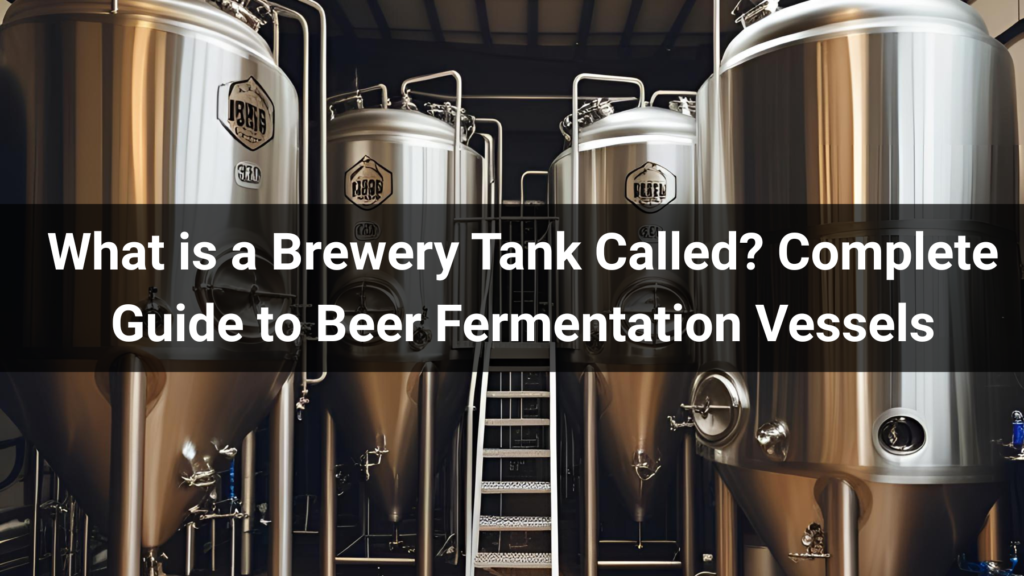
Understanding brewery equipment terminology is crucial for anyone involved in beer production, from craft brewery startups to established commercial operations. This comprehensive guide explores the various names and types of brewery tanks, their specific functions, and how to choose the right equipment for your brewing needs.
Table of Contents
What Are Brewery Tanks Called?
Brewery tanks go by several names depending on their specific function in the brewing process. The most common terms include fermentation tanks, fermenters, brewing vessels, and beer tanks. Each name reflects the tank’s role in transforming raw ingredients into finished beer.
The primary categories of brewery tanks include:
Tank Type | Primary Function | Common Names |
---|---|---|
Primary Fermenter | Initial fermentation process | Fermenter, FV, Primary Tank |
Secondary Fermenter | Secondary fermentation/conditioning | Secondary Tank, Conditioning Vessel |
Bright Tank | Final conditioning and carbonation | Bright Beer Tank, BBT, Serving Tank |
Brite Tank | Storage and dispensing | Serving Vessel, Storage Tank |
Primary Fermentation Tanks
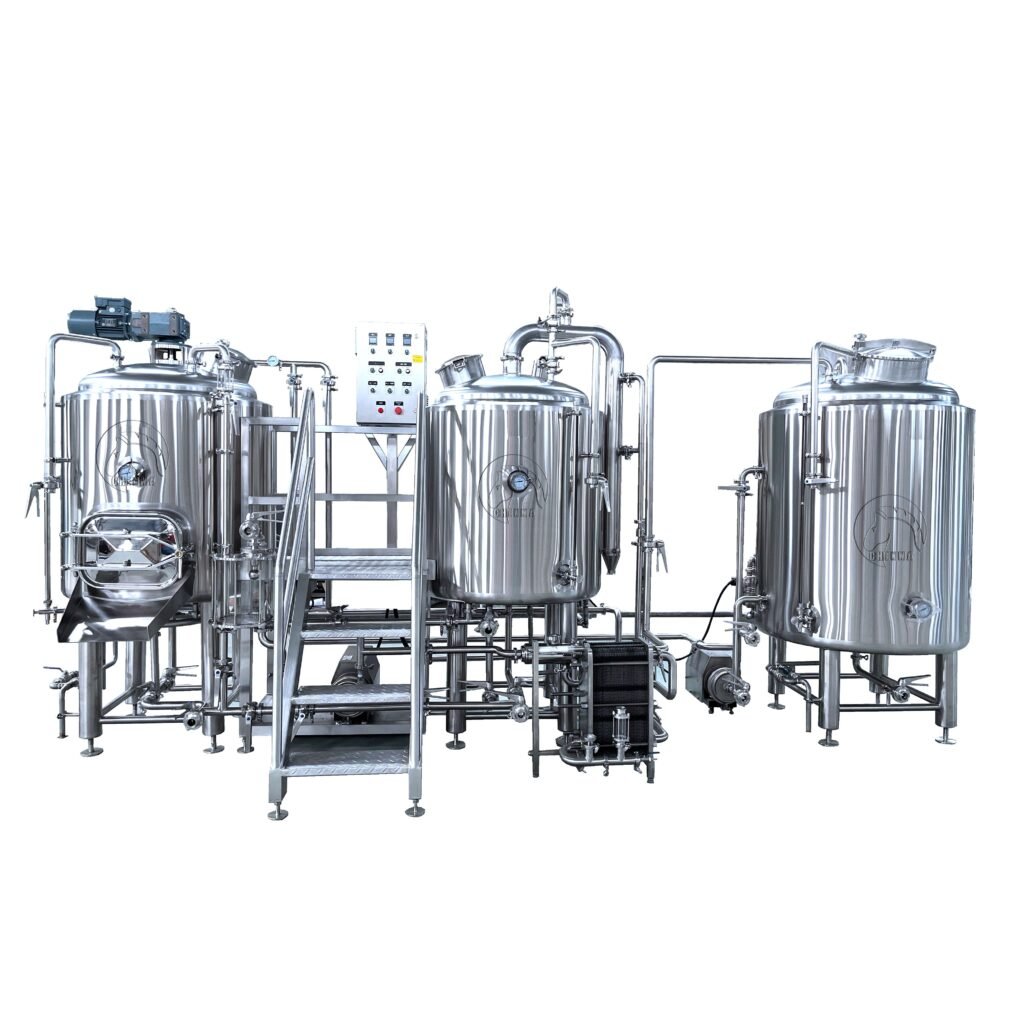
Primary fermentation tanks, commonly called fermenters or FVs, are where the magic of beer production begins. These vessels house the initial fermentation process where yeast converts sugars from malted grains into alcohol and carbon dioxide.
Modern beer fermentation tanks typically feature conical bottoms, which serve multiple purposes:
- Yeast Collection: The conical shape allows yeast to settle at the bottom for easy harvesting
- Trub Removal: Protein and hop debris settle efficiently
- Temperature Control: Better circulation and heat transfer
- Cleaning Efficiency: Easier sanitization and maintenance
Key features of professional fermentation tanks include:
Temperature Control Systems
Most commercial fermenters incorporate cooling jackets or glycol cooling systems to maintain precise temperature control throughout fermentation. This is crucial because different yeast strains require specific temperature ranges for optimal performance.
Pressure Relief Systems
Safety valves and pressure relief systems prevent over-pressurization during active fermentation, protecting both the equipment and the beer quality.
Secondary Fermentation Vessels
Secondary fermentation tanks, also known as conditioning tanks or lagering vessels, are used for extended aging and flavor development. These tanks allow for:
- Flavor maturation and mellowing
- Additional yeast settling
- Cold conditioning (lagering)
- Natural carbonation development
Many breweries utilize conical fermenters that can serve both primary and secondary fermentation functions, maximizing efficiency and reducing transfer requirements.
Bright Tanks and Conditioning Vessels
Bright tanks (also called brite tanks or bright beer tanks) represent the final stage in the brewing process before packaging or serving. These vessels serve several critical functions:
Carbonation Control
Bright tanks allow brewers to precisely control carbonation levels through forced CO2 injection, ensuring consistent product quality.
Final Conditioning
The beer undergoes final conditioning, allowing any remaining suspended particles to settle and flavors to stabilize.
Quality Assurance
Brewers can sample and test the beer before packaging, ensuring it meets quality standards.
Bright Tank Feature | Purpose | Benefit |
---|---|---|
Carbonation Stone | CO2 injection | Precise carbonation control |
Sample Ports | Quality testing | Consistent product quality |
Bottom Outlet | Sediment removal | Clear, bright beer |
Pressure Gauge | Pressure monitoring | Safety and quality control |
Specialized Brewery Tanks
Beyond the standard fermentation and conditioning vessels, breweries often employ specialized tanks for specific processes:
Hot Liquor Tanks (HLT)
These tanks store heated water used for mashing and sparging during the brewing process.
Cold Liquor Tanks (CLT)
Used for storing cold water needed for cooling wort and cleaning operations.
Whirlpool Tanks
Separate hop debris and proteins from wort before fermentation begins.
Yeast Propagation Tanks
Specialized vessels for growing and maintaining yeast cultures.
For breweries expanding their operations, understanding the different types of industrial stainless steel tanks is essential for making informed equipment decisions.
Materials and Construction
Modern brewery tanks are predominantly constructed from stainless steel, typically grade 304 or 316L, due to their superior properties:
- Corrosion Resistance: Withstands acidic conditions and cleaning chemicals
- Hygienic Surface: Easy to clean and sanitize
- Durability: Long-lasting with proper maintenance
- Temperature Stability: Handles extreme temperature variations
- Non-reactive: Won’t affect beer flavor or quality
Design Considerations
Professional brewery tanks incorporate several design elements:
- Conical Bottoms: Facilitate yeast harvesting and cleaning
- Manways: Large access ports for interior cleaning and inspection
- CIP (Clean-in-Place) Systems: Automated cleaning capabilities
- Insulation: Temperature control and energy efficiency
- Pressure Ratings: Designed for specific operating pressures
Shandong Chenma Machinery Co., Ltd. specializes in manufacturing high-quality stainless steel brewery tanks designed to meet the demanding requirements of modern brewing operations. Our brewing tanks and fermenters feature state-of-the-art conical designs and integrated CIP systems for maximum efficiency and product quality.
Sizing and Capacity Considerations
Choosing the right tank size depends on several factors:
Production Volume
Tank capacity should align with your brewing volume and frequency. Common sizes range from 1 barrel (31 gallons) for small craft breweries to 200+ barrels for large commercial operations.
Fermentation Duration
Different beer styles require varying fermentation times, affecting tank turnover rates and capacity planning.
Space Constraints
Physical brewery layout influences tank dimensions and configuration options.
Brewery Size | Typical Tank Capacity | Annual Production |
---|---|---|
Nano Brewery | 1-7 barrels | < 1,000 BBL/year |
Microbrewery | 7-30 barrels | 1,000-15,000 BBL/year |
Regional Brewery | 30-200 barrels | 15,000-6M BBL/year |
Large Brewery | 200+ barrels | 6M+ BBL/year |
Future Growth Planning
Consider your brewery’s growth projections when selecting tank sizes. Modular systems allow for easier expansion as production increases.
Our team at Chenma Machinery works closely with breweries to design custom tank solutions that accommodate current needs while allowing for future expansion. Contact us at WhatsApp: 008618063421809 or email: admin@sdchenma.com to discuss your specific requirements.
Maintenance and Cleaning
Proper maintenance and cleaning of brewery tanks are critical for product quality and equipment longevity:
Cleaning Protocols
Regular cleaning schedules prevent contamination and maintain beer quality:
- Pre-rinse: Remove gross soils and residues
- Alkaline Wash: Remove organic deposits and proteins
- Acid Rinse: Remove mineral deposits and neutralize alkalinity
- Sanitization: Eliminate remaining microorganisms
- Final Rinse: Remove cleaning chemical residues
CIP (Clean-in-Place) Systems
Modern brewery tanks often incorporate automated CIP systems that ensure consistent, thorough cleaning without manual intervention. These systems offer several advantages:
- Consistent cleaning results
- Reduced labor requirements
- Minimized cleaning chemical usage
- Documented cleaning cycles for quality assurance
- Reduced contamination risk
Preventive Maintenance
Regular maintenance schedules help prevent costly breakdowns and extend equipment life:
- Gasket Inspection: Check seals for wear and proper function
- Valve Maintenance: Service and calibrate control valves
- Pressure Testing: Verify tank integrity and safety systems
- Surface Inspection: Check for corrosion or damage
- Cooling System Service: Maintain glycol and refrigeration systems
Proper maintenance extends beyond just cleaning. Understanding mixing tank types and their advantages can help optimize your brewery’s overall efficiency and product consistency.
Common Maintenance Issues
Being aware of potential problems helps prevent costly downtime:
Issue | Symptoms | Prevention |
---|---|---|
Gasket Failure | Leaks, pressure loss | Regular inspection and replacement |
Valve Problems | Poor flow control, leakage | Routine maintenance and calibration |
Cooling Issues | Temperature fluctuations | System monitoring and service |
Surface Corrosion | Discoloration, pitting | Proper cleaning protocols |
Shandong Chenma Machinery Co., Ltd. provides comprehensive support for brewery tank maintenance and operation. Our experienced team offers technical training, installation services, and ongoing support to ensure your equipment operates at peak efficiency. Located in Pingyuan County Economic Development Zone, Dezhou City, Shandong Province, we’re committed to helping breweries worldwide achieve success through quality equipment and expert service.
Quality Certifications
Our commitment to quality is demonstrated through multiple certifications:
- ISO9001-2005 quality system certification
- ISO14001-2015 environmental management system certification
- OHSAS18001-2007 occupational health management system certification
- EU CE certification
These certifications ensure that our brewery tanks meet the highest international standards for safety, quality, and environmental responsibility.
Whether you’re starting a new brewery or expanding existing operations, understanding what brewery tanks are called and how they function is essential for success. From fermentation vessels to bright tanks, each component plays a crucial role in creating quality beer. For expert guidance on selecting the right brewery equipment for your needs, contact Chenma Machinery today.
Contact Shandong Chenma Machinery Co., Ltd.
Ready to upgrade your brewery with premium stainless steel tanks? Our expert team is here to help you select the perfect fermentation and storage solutions for your operation.
📍 Address:
Pingyuan County Economic Development Zone
Dezhou City, Shandong Province, China
📱 WhatsApp:
+86 180 6342 1809
✉️ Email:
admin@sdchenma.com
🏭 Production Facility:
20,000 m² state-of-the-art manufacturing facility
200+ skilled professionals
Why Choose Chenma Machinery?
- ✅ Complete turnkey brewing solutions
- ✅ Custom tank design and manufacturing
- ✅ Professional installation and commissioning
- ✅ Technical training and ongoing support
- ✅ ISO certified quality management systems
Contact us today for a free consultation and customized brewery tank solution!