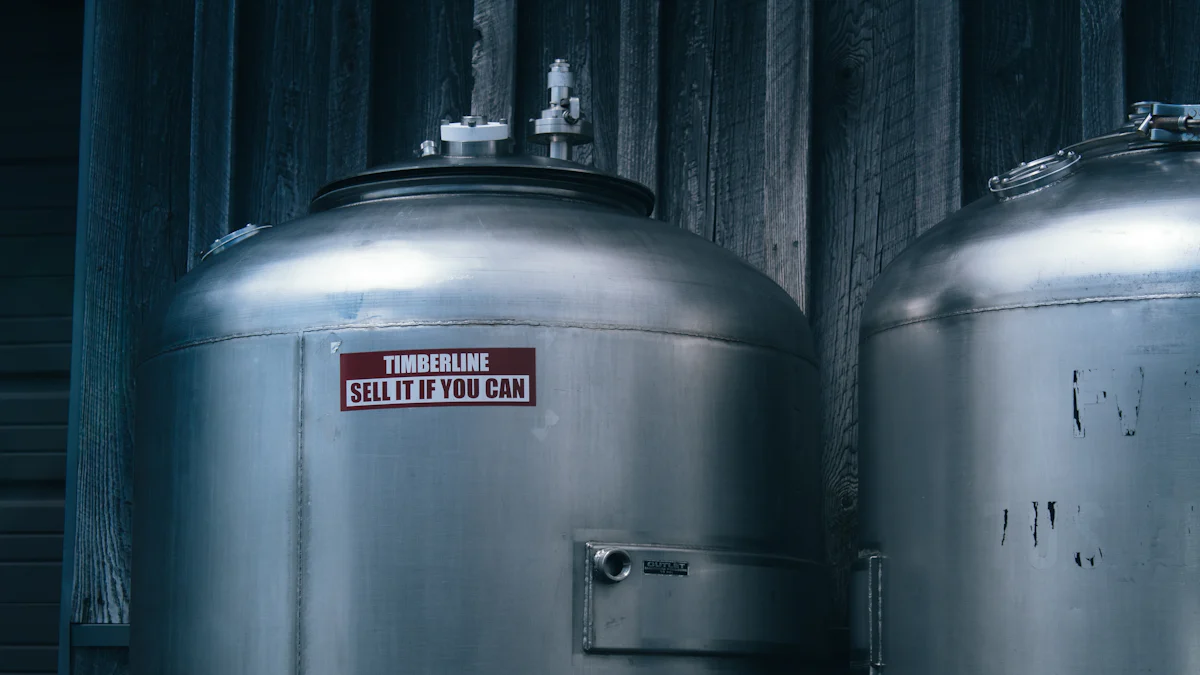
Safety should always come first when working with agricultural chemical mixing tanks. Improper handling can lead to severe consequences, including hazardous chemical reactions, environmental damage, and health risks. For instance, between 2001 and 2018, 262 chemical incidents in the U.S. caused 490 injuries and 10 fatalities. These numbers highlight the dangers of neglecting proper procedures. By following correct mixing practices, you not only protect yourself but also ensure effective pesticide application and compliance with safety standards. Proper handling safeguards the environment, enhances product performance, and minimizes risks during every step of the process.
Why Proper Chemical Mixing Matters
Proper chemical mixing plays a vital role in ensuring safety, efficiency, and effectiveness in agricultural practices. When you follow the correct procedures, you not only protect yourself but also maximize the performance of the chemicals you use. On the other hand, improper mixing can lead to serious consequences, including safety hazards, environmental damage, and financial losses.
Benefits of Proper Mixing
Proper mixing ensures that the chemicals are evenly distributed, which leads to consistent results. This consistency is crucial for achieving effective pesticide application. When the mixture is uniform, the pesticide works as intended, targeting pests without harming crops or the environment. Additionally, proper mixing reduces the need for reapplications, saving you time and money.
Another benefit is enhanced safety. By following the correct mixing order and using appropriate equipment, you minimize the risk of chemical reactions that could cause fires, explosions, or toxic fumes. Proper mixing also helps you comply with safety regulations, avoiding potential legal issues and fines.
Moreover, proper mixing improves efficiency. It reduces waste by ensuring that every drop of chemical is used effectively. This not only lowers costs but also minimizes the environmental impact of your agricultural practices. High-quality mixing also contributes to the stability of the chemical solution, ensuring it remains effective over time.
Risks of Improper Mixing
Improper mixing can have severe consequences. One major risk is uneven distribution of ingredients, which can lead to poor results. For example, if the pesticide is not mixed properly, some areas may receive too much, causing crop damage, while others may receive too little, leaving pests untreated. This inconsistency can force you to reapply the pesticide, increasing costs and labor.
Safety risks are another significant concern. Mixing incompatible chemicals can result in dangerous reactions, such as the release of toxic gases or even explosions. These incidents can harm you, your workers, and the surrounding environment. Improper mixing can also damage your equipment, leading to costly repairs or replacements.
Environmental harm is another critical issue. When chemicals are not mixed correctly, they may not bind properly to their target surfaces. This can result in runoff, contaminating nearby water sources and harming wildlife. Improper mixing also increases the likelihood of chemical waste, further impacting the environment.
Understanding Agricultural Chemical Mixing Tanks
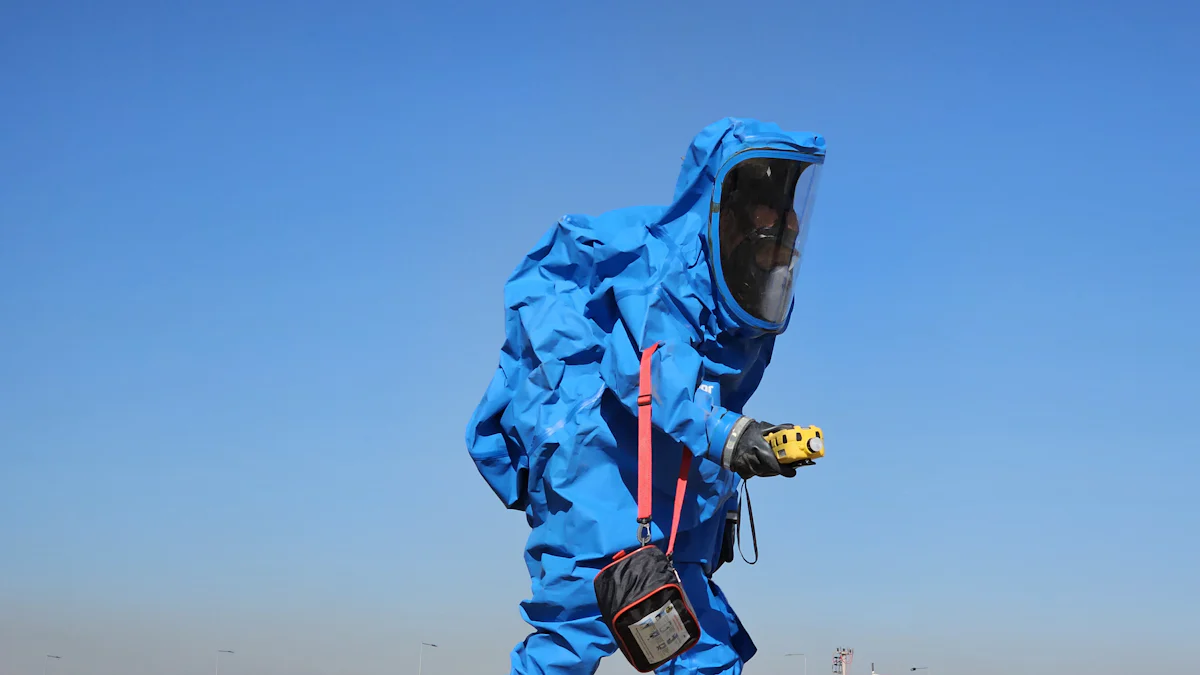
Agricultural chemical mixing tanks play a crucial role in ensuring the safe and effective preparation of chemical solutions for agricultural applications. These tanks are specifically designed to handle various chemicals, ensuring proper mixing and storage while maintaining safety and efficiency.
Features of Agricultural Chemical Mixing Tanks
Agricultural chemical mixing tanks come equipped with features that enhance their functionality and durability. Most tanks are constructed from materials like stainless steel, which is non-corrosive, non-oxidizing, and easy to clean. These properties make stainless steel an ideal choice for handling chemicals that may otherwise degrade other materials.
Many tanks are designed to accommodate liquids, powders, or even gases, making them versatile for different agricultural needs. They often include advanced mixing mechanisms, such as impellers or pumps, to ensure homogeneity in the chemical mixture. Some tanks also feature pressure-testing capabilities to handle high-pressure environments safely. These features not only improve the consistency of the mixture but also extend the lifespan of the tank.
Additionally, modern agricultural chemical mixing tanks are built with user-friendly designs. They may include clear measurement markings, easy-access openings, and secure sealing systems to prevent leaks or spills. These features simplify the mixing process and reduce the risk of accidents during operation.
Importance of Using High-Quality Tanks
Using high-quality tanks is essential for maintaining safety and achieving optimal results. High-grade tanks, such as those made from 304 or 316 stainless steel, resist corrosion and wear, ensuring long-term reliability. This durability minimizes the risk of chemical leaks, which could harm the environment or compromise your safety.
High-quality tanks also contribute to better mixing performance. Their robust construction supports advanced mixing systems, allowing you to achieve uniform chemical distribution. This consistency ensures that your agricultural chemicals perform as intended, reducing the need for reapplications and saving you time and resources.
Moreover, investing in high-quality tanks helps you comply with safety and environmental regulations. Tanks manufactured to meet strict quality standards undergo rigorous testing, ensuring they can handle the demands of agricultural chemical mixing. By using reliable equipment, you reduce the likelihood of accidents and demonstrate your commitment to responsible agricultural practices.
Chenma’s Expertise in Stainless Steel Tanks
When it comes to stainless steel tanks, Chenma stands out as a leader in the industry. With a state-of-the-art production facility and a team of over 200 skilled professionals, Chenma manufactures tanks that meet the highest safety and quality standards. Each tank undergoes meticulous design and fabrication processes, ensuring it meets the unique needs of its users.
Chenma’s stainless steel tanks are crafted from premium materials, offering exceptional durability and resistance to corrosion. These tanks are pressure-tested and subjected to continuous quality control measures, guaranteeing their reliability in demanding agricultural settings. Whether you need a standard tank or a custom solution, Chenma’s engineers can adapt designs to suit your specific requirements.
In addition to manufacturing high-quality tanks, Chenma provides comprehensive support services. From process design to technical training, Chenma ensures you have the knowledge and tools to use your tanks effectively. By choosing Chenma, you gain access to expertise that enhances the safety and efficiency of your agricultural chemical mixing operations.
Identifying and Addressing Chemical Compatibility Issues
Chemical compatibility is a critical factor when preparing mixtures in agricultural chemical mixing tanks. Understanding how different chemicals interact helps you prevent accidents, protect the environment, and ensure the effectiveness of your pesticide applications. Addressing compatibility issues requires careful attention to legal guidelines, chemical reactions, and physical challenges during mixing.
Legal Considerations
Legal regulations play a significant role in guiding safe chemical mixing practices. Agencies like the Environmental Protection Agency (EPA) mandate strict compliance with chemical handling and storage laws. These laws require you to consult Safety Data Sheets (SDS) for every chemical you use. The SDS provides essential information about chemical properties, potential hazards, and compatibility guidelines.
For example, the SDS for a pesticide will specify which substances it can safely mix with and highlight any risks of hazardous reactions.
You must also follow local and federal laws regarding chemical segregation. Certain chemicals, such as oxidizers and flammables, must remain stored separately to avoid dangerous interactions. Non-compliance with these regulations can lead to fines, legal action, or even accidents that harm workers and the environment. Always prioritize legal compliance to maintain safety and avoid liability.
Chemical Reactions and Incompatibilities
Mixing incompatible chemicals can result in dangerous reactions. Some combinations release toxic gases, while others may cause explosions or fires. For instance, combining acids with bases generates heat and gas, which can damage your equipment or harm you. Similarly, certain pesticides react with other chemicals, reducing their effectiveness or creating harmful byproducts.
To avoid these risks, you should always refer to chemical compatibility charts. These charts categorize chemicals based on their reactivity and provide clear guidance on safe combinations. For example, they help you identify which pesticides can mix without compromising their performance or safety. Additionally, you should introduce each chemical into the tank one at a time, allowing sufficient mixing time between additions. This step minimizes the risk of unintended reactions.
Physical Issues During Mixing
Physical challenges can arise during the mixing process, especially when dealing with chemicals of varying viscosities or densities. For example, some powders may clump together, while certain liquids may separate instead of forming a uniform solution. These issues can lead to uneven distribution of the pesticide, reducing its effectiveness and requiring reapplication.
To address these problems, you should use high-quality mixing equipment designed for agricultural applications. Impellers or pumps in your tank ensure thorough blending, even for challenging mixtures. Additionally, always follow the recommended mixing order provided on product labels. This order often specifies adding wettable powders first, followed by dispersible granules, and then liquids. Proper technique ensures that all components dissolve or disperse evenly, creating a stable and effective solution.
Finally, always inspect your tank for signs of wear or corrosion. Tank compatibility with the chemicals you use is essential to prevent leaks or contamination. Stainless steel tanks, like those from Chenma, resist corrosion and maintain structural integrity, ensuring safe and efficient mixing operations.
Herbicide Mixing Order: The APPLES Framework
When mixing herbicides, following the correct sequence is essential for safety, effectiveness, and efficiency. The APPLES Framework provides a simple yet reliable guideline to ensure you achieve the best results while avoiding costly mistakes. This method helps you maintain the integrity of your herbicide mixture, prevent chemical incompatibilities, and protect your equipment.
What is the APPLES Framework?
The APPLES Framework is a step-by-step approach designed to guide you through the proper herbicide mixing order. Each letter in “APPLES” represents a specific category of products that must be added to the tank in a particular sequence. This framework ensures that all components mix thoroughly and remain stable, reducing the risk of clumping, separation, or dangerous chemical reactions.
Here’s what each letter stands for:
- A: Agitator – Start by turning on the tank’s agitator or mixing system. Proper agitation ensures that all chemicals disperse evenly throughout the solution.
- P: Powders – Add wettable powders or water-dispersible granules first. These products require more time to dissolve and mix properly.
- P: Premixes – Introduce premixed formulations, such as flowables or suspension concentrates, after powders have dissolved.
- L: Liquids – Add liquid formulations, including emulsifiable concentrates, to the tank next.
- E: Emulsifiers – Incorporate any adjuvants, surfactants, or emulsifiers to enhance the performance of the herbicide mixture.
- S: Solutions – Finally, add water-soluble solutions or fertilizers to complete the mixture.
This structured process minimizes the risk of incompatibility and ensures that each component integrates seamlessly into the solution.
Step-by-Step Guide to the Correct Herbicide Mixing Order
To apply the APPLES Framework effectively, follow these steps:
Start with clean water
Fill the tank halfway with clean water before adding any herbicide. Clean water prevents contamination and provides a neutral base for mixing. Begin agitation immediately to create a consistent flow within the tank.Add wettable powders or dispersible granules
Introduce powders or granules into the tank first. These products take longer to dissolve and require vigorous mixing. Allow sufficient time for them to disperse completely before moving to the next step.Incorporate premixed formulations
Add flowables or suspension concentrates. These products are thicker and need proper agitation to blend evenly with the water and powders already in the tank.Pour in liquid formulations
Add emulsifiable concentrates or other liquid herbicides. These products mix more easily but still require thorough agitation to ensure uniform distribution.Enhance with adjuvants or surfactants
Add any adjuvants, surfactants, or emulsifiers. These additives improve the effectiveness of the herbicide by enhancing its ability to stick to plant surfaces or penetrate target weeds.Finish with water-soluble solutions
Add water-soluble fertilizers or other solutions last. These products dissolve quickly and complete the herbicide mixture.Top off with water and continue agitation
Fill the tank with the remaining water while maintaining agitation. This step ensures that all components mix thoroughly and the solution remains stable.Test the mixture before application
Perform a small jar test to confirm compatibility if you’re using a new combination of herbicides. This precaution helps you avoid potential issues during application.
Pro Tip: Use tools like the Mix Tank app to double-check the compatibility of your herbicide mixture. This app provides valuable insights into the proper mixing order and helps you avoid costly errors.
By following this step-by-step guide, you can ensure that your herbicide mixing order aligns with best practices. Proper mixing order not only improves the effectiveness of your herbicide but also reduces waste, protects your equipment, and minimizes environmental risks.
Essential Safety Measures for Mixing Chemicals
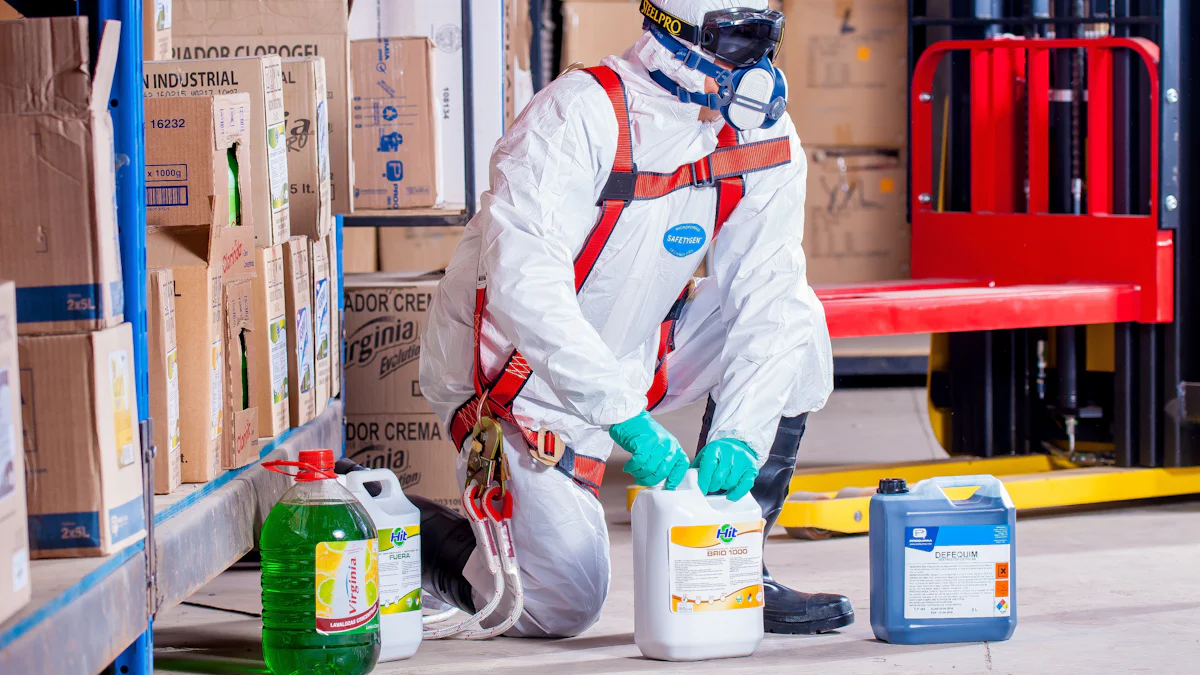
Ensuring safety during chemical mixing is not just a precaution—it is a necessity. By adopting proper safety measures, you protect yourself, your team, and the environment from potential hazards. This section outlines essential practices to follow when handling agricultural chemicals.
Personal Protective Equipment (PPE)
Wearing the right Personal Protective Equipment (PPE) is your first line of defense against chemical exposure. PPE shields you from harmful substances that can cause skin irritation, respiratory issues, or even long-term health problems. Essential PPE items include:
- Gloves: Use chemical-resistant gloves to protect your hands from direct contact with hazardous substances.
- Goggles: Wear safety goggles to prevent splashes from reaching your eyes.
- Respirators: Use a respirator to avoid inhaling toxic fumes, especially when working in enclosed spaces.
- Protective Clothing: Choose long-sleeved shirts, pants, and chemical-resistant aprons to cover exposed skin.
Expert Testimony:
“It is important to always wear personal protective equipment when dealing with physical incompatibility problems just as you would when mixing and spraying the products.” – Industry Experts
Always inspect your PPE for damage before use. Replace any worn-out or compromised equipment immediately. Properly fitted PPE ensures maximum protection and minimizes risks during pesticide mixing.
Safe Handling Practices
Safe handling practices are critical to preventing accidents and ensuring effective chemical application. Follow these steps to handle chemicals responsibly:
Read Labels and Safety Data Sheets (SDS)
Always review the product label and SDS before starting. These documents provide vital information about the chemical’s properties, hazards, and compatibility.Store Chemicals Properly
Keep chemicals in their original containers with labels intact. Store incompatible substances separately to avoid dangerous reactions. For example, oxidizers and flammables must never be stored together.Measure Accurately
Use precise measuring tools to ensure correct chemical ratios. Overdosing or underdosing can compromise the effectiveness of the pesticide and pose safety risks.Mix in a Well-Ventilated Area
Perform mixing outdoors or in areas with proper ventilation. This reduces the risk of inhaling harmful fumes.Avoid Direct Contact
Never use your hands to stir or mix chemicals. Use designated tools and equipment to minimize exposure.
Expert Testimony:
“Strict guidelines should be in place for the safe handling and storage of chemicals. Safety protocols minimize risks to workers, the environment, and the public.” – Industry Experts
By adhering to these practices, you create a safer working environment and reduce the likelihood of accidents.
Emergency Preparedness
Even with the best precautions, emergencies can happen. Being prepared ensures you can respond quickly and effectively to minimize harm. Key steps for emergency preparedness include:
Create an Emergency Plan
Develop a clear plan outlining steps to take in case of spills, leaks, or exposure. Ensure all team members are familiar with the plan.Keep Emergency Equipment Nearby
Equip your workspace with fire extinguishers, eyewash stations, and spill containment kits. These tools can mitigate damage during an incident.Conduct Regular Drills
Practice emergency scenarios to ensure everyone knows their role. Regular drills build confidence and improve response times.Know First Aid Procedures
Learn basic first aid for chemical exposure, such as flushing eyes with water or removing contaminated clothing. Quick action can prevent serious injuries.
Expert Testimony:
“Implementing a chemical hygiene plan, using appropriate Personal Protective Equipment (PPE), and conducting regular training and emergency response drills are all essential in minimizing risks associated with chemical exposure.” – Industry Experts
Preparation is key to managing emergencies effectively. By staying ready, you protect yourself and others from potential harm.
Maintaining and Cleaning Agricultural Chemical Mixing Tanks
Proper maintenance and cleaning of agricultural chemical mixing tanks are essential for ensuring their longevity, performance, and safety. Neglecting these tasks can lead to residue buildup, contamination, and equipment failure. By following regular maintenance routines and adopting effective cleaning practices, you can keep your tanks in optimal condition.
Regular Maintenance Tips
Maintaining your chemical mixing tanks involves consistent care and attention to detail. Regular upkeep not only extends the life of your equipment but also ensures safe and efficient operations. Here are some key maintenance tips:
Inspect Tanks Frequently: Check for signs of wear, corrosion, or damage. Look for cracks, leaks, or weakened seals that could compromise the tank’s integrity. Address any issues immediately to prevent further damage.
Monitor Mixing Mechanisms: Ensure that impellers, pumps, or other mixing components function properly. Malfunctioning parts can lead to uneven mixing or equipment failure. Replace worn-out components promptly.
Store Tanks Correctly: Keep tanks in a clean, dry, and shaded area when not in use. Proper storage prevents exposure to harsh environmental conditions that may degrade materials over time.
Follow Manufacturer Guidelines: Adhere to the manufacturer’s instructions for maintenance and operation. These guidelines provide specific recommendations tailored to your tank’s design and materials.
Prevent Residue Buildup: After each use, rinse the tank thoroughly to remove chemical residues. Residue buildup can cause clumping, gelling, or contamination during future applications.
Pro Tip: Regular maintenance of mixers and tanks ensures product quality, prevents contamination, and enhances the longevity of your equipment.
By incorporating these practices into your routine, you can maintain the reliability and safety of your agricultural chemical mixing tanks.
Proper Cleaning Procedures for Different Chemicals
Cleaning your tanks effectively is crucial for preventing cross-contamination and ensuring accurate chemical applications. Different chemicals require specific cleaning methods to remove residues and maintain tank performance. Follow these steps for proper cleaning:
Empty the Tank Completely
Drain all remaining liquid from the tank. Ensure no residual chemicals remain before starting the cleaning process.Rinse with Clean Water
Use clean water to rinse the interior of the tank. This initial rinse removes loose particles and dilutes any leftover chemicals.Use Appropriate Cleaning Agents
Select cleaning agents based on the type of chemicals previously used. For example:- Use mild detergents for general cleaning.
- Apply specialized cleaners for stubborn residues or oily substances.
- Follow label instructions for dilution and application to ensure safety and effectiveness.
Scrub Interior Surfaces
Use brushes or cleaning tools to scrub the tank’s interior. Pay extra attention to corners, seams, and hard-to-reach areas where residues may accumulate.Rinse Thoroughly
Rinse the tank multiple times with clean water to remove all cleaning agents and residues. Ensure no traces of chemicals or detergents remain.Dry the Tank Completely
Allow the tank to air dry or use clean towels to wipe it down. A dry tank prevents mold or mildew growth and ensures readiness for the next use.Dispose of Waste Properly
Dispose of rinse water and cleaning waste according to local regulations. Avoid releasing contaminated water into the environment.
Safety Reminder: Always wear protective gear, such as gloves and goggles, when handling cleaning agents or chemical residues. Work in a well-ventilated area to avoid inhaling fumes.
By following these cleaning procedures, you can maintain the cleanliness and functionality of your agricultural chemical mixing tanks. Clean tanks ensure accurate chemical applications, reduce the risk of contamination, and protect the environment.
Common Mistakes to Avoid When Mixing Chemicals
Skipping Label Instructions
Ignoring the instructions on a chemical label is one of the most common and dangerous mistakes you can make. Labels provide critical information about the chemical’s properties, proper usage, and potential hazards. Skipping this step leaves you vulnerable to improper application, which can harm crops, reduce pesticide effectiveness, or even cause environmental damage.
Labels also outline the correct mixing order for chemicals. Following this order ensures that each component integrates properly into the solution. For example, adding a liquid pesticide before dissolving powders can lead to clumping or uneven distribution. This mistake not only wastes resources but also compromises the safety and efficacy of your application.
Important Reminder: “Reading the label beforehand helps you understand what you’re using and how to use it properly.” Always take a few minutes to review the label before starting. This simple step can save you from costly errors and ensure a successful application.
Mixing Incompatible Chemicals
Combining incompatible chemicals can result in catastrophic outcomes. Certain chemicals react violently when mixed, producing heat, pressure, or toxic fumes. These reactions can lead to fires, explosions, or airborne hazards that endanger you, your team, and the surrounding environment.
For instance, mixing acids with bases generates heat and gas, which can damage your equipment or cause injuries. Similarly, some pesticides lose their effectiveness when combined with other substances, rendering your efforts useless. To avoid these risks, always consult chemical compatibility charts and perform a small jar test before mixing new combinations.
Uncontrolled mixing often occurs due to spills, leaking containers, or improper storage. Segregating incompatible chemicals in storage areas is essential to prevent accidental contact. Proper storage practices not only reduce the risk of dangerous reactions but also protect your workforce and build trust in your safety protocols.
Pro Tip: Never mix chemicals without verifying their compatibility. Use tools like compatibility charts or apps to double-check before proceeding.
Neglecting Safety Equipment
Failing to use safety equipment puts you at significant risk during chemical mixing. Personal Protective Equipment (PPE) acts as your first line of defense against exposure to harmful substances. Without it, you risk skin irritation, respiratory issues, or long-term health problems.
Essential PPE includes gloves, goggles, respirators, and protective clothing. Gloves shield your hands from direct contact with hazardous chemicals. Goggles protect your eyes from splashes, while respirators prevent you from inhaling toxic fumes. Wearing long-sleeved shirts and chemical-resistant aprons ensures that your skin remains covered and safe.
Expert Advice: “It is important to always wear personal protective equipment when dealing with physical incompatibility problems just as you would when mixing and spraying the products.”
Inspect your safety gear before each use to ensure it is in good condition. Replace damaged or worn-out equipment immediately. Neglecting safety equipment not only endangers your health but also increases the likelihood of accidents during the mixing process.
By avoiding these common mistakes, you can ensure a safer and more effective chemical mixing process. Always read the label, verify chemical compatibility, and prioritize safety equipment to protect yourself and others.
Environmental Considerations for Chemical Mixing
Preventing Chemical Runoff
Chemical runoff poses a significant threat to the environment, contaminating soil, water sources, and ecosystems. To prevent this, you must adopt responsible practices during chemical mixing and application. Begin by selecting a well-drained, level area for mixing. Avoid locations near water bodies, such as rivers, lakes, or wells, to minimize the risk of contamination.
Use buffer zones to protect sensitive areas. These zones act as barriers, reducing the likelihood of chemicals reaching unintended locations. For example, planting grass strips around fields can help absorb excess chemicals and prevent them from entering waterways.
Proper equipment maintenance also plays a crucial role. Leaking tanks or faulty sprayers can lead to unintended spills, increasing the risk of runoff. Regularly inspect your equipment for wear and tear, and address any issues immediately. Additionally, always follow the recommended application rates on the product label. Overapplication not only wastes resources but also increases the likelihood of runoff.
Important Reminder: “Improper handling of chemicals can lead to environmental damage, including contamination of nearby water sources and harm to wildlife.”
By implementing these measures, you can significantly reduce the environmental impact of your agricultural practices.
Proper Disposal of Chemical Waste
Disposing of chemical waste improperly can harm both human health and the environment. You must follow strict guidelines to ensure safe disposal. Always consult the product label for specific instructions on how to handle leftover chemicals or empty containers.
Many communities offer hazardous waste collection programs. These programs provide a safe and responsible way to dispose of unused chemicals, preventing them from entering landfills or water systems. Contact your local waste management authority to learn about available services in your area.
Never pour chemicals down drains, into sewers, or onto the ground. These actions can lead to contamination of drinking water supplies and harm aquatic life. Instead, store leftover chemicals in their original containers with labels intact until you can dispose of them properly.
Pro Tip: Rinse empty pesticide containers three times with clean water before disposal. Use the rinse water in your tank mix to avoid waste.
By adhering to these practices, you protect the environment and comply with legal regulations.
Minimizing Water Contamination
Water contamination from agricultural chemicals can have devastating effects on ecosystems and human health. To minimize this risk, you must take proactive steps during every stage of chemical use.
Start by using clean water for mixing. Contaminated water can interact with pesticides, reducing their effectiveness and potentially creating harmful byproducts. Always test your water quality before use to ensure it meets the required standards for effective pesticide application.
Avoid mixing chemicals near water sources. Even small spills can quickly spread, polluting rivers, lakes, and groundwater. Use secondary containment systems, such as spill trays or berms, to catch any accidental leaks during mixing.
Proper storage of chemicals is equally important. Keep chemicals in a secure, well-ventilated area away from water sources. Ensure that containers are sealed tightly to prevent leaks or spills. Additionally, never store incompatible chemicals together, as this can lead to dangerous reactions that may compromise container integrity.
Scientific Research Findings: “Mixing incompatible chemicals can produce hazardous gases and rapid temperature inversions, causing irreparable environmental damage.”
Finally, educate yourself and your team on emergency response procedures. Quick action during a spill can prevent chemicals from reaching water sources. Equip your workspace with spill containment kits and train your team on their proper use.
By taking these precautions, you safeguard water quality and contribute to sustainable agricultural practices.
Tips for Efficient and Effective Chemical Mixing
Planning and Preparation
Effective chemical mixing begins with thorough planning and preparation. Before you start, review the labels and Safety Data Sheets (SDS) for every product you plan to use. These documents provide essential details about the chemical properties, proper handling, and compatibility. Skipping this step can lead to costly mistakes, such as improper pesticide application or dangerous reactions.
Perform a jar test to check the compatibility of your chosen chemicals. This small-scale test ensures that the ingredients mix well without clumping, separating, or reacting adversely. It also helps you avoid wasting time and resources on incompatible mixtures. Always conduct this test in a controlled environment to minimize risks.
Prepare your workspace by ensuring it is clean, organized, and well-ventilated. Keep all necessary tools, such as measuring cups, stirring rods, and protective gear, within reach. A clutter-free area reduces the chances of accidents and makes the process more efficient. Additionally, select a location away from water sources to prevent contamination in case of spills.
Pro Tip: “Proper planning not only saves time but also ensures safety and effectiveness during chemical mixing.”
Accurate Measurements and Record-Keeping
Precision is key to achieving consistent and effective results. Use accurate measuring tools to ensure the correct ratios of each chemical. Overdosing can harm crops, while underdosing reduces the effectiveness of the pesticide. Both scenarios waste resources and may require reapplication, increasing costs and labor.
Document every step of the mixing process. Record the quantities of each chemical, the order in which they were added, and any observations during the process. This information is invaluable for troubleshooting issues, maintaining quality control, and improving future applications. Detailed records also help you comply with regulatory requirements and demonstrate responsible chemical handling practices.
Expert Advice: “Accurate measurements and meticulous record-keeping are essential for maintaining product quality and ensuring safety.”
When measuring, always follow the recommended mixing order provided on the product labels. For example, add wettable powders before liquids to prevent clumping and ensure even distribution. This sequence minimizes the risk of incompatibility and enhances the stability of the final mixture.
Using the Right Equipment for the Job
The equipment you use plays a significant role in the efficiency and safety of the mixing process. Choose tanks and mixers that are compatible with the chemicals you plan to use. Stainless steel tanks, like those manufactured by Chenma, resist corrosion and maintain structural integrity, making them ideal for agricultural applications.
Ensure your tank has an effective agitation system, such as impellers or pumps, to achieve uniform mixing. Proper agitation prevents separation and ensures that the pesticide solution remains stable throughout the application process. For larger tanks, consider using circulation pumps to maintain homogeneity.
Inspect your equipment regularly for signs of wear or damage. Leaks, cracks, or malfunctioning components can compromise the quality of the mixture and pose safety risks. Address any issues immediately to avoid disruptions during the mixing process.
Important Reminder: “Using high-quality equipment not only improves efficiency but also reduces the likelihood of accidents and environmental harm.”
By investing in the right tools and maintaining them properly, you can streamline your operations and achieve consistent results.
Following proper procedures for chemical mixing ensures safety, enhances efficacy, and protects the environment. By adopting these practices, you reduce risks, improve the performance of your agricultural chemicals, and contribute to sustainable farming. As experts emphasize, “Proper mixing stands as a cornerstone in the production of consistent, high-quality chemical products.”
Take proactive steps to safeguard your operations. Use high-quality equipment, like Chenma’s stainless steel tanks, to achieve reliable results. Consult professionals for technical support and guidance. Your commitment to safe and effective mixing practices benefits not only your crops but also the world around you.
FAQ
What are the benefits of tank mixing?
Tank mixing offers several advantages that make it a valuable practice in agriculture. By combining multiple products in a single application, you save time and reduce labor costs. This efficiency allows you to cover more ground with fewer passes, minimizing wear on equipment and fuel consumption. Additionally, tank mixing enhances the efficacy of treatments by ensuring that crops receive a balanced combination of pesticides, fertilizers, or other additives. This approach improves crop health and productivity while streamlining your operations.
Key Takeaway: Tank mixing not only saves resources but also boosts the effectiveness of agricultural treatments, making it an essential practice for modern farming.
Why is tank mixing common in agriculture?
Tank mixing has become a standard practice in agriculture due to its practicality and efficiency. Treating crops individually with separate applications for each pesticide or fertilizer would be time-consuming and labor-intensive. Instead, farmers can combine compatible products into one tank mix, allowing them to treat crops in a single pass. This method reduces the need for repeated trips across the field, saving time and resources. Moreover, tank mixing enables farmers to address multiple crop needs simultaneously, such as pest control and nutrient supplementation.
Imagine driving the same field repeatedly for individual treatments—it would feel like a never-ending cycle! Tank mixing simplifies this process, making it a go-to solution for farmers.
What are the critical factors to avoid tank-mix incompatibilities?
Avoiding tank-mix incompatibilities requires a clear understanding of several key factors. These include the chemical properties of the products being mixed, the order in which they are added, and the water quality used in the solution. Compatibility charts and product labels provide essential guidance on safe combinations. Proper agitation during mixing also ensures uniformity and prevents clumping or separation. By paying attention to these details, you can create a stable and effective tank mix.
Pro Tip: Always perform a small jar test before mixing large quantities to confirm compatibility and avoid costly mistakes.
What are the regulations and standards for tank mixers?
Tank mixers are subject to strict regulations and standards to ensure safety, environmental protection, and operational efficiency. Both international and national organizations have established guidelines for their use. These regulations cover aspects such as chemical handling, equipment design, and worker safety. Regular updates align these standards with technological advancements, ensuring that tank mixers remain reliable and compliant with modern requirements.
Important Reminder: Familiarize yourself with local and international regulations to ensure your practices meet legal and safety standards.
Why are chemical mixing tanks essential in industries?
Chemical mixing tanks play a vital role in industries that rely on precise formulations. They ensure product uniformity, which is critical for achieving consistent results. Industries such as agriculture, food processing, and pharmaceuticals depend on these tanks to mix chemicals safely and effectively. High-quality mixing tanks also enhance safety by preventing leaks, spills, or contamination during the mixing process.
Did You Know? Mixing tanks are indispensable for maintaining the quality and safety of products in various industrial applications.
How can you learn about tank mix order, agitation, and water amount?
Learning the correct tank mix order, proper agitation techniques, and the required water amount is essential for successful chemical mixing. Resources like instructional videos or expert consultations can provide valuable insights. For example, the CHS Agronomy “Proper Tank Mix Procedures” video offers a step-by-step guide to mastering these techniques. You can also reach out to local agronomy representatives for personalized advice.
Pro Tip: Leverage educational resources and expert guidance to refine your mixing practices and achieve optimal results.
What precautions should you take when using tank mixers?
Using tank mixers safely requires adherence to several precautions. Always wear appropriate Personal Protective Equipment (PPE), such as gloves, goggles, and respirators, to protect yourself from chemical exposure. Follow the manufacturer’s instructions for operating and maintaining the equipment. Regularly inspect your tank mixer for signs of wear or damage, and address any issues promptly. Additionally, ensure that your workspace is well-ventilated and free from potential hazards.
Safety First: Proper precautions not only protect you but also ensure the longevity and reliability of your equipment.
Can fertilizers and pesticides be mixed in the same tank?
Yes, fertilizers and pesticides can often be mixed in the same tank, provided they are compatible. This combination allows you to nourish crops while simultaneously protecting them from pests. However, it is crucial to consult compatibility charts and product labels to avoid adverse reactions. Performing a jar test can help confirm that the mixture will remain stable and effective.
Expert Advice: Always verify compatibility before mixing fertilizers and pesticides to maximize their benefits and prevent issues.
What should you do if a tank mix fails?
If a tank mix fails, act quickly to minimize damage. Stop the mixing process immediately and assess the situation. Identify the cause of the failure, such as incompatible chemicals or improper mixing order. Dispose of the failed mixture according to local regulations to prevent environmental harm. Learn from the experience by reviewing compatibility charts and refining your mixing practices for future applications.
Lesson Learned: Every failure is an opportunity to improve. Use the experience to enhance your knowledge and avoid similar issues in the future.
How does water quality affect tank mixing?
Water quality significantly impacts the success of tank mixing. Hard water, for example, can interact with certain chemicals, reducing their effectiveness. Contaminants in the water may also cause clumping or separation in the mixture. Always use clean, high-quality water for mixing, and consider adding water conditioners if necessary. Testing your water quality beforehand ensures that it meets the requirements for effective chemical applications.
Pro Tip: Clean water is the foundation of a successful tank mix. Never underestimate its importance in achieving optimal results.