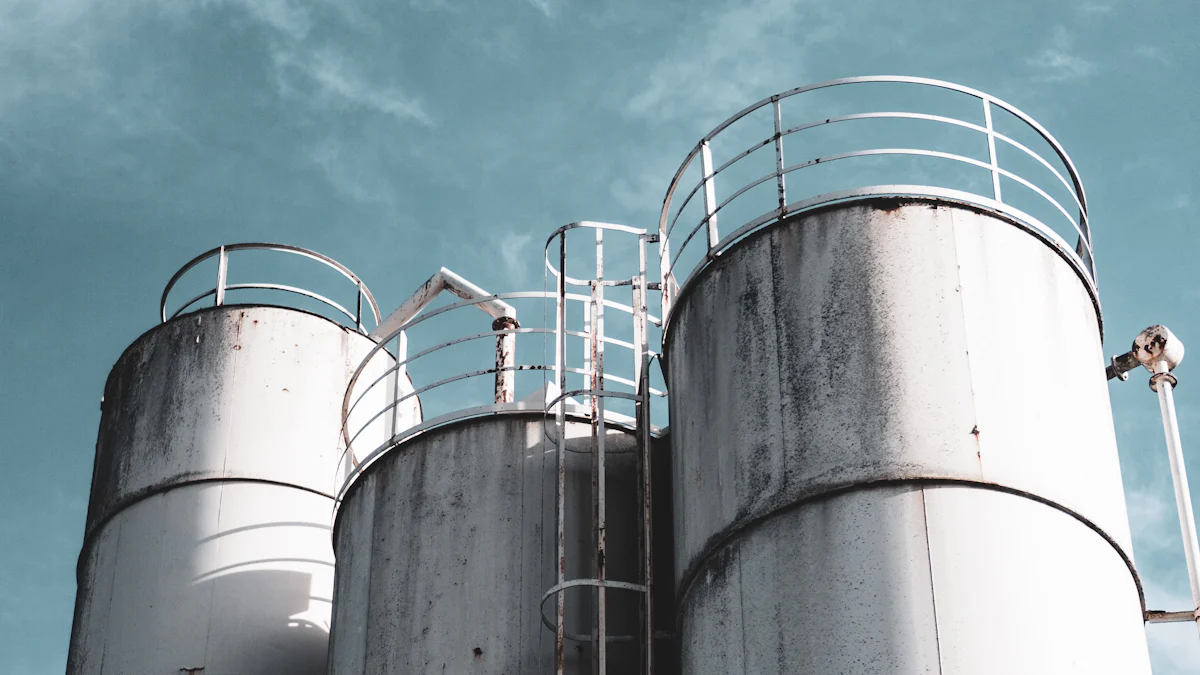
In modern industries, precision and efficiency are non-negotiable. A chemical mix tank ensures consistent results by blending substances with accuracy, which is vital for maintaining product quality. Industries like pharmaceuticals and food production rely on these tanks to meet strict standards. Without them, you risk inconsistent products, safety hazards, and higher operational costs. These tanks also streamline processes, reducing manual labor and downtime. Their role extends beyond mixing; they safeguard compliance with regulations, preventing costly recalls or waste disposal issues. This makes them an indispensable tool in today’s industrial landscape.
What Is a Chemical Mix Tank?
Chemical mix tanks are essential tools in industrial processes. These specialized tanks are designed to mix, blend, and homogenize various substances, ensuring precise and consistent results. Whether you work in the chemical, pharmaceutical, or food industry, these tanks play a pivotal role in achieving production goals and maintaining high-quality standards.
Definition and Purpose of Chemical Mix Tanks
A chemical mix tank is a piece of industrial equipment used to combine different materials, such as liquids, powders, or gases, into a uniform mixture. These tanks are built to handle diverse chemicals and are often customized to meet specific operational requirements. Their primary purpose is to provide a controlled environment for mixing, which is critical for industries that demand accuracy and consistency in their products.
Did you know? Chemical mix tanks are widely used in industries like water treatment, pharmaceuticals, and food production to ensure product safety and quality.
By using chemical mix tanks, you can streamline your production processes, reduce manual labor, and enhance operational efficiency. These tanks also help maintain compliance with industry regulations, making them indispensable for businesses that prioritize safety and quality.
Core Functions of Chemical Mix Tanks
Mixing and Blending of Substances
The primary function of a chemical mix tank is to mix and blend different substances effectively. Whether you need to combine liquids of varying viscosities or dissolve solids into liquids, these tanks ensure thorough and uniform mixing. This process is vital for creating products that meet specific standards and specifications.
For example, in the chemical industry, mixing tanks are used to blend adhesives, paints, and coatings. In the pharmaceutical sector, they help mix drug raw materials and solutions to produce medicines that meet stringent quality requirements.
Facilitating Chemical Reactions
Chemical mix tanks also play a crucial role in facilitating chemical reactions. By providing a controlled environment, these tanks allow you to manage reaction rates and achieve desired outcomes. Efficient mixing enhances heat transfer during reactions, which is essential for both exothermic and endothermic processes.
Pro Tip: Proper mixing not only speeds up chemical reactions but also ensures maximum completion, reducing waste and improving overall efficiency.
Maintaining Product Uniformity
Consistency is key in industrial production, and chemical mix tanks help you achieve it. These tanks ensure that every batch of your product has the same composition and quality. This uniformity is especially important in industries like food and beverage, where even slight variations can impact taste, texture, or safety.
By maintaining product uniformity, chemical mix tanks help you build trust with your customers and meet regulatory standards. They also minimize the risk of product recalls, saving you time and money in the long run.
Why Are Chemical Mixing Tanks Essential in Modern Industry?
Chemical mixing tanks are indispensable in modern industrial operations. They ensure precision, consistency, and safety in processes that demand meticulous control. From supporting critical production tasks to maintaining compliance with industry standards, these tanks play a pivotal role in driving efficiency and quality.
Supporting Critical Industrial Processes
Chemical mixing tanks form the backbone of many industrial processes. They enable you to blend, mix, and homogenize substances with precision, which is essential for achieving specific production goals. Whether you are producing detergents, adhesives, or medicines, these tanks ensure that the mixing process meets the required standards.
Fact: Industrial mixers are widely used in chemical production to create products like paints, coatings, and water treatment solutions. Without them, achieving the desired consistency and quality would be nearly impossible.
The advanced mixing technology integrated into these tanks enhances their efficiency. By optimizing the blending of liquids, powders, and gases, they help you streamline operations and reduce production time. This makes them a vital component in industries like pharmaceuticals, food processing, and chemical manufacturing.
Ensuring Product Quality and Consistency
Consistency is key in industrial production. Chemical mixing tanks ensure that every batch of your product meets the same high standards. They provide a controlled environment for blending, which eliminates variations and guarantees uniformity.
For example, in the food and beverage industry, even minor inconsistencies can affect taste, texture, or safety. Chemical mixing tanks prevent such issues by delivering precise and repeatable results. Similarly, in the pharmaceutical sector, these tanks ensure that medicines meet stringent quality requirements, protecting both your reputation and consumer health.
Pro Tip: Using high-quality mixing equipment not only improves product consistency but also reduces waste, saving you time and resources.
By investing in reliable industrial mixers, you can enhance your production capabilities and build trust with your customers. Consistent quality fosters brand loyalty and helps you stay competitive in a demanding market.
Enhancing Safety and Compliance
Safety is a top priority in any industrial setting. Chemical mixing tanks come equipped with advanced safety features that protect both workers and the environment. Leak-proof designs and pressure relief systems minimize the risk of accidents, ensuring a secure working environment.
Did you know? Properly designed safety features in chemical mixing tanks help prevent contamination and chemical spills, reducing environmental impact.
Compliance with industry regulations is another critical aspect. Chemical mixing tanks help you meet strict safety and quality standards, avoiding costly penalties or recalls. By using industrial mixing equipment that adheres to these standards, you can maintain operational integrity and safeguard your business reputation.
Incorporating chemical mixing tanks into your operations not only enhances safety but also ensures long-term sustainability. Their durability and efficiency make them a smart investment for any industry that values quality and compliance.
Benefits of Using Chemical Mixing Tanks
Chemical mixing tanks bring unparalleled advantages to industrial operations. Their ability to streamline processes, ensure compliance, and enhance product quality makes them an essential investment for businesses aiming to optimize performance and maintain competitive edges.
Cost Efficiency in Operations
Chemical mixing tanks significantly reduce operational costs by improving efficiency and minimizing waste. These tanks automate blending processes, eliminating the need for extensive manual labor. This not only saves time but also reduces labor expenses. For example, instead of relying on workers to manually mix substances, you can use industrial mixers to achieve faster and more consistent results.
Additionally, chemical mixing tanks help reduce material waste. Precise mixing ensures that every ingredient is utilized effectively, leaving no room for overuse or spillage. This level of accuracy translates into cost savings, especially in industries like pharmaceuticals and food production, where raw materials can be expensive.
Fact: Tank mixers provide a cost-effective solution for blending liquids, powders, and gases, making them indispensable in large-scale production environments.
By investing in high-quality mixing equipment, you can lower your production costs while maintaining superior product standards.
Compliance with Industry Standards
Meeting industry regulations is crucial for maintaining your business’s reputation and avoiding penalties. Chemical mixing tanks are designed to help you comply with strict safety and quality standards. Their advanced features, such as leak-proof designs and pressure control systems, ensure safe operations and prevent contamination.
For industries like pharmaceuticals and food production, adherence to regulatory guidelines is non-negotiable. Chemical mixing tanks provide the controlled environment necessary to meet these requirements. They also support the use of mixing technology that ensures uniformity and consistency, which are critical for passing quality inspections.
Did you know? Properly designed chemical mixing tanks reduce the risk of product recalls by ensuring compliance with safety and quality standards.
Using industrial mixers that align with regulatory expectations not only protects your business but also builds trust with your customers.
Improved Production Quality and Reliability
Consistency and reliability are the cornerstones of successful industrial production. Chemical mixing tanks ensure that every batch of your product meets the same high standards. Their ability to blend substances uniformly eliminates variations, guaranteeing consistent quality.
For instance, in the food and beverage industry, even minor inconsistencies can affect taste and texture. Chemical mixing tanks prevent such issues by delivering precise and repeatable results. Similarly, in chemical manufacturing, these tanks enhance the performance of reactions by ensuring thorough mixing and heat transfer.
Pro Tip: High-quality industrial mixers improve production reliability, helping you meet customer expectations and maintain brand loyalty.
The durability and advanced design considerations of chemical mixing tanks also contribute to their reliability. Built with corrosion-resistant materials and equipped with cutting-edge features, these tanks ensure long-term performance, even in demanding environments.
By incorporating chemical mixing tanks into your operations, you can achieve higher production quality, reduce downtime, and enhance overall efficiency.
Types of Chemical Mixing Tanks and Their Applications
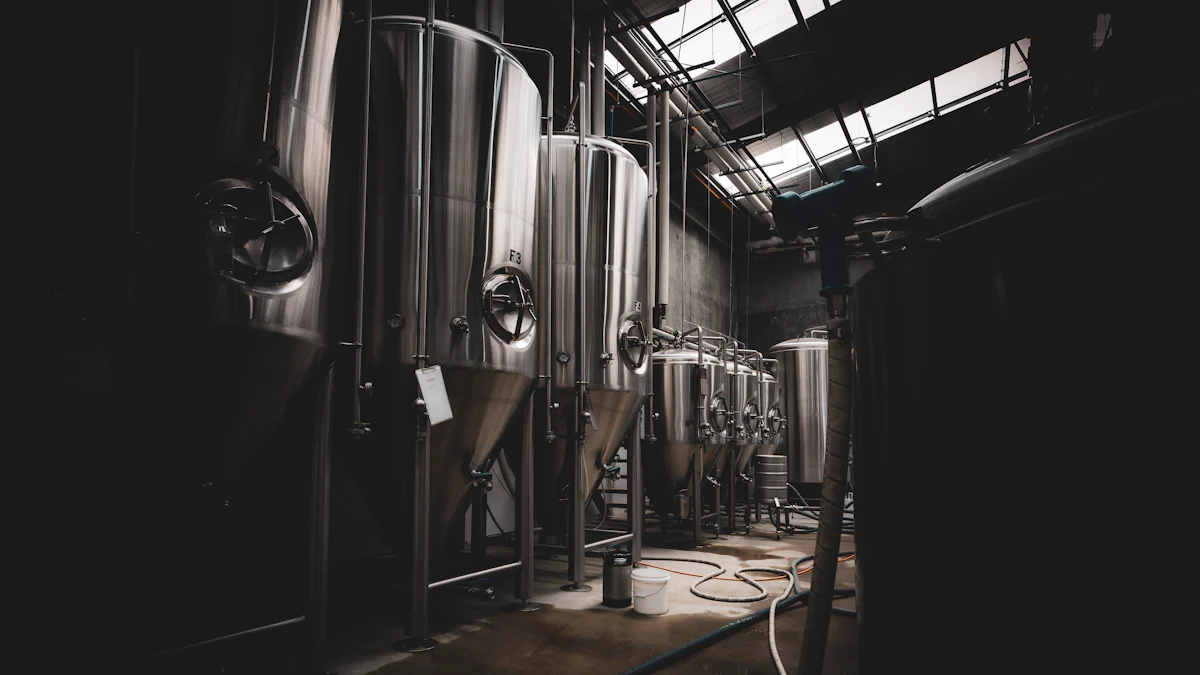
Chemical mixing tanks come in various types, each designed to meet specific industrial needs. Understanding the different types and their applications helps you select the right equipment for your operations. These tanks not only enhance efficiency but also ensure consistent results across diverse industries.
Common Types of Chemical Mixing Tanks
Stainless Steel Tanks
Stainless steel tanks are among the most popular choices for industrial mixing. Their durability and resistance to corrosion make them ideal for handling a wide range of chemicals. These tanks can withstand high temperatures, making them suitable for processes that involve heat or pressure. You often find stainless steel tanks in industries like pharmaceuticals, food production, and chemical manufacturing.
Fact: Stainless steel tanks are easy to clean and maintain, which helps you meet strict hygiene standards in sensitive industries like healthcare and food processing.
Polyethylene Tanks
Polyethylene tanks offer a cost-effective solution for mixing applications. These tanks are lightweight yet durable, making them easy to transport and install. They are resistant to many chemicals, which makes them a practical choice for industries like water treatment and sanitation. Polyethylene tanks are particularly effective for mixing liquids with low to moderate viscosity.
Pro Tip: Use polyethylene tanks for applications where chemical compatibility and affordability are key considerations.
Custom-Designed Tanks
Custom-designed tanks provide tailored solutions for unique industrial requirements. These tanks are engineered to meet specific operational needs, such as mixing highly reactive chemicals or handling large volumes. Customization options include material selection, tank size, and advanced features like automated mixers or monitoring systems. Industries with specialized processes, such as cosmetics or advanced chemical synthesis, benefit greatly from these tanks.
Did you know? Custom-designed tanks can integrate smart technologies like IoT sensors, enabling real-time monitoring and control of mixing processes.
Applications Across Industries
Pharmaceuticals and Healthcare
In the pharmaceutical and healthcare sectors, chemical mixing tanks play a critical role in drug formulation and production. These tanks ensure precise blending of active ingredients, excipients, and solvents. Consistency is vital in this industry, as even minor deviations can impact drug efficacy and safety.
Example: Mixing tanks are used to produce liquid medicines, ointments, and vaccines, ensuring compliance with stringent quality standards.
Food and Beverage Production
The food and beverage industry relies on chemical mixing tanks to create products with consistent taste, texture, and quality. These tanks handle tasks like emulsifying sauces, blending beverages, and homogenizing dairy products. Their ability to maintain hygiene and prevent contamination makes them indispensable in this sector.
Fact: Stainless steel tanks are commonly used in food production due to their non-reactive surfaces, which preserve the flavor and safety of the products.
Water Treatment and Purification
Water treatment facilities use chemical mixing tanks to prepare and distribute treatment chemicals. These tanks mix coagulants, disinfectants, and pH adjusters to ensure clean and safe water. Their robust design allows them to handle corrosive substances and operate in demanding environments.
Pro Tip: Polyethylene tanks are often chosen for water treatment applications because of their chemical resistance and affordability.
Paints, Coatings, and Chemical Manufacturing
In the production of paints, coatings, and other chemical products, mixing tanks ensure uniformity and quality. These tanks blend pigments, solvents, and additives to create products with consistent properties. Advanced industrial mixers enhance the efficiency of these processes, reducing production time and waste.
Example: Chemical mixing tanks are essential for producing adhesives, resins, and polymers, which require precise mixing to achieve desired performance characteristics.
By understanding the types of chemical mixing tanks and their applications, you can make informed decisions that optimize your production processes. Whether you need a durable stainless steel tank, a cost-effective polyethylene option, or a custom-designed solution, these tanks provide the versatility and reliability required in modern industries.
Features That Make Chemical Mix Tanks Indispensable
Chemical mixing tanks are more than just vessels for blending substances. Their advanced features ensure safety, durability, and operational efficiency, making them a cornerstone of modern industrial processes. Below, we explore the key attributes that make these tanks indispensable.
Advanced Safety Mechanisms
Safety features in chemical mixing tanks are critical for protecting workers, the environment, and your operations. These mechanisms minimize risks and ensure smooth, accident-free processes.
Pressure Relief Systems
Pressure relief systems are essential in preventing dangerous pressure build-ups during mixing. These systems release excess pressure safely, avoiding potential tank ruptures or explosions. For industries handling volatile chemicals, this feature is non-negotiable. It ensures that your operations remain secure, even under high-pressure conditions.
Fact: According to industry experts, pressure relief systems are among the most effective ways to mitigate risks in chemical mixing environments.
Leak-Proof Designs
Leak-proof designs safeguard against chemical spills, which can harm workers and the environment. These designs use advanced sealing technologies to prevent leaks, even when handling corrosive or reactive substances. By investing in tanks with leak-proof features, you protect your facility from contamination and costly clean-up efforts.
Pro Tip: Regularly inspect seals and gaskets in your mixing equipment to maintain leak-proof performance over time.
Material Durability and Longevity
The materials used in chemical mixing tanks determine their durability and ability to withstand harsh industrial conditions. High-quality materials ensure long-term performance and reduce maintenance needs.
Corrosion-Resistant Materials
Corrosion-resistant materials, such as stainless steel, are vital for tanks exposed to aggressive chemicals. These materials prevent degradation, ensuring the tank remains functional and safe. Corrosion resistance also extends the lifespan of your equipment, saving you money on replacements.
Did you know? Stainless steel tanks are widely used in industries like pharmaceuticals and food production due to their superior corrosion resistance and ease of cleaning.
High-Temperature Tolerance
Many industrial mixers operate under extreme temperatures. Tanks with high-temperature tolerance can handle these conditions without compromising structural integrity. This feature is especially important in processes involving exothermic reactions or heat-sensitive substances.
Example: In chemical manufacturing, tanks with high-temperature tolerance ensure consistent mixing even during intense thermal reactions.
Integration of Advanced Monitoring Systems
Modern chemical mixing tanks incorporate advanced monitoring systems to enhance precision and control. These systems allow you to oversee and optimize your mixing processes in real time.
Real-Time Tracking and Control
Real-time tracking systems provide instant data on variables like temperature, pressure, and mixing speed. This information helps you make immediate adjustments, ensuring optimal performance. With real-time control, you can prevent errors and maintain product consistency across batches.
Fact: Monitoring systems equipped with IoT technology enable remote access, allowing you to manage operations from anywhere.
Automated Process Management
Automation takes the efficiency of industrial mixers to the next level. Automated systems handle tasks like adjusting mixing speeds, adding ingredients, and maintaining environmental conditions. This reduces manual intervention, minimizes errors, and boosts productivity.
Pro Tip: Automated mixing technology not only saves time but also ensures repeatable results, which is crucial for meeting industry standards.
By integrating these features into your operations, you enhance safety, durability, and efficiency. Chemical mixing tanks equipped with advanced safety mechanisms, durable materials, and cutting-edge monitoring systems provide unmatched reliability. These attributes make them an essential investment for any industry aiming to optimize performance and maintain high-quality standards.
Consequences of Ineffective Use or Absence of Chemical Mix Tanks
Risks to Product Quality and Consistency
The absence or improper use of chemical mixing tanks can severely impact the quality and consistency of your products. Without these tanks, achieving uniform blending becomes nearly impossible. Variations in the mixture can lead to uneven distribution of ingredients, which compromises the final product. For instance, in industries like pharmaceuticals or food production, even minor inconsistencies can render a product ineffective or unsafe for consumption.
Cross-contamination is another significant risk. When incompatible substances are mixed in a poorly maintained tank, residue from previous batches can contaminate the new mixture. This not only affects the efficacy of the product but also damages your reputation. A real-world example highlights this issue: residue left in tanks caused by improper cleaning led to cross-contamination, resulting in unusable products and financial losses.
Fact: Consistent product quality builds customer trust and ensures compliance with industry standards. Neglecting proper mixing practices jeopardizes both.
By using chemical mixing tanks equipped with advanced safety features, you can maintain product uniformity and avoid costly recalls or rejections. These tanks provide the controlled environment necessary to meet stringent quality requirements.
Increased Safety Hazards in Operations
Operating without chemical mixing tanks or using them ineffectively increases safety risks in your facility. Poorly designed or outdated equipment lacks essential safety features like pressure relief systems and leak-proof designs. This creates a hazardous environment, especially when handling volatile or corrosive substances.
For example, corrosion in storage tanks has led to severe damage, including the failure of tank bottom plates. Such incidents not only result in inventory loss but also pose significant risks to workers and the surrounding environment. Without proper safety mechanisms, the likelihood of chemical spills, leaks, or even explosions rises dramatically.
Pro Tip: Regular maintenance and inspection of your mixing tanks can prevent accidents and ensure long-term operational safety.
Chemical mixing tanks with modern safety features mitigate these risks. Leak-proof designs prevent spills, while pressure relief systems handle unexpected pressure build-ups. These features protect your workforce and reduce the environmental impact of your operations.
Higher Operational Costs and Inefficiencies
Inefficient mixing processes lead to higher operational costs. Without chemical mixing tanks, you rely on manual labor or outdated methods, which consume more time and resources. This inefficiency slows down production and increases labor expenses, making it harder to meet deadlines or scale operations.
Material waste is another consequence. Inaccurate mixing results in overuse or spillage of raw materials, driving up costs. For instance, when tanks fail to blend substances properly, you may need to discard entire batches, wasting valuable resources. Additionally, equipment failures caused by corrosion or poor maintenance can halt production, leading to costly downtime.
Fact: The failure of four aboveground storage tanks due to corrosion caused significant financial losses and operational delays.
Investing in high-performance chemical mixing tanks reduces these inefficiencies. These tanks automate blending processes, ensuring precise mixing and minimizing waste. By optimizing your operations, you save time, reduce costs, and improve overall productivity.
Innovations and Future Trends in Industrial Mixing
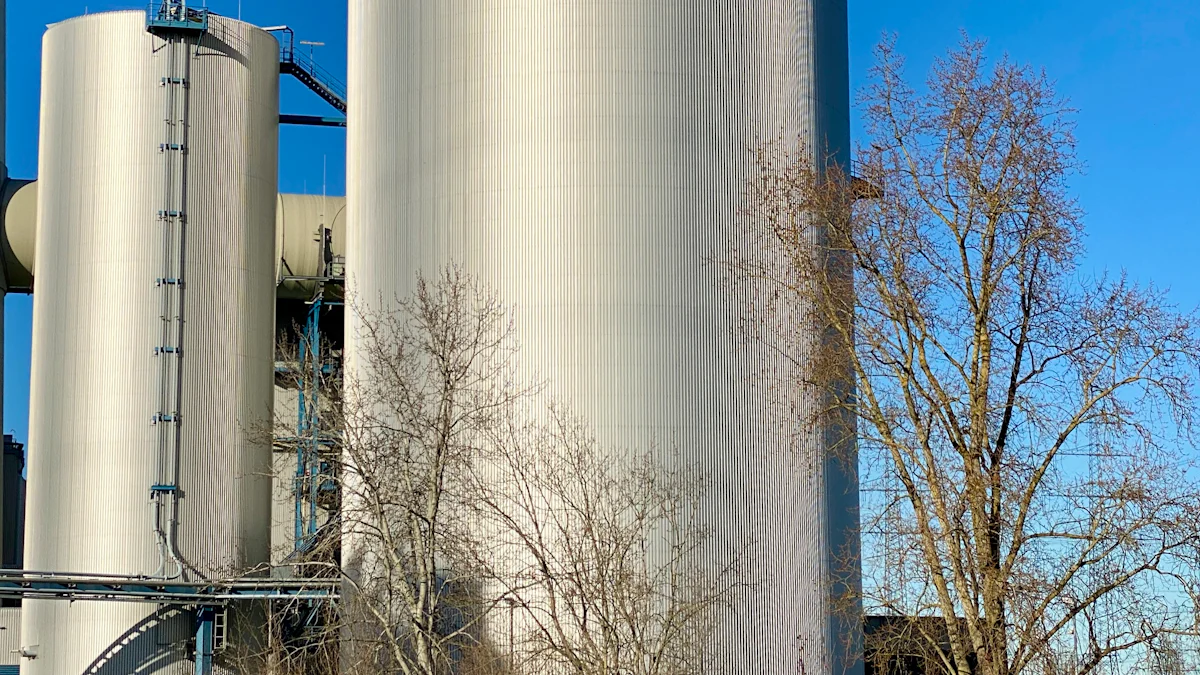
The field of industrial mixing continues to evolve, driven by technological advancements and the growing demand for sustainable and efficient solutions. These innovations not only enhance the performance of mixers but also address critical challenges such as energy consumption, environmental impact, and industry-specific requirements. Below, we explore the key trends shaping the future of industrial mixing.
Adoption of IoT and Smart Technologies
The integration of IoT and smart technologies into chemical mixing tanks is revolutionizing the way you manage and monitor your processes. IoT-enabled mixers provide real-time data on variables such as temperature, pressure, and mixing speed. This allows you to make immediate adjustments, ensuring optimal performance and reducing the risk of errors.
Fact: IoT-enabled mixing tanks improve process traceability, helping you maintain compliance with industry standards and regulations.
Smart monitoring systems also enhance efficiency by identifying potential issues before they escalate. For example, predictive maintenance features can alert you to wear and tear in your equipment, preventing costly downtime. These systems not only save time but also extend the lifespan of your mixing tanks.
Pro Tip: Incorporating IoT technology into your operations can reduce downtime and improve overall productivity, giving you a competitive edge in the market.
By adopting these advanced technologies, you can streamline your operations, enhance safety, and achieve higher levels of precision in your mixing processes.
Development of Sustainable and Eco-Friendly Designs
Sustainability is becoming a top priority in industrial mixing. Manufacturers are now focusing on creating eco-friendly designs that minimize environmental impact while maintaining high performance. For instance, self-cleaning mixing tanks reduce water and chemical usage during cleaning processes, making them an environmentally responsible choice.
Did you know? The use of environmentally friendly materials in mixing tanks not only reduces waste but also ensures compliance with stringent environmental regulations.
Energy-efficient mixers are another significant innovation. These mixers optimize energy consumption without compromising on performance, helping you lower operational costs and reduce your carbon footprint. Additionally, advancements in mixing technology, such as the integration of AI and machine learning, enable you to optimize performance and achieve better results with fewer resources.
Fact: Energy-efficient mixing tanks are particularly beneficial in industries like food production and pharmaceuticals, where sustainability and cost-effectiveness are critical.
By investing in sustainable designs, you contribute to environmental conservation while improving the efficiency and profitability of your operations.
Customization for Industry-Specific Needs
Every industry has unique requirements, and the ability to customize mixing tanks to meet these needs is a game-changer. Custom-designed mixers allow you to address specific challenges, such as handling highly reactive chemicals or achieving precise blending for complex formulations.
Example: In the cosmetics industry, custom mixing tanks are used to create products with specific textures and consistencies, ensuring customer satisfaction.
Customization also extends to the integration of advanced features like automated monitoring systems and IoT sensors. These additions enable you to tailor your equipment to your operational needs, enhancing both efficiency and reliability. For industries with strict regulatory guidelines, customized tanks ensure compliance while optimizing performance.
Pro Tip: Collaborate with manufacturers who offer tailored solutions to maximize the effectiveness of your mixing equipment.
By choosing customized solutions, you can overcome industry-specific challenges, improve product quality, and maintain a competitive edge in your market.
How to Choose the Right Chemical Mix Tank for Your Industry
Selecting the right chemical mix tank is a critical decision that directly impacts your operational efficiency, product quality, and long-term costs. With various options available, understanding the key factors can help you make an informed choice tailored to your industry’s specific needs. Below, we break down the essential considerations to guide your selection process.
Assessing Material Compatibility and Durability
The materials used in a chemical mix tank determine its ability to handle specific substances and withstand challenging conditions. You must evaluate the chemical compatibility of the tank material with the substances you plan to mix. For instance, corrosive chemicals require tanks made from corrosion-resistant materials like stainless steel or specialized plastics. These materials ensure the tank remains functional and safe over time.
Durability is another crucial factor. Tanks exposed to high temperatures or pressure during the mixing process need materials that can endure such conditions without compromising structural integrity. Stainless steel, for example, offers excellent durability and high-temperature tolerance, making it a popular choice for industries like pharmaceuticals and food production.
Pro Tip: Always match the tank material to the chemical properties of your substances. This prevents degradation, extends the tank’s lifespan, and ensures consistent performance.
Evaluating Capacity and Size Requirements
The size and capacity of your chemical mix tank should align with your production needs. Tanks that are too small may lead to inefficiencies, while oversized tanks can result in unnecessary costs. Start by assessing the volume of substances you need to mix in a single batch. Consider the space available in your facility to ensure the tank fits seamlessly into your operations.
For industries requiring frequent production scaling, flexibility in capacity becomes essential. Custom-designed tanks can address these needs by offering adjustable features or modular designs. This adaptability ensures your tank remains relevant as your production demands evolve.
Fact: Proper sizing not only optimizes the mixing process but also reduces energy consumption, making your operations more cost-effective.
Considering Maintenance and Long-Term Costs
Maintenance plays a significant role in the overall cost of owning a chemical mix tank. Tanks with complex designs or hard-to-reach areas can increase maintenance efforts and downtime. Look for tanks with accessible access points for cleaning and inspection. Features like self-cleaning mechanisms can further simplify maintenance, saving you time and labor costs.
Long-term costs extend beyond maintenance. Energy efficiency, material longevity, and repair frequency all contribute to the total cost of ownership. Investing in a high-quality tank with advanced features may have a higher upfront cost but can save you money in the long run by reducing operational inefficiencies and extending the tank’s lifespan.
Did you know? Tanks with advanced monitoring systems can alert you to potential issues, allowing you to address them before they escalate into costly repairs.
By carefully considering material compatibility, capacity, and maintenance requirements, you can select a chemical mix tank that meets your industry’s unique demands. This thoughtful approach ensures optimal performance, safety, and cost-efficiency in your operations.
Chenma Machinery Co., Ltd.: A Leader in Chemical Mixing Tanks
Expertise in Stainless Steel Tank Manufacturing
Chenma Machinery Co., Ltd. stands out as a trusted name in the manufacturing of stainless steel tanks. With a focus on precision and durability, the company produces tanks that meet the rigorous demands of modern industries. Stainless steel, known for its corrosion resistance and strength, forms the backbone of their designs. This material ensures that the tanks can handle harsh chemicals, high temperatures, and demanding operational conditions without compromising performance.
The company operates a state-of-the-art production facility spanning 20,000 square meters. Over 200 skilled professionals work with advanced machinery to create tanks that meet even the most complex technical requirements. Whether you need a standard tank or a custom solution, Chenma’s expertise ensures that every product delivers exceptional quality and reliability. Their stainless steel tanks are widely used in industries such as pharmaceuticals, food and beverage, and chemical manufacturing, where hygiene, safety, and durability are critical.
Fact: Stainless steel tanks from Chenma are easy to clean and maintain, making them ideal for industries with strict hygiene standards, such as food production and healthcare.
Customization and Turnkey Solutions for Industries
Chenma Machinery Co., Ltd. excels in providing tailored solutions to meet the unique needs of various industries. Their engineering team collaborates closely with clients to design and manufacture tanks that align with specific operational requirements. Whether you need a tank for blending delicate pharmaceutical ingredients or mixing high-viscosity adhesives, Chenma offers customized designs that ensure optimal performance.
The company also provides comprehensive turnkey solutions. These include process design, equipment manufacturing, installation, commissioning, and technical training. By offering end-to-end services, Chenma simplifies the integration of industrial mixing systems into your operations. This approach saves you time and ensures that every aspect of the project meets your expectations.
Pro Tip: Custom-designed tanks from Chenma can incorporate advanced features like automated mixers or IoT-enabled monitoring systems, giving you greater control over your processes.
Chenma’s ability to adapt its products to industry-specific challenges makes it a preferred partner for businesses in sectors like alcohol production, water treatment, and chemical manufacturing. Their commitment to customization ensures that you receive a solution tailored to your exact needs.
Commitment to Quality, Safety, and Innovation
Quality and safety are at the core of Chenma Machinery Co., Ltd.’s operations. The company adheres to the latest safety and quality standards, including ISO9001-2005, ISO14001-2015, and EU CE certifications. These certifications reflect their dedication to producing tanks that meet stringent regulatory requirements while ensuring safe and efficient operations.
Chenma’s focus on innovation drives the development of cutting-edge industrial mixing solutions. Their tanks integrate advanced safety mechanisms, such as pressure relief systems and leak-proof designs, to minimize risks during operation. Additionally, the company invests in research and development to incorporate the latest technologies, such as IoT-enabled monitoring and automated process management, into their products.
Did you know? Chenma’s innovative designs not only enhance safety but also improve efficiency by reducing downtime and maintenance needs.
By choosing Chenma Machinery Co., Ltd., you gain access to a partner committed to delivering high-quality, innovative, and safe solutions. Their expertise, customization capabilities, and focus on excellence make them a leader in the chemical mix tank industry.
Chemical mix tanks serve as the backbone of modern industrial processes, ensuring precision, safety, and efficiency. Their ability to blend substances with accuracy makes them indispensable for maintaining product quality across industries like pharmaceuticals, food production, and water treatment. These tanks not only enhance production consistency but also support environmental protection through advanced safety features and sustainable designs. With innovations such as IoT integration and energy-efficient systems, chemical mix tanks continue to drive industrial progress. Companies like Chenma Machinery Co., Ltd. lead the way by offering high-quality, customized solutions tailored to meet diverse industry needs.
FAQ
What is the purpose of a mixing tank?
A mixing tank, also called a blending tank or stirring vessel, serves to mix, emulsify, homogenize, or blend various materials. These tanks are essential in industries like chemical processing, pharmaceuticals, food and beverages, cosmetics, and water treatment. Their primary goal is to ensure uniform mixing of liquids, solids, or gases, which helps achieve the desired product quality or process outcomes.
Key Insight: Mixing tanks play a vital role in creating consistent products, whether it’s a pharmaceutical solution, a food ingredient, or a cosmetic cream.
What are the primary safety considerations when designing chemical mixing tanks?
Safety is a top priority when designing chemical mixing tanks. Key considerations include incorporating pressure relief systems, leak-proof designs, and corrosion-resistant materials. These features protect workers and the environment from potential hazards like chemical spills, pressure build-ups, or material degradation. Regular maintenance and inspections further enhance safety.
Pro Tip: Always choose tanks with advanced safety mechanisms to minimize risks and ensure compliance with industry standards.
What is a mixing tank?
A mixing tank is a piece of industrial equipment used to combine multiple liquid components into a uniform mixture. These tanks often feature separate inputs for each material and output piping to move the mixture to the next stage of production. They are indispensable in processes requiring precise blending to create new compounds or products.
Fact: Mixing tanks are widely used in industries like chemical manufacturing, where accuracy and consistency are critical.
What is the working capacity of a mixing tank?
The working capacity of a mixing tank can vary widely based on your needs. Common capacities include 50 gallons, 100 gallons, 200 gallons, 300 gallons, and even larger sizes like 1,000 or 2,000 gallons. The agitator or configuration inside the tank will differ depending on the specific process requirements.
Did you know? Customizing the capacity of your mixing tank ensures it aligns perfectly with your production scale and operational goals.
How do mixing tanks ensure product consistency?
Mixing tanks use advanced agitators and controlled environments to blend substances uniformly. This eliminates variations in the mixture, ensuring every batch meets the same high standards. Consistency is especially important in industries like food production and pharmaceuticals, where even minor deviations can affect safety or quality.
Pro Tip: Investing in high-quality mixing tanks helps you maintain product uniformity and build trust with your customers.
What materials are commonly used to manufacture mixing tanks?
Mixing tanks are typically made from materials like stainless steel or polyethylene. Stainless steel offers excellent corrosion resistance, durability, and high-temperature tolerance, making it ideal for demanding applications. Polyethylene provides a lightweight and cost-effective option for less aggressive substances.
Fact: Stainless steel tanks are preferred in industries with strict hygiene standards, such as food and beverage production.
Can mixing tanks be customized for specific industrial needs?
Yes, mixing tanks can be customized to meet unique operational requirements. Customization options include selecting specific materials, adjusting tank size, and integrating advanced features like automated mixers or IoT-enabled monitoring systems. These tailored solutions ensure optimal performance for specialized processes.
Example: In the cosmetics industry, custom-designed tanks help achieve precise textures and consistencies for creams and lotions.
How do mixing tanks contribute to operational efficiency?
Mixing tanks automate blending processes, reducing the need for manual labor and minimizing material waste. Their precise mixing capabilities ensure efficient use of raw materials, saving time and resources. Additionally, advanced features like real-time monitoring systems optimize performance and reduce downtime.
Did you know? Efficient mixing tanks can significantly lower production costs while maintaining superior product quality.
Why are mixing tanks essential in water treatment?
In water treatment facilities, mixing tanks prepare and distribute treatment chemicals like coagulants, disinfectants, and pH adjusters. These tanks ensure thorough mixing, which is crucial for producing clean and safe water. Their robust design allows them to handle corrosive substances effectively.
Pro Tip: Polyethylene tanks are often used in water treatment due to their chemical resistance and affordability.
How do I choose the right mixing tank for my industry?
To select the right mixing tank, consider factors like material compatibility, capacity, and maintenance requirements. Match the tank material to the chemicals you’ll handle to prevent degradation. Ensure the tank size aligns with your production needs. Look for features like easy access for cleaning and advanced monitoring systems to simplify maintenance.
Fact: Choosing the right tank enhances efficiency, reduces long-term costs, and ensures consistent product quality.