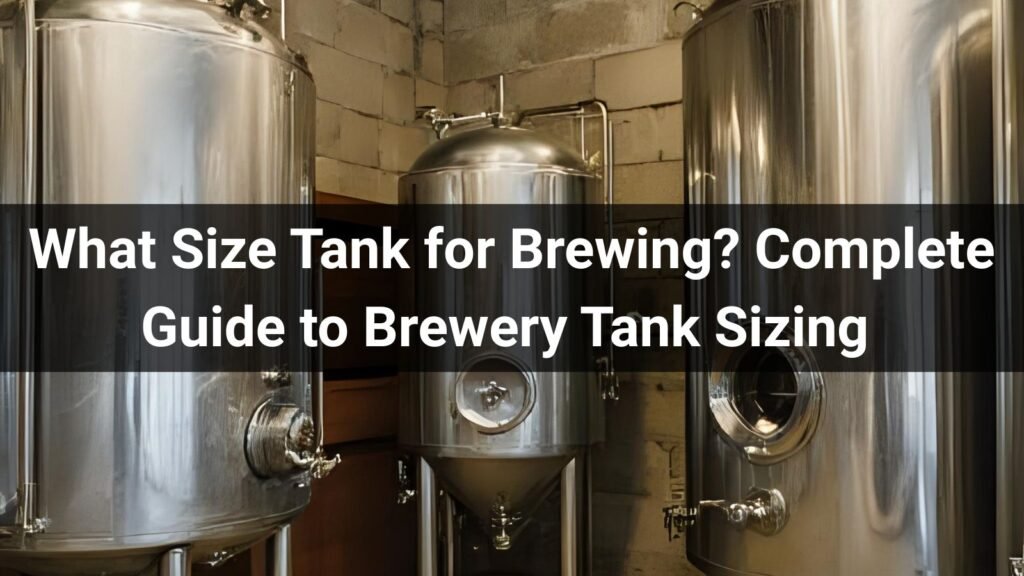
Selecting the appropriate tank size is one of the most critical decisions in brewery planning, directly impacting
production capacity, efficiency, and long-term profitability. Whether you’re establishing a craft brewery,
expanding existing operations, or upgrading equipment, understanding tank sizing principles ensures optimal
brewing performance and scalable growth. This comprehensive guide explores tank sizing considerations across
different brewing scales, from homebrewing setups to commercial operations, while highlighting how professional
equipment manufacturers support breweries in making informed sizing decisions.
Table of Contents
- Understanding Brewing Tank Sizes
- Homebrewing Tank Sizes
- Microbrewery and Craft Brewery Sizing
- Commercial Brewery Tank Sizing
- Tank Types and Sizing Considerations
- Production Volume Calculations
- Space and Layout Considerations
- Scaling and Growth Planning
- Cost Considerations by Tank Size
- Expert Recommendations and Best Practices
Understanding Brewing Tank Sizes
Brewing tank sizes vary dramatically based on production goals, available space, and target market reach. Tank
capacity is typically measured in barrels (bbl), hectoliters (HL), gallons, or liters, with different regions
preferring different units of measurement.
The fundamental principle of tank sizing involves matching fermentation capacity to brewing frequency and target
production volume. Proper sizing ensures optimal fermentation conditions while maintaining economic efficiency
throughout the brewing process.
Brewery Scale | Typical Tank Sizes | Annual Production Range | Primary Market |
---|---|---|---|
Homebrewing | 5-15 gallons (19-57 liters) | 50-500 gallons annually | Personal consumption |
Nano Brewery | 1-3 bbl (117-350 liters) | 200-1,000 bbls annually | Local taproom, limited distribution |
Microbrewery | 7-15 bbl (820-1,750 liters) | 1,000-15,000 bbls annually | Regional distribution |
Regional Brewery | 30-100 bbl (3,500-11,700 liters) | 15,000-200,000 bbls annually | Multi-state distribution |
Large Commercial | 200+ bbl (23,400+ liters) | 200,000+ bbls annually | National/international markets |
Understanding these scaling categories helps brewers identify appropriate tank sizes for their specific
production goals and market positioning. Each category requires different approaches to tank selection, facility
design, and operational planning.
Homebrewing Tank Sizes
Homebrewing represents the entry point for many brewing enthusiasts, with tank sizes designed for personal
consumption and experimentation. Standard homebrewing fermentation vessels range from 5 to 15 gallons, with
5-gallon systems being the most popular starting point.
5-Gallon Systems: The standard homebrewing size produces approximately two cases of beer per
batch. These systems are ideal for beginners due to manageable batch sizes, reasonable ingredient costs, and
storage requirements that fit most homes. A typical 5-gallon fermentation yields about 48-50 twelve-ounce
bottles.
10-Gallon Systems: Serious homebrewers often upgrade to 10-gallon systems to increase production
efficiency and reduce the frequency of brewing sessions. These systems require more storage space and higher
initial ingredient investments but provide better economies of scale for dedicated hobbyists.
15-Gallon Systems: Advanced homebrewers and those transitioning toward commercial brewing may
utilize 15-gallon systems. These larger vessels allow for more consistent fermentation conditions and provide
stepping stones toward understanding commercial brewing challenges.
When selecting homebrewing tank sizes, consider available storage space, consumption patterns, and long-term
brewing goals. Many successful commercial brewers started with modest homebrewing systems and gradually scaled
their operations.
Microbrewery and Craft Brewery Sizing
Microbreweries and craft breweries represent the fastest-growing segment of the brewing industry, with tank
sizing decisions directly impacting operational efficiency and market competitiveness. These operations
typically utilize tank systems ranging from 3 to 30 barrels.
3-7 Barrel Systems: Nano breweries often start with smaller systems to minimize initial capital
investment and test market demand. These systems are perfect for taproom operations where fresh beer is served
directly to customers. Understanding the top beer fermentation
tanks available for 2025 helps nano breweries select equipment that supports growth.
10-15 Barrel Systems: This size range represents the sweet spot for many craft breweries,
providing sufficient production capacity for local distribution while maintaining manageable operational
complexity. A 15-barrel system can produce approximately 450 cases of beer per batch, supporting taproom sales
and limited distribution.
20-30 Barrel Systems: Established craft breweries expanding into regional markets often utilize
larger tank systems. These systems require significant capital investment but provide the production capacity
necessary for broader distribution networks.
Craft breweries must balance tank size with fermentation time requirements, as different beer styles require
varying fermentation periods. Lagers typically require longer fermentation times than ales, influencing tank
turnover rates and overall production planning.
Commercial Brewery Tank Sizing
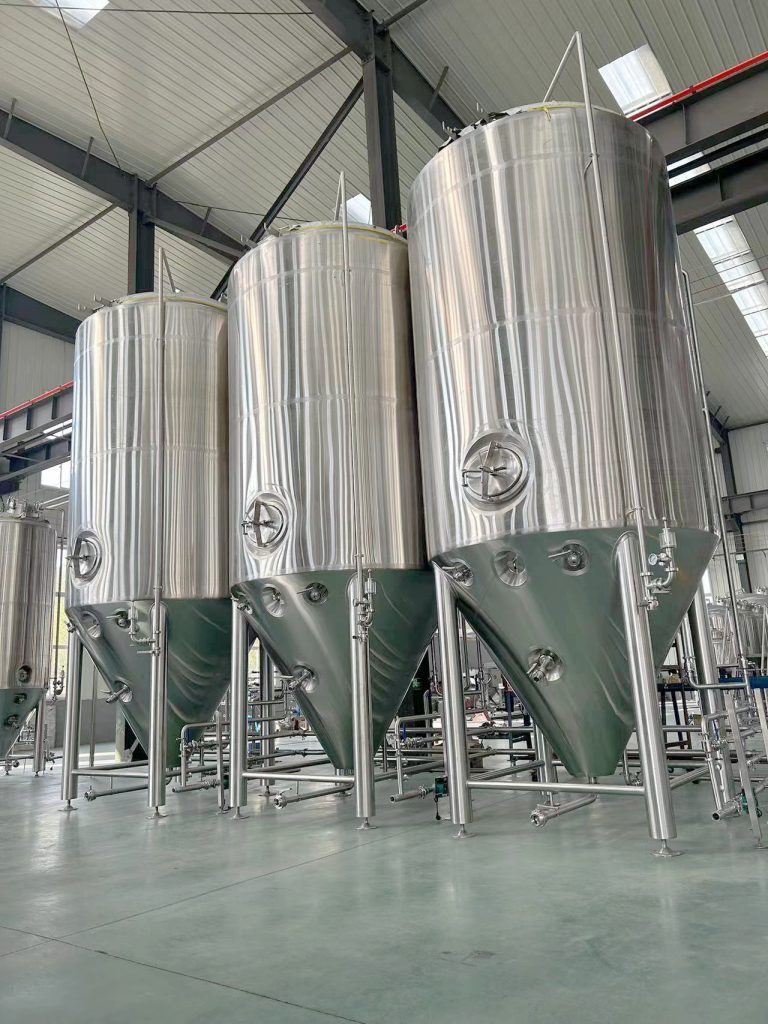
Commercial breweries operate at scales requiring sophisticated tank sizing strategies to optimize production
efficiency, quality consistency, and operational costs. These operations typically utilize tank systems ranging
from 50 to 1,000+ barrels.
50-100 Barrel Systems: Regional breweries often operate multiple tanks in this size range to
maintain production flexibility while achieving economies of scale. These systems support multi-state
distribution and seasonal production variations.
200-500 Barrel Systems: Large commercial breweries utilize massive tank systems to support
national distribution networks. These systems require sophisticated temperature control, cleaning systems, and
quality monitoring equipment.
1,000+ Barrel Systems: The largest brewing operations employ enormous tank systems that require
specialized engineering and installation expertise. Professional equipment manufacturers like Shandong
Chenma Machinery Co., Ltd. provide comprehensive support for large-scale brewing operations,
including custom tank design, manufacturing, and installation services.
Commercial brewery tank sizing must account for production scheduling, quality control requirements, and
distribution logistics. Large systems require longer lead times for manufacturing and installation but provide
significant per-unit cost advantages.
Tank Types and Sizing Considerations
Different tank types serve specific functions in brewing operations, each with unique sizing considerations that
impact overall system design and operational efficiency.
Fermentation Tanks: Primary fermentation tanks require sizing based on batch volumes and
fermentation duration. Understanding brewing
tanks and fermenters guide including conical designs helps optimize fermentation tank selection for
specific brewing needs.
Bright Tanks: Secondary fermentation and conditioning tanks typically match primary fermentation
tank sizes but may be slightly larger to accommodate multiple batches during blending operations.
Storage Tanks: Finished beer storage tanks should provide sufficient capacity to support
distribution schedules while maintaining product freshness. These tanks often exceed fermentation tank sizes to
accommodate multiple batches.
Tank Type | Sizing Factors | Typical Size Ratio |
---|---|---|
Primary Fermentation | Batch size, fermentation time | Base capacity |
Secondary/Bright | Conditioning time, blending needs | 100-120% of primary |
Storage | Distribution schedule, inventory | 150-200% of primary |
Hot Liquor | Cleaning, sanitizing needs | 50-75% of primary |
Mixing and Blending Tanks: Specialized tanks for ingredient mixing and beer blending require
careful sizing based on recipe requirements and production volumes. Professional manufacturers provide comprehensive
mixing tank guides covering types, advantages, and selection criteria to help breweries optimize their
mixing operations.
Production Volume Calculations
Accurate production volume calculations form the foundation of proper tank sizing decisions. Breweries must
consider multiple factors including target annual production, brewing frequency, and seasonal variations.
Annual Production Planning: Start with annual production goals and work backward to determine
required tank capacity. For example, a brewery targeting 1,000 barrels annually with weekly brewing schedules
requires approximately 20-barrel batches to meet production goals.
Fermentation Duration: Different beer styles require varying fermentation times, affecting tank
turnover rates. Ales typically ferment in 7-14 days, while lagers may require 4-8 weeks. Longer fermentation
times require additional tank capacity or reduced production frequency.
Seasonal Considerations: Many breweries experience seasonal demand variations, requiring
flexible tank sizing strategies. Summer wheat beers and winter stouts may require different production schedules
and tank utilization patterns.
Growth Planning: Successful breweries plan tank sizing with future growth in mind. Installing
slightly oversized tanks initially can accommodate growth without requiring complete system replacement.
Professional brewing consultants recommend maintaining 20-30% excess capacity to accommodate demand spikes and
production flexibility. This approach prevents production bottlenecks while providing room for experimentation
and special releases.
Space and Layout Considerations
Tank sizing decisions must account for available facility space, ceiling heights, and equipment access
requirements. Proper space planning ensures efficient operations and future expansion capability.
Ceiling Height Requirements: Fermentation tanks require adequate headspace for installation,
maintenance, and cleaning. Conical bottom tanks need additional height for cone clearance and valve access.
Facilities with limited ceiling height may require horizontal tanks or specialized designs.
Floor Loading: Large tanks filled with beer create significant floor loading requirements.
Structural engineers must verify floor capacity, and some installations require reinforcement or special
foundations.
Access and Maintenance: Tank sizing must accommodate maintenance access, cleaning equipment, and
safety requirements. Larger tanks require specialized cleaning systems and safety platforms for personnel
access.
Expansion Planning: Smart facility design reserves space for additional tanks as production
grows. Understanding industrial
stainless steel tanks for brewing applications helps breweries plan facility layouts that support
long-term growth.
Scaling and Growth Planning
Successful breweries plan tank sizing strategies that support sustainable growth while maintaining operational
efficiency and product quality. Scaling decisions impact everything from facility design to distribution
capabilities.
Modular Systems: Many breweries adopt modular tank systems that allow capacity increases through
additional tank installation rather than complete system replacement. This approach reduces capital requirements
and maintains production continuity during expansion.
Tank Size Standardization: Standardizing tank sizes throughout the brewery simplifies
operations, maintenance, and spare parts inventory. Many successful breweries utilize consistent tank sizes
across their fermentation, conditioning, and storage systems.
Market-Driven Scaling: Tank sizing decisions should align with market development strategies.
Breweries focusing on taproom sales may prioritize smaller, more frequent batches, while distribution-focused
operations benefit from larger, less frequent production runs.
Financial Planning: Tank investments represent significant capital expenditures requiring
careful financial planning. Leasing options, used equipment, and phased installation strategies help manage cash
flow during growth phases.
Cost Considerations by Tank Size
Tank costs vary significantly based on size, construction materials, features, and manufacturer specifications.
Understanding cost factors helps breweries make informed investment decisions that balance performance
requirements with budget constraints.
Size-Based Pricing: Tank costs generally increase with capacity, but per-unit costs typically
decrease for larger sizes. A 30-barrel tank costs more than a 15-barrel tank but provides better cost-per-barrel
value.
Tank Size Range | Typical Cost Range | Cost per Barrel | Key Features |
---|---|---|---|
1-5 bbl | $3,000 – $15,000 | $2,000 – $4,000 | Basic cooling, manual valves |
7-15 bbl | $15,000 – $50,000 | $1,500 – $3,000 | Automated controls, CIP systems |
20-50 bbl | $40,000 – $150,000 | $1,200 – $2,500 | Advanced monitoring, pressure rated |
60+ bbl | $100,000+ | $800 – $2,000 | Complete automation, custom designs |
Feature Impact on Costs: Tank features significantly impact overall costs. Basic fermentation
tanks cost less than vessels with advanced temperature control, pressure rating, and automated monitoring
systems. Understanding how stainless
steel tanks make food processing safer and easier helps justify premium features that improve
operational efficiency.
Installation and Setup Costs: Tank installation requires additional investment in electrical,
plumbing, and ventilation systems. Professional installation ensures proper operation and warranty coverage.
Operating Cost Considerations: Larger tanks may reduce per-unit production costs but require
higher utility consumption for heating, cooling, and cleaning operations. Energy-efficient designs help minimize
long-term operating costs.
Expert Recommendations and Best Practices
Industry experts and successful brewers have developed proven strategies for optimal tank sizing that balance
production requirements, quality standards, and economic efficiency.
Start Conservatively: Most brewing experts recommend starting with smaller tanks and expanding
as demand grows. This approach minimizes initial investment risks while providing operational learning
opportunities.
Plan for Flexibility: Tank sizing should accommodate multiple beer styles and seasonal
variations. Flexible systems adapt to changing market demands and production requirements.
Quality Over Quantity: Investing in properly sized, high-quality tanks provides better long-term
value than oversized systems that compromise product quality or operational efficiency.
Professional Consultation: Experienced equipment manufacturers provide valuable guidance for
tank sizing decisions. Companies like Shandong Chenma Machinery Co., Ltd. offer comprehensive
consultation services, helping breweries select optimal tank sizes for their specific applications.
Located in Pingyuan County Economic Development Zone, Dezhou City, Shandong Province, Chenma Machinery combines
over 200 professionals and 20,000 m² of production capacity to manufacture custom brewing equipment. Their
ISO9001-2005 quality certification, ISO14001-2015 environmental management certification, OHSAS18001-2007
occupational health certification, and EU CE certification demonstrate commitment to excellence in brewing
equipment manufacturing.
Maintenance Planning: Tank sizing decisions should consider maintenance requirements and
cleaning procedures. Properly sized tanks with appropriate access features reduce maintenance costs and improve
operational reliability.
Future Expansion: Successful breweries plan tank installations with future expansion in mind.
Modular designs and standardized connections facilitate system growth without major infrastructure changes.
Contact Shandong Chenma Machinery Co., Ltd.
Ready to determine the optimal tank sizes for your brewing operation? Shandong Chenma Machinery Co.,
Ltd. provides expert consultation and custom manufacturing services for breweries of all sizes.
Our experienced engineering team specializes in brewing equipment design and can help you select the perfect tank
sizes for your specific production goals, facility constraints, and growth plans. From nano brewery startups to
large commercial operations, we provide comprehensive solutions that ensure optimal brewing performance.
Get professional tank sizing consultation today:
- WhatsApp: +86 180 6342 1809
- Email: admin@sdchenma.com
- Address: Pingyuan County Economic Development Zone, Dezhou City, Shandong Province, China
Whether you’re planning your first brewing system or expanding existing operations, our team provides expert
guidance on tank sizing, system design, and turnkey installation services that meet your unique brewing
requirements.