
Choosing the right mixer tank chemical plays a vital role in ensuring efficiency, safety, and cost-effectiveness in your operations. A well-selected tank improves mixing efficiency, leading to uniform ingredient distribution and enhanced process performance. It also offers customization options tailored to your specific needs, ensuring optimal results for various applications.
Chenma is one of the professional stainless steel mixing tank manufacturers that can provide various stain steel tank solutions.
The long-term benefits extend beyond immediate performance. For example, the right tank provides consistent product quality, reduces wastage, and saves costs over time. The table below highlights these advantages:
| Benefit | Description | |—————————–|————————————————————————————————–| | Improved Mixing Efficiency | Ensures uniform distribution of ingredients throughout the tank, enhancing overall process efficiency. | | Customization Options | Tailored to meet specific process requirements, optimizing performance for various applications. | | Process Control | Leads to consistent product quality and reduced wastage, contributing to cost savings over time. | | Versatility | Applicable across various industries, increasing the potential for use and reducing the need for multiple systems. | | Speed and Time Savings | Reduces mixing times, leading to increased productivity and lower operational costs. |
By understanding your specific needs, you can select mixers that align with your goals, ensuring long-term benefits and reliable performance.
Define Your Chemical Mixing Needs
Understanding your specific mixing needs is the first step in selecting the right mixer tank chemical. By evaluating the properties of the chemicals, the scale of production, and the desired outcomes, you can ensure the tank meets your requirements effectively.
Assess Chemical Properties
Start by analyzing the properties of the chemicals you plan to mix. Consider factors like viscosity, density, and chemical reactivity. For example, highly viscous substances may require specialized mixers to achieve uniform blending. Similarly, reactive chemicals demand tanks made from materials that resist corrosion and prevent contamination.
Temperature and pressure conditions also play a critical role. Some chemicals require precise temperature control during mixing to maintain stability. Others may need tanks that can withstand high pressure without compromising safety. By understanding these properties, you can choose a tank that ensures efficient and safe chemical mixing.
Determine Batch Size and Production Scale
The size of your batches and the scale of your production directly influence the type of mixer tank chemical you need. For small-scale operations, compact tanks with lower capacities may suffice. However, large-scale production often requires industrial-sized tanks capable of handling significant volumes.
Think about your future needs as well. If you anticipate scaling up production, investing in a larger tank now can save costs later. Additionally, consider whether you need a fixed or portable tank. Portable tanks offer flexibility for smaller batches, while fixed tanks are ideal for continuous, high-volume operations.
Identify Desired Mixing Outcomes
Define what you aim to achieve with your chemical mixing process. Common goals in the chemical industry include:
- Precise mixing to achieve high purity in fine chemicals.
- Speeding up desired reactions to ensure maximum completion.
- Homogeneous blending of reagents on a molecular scale before significant conversion.
- Minimizing unwanted by-products to meet strict purity standards.
Each of these outcomes requires specific mixing mechanisms and tank designs. For instance, achieving molecular-level blending may call for advanced agitation systems. By identifying your goals, you can select a tank that aligns with your mixing requirements and delivers consistent results.
Types of Mixer Tanks for Chemical Applications
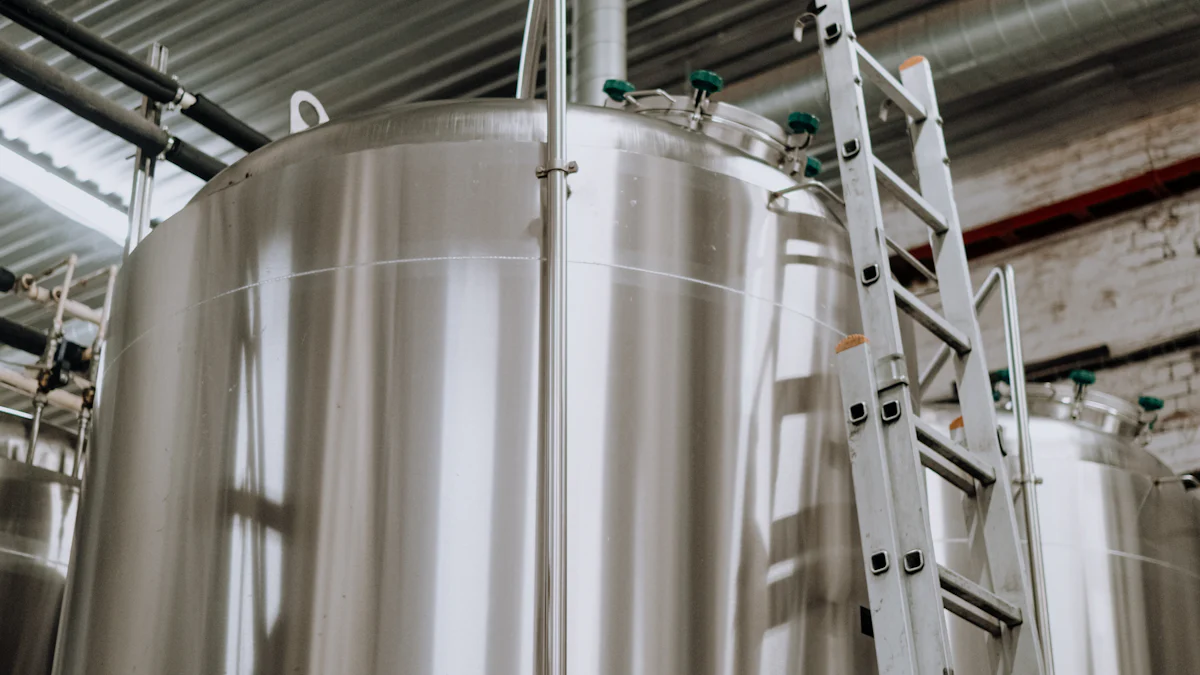
Choosing the right type of mixer tank is essential for achieving efficient chemical mixing. Different designs cater to various operational needs, offering flexibility and performance tailored to your processes.
Fixed vs. Portable Mixer Tanks
Fixed mixer tanks are ideal for large-scale operations requiring continuous mixing. These tanks remain stationary, providing stability and durability for high-volume production. They often integrate advanced features like automated controls and robust mixing mechanisms, making them suitable for industrial applications.
Portable mixer tanks, on the other hand, offer flexibility. You can move them between locations, making them perfect for small-scale or batch operations. These tanks are lightweight and compact, allowing you to adapt to changing production needs. If your process involves frequent adjustments or smaller batches, portable tanks provide a cost-effective and versatile solution.
Open-Top vs. Closed-Top Tanks
Open-top tanks are designed for easy access. They allow you to monitor the mixing process visually and make adjustments as needed. These tanks are commonly used for processes that require manual intervention or the addition of ingredients during mixing. However, they may not be suitable for volatile or hazardous chemicals due to potential exposure risks.
Closed-top tanks provide a sealed environment, ensuring safety and preventing contamination. These tanks are ideal for handling sensitive or reactive chemicals. They also support pressurized mixing, making them suitable for processes requiring controlled environments. If safety and containment are priorities, closed-top tanks are the better choice.
Specialty Designs for Specific Applications
Specialty mixer tanks are engineered for unique chemical mixing requirements. These tanks feature advanced designs to handle specific challenges. For example, they include customizable impeller configurations for uniform mixing and variable speed controls for precise adjustments. Durable construction materials like stainless steel ensure longevity in harsh environments.
The table below highlights key features of specialty designs:
| Feature | Description | |—————————–|—————————————————————————————————| | Uniform Mixing | Specialized impeller configurations ensure thorough and uniform mixing, preventing stratification. | | Easy Installation and Maintenance | Designed for ease of installation and maintenance, simplifying access for cleaning and servicing. | | Powerful Motor | Equipped with robust motors to generate necessary torque for effective agitation and blending. | | Customizable Impeller Designs| Offers a range of impeller designs tailored to specific viscosity and mixing requirements. | | Variable Speed Control | Allows operators to adjust mixing speed and intensity based on liquid characteristics. | | Durable Construction | Made from high-quality materials like stainless steel for longevity in harsh environments. | | Applications | Versatile systems for high-viscosity mixing in industries like adhesives, cosmetics, and polymers. |
These specialty tanks excel in demanding applications, ensuring reliable performance and consistent results.
Material Compatibility in Chemical Mixers
Choosing the right material for your mixer tank ensures durability and safety during chemical mixing. The tank material must resist corrosion, withstand temperature and pressure changes, and endure abrasive forces. Understanding these factors helps you select a tank that performs reliably under challenging conditions.
Corrosion Resistance and Chemical Reactivity
Corrosion resistance is critical when working with reactive chemicals. Materials like stainless steel, Hastelloy, and polypropylene offer excellent protection against chemical reactions. For example:
- Hastelloy C276 and C22 handle aggressive chemicals, including acids.
- Teflon, Halar, and Kynar PVDF are ideal for production agitators.
- Titanium and exotic alloys excel in demanding applications requiring top-entry mixers.
The table below highlights common materials and their properties:
| Material | Properties | Applications | |——————————|———————————————————————————————–|————————————————–| | Stainless Steel | Excellent corrosion resistance, durability; grades like 304, 316, and 316L available. | Food and beverage, pharmaceuticals, chemical processing. | | Hastelloy | Exceptional corrosion resistance in aggressive environments; includes Hastelloy C276 and C22. | Industries handling aggressive chemicals and acids. | | Polypropylene (PP) / PE | Lightweight, durable, resistant to a wide range of chemicals. | Water treatment, wastewater treatment, chemical processing. |
Selecting the right material prevents contamination and extends the tank’s lifespan.
Temperature and Pressure Tolerance
Chemical mixing often involves extreme temperatures and pressures. Tanks must maintain structural integrity under these conditions. Stainless steel, for instance, withstands high temperatures and resists deformation. Exotic alloys like titanium handle both high pressure and temperature fluctuations effectively.
If your process involves heating or cooling, consider materials with excellent thermal conductivity. This ensures uniform temperature distribution, preventing hotspots that could compromise chemical stability. For pressurized mixing, closed-top tanks made from reinforced materials provide the necessary strength and safety.
Abrasion and Wear Resistance
Abrasive materials can damage your mixer tank over time. Solid particles rubbing against the tank walls cause wear, leading to cracks and reduced efficiency. Using abrasion-resistant materials, such as specific alloys, minimizes this damage.
For example, stainless steel and Hastelloy resist wear effectively, making them suitable for abrasive products. These materials enhance the tank’s durability, ensuring consistent performance even in harsh environments. By prioritizing abrasion resistance, you reduce maintenance costs and extend the tank’s operational life.
Operational Features of the Best Industrial Chemical Mixer
Mixing Mechanisms and Speed Variability
The mixing mechanism is the heart of any chemical mixer. It determines how effectively the components blend together. Different mechanisms, such as impellers, paddles, or static mixers, cater to specific chemical properties and mixing goals. For example, high-viscosity liquids often require powerful impellers to ensure uniform blending, while static mixers work well for low-viscosity fluids.
Speed variability is another critical feature. Adjustable speeds allow you to fine-tune the mixing process based on the chemical’s viscosity and desired outcomes. For instance, slow speeds may suit delicate reactions, while faster speeds can accelerate blending in high-volume operations. This flexibility ensures the mixer adapts to your unique requirements, making it an optimal chemical mixer for diverse applications.
Automation and Control Systems
Automation enhances the efficiency and precision of chemical mixers. Modern systems integrate advanced control features that streamline operations and reduce human intervention. Key benefits include:
- Precision and consistency: Automation ensures accurate control over parameters like speed and temperature, resulting in consistent product quality.
- Real-time monitoring and adjustments: Integrated systems continuously monitor the process, making automatic adjustments to minimize errors.
- Data analytics and predictive maintenance: Automated mixers collect data to predict maintenance needs, reducing downtime and extending equipment life.
These features not only improve operational efficiency but also enhance safety by minimizing manual handling of hazardous chemicals.
Energy Efficiency and Cost Savings
Energy-efficient mixers offer significant cost-saving benefits. They reduce energy consumption, which lowers operating expenses and supports sustainable practices. Additional advantages include:
- Low maintenance reduces repair costs: Static mixers, for instance, lack moving parts, leading to fewer breakdowns and lower repair expenses.
- Efficient chemical consumption: These mixers ensure thorough blending, minimizing waste and saving on raw material costs.
- Exceptional durability: Robust designs enhance longevity, providing long-term cost efficiency.
By choosing an energy-efficient mixer, you not only save money but also contribute to environmentally friendly operations. This makes it a key feature of the best industrial chemical mixer.
Safety Features in Chemical Mixers
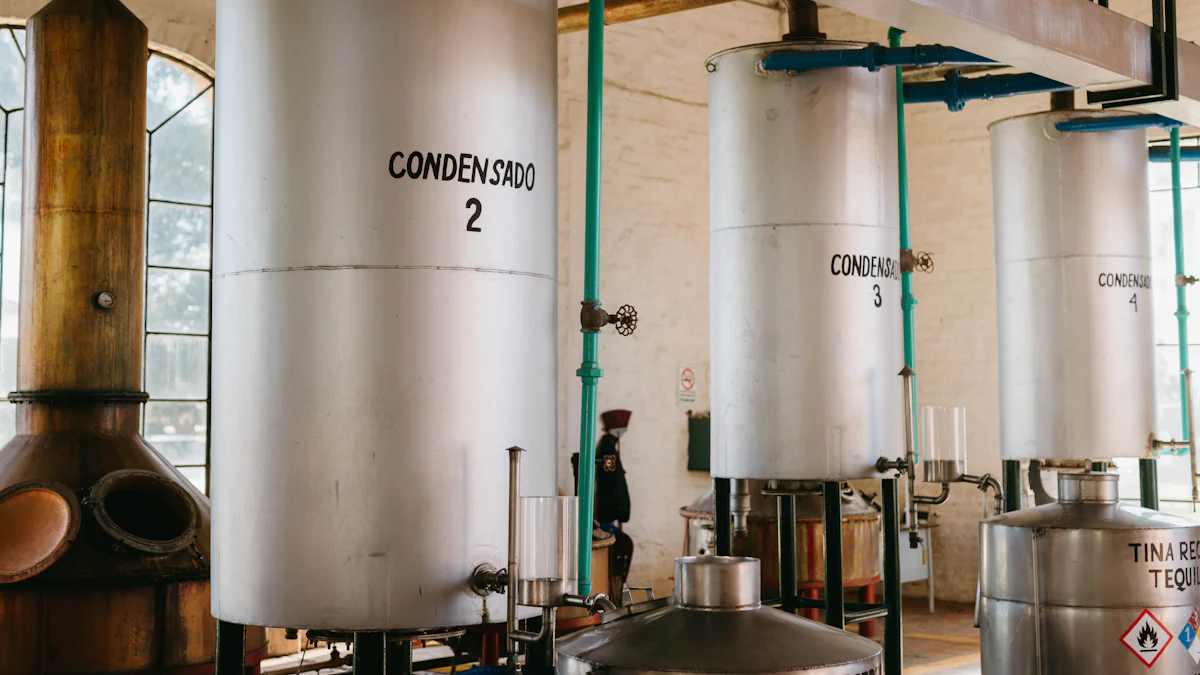
Built-in Safety Mechanisms
Safety mechanisms in chemical mixers are essential for preventing accidents and ensuring smooth operations. You should prioritize features that minimize risks during mixing processes. For instance, emergency shut-off systems allow you to stop the mixer immediately in case of malfunction. Overload protection prevents damage by shutting down the motor when it exceeds its capacity. Additionally, pressure relief valves ensure safe operation by releasing excess pressure in closed-top tanks.
To prevent chemical spills, secure the mixer on a flat, stable surface. Keep the surrounding area free of clutter and ensure proper ventilation. A well-organized workspace reduces tripping hazards and allows operators to move freely. These measures not only enhance safety but also improve operational efficiency.
Compliance with Industry Standards
Compliance with industry standards ensures your chemical mixers meet safety and quality requirements. Look for certifications like ISO9001, which guarantees adherence to quality management systems. Environmental standards, such as ISO14001, confirm that the mixer aligns with sustainable practices. Occupational health certifications, like OHSAS18001, demonstrate a commitment to operator safety.
You should also verify that the mixer complies with local and international regulations. For example, CE certification indicates conformity with European safety standards. By choosing a mixer with these certifications, you ensure reliable performance and reduce the risk of regulatory issues.
Operator Safety and Ergonomics
Operator safety and ergonomics play a crucial role in maintaining a safe working environment. Ergonomic designs reduce physical strain, allowing operators to work comfortably for extended periods. Features like adjustable controls and user-friendly interfaces make the mixer easier to operate. This minimizes errors and enhances productivity.
Proper lighting and clear labeling on the mixer improve visibility and reduce the likelihood of accidents. Additionally, training operators on safe handling practices ensures they can use the equipment confidently. By focusing on ergonomics and operator safety, you create a safer and more efficient workspace.
Maintenance and Cleaning Considerations
Proper maintenance and cleaning of chemical mixer tanks ensure optimal performance and extend their lifespan. By addressing common challenges and implementing effective solutions, you can maintain efficiency and safety in your operations.
Ease of Cleaning and CIP Systems
Cleaning chemical mixer tanks can be challenging, especially when dealing with uneven mixing, equipment corrosion, or clogging. Uneven mixing often results from residue buildup, which you can prevent by optimizing tank designs and using high-capacity mixers. Corrosion caused by harsh chemicals requires tanks made from corrosion-resistant materials and regular preventative maintenance. Solid particles that cause clogging can be managed with high-shear mixers and frequent cleaning routines.
To simplify cleaning, consider using Clean-in-Place (CIP) systems. These systems offer several advantages:
- Increased product safety by reducing contamination risks.
- Enhanced employee safety by minimizing chemical exposure and eliminating the need for vessel entry.
- Economic benefits, including more production time, improved product quality, and lower utility costs.
- Compliance with hygiene regulations like FSMA and CFR21.
CIP systems streamline cleaning processes, making them an excellent choice for maintaining chemical mixer tanks.
Availability of Spare Parts and Support
Access to spare parts and technical support is crucial for minimizing downtime. When selecting a mixer tank, ensure the manufacturer provides readily available replacement parts. This reduces delays caused by waiting for components. Reliable technical support also helps you address issues quickly, ensuring uninterrupted operations.
Partnering with manufacturers who offer comprehensive after-sales services can save you time and resources. Look for companies that provide detailed maintenance guides, troubleshooting assistance, and training for your team. These services ensure you can maintain your equipment effectively.
Durability and Long-Term Maintenance
Durability plays a key role in reducing long-term maintenance costs. Tanks made from high-quality materials like stainless steel resist wear and corrosion, ensuring consistent performance. Abrasion-resistant materials are particularly important when handling abrasive chemicals or solid particles. Regular inspections and maintenance schedules help identify potential issues early, preventing costly repairs.
Investing in durable tanks and following a proactive maintenance plan ensures your equipment remains reliable over time. This approach not only extends the lifespan of your mixer tanks but also enhances overall operational efficiency.
Cost and Budget Factors
Balancing Initial Investment with ROI
When choosing a mixer tank, you must weigh the initial investment against the potential return on investment (ROI). A high-quality tank may seem expensive upfront, but it often delivers long-term savings. Durable materials like stainless steel reduce maintenance costs and extend the tank’s lifespan. Energy-efficient designs lower operational expenses by consuming less power. These features ensure you save money over time while maintaining consistent performance.
Consider the productivity gains a reliable tank offers. Faster mixing speeds and uniform blending improve output, allowing you to meet production targets efficiently. This increased productivity translates into higher profits, offsetting the initial cost. By evaluating the ROI, you can make an informed decision that benefits your operations in the long run.
Customization Options and Costs
Customization allows you to tailor the tank to your specific needs, but it also impacts the overall cost. Features like specialized impellers, variable speed controls, and advanced automation systems enhance performance but may increase the price. You should assess which customizations are essential for your processes. For example, if you handle high-viscosity chemicals, investing in a powerful motor and abrasion-resistant materials ensures optimal mixing.
Requesting a detailed quote from the manufacturer helps you understand the cost implications of each customization. This transparency allows you to prioritize features that align with your budget and operational goals. Customization ensures the tank meets your unique requirements, offering value for every dollar spent.
Warranty and Manufacturer Support
A comprehensive warranty provides peace of mind and protects your investment. Look for manufacturers that offer warranties covering defects in materials and workmanship. A longer warranty period often indicates the manufacturer’s confidence in their product’s quality. Reliable support services, such as technical assistance and spare parts availability, ensure uninterrupted operations.
You should also evaluate the manufacturer’s reputation. Companies with a proven track record of excellent customer service often provide better post-purchase support. Partnering with a trusted manufacturer ensures you receive timely assistance, minimizing downtime and maximizing the tank’s lifespan.
Tip: Always review the warranty terms carefully to understand what is covered and for how long. This step helps you avoid unexpected expenses in the future.
Leveraging Expert Advice for Choosing Chemical Mixers
Consulting Industry Professionals
Consulting industry professionals can help you make informed decisions when selecting a chemical mixer. These experts bring years of experience and technical knowledge to the table. They analyze your specific requirements and recommend solutions that align with your operational goals. By working with professionals, you gain access to insights that improve efficiency and reduce costs.
The table below highlights the benefits of consulting industry professionals:
| Benefit | Description | |———————————-|————————————————–| | Cost Reduction | Reduces production and energy costs. | | Quality Improvement | Increases the quality of end products. | | Risk Mitigation | Provides tangible optimization approaches. |
These advantages ensure you choose a mixer that enhances your processes while minimizing risks. Professionals also guide you in selecting the right blending system choices, ensuring compatibility with your chemical applications.
Manufacturer Expertise and Custom Solutions
Manufacturers with expertise in chemical mixers offer valuable support. They understand the technical aspects of mixer design and can tailor solutions to meet your needs. For example, they may recommend custom impellers or advanced automation systems to optimize performance. Their experience ensures the mixer integrates seamlessly into your operations.
Custom solutions also address unique challenges. If you handle abrasive chemicals or high-viscosity substances, manufacturers can design tanks with durable materials and powerful motors. This customization improves mixing efficiency and extends the equipment’s lifespan. Partnering with a knowledgeable manufacturer ensures you receive a product that delivers consistent results.
Learning from Case Studies and Reviews
Case studies and reviews provide real-world insights into the performance of chemical mixers. By examining these resources, you can learn how others have solved similar challenges. Case studies often detail the specific features and benefits of a mixer, helping you understand its capabilities.
Customer reviews highlight practical experiences, including ease of use, maintenance, and reliability. Look for patterns in feedback to identify common strengths and weaknesses. This information helps you make confident decisions and avoid potential pitfalls. Learning from others’ experiences ensures you select a mixer that meets your expectations and supports your goals.
Why Choose Chenma for Mixer Tank Chemical Solutions
Expertise in Stainless Steel Tank Manufacturing
Chenma stands out as a leader in stainless steel tank manufacturing. With over 200 skilled professionals and a 20,000 m² production facility, the company produces tanks that meet the most demanding technical requirements. Advanced machinery ensures precision in every design, whether you need a standard tank or a custom solution. Chenma’s expertise allows you to benefit from durable, high-quality tanks tailored to your specific needs. This focus on excellence ensures your mixers perform reliably in even the most challenging environments.
Customization and Turnkey Solutions
Chenma offers unmatched customization options to meet your unique chemical mixing requirements. Talented engineers work closely with you to adapt tanks to your processes. Whether you need specialized impellers, variable speed controls, or advanced automation systems, Chenma delivers solutions that enhance efficiency and performance. The company also provides turnkey projects, including process design, equipment manufacturing, installation, and technical training. This comprehensive approach simplifies your operations and ensures seamless integration of the tanks into your production line.
Certifications and Quality Assurance
Certifications play a vital role in ensuring the quality and safety of mixer tanks. Chenma products meet the highest standards, holding ISO9001, ISO14001, OHSAS18001, and CE certifications. These certifications guarantee compliance with quality, environmental, and occupational health standards. Additionally, certifications like ASME “U” and National Board “R” validate the tanks’ ability to handle pressure vessel requirements and repairs.
| Certification Type | Description | |—————————–|———————————————–| | ASME “U” certification | Ensures compliance with pressure vessel standards. | | National Board “R” certification | Validates the repair and alteration of pressure vessels. |
By choosing Chenma, you gain access to tanks that meet rigorous safety and quality benchmarks. This commitment to excellence ensures your operations remain efficient and compliant with industry regulations.
Selecting the right mixer tank for chemicals involves evaluating several critical factors. You must consider the liquid’s viscosity, specific gravity, tank volume, and desired mixing speed. These elements influence the tank’s performance and ensure efficient mixing. Aligning the tank choice with your specific chemical application guarantees optimal results. Each mixer type is designed for unique needs, making it essential to match the tank to your process requirements. Consulting experts like Chenma ensures you prioritize quality, safety, and long-term efficiency. This approach helps you achieve consistent performance and operational success.
FAQ
1. How do I choose the right material for my mixer tank?
You should evaluate the chemical properties, such as reactivity, temperature, and pressure requirements. Stainless steel works well for most applications due to its durability and corrosion resistance. For highly reactive chemicals, consider specialized materials like Hastelloy or polypropylene.
2. What is the difference between fixed and portable mixer tanks?
Fixed tanks remain stationary and suit large-scale, continuous operations. Portable tanks offer flexibility and are ideal for small-scale or batch processes. Choose based on your production scale and whether you need mobility for your operations.
3. How can I ensure my mixer tank meets safety standards?
Look for certifications like ISO9001, ISO14001, and CE. These ensure compliance with quality, environmental, and safety standards. Additionally, prioritize tanks with built-in safety features like emergency shut-offs and pressure relief valves.
4. Are Clean-in-Place (CIP) systems necessary for chemical mixers?
CIP systems simplify cleaning, reduce contamination risks, and improve safety. They are essential for industries requiring strict hygiene, such as food and pharmaceuticals. If your process involves frequent cleaning, CIP systems save time and enhance efficiency.
5. Can I customize my mixer tank for specific needs?
Yes, many manufacturers, like Chenma, offer customization options. You can request features like specialized impellers, variable speed controls, or advanced automation. Customization ensures the tank aligns with your unique chemical mixing requirements.