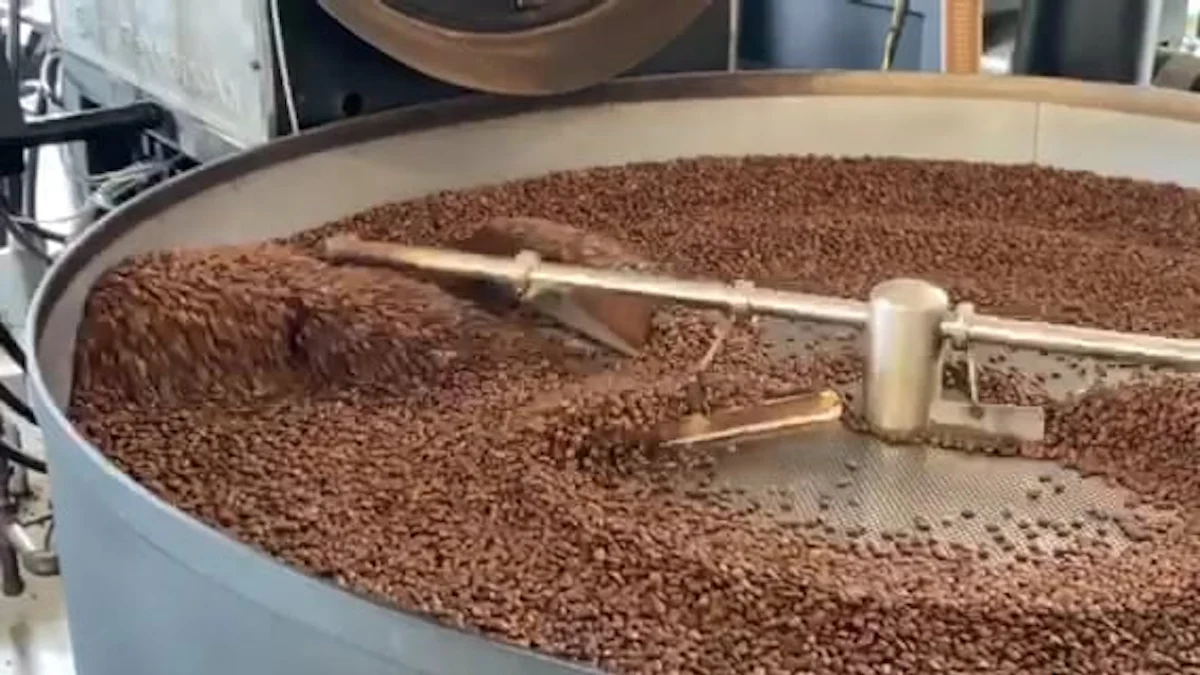
Chemical mixing tanks with agitators are indispensable in modern industries. These tanks ensure effective blending of liquids and solids, creating uniform mixtures for various industrial applications. The agitators inside the tanks generate controlled agitation, preventing separation and ensuring consistent quality. Whether you need to mix chemicals for detergents or blend ingredients in food production, these reliable mixing tanks deliver unmatched precision and efficiency. Their robust design supports large-scale operations, reduces processing time, and enhances productivity. By using advanced mixing equipment, you achieve safe, efficient, and reliable results across diverse industrial processes.
Chemical Manufacturing Applications of Chemical Mixing Tanks with Agitators
Chemical manufacturing relies heavily on precision and efficiency. Industrial mixing tanks equipped with agitators play a pivotal role in ensuring these standards are met. These tanks are designed to handle complex mixing applications, making them indispensable in the chemical industry. Whether you need to dissolve solids, blend liquids, or create homogenous mixtures, these tanks deliver consistent results.
Key Roles in Chemical Production
In the chemical industry, the production process often involves multiple stages of mixing and blending. A mixing tank with agitator ensures that each stage is executed with precision. These tanks are commonly used for:
- Dissolving and reacting substances: They facilitate the dissolution of solids into liquids and promote chemical reactions by maintaining uniform conditions.
- Crystallization processes: The controlled agitation provided by the agitators helps in forming crystals of the desired size and shape.
- Homogenization: They ensure that all components are evenly distributed, creating a uniform mixture.
The versatility of these tanks allows them to handle a wide range of chemical mixing tasks, from small-scale laboratory experiments to large-scale industrial production.
Benefits of Using Mixing Tanks with Agitators in Chemical Manufacturing
Investing in a mixing tank with agitator offers numerous advantages for your chemical production processes. These benefits include:
- Enhanced Efficiency: The agitators ensure rapid and thorough mixing, reducing processing time and increasing productivity.
- Improved Consistency: By maintaining uniform conditions, these tanks produce consistent results, which is crucial for quality control.
- Durability and Reliability: Made from high-grade stainless steel, these tanks resist corrosion and wear, ensuring long-term performance even in harsh chemical environments.
- Versatility: They can handle a variety of materials, including liquids, semi-solids, and powders, making them suitable for diverse industrial needs.
- Ease of Maintenance: The smooth, non-stick surface of stainless steel makes cleaning and maintenance simple, minimizing downtime.
“Mixing Tanks USA designs, engineers, and fabricates stainless steel mixing and storage tanks for chemical process systems that increase efficiency, consistency, and production in your facility.”
By incorporating advanced mixing equipment like these tanks into your operations, you can optimize your processes and achieve superior results. Their ability to handle continuous input and output of materials makes them ideal for large-scale production, ensuring a steady supply of mixed products.
Food and Beverage Industry Applications for Industrial Mixing Tanks
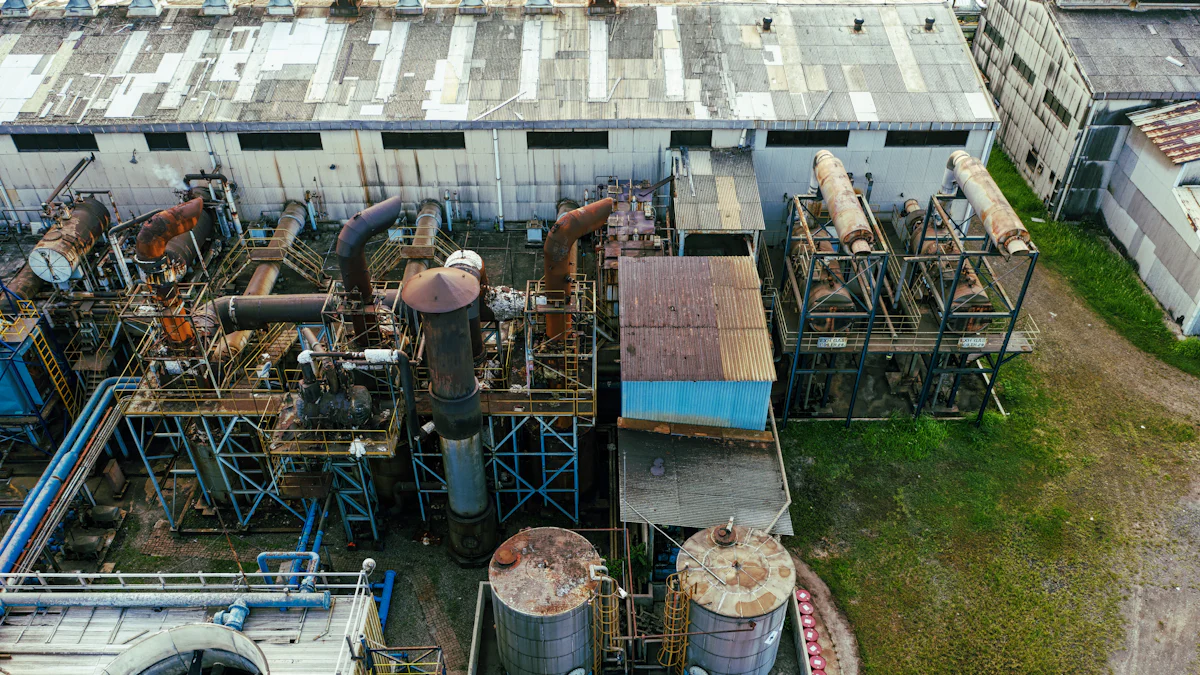
The food and beverage industry demands precision and hygiene in every step of production. An industrial mixing tank plays a critical role in meeting these requirements. These tanks ensure the seamless mixing of ingredients, creating consistent and high-quality products. From sauces to beverages, these tanks are indispensable tools for modern food processing.
Common Uses in Food and Beverage Processing
In food and beverage production, mixing tanks with agitators handle a variety of tasks. They are designed to blend ingredients efficiently, ensuring uniformity in the final product. Some common applications include:
- Blending sauces and condiments: These tanks mix ingredients like oils, spices, and emulsifiers to create smooth and flavorful sauces.
- Dairy product preparation: They homogenize milk, cream, and other dairy components to produce items like yogurt and cheese.
- Beverage production: Whether it’s juice, soda, or alcoholic drinks, these tanks ensure the even distribution of flavors and additives.
- Heating and cooling processes: Many tanks come equipped with temperature controls, allowing you to heat or cool mixtures as needed during production.
The versatility of these tanks makes them essential for handling diverse industrial food and beverage needs. Their ability to maintain consistent quality ensures that your products meet consumer expectations.
Advantages of Stainless Steel Mixing Tanks in Food Production
Stainless steel mixing tanks are the preferred choice for food production due to their durability and compliance with hygiene standards. Here are some key benefits:
- Hygiene and Safety: Stainless steel surfaces resist corrosion and are easy to clean, ensuring that your equipment meets strict food safety regulations.
- Durability: These tanks withstand the rigors of daily use, including exposure to acidic ingredients and high temperatures.
- Precision in Mixing: The agitators provide controlled mixing, ensuring that all ingredients are evenly distributed without clumps or inconsistencies.
- Versatility: They can handle a wide range of tasks, from blending liquids to suspending solids in mixtures.
- Cost-Effectiveness: Their long lifespan and low maintenance requirements make them a smart investment for any food production facility.
“Mixing tanks are essential in food processing, not only for blending ingredients but also for maintaining the highest hygiene standards.” – Micet Craft
By incorporating chemical mixing tanks with agitators into your operations, you can enhance efficiency and product quality. These tanks streamline production processes, reduce waste, and ensure that your food and beverage products consistently meet industry standards.
Pharmaceutical Applications of Mixing Tanks with Agitators
The pharmaceutical industry demands precision, safety, and consistency in every production process. An industrial mixing tank equipped with an agitator plays a vital role in meeting these stringent requirements. These tanks ensure uniform mixing of active ingredients, excipients, and other components, which is essential for producing high-quality pharmaceutical products. Whether you are manufacturing tablets, syrups, or injectable solutions, a mixing tank with agitator guarantees the accuracy and reliability needed in pharmaceutical production.
Use Cases in Pharmaceutical Manufacturing
In pharmaceutical manufacturing, industrial mixing tanks are indispensable for various applications. These tanks support critical processes that require precise control and uniformity. Some of the most common use cases include:
- Blending active ingredients and excipients: Mixing tanks ensure even distribution of active pharmaceutical ingredients (APIs) with excipients, creating a consistent formulation for tablets, capsules, or powders.
- Preparation of liquid formulations: These tanks are ideal for mixing syrups, suspensions, and emulsions, ensuring homogeneity and stability in the final product.
- Sterile mixing for injectables: Stainless steel mixing tanks with advanced agitation systems maintain sterile conditions, making them suitable for producing injectable solutions in the biopharmaceutical industry.
- Dissolution of powders: Agitators facilitate the dissolution of powders into liquids, ensuring complete solubility and avoiding clumps or inconsistencies.
The versatility of these tanks allows them to handle a wide range of pharmaceutical applications, from small-scale research and development to large-scale industrial production.
Importance of Agitators in Ensuring Precision and Safety
Agitators are the heart of any mixing tank, especially in pharmaceutical applications where precision and safety are paramount. The controlled agitation provided by these systems ensures that every component is thoroughly mixed, eliminating the risk of uneven distribution. This level of precision is crucial for maintaining the efficacy and safety of pharmaceutical products.
Here are some key benefits of using agitators in pharmaceutical manufacturing:
- Uniform Mixing: Agitators create consistent mixing conditions, ensuring that all ingredients are evenly distributed throughout the batch. This uniformity is essential for maintaining product quality and meeting regulatory standards.
- Enhanced Process Control: The ability to adjust agitation speed and intensity allows you to tailor the mixing process to specific materials and desired outcomes. This flexibility ensures optimal results for each formulation.
- Improved Safety: Agitators minimize the risk of contamination by maintaining a closed system during mixing. This feature is particularly important in the biopharmaceutical industry, where sterility is critical.
- Efficient Dissolution and Blending: Agitators accelerate the dissolution of powders and the blending of liquids, reducing processing time and increasing productivity.
- Scalability: Whether you are working on a small batch or a large-scale production run, mixing tanks with agitators can be customized to meet your needs.
“Agitators are essential for achieving precise and consistent mixing, which is critical for maintaining the quality of pharmaceutical products.”
By incorporating industrial mixing tanks with agitators into your pharmaceutical processes, you can achieve unparalleled precision, safety, and efficiency. These tanks not only enhance the quality of your products but also streamline your operations, making them an invaluable asset in the pharmaceutical industry.
Water Treatment Applications of Industrial Mixing Tanks
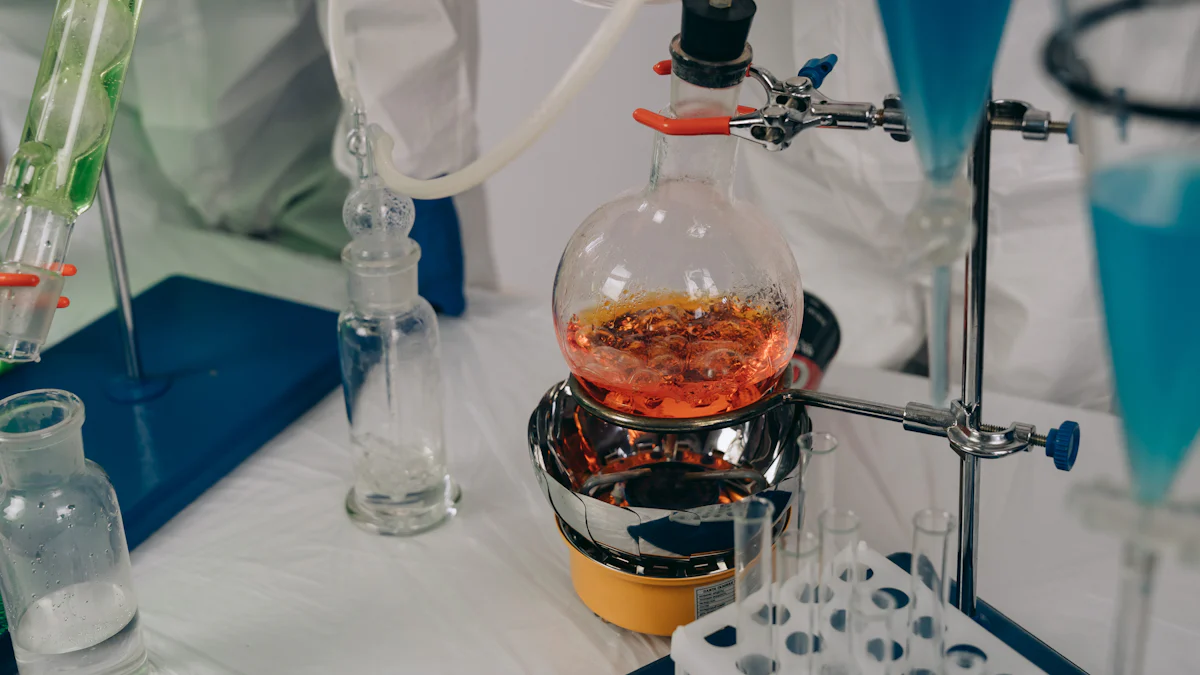
Water treatment processes demand precision and efficiency to ensure clean and safe water for various applications. An industrial mixing tank equipped with an agitator plays a vital role in achieving these goals. These tanks streamline the purification process by promoting uniform mixing, enhancing chemical reactions, and optimizing energy use. Whether you are treating drinking water or managing wastewater, these tanks provide reliable solutions for your needs.
Role of Mixing Tanks in Water Purification Processes
In water and wastewater treatment, the mixing tank with agitator is indispensable. It ensures that chemicals, such as coagulants and disinfectants, are evenly distributed throughout the water. This uniform distribution enhances the effectiveness of the treatment process. For example:
- Coagulation and flocculation: Agitators help mix coagulants into the water, causing impurities to clump together into larger particles (flocs) that can be easily removed.
- Neutralization: Mixing tanks facilitate the even blending of acids or bases to adjust the pH levels of water, ensuring it meets safety standards.
- Chemical reactions: Agitators maintain consistent conditions for reactions, such as oxidation or disinfection, to occur effectively.
The controlled agitation provided by these tanks ensures that every stage of the purification process operates efficiently. This precision reduces waste and improves the overall quality of treated water.
Benefits of Agitators in Water Treatment Efficiency
Agitators significantly enhance the efficiency of water treatment processes. By incorporating a mixing tank with agitator into your operations, you can achieve several key benefits:
- Optimized Energy Use: Agitators ensure thorough mixing with minimal energy consumption, making the process cost-effective.
- Reduced Processing Time: The consistent agitation accelerates chemical reactions, cutting down the time required for treatment.
- Improved Productivity: With faster and more efficient processes, you can treat larger volumes of water in less time.
- Effective Temperature Control: Agitators help maintain uniform temperatures within the tank, which is crucial for certain chemical reactions.
- Enhanced Purification: By ensuring even distribution of chemicals, agitators improve the removal of impurities and contaminants.
“Agitators in stainless steel mixing tanks are critical for achieving efficient and uniform mixing in water treatment processes.”
The durability of stainless steel mixing tanks further adds to their value. These tanks resist corrosion and wear, ensuring long-term performance even in demanding environments. Their versatility allows them to handle various tasks, from blending chemicals to maintaining consistent water quality.
By using chemical mixing tanks with agitators, you can optimize your water treatment operations. These tanks not only improve efficiency but also ensure compliance with environmental and safety standards. Whether you are managing industrial wastewater or purifying drinking water, they provide a dependable solution for your needs.
Cosmetics and Personal Care Product Applications for Stainless Steel Mixing Tanks
The cosmetics industry relies heavily on precision and consistency to meet the high standards of product quality and consumer satisfaction. An industrial mixing tank plays a pivotal role in achieving these goals. These tanks are essential for producing a wide range of beauty and personal care products, including creams, lotions, shampoos, and perfumes. By using advanced sanitary mixing equipment, you can ensure that your formulations maintain uniformity and meet regulatory requirements.
Uses in Cosmetics and Personal Care Manufacturing
In the cosmetics industry, the production process often involves combining multiple ingredients to create complex formulations. A mixing tank with agitator simplifies this process by ensuring thorough and efficient mixing. Here are some common applications:
- Creams and lotions: These tanks blend oils, water, and emulsifiers to create smooth and stable formulations for skincare products.
- Shampoos and conditioners: They mix surfactants, fragrances, and other additives to produce hair care products with consistent texture and performance.
- Perfumes and colognes: The tanks ensure even distribution of essential oils and alcohol, resulting in balanced and long-lasting fragrances.
- Makeup products: From liquid foundations to mascaras, these tanks handle the precise blending of pigments, binders, and other components.
The versatility of stainless steel mixing tanks makes them indispensable for handling diverse formulations in the cosmetics industry. Their ability to adapt to varying batch sizes and ingredient types ensures that you can meet changing market demands efficiently.
Advantages of Mixing Tanks with Agitators in Ensuring Product Consistency
Consistency is critical in the production of cosmetics and personal care products. A slight variation in formulation can lead to noticeable differences in texture, appearance, or performance. Stainless steel mixing tanks equipped with agitators help you maintain the highest level of consistency. Here’s how:
- Uniform Mixing: The agitators ensure that all ingredients are evenly distributed, eliminating clumps or inconsistencies in the final product.
- Sanitary Design: These tanks feature smooth, non-porous surfaces that resist contamination. This design supports compliance with hygiene standards, making them ideal for producing safe and high-quality products.
- Temperature Control: Many tanks include heating or cooling systems, allowing you to maintain optimal temperatures for emulsification or other chemical processes.
- Durability: The robust construction of stainless steel mixing tanks ensures long-term performance, even when handling abrasive or acidic ingredients.
- Scalability: Whether you’re producing small batches for niche markets or large volumes for mass distribution, these tanks can be customized to suit your needs.
“Sanitary mixing systems are essential for maintaining product quality and meeting the rigorous standards of the cosmetics industry.”
By incorporating a sanitary mixing system into your operations, you can streamline production processes and reduce waste. These systems not only enhance efficiency but also ensure that your products consistently meet consumer expectations. With the right industrial mixing tank, you can stay ahead in the competitive world of beauty and personal care manufacturing.
Biotechnology and Fermentation Applications of Chemical Mixing Tanks with Agitators
Chemical mixing tanks with agitators play a vital role in biotechnology and fermentation processes. These tanks ensure precise mixing, which is essential for maintaining optimal conditions during the production of biochemical products. Whether you are preparing cell cultures or mixing buffer solutions, these tanks provide the consistency and reliability needed for successful outcomes.
Role in Cell Culture and Buffer Solution Preparation
In biotechnology, cell culture preparation requires a controlled environment to support cell growth and productivity. Mixing tanks with agitators prevent cell settling and ensure even distribution of nutrients. This uniformity helps maintain cell viability and promotes efficient biochemical reactions. Agitators also regulate temperature within the tank, which is critical for sensitive biological processes.
Buffer solution preparation is another key application. These solutions stabilize pH levels during experiments or production processes. A mixing tank with an agitator ensures that all components dissolve completely, creating a homogenous solution. This precision minimizes errors and enhances the reproducibility of results.
Scientific Research Findings: Studies highlight the importance of mixing in bioprocessing for preventing nutrient depletion and controlling culture temperature. Proper agitation improves efficiency and reduces operating costs.
Benefits of Stainless Steel Tanks in Biotech Processes
Stainless steel mixing tanks are the preferred choice for biotechnology applications due to their durability and compliance with hygiene standards. These tanks offer several advantages that make them indispensable in biotech processes:
- Corrosion Resistance: Stainless steel resists corrosion from chemicals and biological materials, ensuring long-term performance.
- Sanitary Design: The smooth, non-porous surface prevents contamination, meeting the strict hygiene requirements of the biotechnology industry.
- Temperature Control: Many tanks include integrated heating or cooling systems, allowing precise temperature regulation for sensitive processes.
- Customizability: You can tailor these tanks to meet specific needs, such as varying batch sizes or unique process requirements.
- Scalability: From small-scale research to large-scale production, stainless steel tanks adapt seamlessly to your operations.
“Stainless steel mixing tanks are popular in biotechnology research laboratories for culturing cells and producing biochemical products.”
By incorporating stainless steel mixing tanks with agitators into your biotechnology processes, you can achieve superior efficiency and product quality. These tanks not only enhance the consistency of your results but also reduce downtime and maintenance costs, making them a valuable investment for any biotech facility.
Key Advantages of Chemical Mixing Tanks with Agitators Across Industries
Efficiency and Uniformity in Mixing Processes
A mixing tank with agitator ensures precise and consistent results across various industries. The agitator creates controlled movement within the tank, allowing liquids, solids, and semi-solids to blend evenly. This uniformity is essential for maintaining product quality, whether you are producing pharmaceuticals, food, or cosmetics.
Efficient mixing reduces processing time, enabling you to meet production deadlines without compromising quality. For example, in water treatment, agitators help distribute chemicals like coagulants evenly, speeding up purification processes. Similarly, in chemical manufacturing, these tanks ensure that reactions occur under optimal conditions, minimizing waste and maximizing output.
Fact: Studies show that stainless steel mixing tanks equipped with agitators can reduce mixing time by up to 30% compared to traditional methods, making them a cost-effective solution for high-demand industries.
By investing in advanced mixing equipment, you can streamline operations, improve productivity, and achieve consistent results in every batch.
Durability and Versatility of Stainless Steel Mixing Tanks
Stainless steel mixing tanks stand out for their durability and adaptability. Unlike plastic or glass alternatives, stainless steel resists corrosion, even when exposed to harsh chemicals or extreme temperatures. This makes it an ideal choice for industries like cosmetics, where acidic ingredients are common, or biotechnology, where sterility is critical.
The robust construction of stainless steel ensures a long lifespan, reducing the need for frequent replacements. These tanks also offer versatility, handling a wide range of materials, from viscous creams to volatile liquids. Their ability to adapt to different processes makes them indispensable for industrial applications.
- Key Benefits of Stainless Steel:
- Corrosion resistance ensures longevity, even in demanding environments.
- Easy maintenance due to smooth, non-porous surfaces.
- Compatibility with heating or cooling systems for temperature-sensitive processes.
“Stainless steel mixing tanks outperform other materials in durability and reliability, making them a preferred choice for industries requiring consistent performance.”
Choosing stainless steel tanks means you invest in equipment that delivers both reliability and flexibility, ensuring your operations run smoothly for years to come.
Enhanced Product Quality and Compliance with Industry Standards
Product quality directly impacts customer satisfaction and regulatory compliance. Chemical mixing tanks with agitators play a crucial role in achieving both. The controlled agitation ensures that all components are evenly distributed, eliminating inconsistencies that could compromise the final product.
For industries like pharmaceuticals and food production, compliance with strict hygiene and safety standards is non-negotiable. Stainless steel mixing tanks meet these requirements with their sanitary design, which resists contamination and supports easy cleaning. This ensures that your products not only meet but exceed industry expectations.
- How Mixing Tanks Enhance Quality:
- Uniform mixing prevents clumps or uneven textures.
- Temperature control systems maintain optimal conditions for sensitive formulations.
- Closed systems reduce the risk of contamination during production.
“Using stainless steel mixing tanks ensures your products consistently meet the highest quality and safety standards, giving you a competitive edge in the market.”
By incorporating these tanks into your processes, you can enhance product quality, maintain compliance, and build trust with your customers. Their precision and reliability make them an invaluable asset across industries.
Why Choose Chenma Machinery for Your Industrial Mixing Tank Needs
When selecting a partner for your industrial mixing equipment, you need a company that combines expertise, innovation, and reliability. Chenma Machinery stands out among mixing tank manufacturers, offering tailored solutions that meet the diverse needs of industries worldwide. Here’s why Chenma Machinery is the ideal choice for your mixing tank requirements.
Expertise in Manufacturing Stainless Steel Mixing Tanks
Chenma Machinery brings over 15 years of experience in designing and producing high-quality stainless steel tanks. With a 20,000 m² production facility and a team of more than 200 skilled professionals, the company ensures precision and excellence in every product. Chenma specializes in creating durable and efficient tanks for industries such as food and beverage, pharmaceuticals, cosmetics, and biotechnology.
The company’s engineering team excels in crafting tanks that meet the most demanding technical requirements. Whether you need a standard design or a custom solution, Chenma’s expertise guarantees equipment that enhances your production processes. Their tanks are built to withstand harsh environments, ensuring long-term performance and reliability.
“Chenma Machinery has collaborated with world-renowned companies, delivering equipment that meets the highest industry standards.”
Customization and Turnkey Solutions for Various Applications
Every industry has unique requirements, and Chenma Machinery understands the importance of tailored solutions. The company offers complete customization options, allowing you to adapt the design, size, and features of your mixing tank to your specific needs. From small-scale operations to large industrial facilities, Chenma provides equipment that fits seamlessly into your workflow.
Chenma also delivers turnkey solutions, simplifying the process from start to finish. Their services include process design, equipment manufacturing, installation, commissioning, and technical training. This comprehensive approach ensures that you receive not only a high-quality product but also the support needed to integrate it into your operations effectively.
- Key Features of Chenma’s Customization Services:
- Detailed engineering designs tailored to your requirements.
- Flexible tank configurations for various materials and processes.
- Integration of advanced features like temperature control and automated systems.
By choosing Chenma, you gain access to a partner who prioritizes your success and adapts to your evolving needs.
Commitment to Quality, Safety, and Environmental Standards
Chenma Machinery places a strong emphasis on quality, safety, and sustainability. All products are manufactured according to the latest international standards, including ISO9001-2005 for quality management, ISO14001-2015 for environmental management, and OHSAS18001-2007 for occupational health and safety. The company has also achieved EU CE certification, ensuring compliance with stringent European regulations.
Stainless steel tanks from Chenma are designed with hygiene and safety in mind, making them ideal for industries like pharmaceuticals and food production. The smooth, non-porous surfaces resist contamination, while the robust construction ensures durability and reliability. Additionally, Chenma’s commitment to environmental standards reflects its dedication to sustainable manufacturing practices.
“Chenma Machinery’s certifications and adherence to global standards demonstrate its unwavering commitment to quality and safety.”
By partnering with Chenma, you invest in equipment that not only meets but exceeds industry expectations. Their focus on innovation, customization, and sustainability makes them a trusted choice for businesses seeking reliable mixing solutions.
Chemical mixing tanks with agitators have become essential tools across industries, ensuring precision and efficiency in production processes. Whether in the pharmaceutical industry, where uniform mixing is critical for product safety, or in cosmetics manufacturing, where consistency defines quality, these tanks deliver unmatched reliability. Their role extends beyond mixing; they optimize operations and elevate product standards.
Chenma Machinery stands out as a trusted provider of these solutions. With over 15 years of expertise, a 20,000 m² facility, and a team of 200 professionals, Chenma offers high-quality, customizable tanks tailored to your needs. For reliable and innovative solutions, contact Chenma Machinery today.
FAQ
How Do Chemical Mixing Tanks Ensure Product Consistency and Quality?
Chemical mixing tanks play a critical role in maintaining product uniformity and quality. These tanks are designed to handle diverse materials, including liquids, powders, and gases, ensuring they blend into a homogeneous mixture. By using advanced agitators, the tanks prevent separation and ensure even distribution of components. This consistency is vital for industries like pharmaceuticals, food production, and water treatment, where precision directly impacts safety and compliance.
Key Insight: Custom chemical mixing tanks not only enhance efficiency but also help industries meet regulatory standards, reducing the risk of costly recalls or unusable products.
What Materials Are Used to Manufacture Mixing Tanks?
Mixing tanks are typically made from stainless steel or plastic, depending on the application. Stainless steel is highly durable, resistant to corrosion, and ideal for industries requiring strict hygiene, such as food and pharmaceuticals. Plastic tanks, on the other hand, are suitable for specific chemicals that may react with metal. Choosing the right material depends on the substances being mixed and the operational requirements of your industry.
Pro Tip: Always consult with your supplier to ensure the tank material aligns with your chemical or production needs.
Can Mixing Tanks Handle High-Temperature Processes?
Yes, many mixing tanks are designed to withstand high temperatures. Stainless steel tanks, in particular, excel in handling processes that involve heating or cooling. These tanks maintain structural integrity and resist reactions with chemicals at elevated temperatures. This feature makes them indispensable for industries like chemical manufacturing and food processing, where temperature control is crucial.
Why Are Agitators Important in Mixing Tanks?
Agitators are the core component of mixing tanks. They create controlled movement within the tank, ensuring thorough blending of all ingredients. This uniform mixing eliminates clumps, prevents settling, and enhances the overall quality of the final product. Agitators also speed up chemical reactions and reduce processing time, making them essential for industries that prioritize efficiency.
Fact: Studies show that agitators can reduce mixing time by up to 30%, significantly boosting productivity in industrial operations.
Are Mixing Tanks Suitable for Small-Scale Production?
While mixing tanks are often associated with large-scale operations, they can also be customized for small-scale production. Smaller tanks with tailored features provide the same level of precision and efficiency as their larger counterparts. However, it’s important to consider factors like space availability and budget when investing in mixing equipment for smaller facilities.
How Do Mixing Tanks Support Food and Beverage Production?
In the food and beverage industry, mixing tanks ensure the seamless blending of ingredients while maintaining strict hygiene standards. These tanks are used for tasks like homogenizing dairy products, blending sauces, and preparing beverages. Many tanks also feature temperature controls, allowing for heating or cooling during production.
Industry Insight: Food-grade stainless steel mixing tanks meet stringent safety regulations, ensuring your products remain safe and high-quality.
What Role Do Mixing Tanks Play in Water Treatment?
Mixing tanks are vital in water treatment processes. They evenly distribute chemicals like coagulants and disinfectants, enhancing the effectiveness of purification. Agitators in these tanks promote coagulation and flocculation, helping impurities clump together for easy removal. This precision ensures clean and safe water for various applications.
Did You Know? Agitators in water treatment tanks optimize energy use, making the process more cost-effective and environmentally friendly.
Can Mixing Tanks Be Customized for Specific Applications?
Yes, mixing tanks can be fully customized to meet the unique needs of different industries. From size and material to advanced features like temperature control and automated systems, manufacturers can tailor tanks to fit specific processes. Customization ensures that the equipment integrates seamlessly into your operations, maximizing efficiency and output.
How Do Mixing Tanks Help Industries Comply with Regulations?
Mixing tanks support compliance by ensuring consistent product quality and maintaining hygiene standards. For example, stainless steel tanks resist contamination and are easy to clean, making them ideal for industries with strict safety requirements. Additionally, custom tanks can be designed to meet specific regulatory guidelines, reducing the risk of non-compliance.
Takeaway: Investing in high-quality mixing tanks not only improves production but also safeguards your business against regulatory challenges.
Why Should You Choose Chenma Machinery for Mixing Tanks?
Chenma Machinery offers over 15 years of expertise in manufacturing stainless steel mixing tanks. Their tanks are built to the highest quality standards, ensuring durability, efficiency, and compliance. With customizable options and turnkey solutions, Chenma provides equipment tailored to your specific needs. Their commitment to innovation and sustainability makes them a trusted partner for industries worldwide.
Customer Highlight: “Chenma’s mixing tanks transformed our production process, delivering consistent quality and reducing downtime.” – A satisfied client.