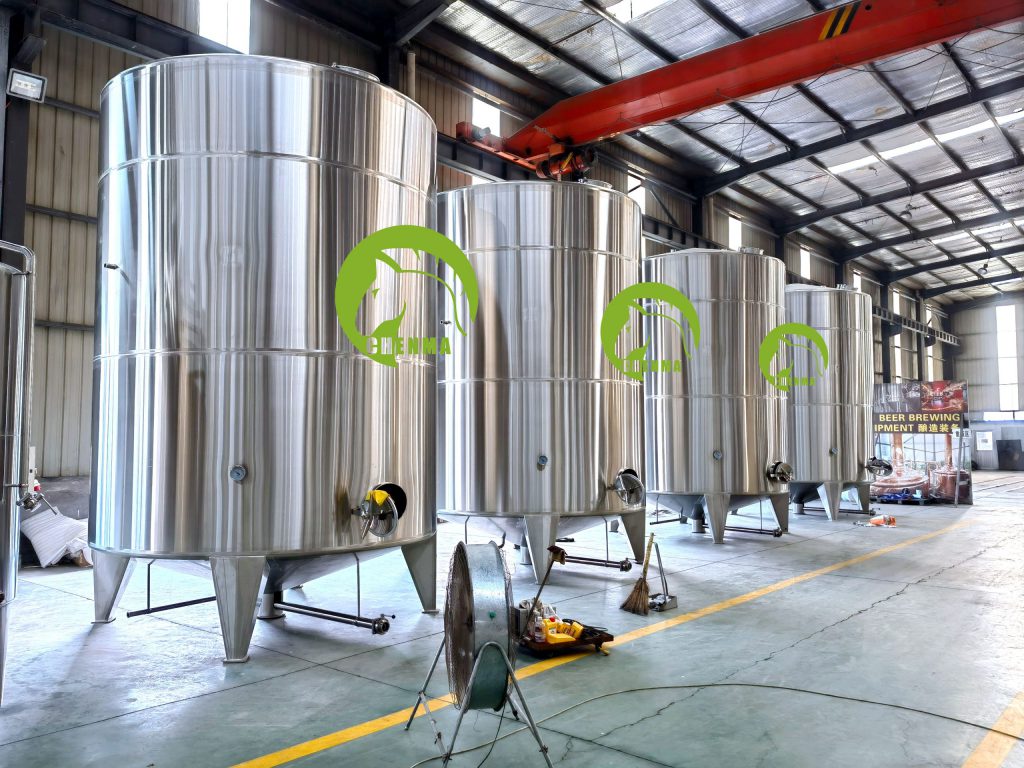
Mixer tank chemical applications demand materials with exceptional properties to ensure safety, durability, and operational efficiency. Selecting the right material for a mixing tank involves addressing critical challenges. The material must exhibit chemical compatibility to prevent corrosion and contamination when blending chemicals. It should also endure the pressure and temperature conditions required by the chemical industry. Commonly used materials include stainless steel, carbon steel, polyethylene, polypropylene, and fiberglass-reinforced plastic. Stainless steel, in particular, stands out for its strength and resistance to harsh environments, making it a preferred choice for mixing vessels in various industries.
Chenma is one of the professional stainless steel mixing tank manufacturers that can provide various stain steel tank solutions.
Overview of Materials Used in Mixing Tanks
Stainless Steel
Stainless steel is one of the most widely used materials in mixing tanks due to its exceptional properties. It offers excellent corrosion resistance, making it suitable for handling a wide range of chemicals. The material’s high strength and durability ensure long-term performance, even under demanding conditions. Stainless steel is also easy to clean, which prevents contamination and supports hygiene standards in industries like food processing and pharmaceuticals.
Two common grades of stainless steel used in mixing tanks are 304 and 316. Grade 304 is a versatile option with good anti-corrosion properties, while grade 316 is ideal for chemical mixing tanks as it tolerates higher concentrations of chemicals and elevated temperatures. These qualities make stainless steel a preferred choice for blending applications in the chemical industry and beyond.
| Stainless Steel Type | Application | |———————-|————————————————————————————————| | 304 | Universal use in engineering for tanks, good anti-corrosion properties. | | 316 | Ideal for chemical mixing tanks, tolerates higher concentrations of chemicals and temperatures. |
Carbon Steel
Carbon steel is another material commonly used in mixing tanks, particularly for general industrial applications. It is known for its high strength and relatively low cost, making it an economical choice for many projects. However, carbon steel requires proper maintenance to prevent rust and corrosion, especially when exposed to moisture or aggressive chemicals.
This material is often used in applications like paint mixing, water treatment, and other processes where cost-effectiveness is a priority. While it lacks the corrosion resistance of stainless steel, its strength and affordability make it a practical option for less demanding environments.
| Material Type | Key Properties | Common Applications | |—————|————————————|—————————————————–| | Carbon Steel | High strength, low cost | General industrial applications like paint and water treatment |
Polyethylene (PE)
Polyethylene (PE) is a lightweight and cost-effective material used in mixing tanks for specific chemical applications. It exhibits excellent corrosion resistance and is non-conductive, making it suitable for handling acidic and alkaline chemicals. Its affordability and ease of manufacturing make it a popular choice for small-scale tank mixing systems.
However, polyethylene is generally used for lighter industrial applications due to its lower strength compared to metals. It is ideal for blending chemicals in environments where weight and cost are critical considerations.
| Material | Key Properties | |——————————|—————————————————————————————————-| | Polyethylene (PE) | Lightweight, corrosion resistance, non-conductive, low cost. |
The variety of materials available allows industries to select the most suitable option for their specific needs. Each material offers unique advantages, ensuring that mixing tanks meet the demands of diverse applications in the chemical industry.
Polypropylene (PP)
Polypropylene (PP) is a versatile material widely used in mixing tanks for its unique properties. It offers excellent chemical resistance, making it suitable for handling a variety of chemicals, including acids, bases, and organic solvents. This property ensures that polypropylene tanks maintain their structural integrity when exposed to aggressive substances, which is critical in the chemical industry.
One of the standout features of polypropylene is its lightweight nature. This characteristic simplifies transportation and installation, especially in tank mixing systems where mobility or modularity is required. Additionally, polypropylene is cost-effective, making it an attractive option for projects with budget constraints. Its affordability does not compromise its performance, as it remains durable under normal operating conditions.
Polypropylene also exhibits good thermal resistance, allowing it to withstand moderate temperature variations. This makes it suitable for blending applications that involve slightly elevated temperatures. However, it is not recommended for high-temperature environments, as prolonged exposure to extreme heat can weaken the material.
Industries often use polypropylene in applications such as water treatment, chemical storage, and low-pressure mixing tank systems. Its non-reactive surface minimizes the risk of contamination, which is essential for maintaining the purity of the chemicals being processed. While it may not match the strength of stainless steel, polypropylene remains a reliable choice for less demanding applications.
Fiberglass-Reinforced Plastic (FRP)
Fiberglass-Reinforced Plastic (FRP) combines the strength of fiberglass with the corrosion resistance of plastic, creating a robust material for mixing tanks. FRP is particularly valued for its lightweight yet durable construction, which makes it ideal for applications requiring portability or weight-sensitive designs.
FRP excels in environments where corrosion resistance is paramount. It can handle exposure to harsh chemicals, including acids, alkalis, and oxidizing agents, without degrading. This makes it a preferred material for mixer tank chemical applications in industries such as wastewater treatment, chemical processing, and marine operations.
Another advantage of FRP is its ability to withstand extreme environmental conditions. It performs well in both high and low temperatures, maintaining its structural integrity under thermal stress. Additionally, FRP offers excellent resistance to UV radiation, making it suitable for outdoor installations.
The material’s versatility extends to its design flexibility. Manufacturers can mold FRP into complex shapes, allowing for customized mixing tank designs tailored to specific industrial needs. This adaptability ensures that FRP tanks meet the unique requirements of various tank mixing systems.
Despite its many advantages, FRP is often chosen for applications where its lightweight and corrosion-resistant properties outweigh the need for high tensile strength. It provides a cost-effective alternative to metals like stainless steel while delivering reliable performance in demanding chemical environments.
Properties and Advantages of Stainless Steel in Mixer Tank Chemical Applications
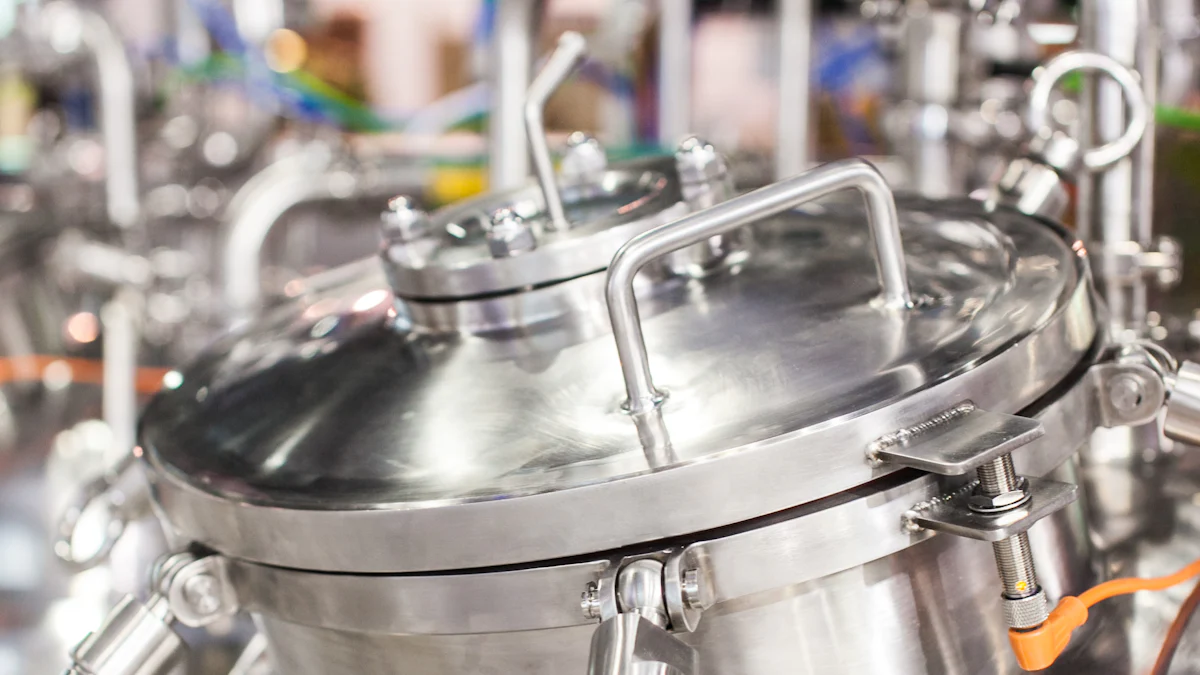
Corrosion Resistance
Stainless steel offers unparalleled corrosion resistance, making it an ideal material for mixing tanks in the chemical industry. Its ability to withstand aggressive agents ensures long-term performance in environments where other materials may fail. Grades like 304 and 316 are widely used due to their resistance to a broad spectrum of chemicals. For more demanding applications, high-alloy grades such as 904L and duplex stainless steels provide enhanced protection.
The secret to stainless steel’s corrosion resistance lies in its unique passivation layer. This microscopically thin film, composed of chromium oxide, forms naturally when the material is exposed to oxygen. The layer is self-repairing, which means it can regenerate if damaged, ensuring continuous protection. This feature guards against various types of corrosion, including stress corrosion cracking and galvanic corrosion, making stainless steel a reliable choice for mixer tank chemical applications.
Durability and Strength
Stainless steel stands out for its exceptional durability and strength, outperforming materials like plastic, rubber, or glass in demanding environments. Its robust construction allows it to endure the rigors of daily use, particularly in industries like beverage production. Stainless steel mixing tanks resist rust and corrosion, ensuring a longer lifespan compared to other materials.
The material’s impact resistance makes it suitable for applications requiring high mechanical strength. Manufacturers benefit from its longevity, as stainless steel mixing tanks minimize the need for frequent repairs or replacements. This durability translates into cost savings over time, making stainless steel a practical and economical choice for blending operations.
Suitability for Food and Beverage Applications
Stainless steel is a preferred material for mixing tanks in the food and beverage industry due to its hygienic properties. Its non-porous surface prevents the absorption of chemicals or contaminants, ensuring the purity of the products being processed. The material is easy to clean, which supports strict sanitation standards required in food and beverage production.
Additionally, stainless steel exhibits excellent compatibility with a wide range of food-grade chemicals used in processing. Its resistance to corrosion ensures that no unwanted reactions occur during blending, preserving the quality and safety of the final product. These attributes make stainless steel mixing tanks indispensable in industries where hygiene and product integrity are paramount.
The Role of Plastics in Tank Mixing Systems
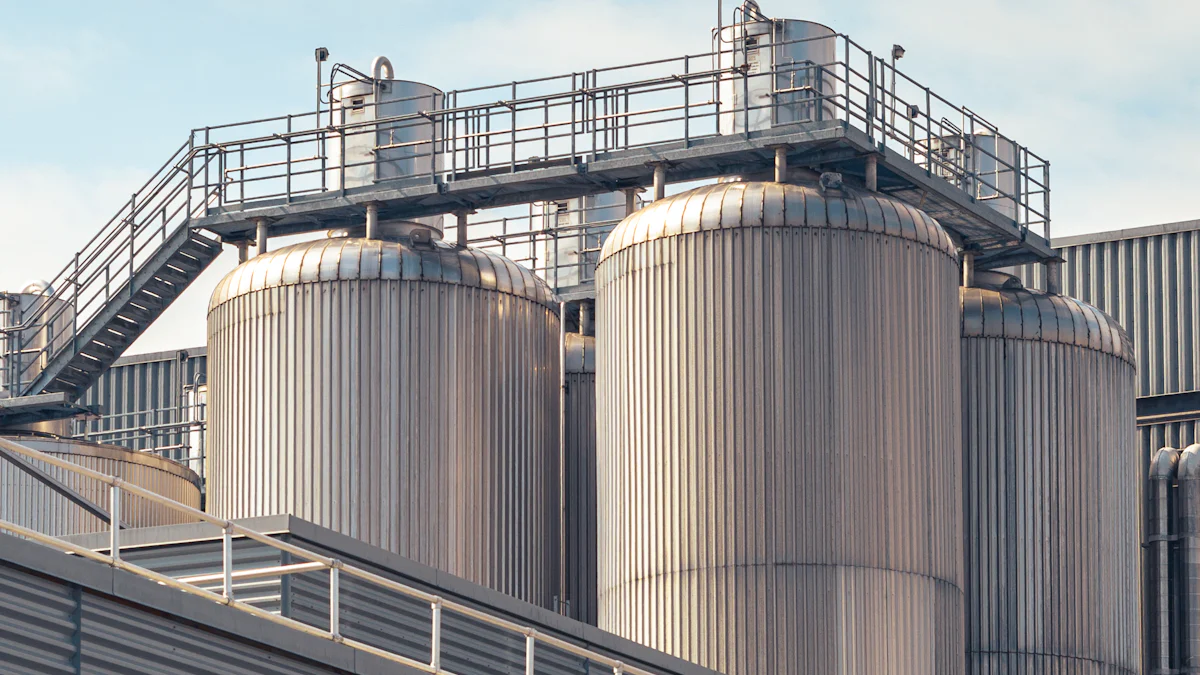
Polyethylene (PE) for Chemical Compatibility
Polyethylene (PE) plays a vital role in mixing tanks due to its excellent chemical compatibility. This material resists corrosion when exposed to a wide range of chemicals, including acids and alkalis. Its non-conductive nature further enhances its suitability for environments where electrical conductivity could pose risks. Industries often rely on polyethylene for blending processes that require lightweight and cost-effective solutions.
PE’s affordability and ease of manufacturing make it a popular choice for small-scale chemical mixing systems. Its lightweight properties simplify transportation and installation, reducing operational costs. While polyethylene excels in handling many chemicals, it is best suited for applications with moderate temperature and pressure requirements. This ensures the material maintains its structural integrity during use.
Polypropylene (PP) for Lightweight and Cost-Effectiveness
Polypropylene (PP) offers a unique combination of lightweight construction and cost-effectiveness, making it a preferred material for mixing tanks in budget-conscious projects. Its chemical resistance allows it to handle a variety of substances, including acids, bases, and organic solvents. This versatility ensures polypropylene tanks perform reliably in diverse chemical industry applications.
The material’s lightweight nature simplifies installation and enhances portability, especially in modular chemical mixing systems. Additionally, polypropylene exhibits good thermal resistance, enabling it to withstand moderate temperature variations during blending operations. However, it is not recommended for high-temperature environments, as prolonged exposure to extreme heat can compromise its durability.
Limitations of Plastic Materials
Despite their advantages, plastic materials like polyethylene and polypropylene have limitations in high-temperature or high-pressure applications. Certain plastics may react with specific chemicals, heat, or pressure, necessitating careful material selection tailored to the intended use. For instance, while plastic tanks can handle many chemicals, they may fail when exposed to high-temperature compounds.
These limitations highlight the importance of understanding the operational conditions of mixing tanks. In demanding environments, materials like stainless steel may offer better performance and longevity. However, for less rigorous applications, plastics remain a cost-effective and practical choice.
Factors to Consider When Choosing a Material for Mixing Tanks
Chemical Compatibility
The chemical compatibility of a material plays a critical role in determining its suitability for mixing tanks. Each chemical used in the blending process interacts differently with materials, making it essential to select one that can withstand the specific properties of the substances involved. For example, acidic chemicals require materials with high corrosion resistance to prevent degradation. Similarly, alkaline or oxidizing agents demand materials that maintain structural integrity under prolonged exposure.
Industries like food processing and pharmaceuticals often prioritize hygiene when selecting materials. Non-reactive surfaces, such as those found in stainless steel, ensure that no contamination occurs during blending. Additionally, the material must align with the operational requirements of the chemical industry, including the ability to handle varying chemical concentrations without compromising performance.
Corrosion Resistance
Corrosion resistance is another vital factor when choosing materials for mixing tanks. Corrosion can weaken the tank’s structure, leading to leaks, contamination, or even equipment failure. Stainless steel, particularly grades like 316, offers exceptional corrosion resistance, making it a preferred choice for mixer tank chemical applications. Its self-repairing chromium oxide layer protects against chemical-induced wear, ensuring long-term durability.
Plastic materials, such as polyethylene and polypropylene, also provide excellent resistance to corrosion. These materials are ideal for handling chemicals like acids and alkalis in less demanding environments. However, for high-corrosion scenarios, stainless steel remains unmatched due to its ability to withstand aggressive agents without compromising safety or efficiency.
Temperature and Pressure Tolerance
Mixing tanks often operate under varying temperature and pressure conditions, making these factors crucial in material selection. Materials like stainless steel excel in high-temperature environments, maintaining their strength and durability even under thermal stress. This makes them suitable for blending operations involving elevated temperatures or pressurized systems.
Plastics, including polyethylene and polypropylene, perform well in moderate temperature ranges but may degrade under extreme heat or pressure. Fiberglass-reinforced plastic offers a middle ground, providing good thermal resistance while remaining lightweight. Selecting a material that aligns with the operational demands ensures the mixing tank performs reliably and safely in the chemical industry.
Cost and Budget Considerations
Cost plays a pivotal role in selecting materials for mixing tanks. Industries often balance performance requirements with budget constraints to ensure cost-effective solutions without compromising safety or efficiency. Each material offers unique advantages and price points, making it essential to evaluate options based on the specific needs of the application.
Stainless steel, known for its durability and corrosion resistance, often represents a higher upfront investment. However, its long lifespan and minimal maintenance requirements make it a cost-effective choice over time. Industries like the chemical industry frequently choose stainless steel for mixing tanks due to its ability to handle aggressive chemicals and high temperatures. This durability reduces the need for frequent replacements, saving costs in the long term.
Plastic materials, such as polyethylene and polypropylene, provide a more affordable alternative for less demanding applications. These materials are lightweight and easy to manufacture, which lowers production and transportation costs. Polyethylene, for instance, is ideal for blending chemicals in environments with moderate temperature and pressure requirements. While these materials may not match the strength of metals, their affordability makes them suitable for budget-sensitive projects.
Fiberglass-reinforced plastic (FRP) offers a middle ground between cost and performance. Its lightweight construction and corrosion resistance make it a practical option for industries requiring portable or custom-designed mixing tanks. Although FRP may not provide the same tensile strength as stainless steel, it delivers reliable performance at a lower cost.
When selecting materials for mixer tank chemical applications, industries must consider both initial costs and long-term expenses. Factors like maintenance, lifespan, and operational efficiency significantly impact the overall budget. By carefully evaluating these aspects, businesses can choose materials that align with their financial and operational goals.
Applications of Mixing Tank Materials in the Chemical Industry
Stainless Steel for High-Corrosion Environments
Stainless steel plays a vital role in the chemical industry due to its exceptional resistance to corrosion. This material is particularly effective in environments where aggressive agents, such as acids and alkalis, are present. Grades like 304 and 316 are commonly used for manufacturing mixing tanks, pipes, and reactors. For more demanding applications, high-alloy grades, including 904L and duplex stainless steels, provide enhanced protection against chemical degradation.
Industries rely on stainless steel for its durability and versatility. It is frequently used in chemical storage tanks, pumps, and piping systems. Additionally, stainless steel is essential in filter and seamless pipe combinations, ensuring efficient and safe chemical processing. Its ability to maintain structural integrity under harsh conditions makes it a preferred choice for high-corrosion environments.
Polyethylene for Acidic and Alkaline Chemicals
Polyethylene offers a cost-effective solution for handling acidic and alkaline chemicals in mixing tanks. Its non-conductive and corrosion-resistant properties make it suitable for blending processes involving a wide range of chemicals. Industries often choose polyethylene for its lightweight nature, which simplifies transportation and installation.
This material is ideal for applications with moderate temperature and pressure requirements. Its affordability and ease of manufacturing make it a popular choice for small-scale mixing tanks for chemical industry applications. While polyethylene may not match the strength of metals, its chemical compatibility ensures reliable performance in less demanding environments.
Fiberglass-Reinforced Plastic for Lightweight Needs
Fiberglass-reinforced plastic (FRP) combines strength and corrosion resistance, making it an excellent choice for lightweight mixing tank applications. Its low weight makes it ideal for scenarios where portability or weight-sensitive designs are critical. FRP tank mixers and drum mixers enhance efficiency in chemical mixing processes.
FRP is compatible with various liquids, including corrosive chemicals, ensuring safe and effective blending. Its ability to withstand extreme environmental conditions, such as UV exposure and temperature fluctuations, further enhances its versatility. Industries often use FRP for custom-designed mixing tanks, as the material can be molded into complex shapes to meet specific requirements.
Comparing Materials for Specific Tank Mixing Systems
Handling Corrosive Chemicals
Corrosive chemicals demand materials that can resist degradation and maintain structural integrity over time. Stainless steel, particularly grades like 316, excels in such environments due to its superior corrosion resistance. Its chromium oxide layer protects against chemical reactions, ensuring durability in aggressive conditions. This makes it a preferred choice for mixing tanks in the chemical industry, where acids, alkalis, and oxidizing agents are frequently used.
Fiberglass-reinforced plastic (FRP) also performs well in handling corrosive substances. Its lightweight construction and resistance to chemical wear make it suitable for applications requiring portability or custom designs. Polyethylene and polypropylene offer cost-effective alternatives for less demanding environments. These plastics resist corrosion effectively but may not withstand prolonged exposure to highly aggressive chemicals. Selecting the right material ensures safety and efficiency in chemical processing operations.
High-Temperature Applications
High-temperature mixing tank applications require materials with excellent thermal stability and corrosion resistance. Stainless steel stands out in this regard. Grade 304 is widely used for its anti-corrosion properties, while grade 316 is specifically designed to endure higher temperatures and aggressive chemicals. This makes it ideal for industries like pharmaceuticals and cosmetics, where blending processes often involve elevated temperatures.
FRP provides moderate thermal resistance, making it a viable option for applications with fluctuating temperatures. However, plastics like polyethylene and polypropylene are less suitable for high-temperature environments. Prolonged exposure to heat can weaken these materials, compromising their performance. For operations requiring consistent thermal stability, stainless steel remains the most reliable choice.
Cost-Sensitive Projects
Cost-sensitive projects often prioritize affordability without compromising functionality. Polyethylene and polypropylene are popular choices for such scenarios. These materials are lightweight, easy to manufacture, and cost-effective, making them ideal for small-scale mixing tanks. Their chemical compatibility ensures reliable performance in environments with moderate temperature and pressure requirements.
FRP offers a balance between cost and performance. Its corrosion resistance and lightweight nature make it a practical option for industries requiring custom designs or portable mixing tanks. While stainless steel involves a higher initial investment, its durability and low maintenance costs make it a cost-effective solution in the long run. Evaluating both short-term and long-term expenses helps industries select the most suitable material for their budget.
Maintenance and Longevity of Mixing Tank Materials
Cleaning and Maintenance Best Practices
Proper cleaning and maintenance are essential for ensuring the longevity and efficiency of mixing tanks. Regular inspections help identify wear, leaks, or damage to seals and valves, preventing costly repairs. Routine checks also ensure agitators remain lubricated, which enhances mixing performance and extends their lifespan. Cleaning methods should align with the tank’s material to avoid damage or product contamination.
For stainless steel tanks, diluted phosphoric or citric acid effectively removes residues, followed by thorough rinsing to maintain hygiene. Plastic tanks, such as those made from polyethylene or polypropylene, benefit from mild detergents or specialized plastic cleaners. Fiberglass-reinforced plastic (FRP) tanks require acid-based cleaning products to preserve their structural integrity. Adhering to these practices minimizes degradation and ensures the tank remains suitable for blending chemicals in the chemical industry.
Preventing Corrosion and Wear
Corrosion poses a significant threat to mixing tanks, particularly in environments involving aggressive chemicals. Selecting the right materials, such as stainless steel, helps mitigate this risk. Stainless steel’s chromium oxide layer provides a natural barrier against corrosion, making it ideal for mixer tank chemical applications. For carbon steel tanks, applying anti-corrosion coatings or linings is crucial to prevent rust.
Plastic materials like polyethylene and polypropylene resist corrosion effectively but may degrade under extreme conditions. Regular cleaning and inspections further reduce the risk of wear. Ensuring proper storage conditions, such as maintaining stable temperatures and avoiding prolonged exposure to UV light, also protects the tank’s surface. These measures safeguard the tank’s structural integrity and prevent contamination during chemical blending.
Extending the Lifespan of Mixing Tanks
Extending the lifespan of mixing tanks requires a combination of proactive maintenance and material-specific care. Regular cleaning prevents residue buildup, which can weaken the tank over time. Inspections should focus on identifying early signs of wear, such as cracks or leaks, to address issues promptly. Lubricating moving parts, such as agitators, ensures smooth operation and reduces mechanical stress.
Choosing durable materials like stainless steel enhances the tank’s longevity. Its resistance to corrosion and wear makes it a reliable choice for demanding applications. For lighter applications, materials like FRP or polyethylene offer cost-effective solutions with proper care. Implementing these strategies ensures mixing tanks remain functional and efficient, reducing the need for frequent replacements and maintaining safety in the chemical industry.
Emerging Trends in Mixer Tank Chemical Materials
Advances in Composite Materials
Composite materials are revolutionizing the design of mixing tanks by combining strength, durability, and lightweight properties. These materials integrate advanced fibers and resins to create tanks that withstand harsh environments while remaining portable. For example, the Ross FDA-50 agitated pressure reactor exemplifies this innovation. It offers precise control over mixing, temperature, and pressure, making it suitable for applications involving composite materials. Its compact and portable design highlights the versatility of modern composites in the chemical industry.
Manufacturers are also exploring hybrid composites that blend fiberglass with other materials to enhance performance. These composites provide superior resistance to corrosion and wear, ensuring longevity in demanding chemical environments. The ability to mold these materials into complex shapes further supports customization, allowing industries to tailor mixing tanks to specific needs.
Sustainable and Eco-Friendly Options
Sustainability is becoming a priority in the development of mixing tanks. Industries are increasingly adopting environmentally friendly materials to reduce their ecological footprint. Recyclable materials, such as certain plastics and metals, are now being used to manufacture mixing tanks. These choices not only minimize waste but also align with global efforts to promote sustainability.
Low-friction materials are another innovation contributing to eco-friendly designs. By reducing energy requirements during blending, these materials enhance efficiency while lowering operational costs. This approach supports the chemical industry’s shift toward greener practices without compromising performance.
Innovations in Coatings and Linings
Coatings and linings play a critical role in extending the lifespan of mixing tanks. Recent advancements focus on enhancing chemical resistance and durability. Modern coatings can withstand exposure to aggressive chemicals, preventing corrosion and maintaining the structural integrity of the tank.
Self-healing coatings represent a significant breakthrough. These coatings repair minor damages automatically, reducing maintenance needs and ensuring continuous protection. Additionally, anti-microbial linings are gaining popularity in industries like food and beverage, where hygiene is paramount. These linings prevent bacterial growth, ensuring the safety and purity of the products being processed.
The integration of these innovations demonstrates the ongoing evolution of materials and technologies in mixer tank chemical applications. By adopting advanced composites, sustainable options, and cutting-edge coatings, industries can achieve greater efficiency and reliability in their operations.
Why Stainless Steel is a Preferred Choice for Mixing Tanks
Insights from Chenma Machinery
Chenma Machinery has established itself as a leader in manufacturing stainless steel mixing tanks. The company’s expertise lies in creating tanks tailored to the unique needs of industries like food, beverage, and the chemical industry. With a focus on innovation, Chenma Machinery designs stainless steel tanks that excel in durability, corrosion resistance, and hygiene. These qualities make them indispensable for blending chemicals and other substances in demanding environments.
Chenma Machinery’s production facility spans 20,000 square meters and employs over 200 skilled professionals. This scale allows the company to produce stainless steel mixing tanks that meet the highest industry standards. The use of advanced machinery ensures precision in every tank, whether it is a standard design or a custom-built solution. By prioritizing quality and adaptability, Chenma Machinery supports industries in achieving efficient and safe mixing processes.
Certifications and Quality Standards
Stainless steel mixing tanks must adhere to rigorous certifications and quality standards to ensure safety and reliability. Chenma Machinery manufactures tanks that comply with globally recognized certifications, including ISO9001-2005, ISO14001-2015, and EU CE standards. These certifications guarantee that the tanks meet stringent requirements for structural integrity, environmental management, and occupational safety.
Key design elements, such as wall thickness calculations and pressure relief valves, align with ASME standards. These features prevent failures under high stress and ensure safe operation in pressurized environments. Additionally, inspection points mandated by ASME standards facilitate regular maintenance. Testing protocols, including hydrostatic and leak testing, further validate the tanks’ performance. These measures underscore the reliability of stainless steel mixing tanks in critical applications.
Customization and Technical Support
Customization enhances the versatility of stainless steel mixing tanks, making them suitable for diverse industrial applications. Chenma Machinery offers highly customizable options, including variations in size, shape, fittings, and coatings. Industries can select materials like 304 or 316 stainless steel, depending on their specific requirements. For instance, 316 stainless steel is ideal for handling aggressive chemicals, while 304 is suitable for general-purpose blending.
Chenma Machinery’s technical support team works closely with clients to design tanks that meet their operational needs. This collaboration ensures that every tank integrates seamlessly into existing systems. By providing tailored solutions and expert guidance, Chenma Machinery helps industries optimize their mixing processes while maintaining safety and efficiency.
Selecting the right material for a mixing tank is crucial for ensuring safety, durability, and efficiency in the chemical industry. Factors such as process conditions, exposure types, design life, and cost must guide the decision. Each material—stainless steel, carbon steel, polyethylene, polypropylene, and FRP—offers unique advantages tailored to specific needs. For instance, stainless steel excels in corrosion resistance and durability, making it ideal for blending chemicals in demanding environments.
Chenma Machinery ensures the safety and efficiency of its stainless steel mixing tanks through rigorous design and manufacturing processes. Features like domed tops and conical bottoms enhance blending performance, while continuous quality control guarantees reliability. These tanks meet the highest standards, offering industries a dependable solution for their mixer tank chemical applications.
FAQ
What factors determine the best material for a mixing tank?
The choice of material depends on chemical compatibility, corrosion resistance, temperature and pressure tolerance, and budget. Industries must evaluate the chemicals involved, operating conditions, and long-term maintenance costs to select the most suitable material for their application.
Why is stainless steel preferred for mixing tanks?
Stainless steel offers unmatched corrosion resistance, durability, and hygiene. Its self-repairing chromium oxide layer ensures long-term performance in harsh environments. Additionally, it meets strict industry standards, making it ideal for food, beverage, and chemical applications.
Can plastic materials handle high-temperature applications?
Plastic materials like polyethylene and polypropylene perform well under moderate temperatures. However, they degrade under extreme heat. For high-temperature applications, stainless steel or fiberglass-reinforced plastic provides better thermal stability and reliability.
How does fiberglass-reinforced plastic (FRP) compare to stainless steel?
FRP is lightweight and corrosion-resistant, making it suitable for portable or custom designs. However, it lacks the tensile strength and thermal stability of stainless steel. FRP works best in less demanding environments, while stainless steel excels in high-stress applications.
What certifications should mixing tanks meet?
Mixing tanks should comply with certifications like ISO9001-2005, ISO14001-2015, and EU CE standards. These ensure structural integrity, environmental safety, and occupational health. Adherence to ASME standards further guarantees safe operation under pressure.