
Stainless steel mix tanks excel in mixer tank chemical applications due to their exceptional properties. Their durability ensures a long service life, even in demanding industrial environments. The chromium-rich surface resists corrosion, making them ideal for handling harsh chemicals. Their smooth, non-porous structure prevents bacterial growth and simplifies cleaning, maintaining product purity. High-temperature resistance allows them to perform reliably in processes like pasteurization. Additionally, stainless steel’s recyclability supports sustainability, while its resistance to contamination preserves product integrity. These qualities make stainless steel indispensable for industries requiring efficient and hygienic mixing solutions.
Chenma is one of the professional stainless steel mixing tank manufacturers that can provide various stain steel tank solutions.
Chemical Resistance of Stainless Steel Mix Tanks
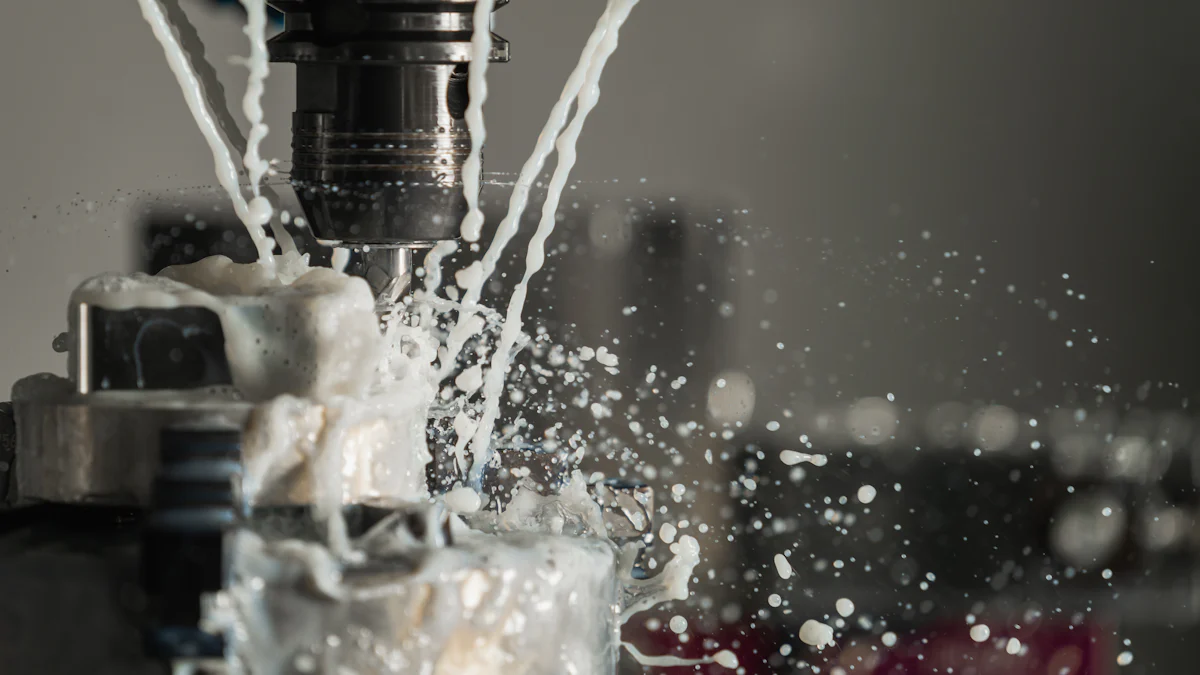
Compatibility with Aggressive Chemicals
Stainless steel mix tanks demonstrate exceptional compatibility with a wide range of aggressive chemicals, making them indispensable in industries like pharmaceuticals, food and beverage, and chemical processing. These tanks can handle substances that would degrade other materials, ensuring reliable performance in demanding environments. Common aggressive chemicals used with stainless steel mix tanks include:
- Caustic (sodium hydroxide): This alkaline agent effectively cleans and removes organic residues from tank surfaces.
- Muriatic acid and phosphoric acid: These acids neutralize caustic solutions and remove calcium deposits, maintaining the tank’s efficiency.
- Nitric acid: This chemical enhances the sanitary surface finish of the equipment, ensuring compliance with hygiene standards.
The ability to withstand such chemicals without compromising structural integrity or contaminating the contents makes stainless steel an ideal choice for mixer tank chemical applications. Its resistance to chemical reactions ensures that the tanks maintain their functionality and longevity, even under continuous exposure to harsh substances.
Corrosion Resistance in Harsh Environments
Stainless steel’s corrosion resistance is a defining feature that sets it apart from other materials. This resistance stems from its unique composition, which includes at least 10.5% chromium. Chromium reacts with oxygen in the environment to form a thin, passive film on the surface of the steel. This film acts as a barrier, preventing oxygen and water from reaching the underlying metal. If the surface becomes scratched, the exposed chromium quickly reforms the protective layer, ensuring continuous protection.
Additional elements like nickel and molybdenum further enhance this corrosion resistance. Molybdenum, in particular, strengthens the steel’s ability to withstand exposure to chlorides, seawater, and acidic conditions. These properties make stainless steel mix tanks highly reliable in environments with high chemical exposure, such as industrial water treatment and cosmetics manufacturing.
Industries benefit from the low maintenance requirements of stainless steel tanks. Their surfaces are easy to clean, and their design allows for effective access during sanitation processes. This ensures that tanks remain free from contamination, even in the most challenging conditions.
Durability and Longevity in Mixer Tank Chemical Applications
Withstanding High Pressure and Vacuum Conditions
Stainless steel mix tanks excel in environments where high pressure and vacuum conditions are common. Their robust construction ensures they maintain structural integrity even under extreme mechanical stress. Industries such as pharmaceuticals and chemical processing often require tanks that can handle rapid pressure fluctuations without deformation or failure. Stainless steel’s inherent strength makes it the material of choice for these demanding applications.
The average lifespan of high-quality stainless steel tanks exceeds 20 years. This durability reduces the need for frequent replacements, offering long-term reliability. Unlike alternative materials, stainless steel resists cracking and warping under pressure, ensuring consistent performance. Its weldability also allows for seamless joints, which further enhances the tank’s ability to withstand high-pressure environments. These features make stainless steel mix tanks indispensable for industries requiring reliable solutions for mixer tank chemical applications.
Performance Under Extreme Temperatures
Stainless steel demonstrates exceptional performance under extreme temperature variations. Its resistance to oxidation and scaling ensures reliability in high-temperature processes, such as pasteurization or chemical reactions. Certain grades, like Grade 321, are specifically designed to maintain corrosion resistance at elevated temperatures, avoiding issues like grain boundary carbide precipitation. This makes stainless steel suitable for applications involving prolonged exposure to heat.
However, thermal expansion can pose challenges in restrained components. Austenitic stainless steels, known for their higher coefficients of thermal expansion, may experience dimensional changes. Despite this, their ability to endure both high and low temperatures without compromising structural stability remains unmatched. For instance, stainless steel resists embrittlement caused by sigma phase formation, which can occur in specific grades like Grade 310 when exposed to temperatures between 590 to 870°C.
Industries benefit from stainless steel’s versatility in handling extreme conditions. Its durability ensures consistent performance, even in processes requiring rapid temperature changes. This reliability, combined with its long service life, makes stainless steel an ideal material for mixer tank chemical applications.
Hygienic Properties for Sanitary Applications
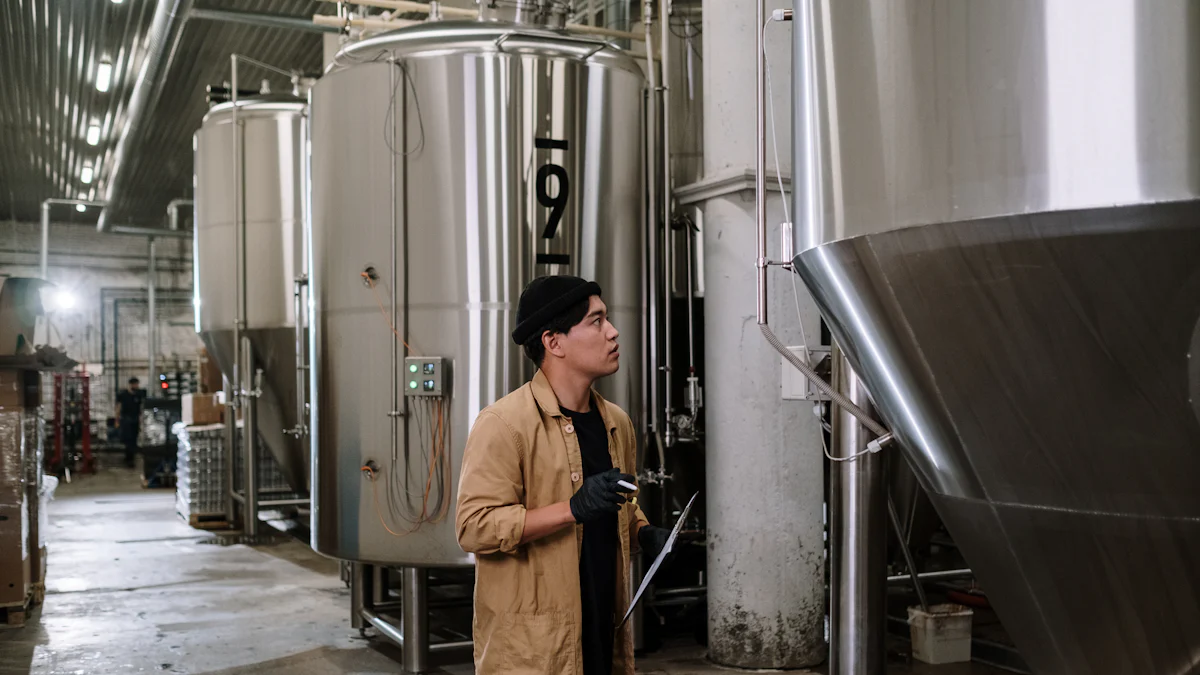
Smooth, Non-Porous Surface for Easy Cleaning
Stainless steel mix tanks offer a smooth, non-porous surface that simplifies cleaning and sanitization processes. This feature is particularly advantageous for industries like food and beverage production, where maintaining product purity is critical. The non-porous nature of stainless steel prevents the accumulation of residues, ensuring that cleaning requires minimal effort. A simple combination of a sponge and warm water effectively removes contaminants, reducing the need for harsh cleaning agents.
The material’s resistance to staining and corrosion further enhances its hygienic properties. Stainless steel surfaces remain intact even after repeated exposure to cleaning chemicals, ensuring long-term usability. Additionally, the ability to sterilize stainless steel easily helps eliminate germs and bacteria, making it an ideal choice for sanitary applications. These characteristics ensure that stainless steel mix tanks meet the stringent hygiene standards required in sensitive environments.
Prevention of Bacterial Growth in Sensitive Environments
The non-porous structure of stainless steel plays a crucial role in preventing bacterial growth. Unlike porous materials, stainless steel eliminates crevices or cracks where bacteria can hide and multiply. This smooth surface minimizes the risk of bacterial contamination over time, ensuring a safer environment for sensitive applications such as pharmaceutical production and chemical processing.
Corrosion resistance also contributes to maintaining a smooth and hygienic surface. The protective passive film formed by the alloy of iron and chromium ensures that the material remains free from pitting or degradation, which could otherwise harbor bacteria. This durability makes stainless steel mix tanks a reliable solution for industries requiring stringent hygiene controls.
In addition to its hygienic benefits, stainless steel offers long-term economic advantages. Although the initial investment may be higher, the material’s durability and low maintenance requirements result in significant cost savings over time. These features make stainless steel mix tanks an excellent choice for industries prioritizing hygiene, efficiency, and cost-effectiveness in mixer tank chemical applications.
Versatility in Mixing Processes
Adaptability to Blending, Emulsifying, and Dissolving
Stainless steel mixing tanks excel in a wide range of mixing processes, making them indispensable across industries such as food and beverage, pharmaceuticals, cosmetics, and chemicals. These tanks are designed to achieve homogeneous mixtures of solids and liquids, regardless of their consistency. Their adaptability ensures efficient performance in blending, emulsifying, and dissolving applications.
Different mixing mechanisms enhance the versatility of stainless steel tanks:
- Agitators create turbulent flow, ensuring thorough blending of ingredients.
- High Shear Mixers utilize high-speed blades to emulsify and disperse materials effectively.
- Static Mixers rely on stationary elements to mix substances through flow dynamics.
For example, in the food and beverage industry, stainless steel blending tanks are used to mix ingredients like syrups, flavorings, and dairy products. In pharmaceutical applications, they ensure precise emulsification of active ingredients. This versatility allows manufacturers to optimize their mixing process, ensuring consistent quality and efficiency in production.
Customization for Specific Industrial Needs
Stainless steel mix tanks offer extensive customization options to meet the unique requirements of various industries. Manufacturers can tailor these tanks with specific features to enhance functionality and accommodate diverse materials. Customizable finishes, such as 2B mill satin or deluxe polished surfaces, make these tanks suitable for sanitary applications like food production.
Various bottom configurations, including conical, elliptical, and sloped designs, allow tanks to handle materials with different viscosities. Additional features, such as pipe legs, mixer mounting brackets, and formed lips, further improve usability. For instance, agitators can be added to create turbulent flow, while high shear mixers are ideal for emulsification. Static mixers can also be integrated for applications requiring flow dynamics.
Capacity and size are critical factors when selecting a stainless steel tank. These parameters determine the tank’s ability to meet current production demands and accommodate future growth. The durability and corrosion resistance of stainless steel, particularly grades 304 and 316, make these tanks ideal for industries requiring sanitary and long-lasting solutions.
By offering tailored solutions, stainless steel mix tanks provide unmatched flexibility, ensuring they meet the specific needs of each industrial application.
Environmental and Economic Benefits of Stainless Steel Mix Tanks
Sustainability Through Recyclability
Stainless steel mix tanks contribute significantly to environmental sustainability due to their recyclability. Steel ranks as one of the most recycled materials globally, surpassing paper, plastic, aluminum, and glass. Approximately 88% of the world’s steel undergoes recycling, showcasing its pivotal role in reducing waste. Recycling stainless steel not only conserves natural resources but also minimizes energy consumption during production. For instance, recycling steel from a single car can cut greenhouse gas emissions equivalent to consuming over 300 gallons of gasoline.
The durability of stainless steel further enhances its sustainability. Its corrosion-resistant properties ensure a long service life, reducing the need for frequent replacements. This longevity minimizes industrial waste and supports eco-friendly practices. Industries that incorporate stainless steel in their infrastructure actively contribute to building a greener future. By choosing stainless steel mix tanks, businesses align with global sustainability goals while maintaining high performance in their mixing processes.
Cost Efficiency Over the Long Term
Stainless steel mix tanks offer unparalleled cost efficiency over time. Their durability and low maintenance needs make them a superior investment compared to alternatives like glass or plastic. These tanks resist corrosion and do not require special cleaning materials, reducing ongoing operational costs. Additionally, their long operational life eliminates the need for frequent replacements, ensuring consistent performance in demanding environments.
Investing in stainless steel tanks involves an initial higher cost, but the long-term benefits outweigh this expense. Their design prioritizes longevity, with features like in-place cleaning systems that reduce maintenance time and costs. Unlike materials prone to breakage, stainless steel withstands harsh conditions, ensuring reliability in production environments. Industries benefit from these economic advantages, as stainless steel tanks deliver consistent value while maintaining efficiency in the mixing process.
By combining sustainability and cost efficiency, stainless steel mix tanks provide a practical solution for industries seeking reliable and eco-conscious equipment.
Compliance with Industry Standards
Meeting Regulatory Requirements for Safety and Quality
Stainless steel mix tanks adhere to stringent industry standards to ensure safety and quality in their applications. These tanks comply with the FDA guidelines for sanitary design, making them suitable for industries like food, beverage, and pharmaceuticals. Their smooth, non-porous surfaces prevent contamination, maintaining the integrity of consumable products. This compliance ensures that the tanks meet hygiene standards critical for sensitive applications.
In pharmaceutical production, stainless steel tanks provide a contaminant-free environment for storing compounds such as acids, dyes, solvents, and bases. Their corrosion resistance ensures safe handling of aggressive chemicals without compromising product safety. Additionally, the tanks feature pressure relief valves or rupture disks to release excess pressure safely, preventing structural failures. The wall thickness of each tank is determined by its pressure rating, ensuring durability under high-stress conditions. Clear access points, such as man-ways or ultrasonic testing attachments, facilitate regular inspections, further enhancing safety and reliability.
These design features and regulatory compliance make stainless steel mix tanks indispensable for industries requiring strict safety and quality standards. Their ability to meet these requirements ensures consistent performance and product integrity across various applications.
Ensuring Reliable Performance in Critical Applications
Stainless steel mix tanks play a vital role in critical applications across multiple industries. In the pharmaceutical sector, they store liquid-based medications, ensuring they remain uncontaminated throughout the production process. The chemical industry relies on these tanks to safely store and mix compounds like acids, dyes, solvents, and bases. Their corrosion-resistant properties make them ideal for handling aggressive substances without compromising safety or performance.
The cosmetics and personal care industry also benefits from stainless steel tanks. These tanks store products such as shampoos, lotions, ointments, and creams, maintaining their purity and quality. Additionally, they are widely used in food, beverage, dairy, and medicine manufacturing processes, where cleanliness and product integrity are paramount.
By delivering reliable performance in these critical applications, stainless steel mix tanks support industries that prioritize safety, hygiene, and efficiency. Their versatility and durability make them a trusted solution for maintaining high standards in production environments.
Aesthetic and Practical Advantages of Stainless Steel Mix Tanks
Professional Appearance for Industrial Settings
Stainless steel mix tanks offer a polished and professional appearance, making them a preferred choice for industrial environments. Their sleek design enhances the visual appeal of production facilities while reflecting a commitment to quality and hygiene. This aesthetic advantage is particularly valuable in industries where cleanliness and professionalism are paramount, such as food processing, pharmaceuticals, and cosmetics manufacturing.
Key benefits of their professional appearance include:
- Durability: Stainless steel resists wear and tear, maintaining its polished look over time.
- Corrosion Resistance: The material withstands exposure to harsh chemicals and moisture without rusting.
- Ease of Maintenance: Its smooth surface simplifies cleaning, ensuring hygienic conditions in production areas.
- Stainless steel outperforms materials like glass or plastic in durability and sturdiness.
- Its resistance to rust ensures a long-lasting, pristine appearance.
- The ability to sanitize stainless steel easily prevents contamination, maintaining product quality.
These qualities not only improve the aesthetic appeal of industrial settings but also contribute to operational efficiency and compliance with hygiene standards.
Practical Design Features for Seamless Integration
Stainless steel mix tanks incorporate practical design features that facilitate seamless integration into existing systems. These features enhance functionality, simplify maintenance, and ensure compatibility with other equipment, making them indispensable in modern industrial processes.
Notable design elements include:
- CIP Spray Balls: Enable thorough cleaning of the tank interior without disassembly.
- Ports and Valves: Allow precise control and efficient transfer of fluids.
- Level and Temperature Sensors: Provide real-time monitoring for optimal process control.
- Manways: Large openings ensure easy access for cleaning and maintenance.
- Heating and Cooling Jackets: Enable precise temperature regulation for sensitive processes.
- Safety Features: Pressure relief valves and temperature sensors enhance operational safety.
- Equipment Integration: Compatibility with pumps and transfer systems streamlines production workflows.
These features ensure that stainless steel mix tanks meet the diverse needs of industries, from pharmaceuticals to food production. Their adaptability and user-friendly design make them a reliable choice for businesses seeking efficient and scalable solutions.
Chenma’s Expertise in Stainless Steel Mix Tanks
Advanced Manufacturing Capabilities
Chenma Machinery leverages cutting-edge manufacturing techniques to produce stainless steel mix tanks that meet the highest industry standards. The company employs advanced processes to ensure durability, efficiency, and safety in every tank. Key techniques include:
| Technique | Description | |———————–|—————————————————————————–| | Material Construction | High-grade 304 and 316 stainless steel ensures durability and corrosion resistance. | | Design Specifications | Tanks feature a domed top and conical bottom for optimal mixing efficiency. | | Agitation Systems | Equipped with advanced mixers or agitators, including high shear mixing options. | | Safety Features | Includes a back-fire relief valve and can operate under pressure or atmospheric conditions. | | Quality Assurance | All tanks undergo rigorous pressure testing and continuous quality control measures. |
These capabilities allow Chenma to deliver tanks that perform reliably in demanding industrial environments. The integration of safety features, such as back-fire relief valves, ensures operational security, while the use of high-grade materials guarantees long-term performance.
Custom Solutions Tailored to Client Needs
Chenma specializes in creating custom stainless steel mix tanks to address the unique requirements of its clients. The company’s team of skilled engineers collaborates closely with customers to design tanks that align with specific industrial processes. Customization options include:
- Capacity Adjustments: Tanks are available in a wide range of sizes to accommodate varying production scales.
- Specialized Features: Options such as heating and cooling jackets, CIP spray balls, and level sensors enhance functionality.
- Surface Finishes: Clients can choose from finishes like 2B mill satin or polished surfaces for sanitary applications.
- Agitation Systems: Tanks can be equipped with agitators or high shear mixers tailored to specific mixing needs.
Chenma’s ability to modify catalog products or engineer entirely new designs ensures that each tank meets the precise demands of its intended application. This flexibility makes the company a trusted partner for industries requiring tailored solutions.
Certifications and Quality Assurance
Chenma’s stainless steel mix tanks adhere to rigorous quality standards, ensuring reliability and safety across all applications. The company holds multiple certifications that demonstrate its commitment to excellence:
| Certification | Description | |———————–|————————————————–| | ISO9001-2005 | Quality system certification | | ISO14001-2015 | Environmental management system certification | | OHSAS18001-2007 | Occupational health management system certification| | EU CE | Compliance with European safety standards |
Chenma enforces strict quality control measures throughout the manufacturing process. Each tank undergoes pressure testing and continuous inspections to ensure compliance with international standards. These certifications and practices guarantee that Chenma’s products meet the safety, environmental, and operational requirements of industries worldwide.
By combining advanced manufacturing, tailored solutions, and certified quality assurance, Chenma delivers stainless steel mix tanks that exceed client expectations in performance and reliability.
Stainless steel mix tanks offer unmatched benefits for mixer tank chemical applications. Their durability, stemming from a protective passive film, ensures resistance to corrosion and a longer service life compared to alternative materials. These tanks maintain structural integrity under high temperatures, making them ideal for processes like pasteurization. Their smooth, non-porous surfaces prevent bacterial growth, ensuring product purity and simplifying cleaning. Furthermore, stainless steel’s recyclability supports sustainability efforts, reducing waste and promoting a circular economy.
Chenma’s expertise enhances the reliability and safety of stainless steel mix tanks. Rigorous pressure testing ensures operational resilience, while continuous quality control maintains high manufacturing standards. High-quality welds prevent leaks, ensuring safe and efficient operation. These features, combined with Chenma’s ability to deliver tailored solutions, make their tanks a dependable choice for industries requiring long-term efficiency and compliance with stringent standards.
Investing in stainless steel mix tanks provides industries with a cost-effective, sustainable, and hygienic solution for their mixing needs.
FAQ
What makes stainless steel mix tanks suitable for chemical applications?
Stainless steel mix tanks resist corrosion, handle aggressive chemicals, and maintain structural integrity under extreme conditions. Their smooth, non-porous surfaces ensure hygiene and prevent contamination. These properties make them ideal for industries like pharmaceuticals, food processing, and chemical manufacturing.
How do stainless steel tanks contribute to sustainability?
Stainless steel is 100% recyclable, reducing waste and conserving resources. Its durability minimizes the need for replacements, lowering environmental impact. Recycling stainless steel consumes less energy compared to producing new material, supporting eco-friendly industrial practices.
Can stainless steel mix tanks be customized for specific needs?
Yes, manufacturers like Chenma offer extensive customization options. Clients can choose tank sizes, surface finishes, agitation systems, and additional features like heating jackets or CIP spray balls. These tailored solutions ensure compatibility with unique industrial processes.
How do stainless steel tanks ensure hygiene in sensitive industries?
The non-porous surface of stainless steel prevents bacterial growth and simplifies cleaning. Its resistance to corrosion maintains a smooth, sanitary finish even after exposure to cleaning agents. These features meet stringent hygiene standards in industries like food, beverage, and pharmaceuticals.
What certifications ensure the quality of stainless steel mix tanks?
Certifications like ISO9001-2005, ISO14001-2015, and EU CE demonstrate compliance with international safety and quality standards. These certifications ensure that stainless steel tanks meet rigorous requirements for durability, hygiene, and environmental responsibility.