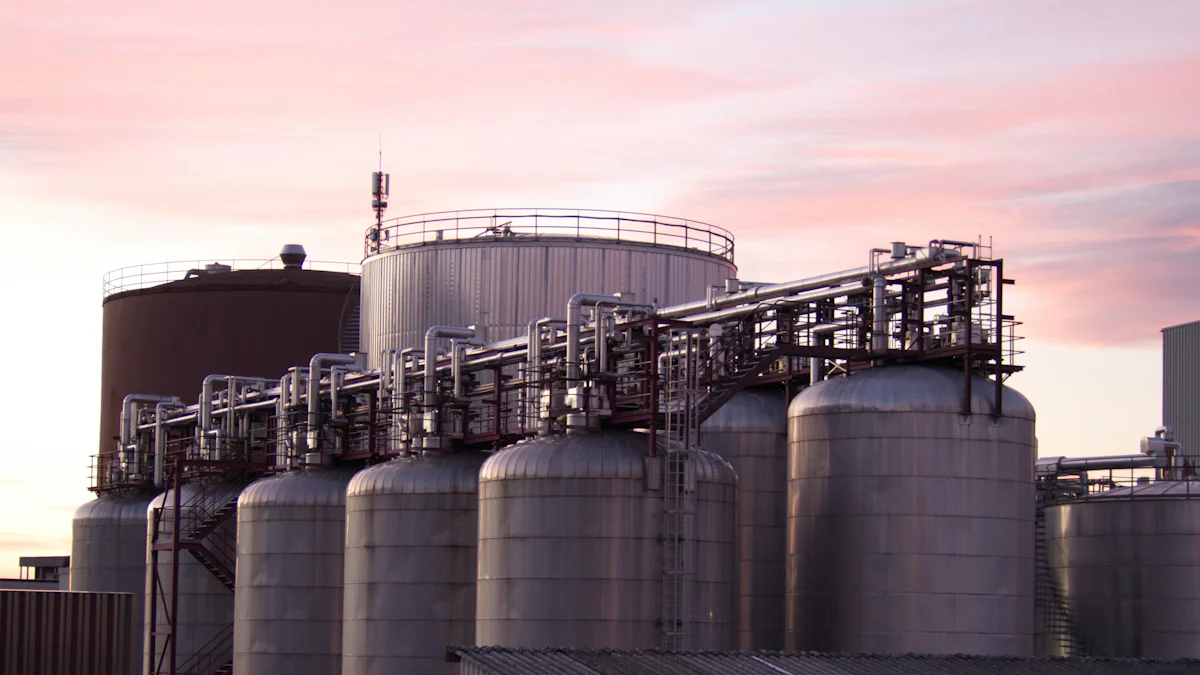
Understanding the components of a chemical mix tank is vital for ensuring efficiency, safety, and optimal performance in industrial processes. These tanks serve as the backbone of industries like pharmaceuticals, food production, and chemical manufacturing. By enabling precise blending, they promote uniformity, enhance product quality, and support large-scale production. Their design accommodates materials with varying viscosities and corrosiveness, ensuring safe handling and reliable operation. Moreover, advanced features like temperature and pressure control facilitate critical chemical reactions, making these chemical mix tanks indispensable for achieving consistent and high-quality outputs.
Overview of Chemical Mixing Tanks
What Is a Chemical Mixing Tank?
A chemical mixing tank is a specialized vessel designed to blend, mix, or combine various substances, such as liquids, powders, or gases, into a uniform mixture. These tanks play a critical role in industries like chemical manufacturing, pharmaceuticals, and food production. Equipped with advanced features, they ensure precise control over mixing parameters, such as temperature, pressure, and agitation speed. This precision allows manufacturers to achieve consistent product quality while meeting stringent safety and regulatory standards.
Chemical mixing tanks are constructed using materials like stainless steel, fiberglass, or plastics, chosen for their durability and compatibility with the chemicals being processed. Their design often includes inlets for adding raw materials, outlets for discharging the final product, and sight glasses for monitoring the mixing process. These features make them indispensable for industries requiring high levels of accuracy and efficiency in their production processes.
Importance of Chemical Mix Tanks in Industrial Processes
Chemical mix tanks serve as the backbone of numerous industrial processes. They enable the production of essential products, such as cleaning agents, adhesives, paints, and medicines. By providing a controlled environment, these tanks facilitate chemical reactions, ensuring the desired compounds are synthesized efficiently and safely. For instance, in the chemical industry, mixing tanks combine liquids under heat and pressure to produce proprietary cleaning solvents or coatings.
Industries rely on these tanks to handle materials with varying viscosities, corrosiveness, and other unique properties. This adaptability ensures safe handling and prevents contamination during production. Additionally, chemical mix tanks support large-scale operations by allowing manufacturers to produce significant quantities of products while maintaining uniformity and quality. Their ability to mix diverse components, such as solids into liquids or liquids with different viscosities, further enhances their versatility.
Key Features of a Chemical Mixing Tank
Chemical mixing tanks come equipped with several key features that enhance their functionality and efficiency:
Agitation Systems: Advanced agitation systems, such as impellers or paddles, ensure thorough mixing and promote uniformity in the final product. These systems also help dissolve solids into liquids or blend liquids with varying viscosities.
Material Compatibility: The tank’s construction material, such as stainless steel or fiberglass, is selected based on its resistance to corrosion and compatibility with the chemicals being processed. This ensures durability and safety during operation.
Temperature and Pressure Control: Many chemical mixing tanks include mechanisms to regulate temperature and pressure, which are crucial for facilitating chemical reactions and achieving desired outcomes.
Inlets and Outlets: Separate inlets for raw materials and outlets for the finished product streamline the production process and minimize cross-contamination risks.
Monitoring Features: Sight glasses and control systems allow operators to monitor the mixing process in real-time, ensuring optimal performance and quality control.
These features make chemical mixing tanks essential for industries aiming to enhance efficiency, reduce operational costs, and maintain high-quality standards in their production processes.
Key Components of a Chemical Mixing Tank
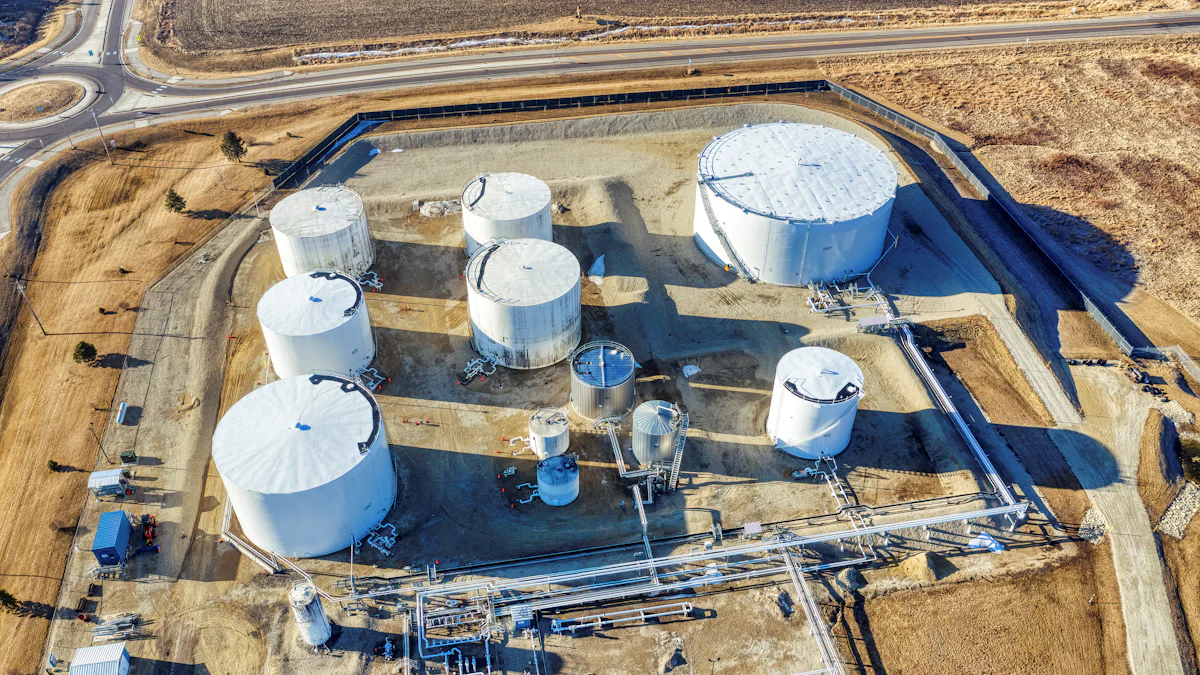
Tank Material
Common Materials
The material of a chemical mixing tank plays a crucial role in its performance and durability. Common materials include:
- Stainless Steel: Known for its corrosion resistance and strength, stainless steel is ideal for handling aggressive chemicals and high-temperature processes. It is widely used in industries like pharmaceuticals and food production.
- Fiberglass: Lightweight and resistant to corrosion, fiberglass suits applications involving less abrasive chemicals. Its affordability makes it a popular choice for certain industrial processes.
- Plastics: Materials like polyethylene and polypropylene are often used for their chemical compatibility and cost-effectiveness. These are suitable for mixing less reactive substances.
Each material offers unique advantages, ensuring compatibility with the specific requirements of the substances being processed.
Factors Influencing Material Choice
Selecting the right material depends on several factors:
- Chemical Compatibility: The tank material must resist corrosion and degradation when exposed to the chemicals being mixed.
- Durability: Industries handling abrasive or high-viscosity substances require robust materials like stainless steel.
- Temperature and Pressure Tolerance: Processes involving extreme conditions demand materials capable of withstanding such environments.
- Cost Considerations: Budget constraints often influence the choice between premium materials like stainless steel and more economical options like plastics.
The material selection process ensures the tank meets operational demands while maintaining safety and efficiency.
Agitator
Types of Agitators
The agitator is a vital component of a chemical mixing tank, responsible for creating the motion necessary for effective mixing. Common types include:
- Impellers: Suitable for low to medium viscosity liquids, impellers generate axial or radial flow patterns, ensuring uniform mixing.
- Turbines: Designed for high-shear mixing, turbines handle medium to high viscosity substances effectively.
- Paddles: Ideal for gentle mixing, paddles work well with fragile materials or when minimal shear is required.
Each type serves specific purposes, ensuring the mixing process aligns with the desired outcomes.
Role in Mixing Efficiency and Flow Patterns
The agitator’s design and placement significantly impact mixing efficiency. Properly selected agitators reduce mixing time and ensure uniform distribution of components. For instance:
“Different agitator types such as paddle, propeller, and turbine are selected based on viscosity and mixing requirements to ensure effective mixing operation and reduce mixing time.”
The agitator also determines the flow pattern within the tank. Axial flow promotes vertical circulation, while radial flow enhances horizontal movement. These patterns ensure thorough blending and prevent settling of heavier components.
Baffles
Purpose of Baffles in Enhancing Mixing
Baffles are flat plates installed inside the tank to improve mixing efficiency. They disrupt the rotational motion of the liquid, preventing vortex formation. This interruption enhances turbulence, ensuring better dispersion of components and uniform mixing.
“Baffles in mixing tanks improve mixing efficiency by interrupting liquid movement and eliminating vortex motion.”
By promoting turbulence, baffles optimize the interaction between the agitator and the liquid, leading to a more effective mixing process.
Design and Placement Considerations
The design and placement of baffles are critical for achieving optimal performance. Cylindrical tanks often include four evenly spaced baffles to maximize efficiency. The width and length of the baffles depend on the tank’s size and the viscosity of the materials being mixed. Proper placement ensures the liquid flows uniformly, enhancing the overall effectiveness of the mixing process.
Control Systems
Control systems in a chemical mixing tank play a pivotal role in ensuring precision and consistency during the mixing process. These systems allow operators to monitor and regulate critical parameters, enhancing both efficiency and safety.
Types of Control Systems
Control systems can be categorized into three main types:
- Manual Control Systems: Operators manually adjust settings such as agitation speed or temperature. This type is suitable for simple processes where minimal adjustments are required.
- Automated Control Systems: These systems use sensors and pre-programmed settings to automatically regulate parameters. They reduce human intervention and improve accuracy.
- PLC-Based Systems: Programmable Logic Controllers (PLCs) offer advanced automation. They integrate with other equipment, enabling real-time monitoring and precise control over complex processes.
Each type serves specific operational needs, ensuring the mixing process aligns with industry requirements.
Monitoring and Regulation of Key Parameters
Effective control systems monitor and regulate essential parameters, including:
- Temperature: Maintaining the correct temperature is crucial for processes involving chemical reactions. Control systems ensure consistent heat levels, preventing overheating or underheating.
- Agitation Speed: Adjusting the speed of the agitator optimizes mixing efficiency. For example, high speeds may be necessary for blending viscous materials, while lower speeds suit delicate substances.
- Pressure: In some applications, maintaining specific pressure levels ensures the desired reaction or mixing outcome.
By managing these parameters, control systems enhance the performance of the chemical mixing tank and ensure product quality.
Additional Features
Modern chemical mixing tanks include additional features that streamline operations and improve functionality.
Inlets and Outlets for Material Flow
Inlets and outlets facilitate the seamless addition and removal of materials. Multiple inlets allow operators to introduce raw ingredients at different stages of the process. Outlets ensure the efficient discharge of the final product, minimizing waste and contamination risks. These features simplify workflows and support continuous production.
Sight Glasses for Monitoring Contents
Sight glasses provide a clear view of the tank’s interior, enabling operators to visually monitor the mixing process. This feature ensures real-time observation of material consistency, color, and volume. It also helps identify potential issues, such as incomplete mixing or foreign particles, allowing for immediate corrective actions.
“Sight glasses enhance operational efficiency by offering a direct view of the mixing process, ensuring quality control and timely adjustments.”
These additional features contribute to the overall reliability and versatility of a chemical mixing tank, making it an indispensable tool in various industries.
Types of Chemical Mixing Tanks
Batch Mixing Tanks
Batch mixing tanks are designed for processes that require precise control over individual production cycles. These tanks handle one batch at a time, making them ideal for applications where consistency and accuracy are critical. Industries such as pharmaceuticals, food production, and specialty chemicals often rely on batch mixing tanks to produce high-quality products.
Key features of batch mixing tanks include:
- Advanced Automation: Many batch tanks incorporate automated control systems to regulate parameters like mixing speed, temperature, and chemical dosing. This ensures consistent results across multiple batches.
- Flexibility: Operators can adjust settings for each batch, allowing customization for different formulations or recipes.
- Efficient Cleaning: Batch tanks often include features like Clean-in-Place (CIP) systems, which simplify cleaning between production cycles and reduce downtime.
“Batch mixing tanks excel in producing small to medium quantities of products with precise control, ensuring uniformity and quality.”
These tanks are particularly useful for processes requiring frequent changes in formulations or ingredients.
Continuous Mixing Tanks
Continuous mixing tanks operate differently from batch tanks by maintaining a constant flow of materials. These tanks are designed for high-volume production, where uninterrupted operation is essential. Industries like water treatment, petrochemicals, and large-scale food manufacturing benefit significantly from continuous mixing tanks.
Key characteristics of continuous mixing tanks include:
- Streamlined Operation: Materials enter and exit the tank simultaneously, ensuring a steady production flow without interruptions.
- Energy Efficiency: Optimized agitators and automated systems reduce energy consumption while maintaining effective mixing.
- Real-Time Monitoring: Sensors and intelligent control systems track parameters such as temperature, pressure, and mixing levels. Operators can make adjustments remotely, improving efficiency and reducing errors.
“Continuous mixing tanks enhance productivity by eliminating downtime between batches, making them ideal for large-scale operations.”
These tanks are well-suited for processes requiring consistent output over extended periods.
Specialty Tanks for Specific Applications
Specialty tanks cater to unique industrial needs, offering customized solutions for specific applications. These tanks are engineered to handle challenging materials or processes, such as highly viscous substances, corrosive chemicals, or temperature-sensitive reactions.
Examples of specialty tanks include:
- Heated Mixing Tanks: Equipped with precise temperature controls, these tanks ensure optimal conditions for processes requiring heat. Regular calibration of temperature controls prevents overheating or underheating, safeguarding both the product and equipment.
- Smart Tanks: Advanced features like IoT-enabled monitoring systems allow real-time tracking of parameters. Sensors relay data to operators, enabling remote adjustments and enhancing operational safety.
- High-Shear Mixing Tanks: Designed for emulsification or homogenization, these tanks use high-speed agitators to achieve fine particle dispersion.
“Specialty tanks provide tailored solutions for complex industrial challenges, ensuring efficiency and reliability in demanding applications.”
Industries requiring innovative and adaptable equipment often turn to specialty tanks to meet their unique production requirements.
Mixing Technologies in Chemical Mix Tanks
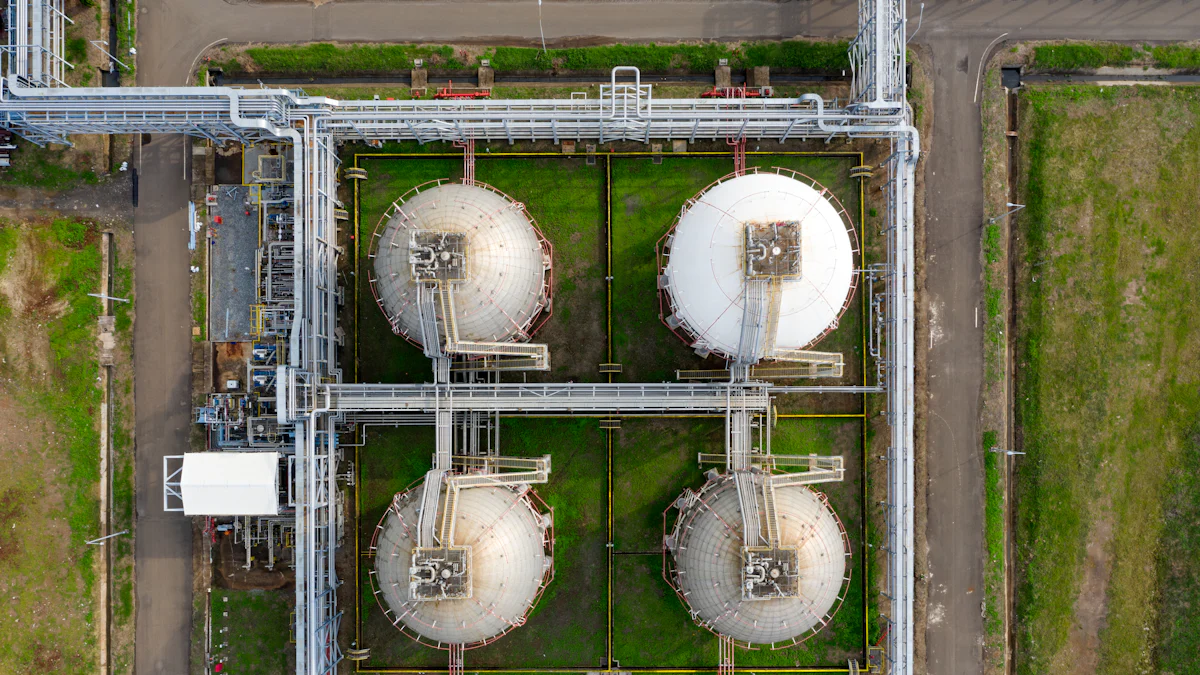
Chemical mix tanks employ various technologies to achieve efficient and uniform mixing. These technologies cater to different industrial needs, ensuring optimal performance for specific applications. The three primary mixing technologies include mechanical, hydraulic, and pneumatic methods. Each method offers unique advantages and is selected based on the nature of the materials and the desired outcomes.
Mechanical Mixing
Mechanical mixing relies on physical components, such as agitators and impellers, to create motion within the tank. This method is widely used due to its versatility and effectiveness in handling a range of viscosities and material types.
How It Works: Mechanical mixing involves the rotation of an agitator, which generates flow patterns that blend the contents of the tank. Impellers, paddles, or turbines are commonly used to achieve this motion. The design and speed of the agitator determine the efficiency of the mixing process.
Applications: Industries like pharmaceuticals, food production, and chemical manufacturing frequently use mechanical mixing. For example, it is ideal for dissolving solids into liquids or blending liquids with varying viscosities.
Advantages:
- Provides precise control over mixing speed and intensity.
- Suitable for both low and high-viscosity materials.
- Ensures uniform distribution of components.
“Mechanical mixing is the most common method due to its adaptability and ability to handle diverse materials effectively.”
Hydraulic Mixing
Hydraulic mixing uses the force of liquid movement to achieve blending. This method is particularly effective for large-scale operations and applications involving liquids with similar densities.
How It Works: Hydraulic mixing involves the introduction of pressurized liquid streams into the tank. These streams create turbulence, which promotes the mixing of the tank’s contents. The process eliminates the need for mechanical agitators, reducing maintenance requirements.
Applications: Hydraulic mixing is commonly used in water treatment plants and industries requiring the blending of large volumes of liquids. It is also effective for processes where minimal shear is necessary.
Advantages:
- Reduces wear and tear on equipment due to the absence of moving parts.
- Energy-efficient for large-scale operations.
- Minimizes contamination risks by avoiding direct contact with mechanical components.
“Hydraulic mixing offers a low-maintenance solution for blending liquids in high-volume applications.”
Pneumatic Mixing
Pneumatic mixing employs compressed air or gas to create motion within the tank. This method is ideal for applications requiring gentle mixing or the aeration of materials.
How It Works: Compressed air or gas is introduced through diffusers or spargers at the bottom of the tank. The rising bubbles generate upward motion, creating circulation and blending the contents. This method is particularly effective for suspending solids or maintaining homogeneity in liquids.
Applications: Pneumatic mixing is widely used in fermentation processes, wastewater treatment, and industries requiring aeration. It is also suitable for mixing delicate materials that could be damaged by mechanical agitation.
Advantages:
- Gentle on fragile materials, preserving their integrity.
- Provides aeration, which is essential for processes like fermentation.
- Simple design with minimal mechanical components, reducing maintenance needs.
“Pneumatic mixing combines simplicity and effectiveness, making it a preferred choice for aeration and gentle blending.”
Each mixing technology serves specific industrial requirements, ensuring that chemical mix tanks deliver optimal performance. The selection of the appropriate method depends on factors such as material properties, process scale, and desired outcomes.
Applications of Chemical Mixing Tanks
Chemical mixing tanks play a pivotal role across various industries, ensuring efficient blending, uniformity, and quality in production processes. Their versatility and adaptability make them indispensable for a wide range of applications.
Industrial Applications (e.g., chemical manufacturing, water treatment)
In industrial settings, chemical mixing tanks are essential for processes like chemical production, water treatment, and adhesive formulation. These tanks enable precise control over mixing parameters, ensuring consistent results. For example, in chemical manufacturing, they facilitate the combination of raw materials under controlled conditions to produce cleaning agents, coatings, and solvents. The ability to handle materials with varying viscosities and corrosiveness ensures safety and efficiency during operations.
Water treatment plants rely on industrial mixing tanks to blend chemicals like coagulants and disinfectants into water. This process ensures the removal of impurities and pathogens, making water safe for consumption. The tanks’ advanced features, such as automated control systems and durable construction materials, enhance their performance in these demanding environments.
“Mixing tanks of better quality lower mixing time, enhance uniformity, improve efficiency, and output levels.”
This efficiency makes them a cost-effective solution for large-scale industrial processes.
Food and Beverage Industry (e.g., blending ingredients, ensuring consistency)
The food and beverage industry depends heavily on mixing tanks to maintain product quality and consistency. These tanks are used to blend ingredients for beverages, sauces, and dairy products. For instance, breweries and distilleries use precision mixing tanks to create consistent flavor profiles in their products. The tanks’ ability to regulate temperature and agitation speed ensures thorough blending, which is crucial for achieving the desired taste and texture.
Mixing tanks also play a significant role in the preparation of beverages. They ensure uniform mixing of ingredients, preventing separation and maintaining the product’s quality throughout its shelf life. Features like Clean-in-Place (CIP) systems simplify cleaning, reducing downtime between production cycles and ensuring hygiene standards are met.
“Mixing tanks are widely used in the food and beverage industry to prepare various beverages, ensuring uniform mixing and maintaining product quality and taste.”
This highlights their importance in delivering high-quality products to consumers.
Pharmaceutical and Cosmetic Industries (e.g., creating emulsions, suspensions)
In the pharmaceutical and cosmetic industries, mixing tanks are vital for producing emulsions, suspensions, and other formulations. These tanks ensure the uniform distribution of active ingredients, which is critical for the efficacy of pharmaceutical products. For example, they are used to mix liquid medications, creams, and ointments, ensuring consistency and stability.
Cosmetic manufacturers use mixing tanks to create products like lotions, shampoos, and makeup. The tanks’ ability to handle delicate materials and maintain precise temperature control ensures the preservation of product quality. Advanced features, such as programmable logic controllers (PLCs), allow operators to monitor and adjust parameters in real-time, enhancing efficiency and reducing errors.
“Precision mixing tanks ensure thorough and efficient blending, crucial for chemical reactions and consistent flavor profiles in breweries and distilleries.”
This precision is equally important in pharmaceutical and cosmetic applications, where product quality directly impacts consumer safety and satisfaction.
Maintenance Practices for Chemical Mixing Tanks
Proper maintenance of chemical mixing tanks ensures their longevity, efficiency, and safety. Regular upkeep minimizes downtime, reduces repair costs, and maintains the quality of the mixing process. Industries such as pharmaceuticals, food production, and chemical manufacturing rely heavily on these tanks, making maintenance a critical aspect of operations.
Cleaning and Sanitation
Importance of Regular Cleaning
Regular cleaning of chemical mixing tanks is essential to prevent contamination and maintain product quality. Residue from previous batches can compromise the integrity of subsequent mixtures, especially in industries like food and pharmaceuticals. Cleaning also removes harmful chemicals or debris that may corrode the tank’s surface over time. This practice ensures compliance with industry hygiene standards and extends the tank’s lifespan.
“Mixing tanks are fundamental in industries where sanitation detergents, medicines, or water treatment chemicals are produced.”
By maintaining cleanliness, operators can ensure that the tank performs optimally and meets strict regulatory requirements.
Cleaning Methods
Several cleaning methods are available, depending on the tank’s design and the nature of the substances being mixed:
- Clean-in-Place (CIP) Systems: These automated systems clean the tank without disassembly. They use high-pressure water jets, detergents, or steam to remove residues. CIP systems save time and reduce labor costs, making them ideal for large-scale operations.
- Manual Cleaning: For smaller tanks or stubborn residues, manual cleaning may be necessary. Operators use brushes, scrapers, and cleaning agents to ensure thorough sanitation. While labor-intensive, this method allows for detailed inspection during the cleaning process.
Both methods play a vital role in maintaining the tank’s functionality and ensuring the safety of the final product.
Inspection and Repairs
Routine Inspections for Wear and Tear
Routine inspections help identify potential issues before they escalate into costly repairs. Operators should check for signs of wear, such as cracks, corrosion, or leaks. Agitators, baffles, and control systems require particular attention, as they are critical to the tank’s performance. Regular inspections ensure that the tank operates efficiently and safely.
“Mixing tanks accommodate diverse chemicals, which upon mixing, can be in a homogeneous form.”
This versatility makes it crucial to monitor the tank’s condition to handle various substances effectively.
Common Repairs
Despite regular maintenance, some components may require repairs over time. Common issues include:
- Agitator Replacement: Agitators experience significant wear due to constant motion. Replacing worn-out agitators ensures consistent mixing efficiency.
- Fixing Leaks: Leaks can occur due to corrosion or damage to the tank’s surface. Prompt repair prevents chemical loss and ensures safety during operation.
Addressing these issues promptly minimizes downtime and maintains the tank’s reliability.
Preventive Maintenance
Scheduling Maintenance
Preventive maintenance involves scheduling regular checks and servicing to avoid unexpected failures. Operators should create a maintenance calendar that includes cleaning, inspections, and component replacements. This proactive approach ensures that the tank remains in optimal condition and reduces the risk of costly breakdowns.
“Having the right mixing tank increases options offered by the market while broadening application scope.”
Preventive maintenance ensures that the tank continues to meet diverse industrial needs.
Benefits of Preventive Maintenance
The benefits of preventive maintenance extend beyond cost savings. It enhances the tank’s performance, ensuring consistent mixing results. Regular upkeep also improves safety by reducing the risk of accidents caused by equipment failure. Additionally, well-maintained tanks comply with industry standards, protecting the manufacturer’s reputation and ensuring customer satisfaction.
By prioritizing maintenance, industries can maximize the efficiency and lifespan of their chemical mixing tanks, ensuring seamless operations and high-quality outputs.
Chenma Machinery’s Expertise in Chemical Mixing Tanks
Overview of Chenma Machinery’s Capabilities
Chenma Machinery stands as a leader in the design and production of chemical mixing tanks. The company operates from a state-of-the-art 20,000 m² facility in Shandong Province, equipped with advanced machinery to meet the most demanding technical requirements. Over 200 skilled professionals contribute to the manufacturing process, ensuring precision and quality in every product.
The company specializes in stainless steel tanks, which are widely recognized for their durability and resistance to corrosion. These tanks cater to industries such as pharmaceuticals, food and beverage, and chemical manufacturing. Chenma Machinery integrates cutting-edge technologies into its designs, enabling precise control over mixing parameters like temperature, pressure, and agitation speed. This ensures that clients achieve consistent product quality while adhering to strict safety standards.
“Tank mixers reduce manual mixing needs, enhance safety, and can be designed to be explosion-proof for hazardous environments.”
Chenma Machinery incorporates these safety features into its products, making them suitable for handling hazardous materials in industrial settings.
Customization and Turnkey Solutions
Chenma Machinery excels in providing customized solutions tailored to the unique needs of its clients. The company’s talented engineers adapt existing designs or create entirely new ones to meet specific operational requirements. This flexibility allows clients to optimize their production processes and achieve desired outcomes efficiently.
The company also offers comprehensive turnkey solutions. These include process design, equipment manufacturing, installation, commissioning, and technical training. By managing every stage of the project, Chenma Machinery ensures seamless integration of its products into the client’s operations. This approach minimizes downtime and maximizes productivity.
- Customization Highlights:
- Tanks designed for specific applications, such as high-shear mixing or temperature-sensitive processes.
- Integration of advanced control systems, including PLC-based automation, for real-time monitoring and adjustments.
- Adaptation of tank materials to suit the chemical compatibility and durability requirements of the client.
“Chemical mixing tanks are essential for product uniformity and safety in industries dealing with formulated chemicals.”
Chenma Machinery’s customized tanks ensure uniform mixing and safe handling of diverse materials, enhancing operational efficiency.
Certifications and Quality Standards
Chenma Machinery prioritizes quality and safety in every aspect of its operations. The company adheres to the latest industry standards, ensuring that its products meet the rigorous demands of modern industrial processes. Chenma Machinery has earned multiple certifications, reflecting its commitment to excellence:
- ISO9001-2005 Quality System Certification: Guarantees consistent product quality and adherence to international manufacturing standards.
- ISO14001-2015 Environmental Management System Certification: Demonstrates the company’s dedication to environmentally responsible practices.
- OHSAS18001-2007 Occupational Health Management System Certification: Ensures the safety and well-being of workers during the manufacturing process.
- EU CE Certification: Confirms compliance with European safety, health, and environmental protection standards.
These certifications validate Chenma Machinery’s expertise and reliability as a manufacturer of chemical mixing tanks. Clients can trust the company to deliver products that enhance safety, efficiency, and performance in their operations.
“Routine maintenance checks ensure safe and effective mixing operations by identifying and addressing minor issues before they escalate.”
Chenma Machinery’s tanks are designed with durability and ease of maintenance in mind, reducing the risk of operational disruptions and ensuring long-term reliability.
Understanding the components of a chemical mix tank is essential for achieving efficiency, safety, and consistent performance in industrial processes. Selecting the right materials, such as stainless steel or fiberglass, ensures durability and chemical compatibility. Advanced technologies, including automated control systems and precision agitators, enhance mixing efficiency and product quality. Regular maintenance practices, like cleaning and inspections, extend the tank’s lifespan and reliability.
Chenma Machinery excels in delivering high-quality, customized solutions for chemical mixing tanks. Their expertise in process design, equipment manufacturing, and turnkey projects ensures tailored systems that meet diverse industrial needs. With a focus on innovation and quality, Chenma Machinery supports industries in optimizing their operations.
FAQ
What is the primary purpose of a chemical mixing tank?
A chemical mixing tank ensures the uniform blending of substances, such as liquids, powders, or gases. These tanks play a critical role in industries like pharmaceuticals, food production, and chemical manufacturing. By providing precise control over parameters like temperature, pressure, and agitation speed, they help achieve consistent product quality and support large-scale production.
“Precision in chemical mixing tanks is crucial for blending substances accurately and ensuring high-quality mixtures.”
How do I choose the right material for a chemical mixing tank?
The choice of material depends on factors like chemical compatibility, durability, and operational conditions. Stainless steel is ideal for handling corrosive chemicals and high temperatures due to its strength and resistance to corrosion. Fiberglass suits applications involving less abrasive chemicals, while plastics like polyethylene are cost-effective for mixing less reactive substances.
“The choice of material, like stainless steel, is critical for maintaining tank integrity and performance.”
Why are agitators essential in chemical mixing tanks?
Agitators create motion within the tank, ensuring thorough mixing and uniform distribution of components. Different types, such as impellers, turbines, and paddles, cater to specific needs. For example, impellers work well with low-viscosity liquids, while turbines handle high-viscosity substances effectively.
“Tank mixers are valuable assets due to their durability and custom designs that address specific industry needs.”
What role do baffles play in the mixing process?
Baffles enhance mixing efficiency by disrupting the rotational flow of liquids, preventing vortex formation. This disruption promotes turbulence, ensuring better dispersion of components. Properly designed and placed baffles optimize the interaction between the agitator and the liquid, leading to more effective mixing.
How can I maintain the longevity of my chemical mixing tank?
Proper maintenance practices, such as regular cleaning, routine inspections, and preventive maintenance, extend the lifespan of a chemical mixing tank. Clean-in-Place (CIP) systems simplify cleaning, while routine checks help identify wear and tear. Scheduling preventive maintenance ensures the tank operates efficiently and safely.
“Proper tank storage, compliance with manufacturer’s instructions, and maintenance are essential for extending the life of chemical mixing tanks.”
What are the benefits of automated control systems in mixing tanks?
Automated control systems enhance precision and consistency by regulating key parameters like temperature, agitation speed, and pressure. Programmable Logic Controllers (PLCs) allow real-time monitoring and adjustments, reducing human intervention and improving accuracy. These systems ensure efficient operations and high-quality outputs.
What types of industries benefit from chemical mixing tanks?
Chemical mixing tanks serve various industries, including pharmaceuticals, food and beverage, water treatment, and chemical manufacturing. They enable processes like blending ingredients, creating emulsions, and facilitating chemical reactions. Their versatility and adaptability make them indispensable for achieving uniformity and quality in production.
“Understanding tank components and quality solutions are crucial for maximizing mixing processes in various industries.”
How does Chenma Machinery customize chemical mixing tanks?
Chenma Machinery provides tailored solutions to meet unique industrial needs. Their engineers adapt designs or create custom tanks based on specific requirements, such as space constraints, chemical compatibility, or operational demands. The company also offers turnkey solutions, including process design, installation, and technical training.
“Chenma Machinery ensures all components of the equipment are customized to meet specifications.”
What certifications ensure the quality of Chenma Machinery’s products?
Chenma Machinery adheres to strict quality and safety standards. The company holds certifications like ISO9001-2005 for quality management, ISO14001-2015 for environmental practices, and OHSAS18001-2007 for occupational health. Additionally, their products meet EU CE certification standards, ensuring compliance with European safety and environmental regulations.
Why should I invest in a high-quality chemical mixing tank?
High-quality chemical mixing tanks improve efficiency, reduce operational costs, and ensure consistent product quality. Durable materials like stainless steel enhance performance and safety. Advanced features, such as automated control systems and precision agitators, optimize mixing processes and support large-scale production.
“Choosing the right materials for tank mixers is crucial for performance, durability, and safety.”