlights the diversity in chemical mixer options, showcasing how features and costs vary across categories. Buyers can use this information to make informed decisions, balancing functionality with budget considerations.
Chenma Machinery: A Trusted Partner for Chemical Mixers
Why Choose Chenma Machinery?
Expertise in stainless steel tanks and processing equipment.
Chenma Machinery has established itself as a leader in the manufacturing of stainless steel tanks and processing equipment. The company specializes in creating solutions that cater to the unique demands of industries such as food and beverage, pharmaceuticals, and chemical processing. Its expertise lies in designing and producing equipment that ensures durability, efficiency, and compliance with stringent industrial standards. By focusing on stainless steel, Chenma Machinery delivers products that resist corrosion, maintain structural integrity, and perform reliably in challenging environments.
The company’s production facility spans over 20,000 square meters and houses state-of-the-art machinery. This advanced infrastructure enables the manufacturing of technically demanding designs, ensuring precision and quality in every product. Chenma Machinery’s team of over 200 skilled professionals works diligently to meet the diverse needs of its clients. Their ability to adapt and innovate allows them to deliver equipment tailored to specific operational requirements, ensuring optimal performance and long-term value.
Customizable solutions tailored to client needs.
Chenma Machinery prioritizes customization to address the unique challenges faced by its clients. The company offers flexible solutions that align with the specific requirements of various industries. Whether clients need modifications to existing designs or entirely custom-built equipment, Chenma Machinery’s talented engineers provide tailored options. This adaptability ensures that each product integrates seamlessly into the client’s operations, enhancing efficiency and productivity.
The company also excels in delivering turnkey projects. These comprehensive solutions include process design, equipment manufacturing, installation, and technical training. By managing every aspect of the project, Chenma Machinery ensures a smooth and hassle-free experience for its clients. This end-to-end approach reflects the company’s commitment to delivering value and fostering long-term partnerships.
Certifications and Quality Standards
ISO9001, ISO14001, OHSAS18001, and EU CE certifications.
Chenma Machinery adheres to the highest quality and safety standards, as evidenced by its numerous certifications. The company has achieved ISO9001 certification for its quality management system, ensuring consistent product quality and customer satisfaction. Its ISO14001 certification highlights its commitment to environmental sustainability, demonstrating responsible practices in manufacturing and resource management.
The OHSAS18001 certification underscores Chenma Machinery’s dedication to occupational health and safety. This certification ensures that the company maintains a safe working environment for its employees while minimizing risks associated with industrial operations. Additionally, the EU CE certification confirms that Chenma Machinery’s products comply with European safety, health, and environmental protection standards. These certifications collectively establish the company’s credibility and reliability as a trusted partner in the industrial sector.
Services Offered
Turnkey projects, including process design, equipment manufacturing, installation, and technical training.
Chenma Machinery provides a comprehensive range of services to support its clients throughout the entire project lifecycle. The company’s turnkey solutions begin with process design, where its experts collaborate with clients to develop efficient and effective systems tailored to their needs. This stage involves analyzing operational requirements, identifying potential challenges, and designing processes that optimize performance.
The next phase involves equipment manufacturing, where Chenma Machinery leverages its advanced production capabilities to create high-quality products. The company’s focus on precision and innovation ensures that each piece of equipment meets the highest standards of functionality and durability.
Installation services follow, with Chenma Machinery’s skilled technicians ensuring seamless integration of the equipment into the client’s facility. This step minimizes downtime and ensures that the system operates as intended from the outset. Finally, the company offers technical training to empower clients with the knowledge and skills needed to operate and maintain their equipment effectively. This training enhances operational efficiency and reduces the likelihood of errors or downtime.
By offering these comprehensive services, Chenma Machinery positions itself as a reliable partner for businesses seeking high-performance industrial solutions. Its commitment to excellence and customer satisfaction sets it apart in the competitive landscape of chemical mixer manufacturing.
Understanding the features and costs of chemical mixers is vital for selecting the right equipment. Buyers should evaluate their specific needs, including application type, budget, and desired features, to ensure the chosen industrial mixer aligns with operational goals. A well-informed decision not only enhances efficiency but also ensures long-term value.
Chenma Machinery stands out as a trusted partner, offering high-quality, customizable solutions tailored to diverse industries. With expertise in stainless steel processing equipment and a commitment to excellence, Chenma Machinery delivers reliable products and comprehensive services. Contact Chenma Machinery today for expert guidance or a personalized quote.
FAQ
What factors should buyers consider when selecting a chemical mixer?
Buyers should evaluate several critical factors to ensure the mixer aligns with their operational needs. These include:
- Material compatibility: Ensure the mixer can handle the specific chemicals or materials involved in the process.
- Mixing capacity: Choose a mixer that matches the required batch size or production scale.
- Features and functionality: Assess the importance of speed, programmability, and advanced features like high-shear capabilities.
- Durability and maintenance: Opt for mixers made from robust materials, such as stainless steel, to minimize wear and tear.
- Budget constraints: Balance upfront costs with long-term value by considering energy efficiency, maintenance, and operational reliability.
Pro Tip: Prioritize mixers with features tailored to your industry to maximize efficiency and product quality.
How do batch mixers differ from continuous mixers?
Batch mixers process materials in set quantities, completing one batch before starting another. Continuous mixers, on the other hand, operate without interruption, blending materials as they flow through the system.
- Batch mixers: Ideal for applications requiring precise control over mixing parameters. Common in industries like pharmaceuticals and cosmetics.
- Continuous mixers: Suitable for large-scale production where consistency and efficiency are paramount, such as in food processing or chemical manufacturing.
Selecting between these two depends on production scale and the level of control needed over the mixing process.
What are the most common industries using chemical mixers?
Chemical mixers serve a wide range of industries due to their versatility. Key sectors include:
- Pharmaceuticals: For blending active ingredients and excipients in drug formulations.
- Food and beverage: To create consistent textures and flavors in sauces, dressings, and beverages.
- Chemical manufacturing: For producing adhesives, coatings, and fine chemicals.
- Cosmetics: To achieve smooth and stable formulations in creams, lotions, and gels.
- Wastewater treatment: For processes like flocculation and sludge production.
Each industry benefits from the precision and efficiency that chemical mixers provide.
What is the price range for chemical mixers?
The cost of chemical mixers varies widely based on type, capacity, and features:
- Vertical agitation mixers: $930–$6,000
- Side-mounted mixers: $275–$1,900
- Emulsifiers: $1,420–$48,000
- Industrial blenders: $2,500–$35,000
- Laboratory mixers: $13.99–$393.59
Logical Reasoning: Investing in a higher-priced mixer with advanced features often results in long-term savings through improved efficiency and reduced maintenance costs.
How can buyers determine the cost-effectiveness of a mixer?
To evaluate cost-effectiveness, buyers should create a matrix that balances upfront costs with long-term benefits. Consider:
- Energy efficiency: Lower energy consumption reduces operational expenses.
- Maintenance requirements: Durable mixers with minimal servicing needs save time and money.
- Productivity gains: Advanced features like automation enhance efficiency and reduce labor costs.
Pro Tip: Focus on total cost of ownership rather than just the initial purchase price.
What are the advantages of high-shear mixers?
High-shear mixers excel in applications requiring fine particle dispersion and stable emulsions. Their benefits include:
- Enhanced mixing efficiency: Achieve uniform consistency in less time.
- Versatility: Suitable for emulsifying, homogenizing, and dispersing tasks.
- Improved product quality: Ensure smooth textures and stable formulations.
These mixers are indispensable in industries like cosmetics, pharmaceuticals, and food processing.
Are chemical mixers customizable for specific applications?
Yes, many manufacturers, including Chenma Machinery, offer customizable solutions. Customization options include:
- Tank size and material: Adjustments to accommodate specific volumes or chemical properties.
- Blade design: Tailored for high-shear, low-shear, or specialized mixing tasks.
- Programmable controls: Features like variable speed settings for precise operation.
Customization ensures the mixer integrates seamlessly into existing processes, enhancing efficiency and productivity.
How do laboratory mixers differ from industrial mixers?
Laboratory mixers are designed for small-scale, precise tasks, while industrial mixers handle large-scale production. Key differences include:
- Size and capacity: Laboratory mixers are compact, whereas industrial mixers feature large tanks.
- Precision: Laboratory mixers focus on accuracy for research and development.
- Durability: Industrial mixers are built to withstand heavy-duty operations.
Both types serve distinct purposes but share the goal of achieving optimal mixing results.
What certifications should buyers look for in chemical mixers?
Certifications ensure the mixer meets industry standards for quality and safety. Look for:
- ISO9001: Guarantees consistent product quality.
- ISO14001: Reflects environmental sustainability practices.
- OHSAS18001: Ensures occupational health and safety compliance.
- EU CE certification: Confirms adherence to European safety and environmental standards.
Certified mixers provide peace of mind and demonstrate the manufacturer’s commitment to excellence.
Why choose Chenma Machinery for chemical mixers?
Chenma Machinery stands out for its expertise in stainless steel tanks and processing equipment. Key advantages include:
- Customizable solutions: Tailored designs to meet unique operational needs.
- Comprehensive services: Turnkey projects covering design, manufacturing, installation, and training.
- Certifications: Compliance with ISO9001, ISO14001, OHSAS18001, and EU CE standards.
Chenma Machinery delivers reliable, high-quality products backed by exceptional customer support.